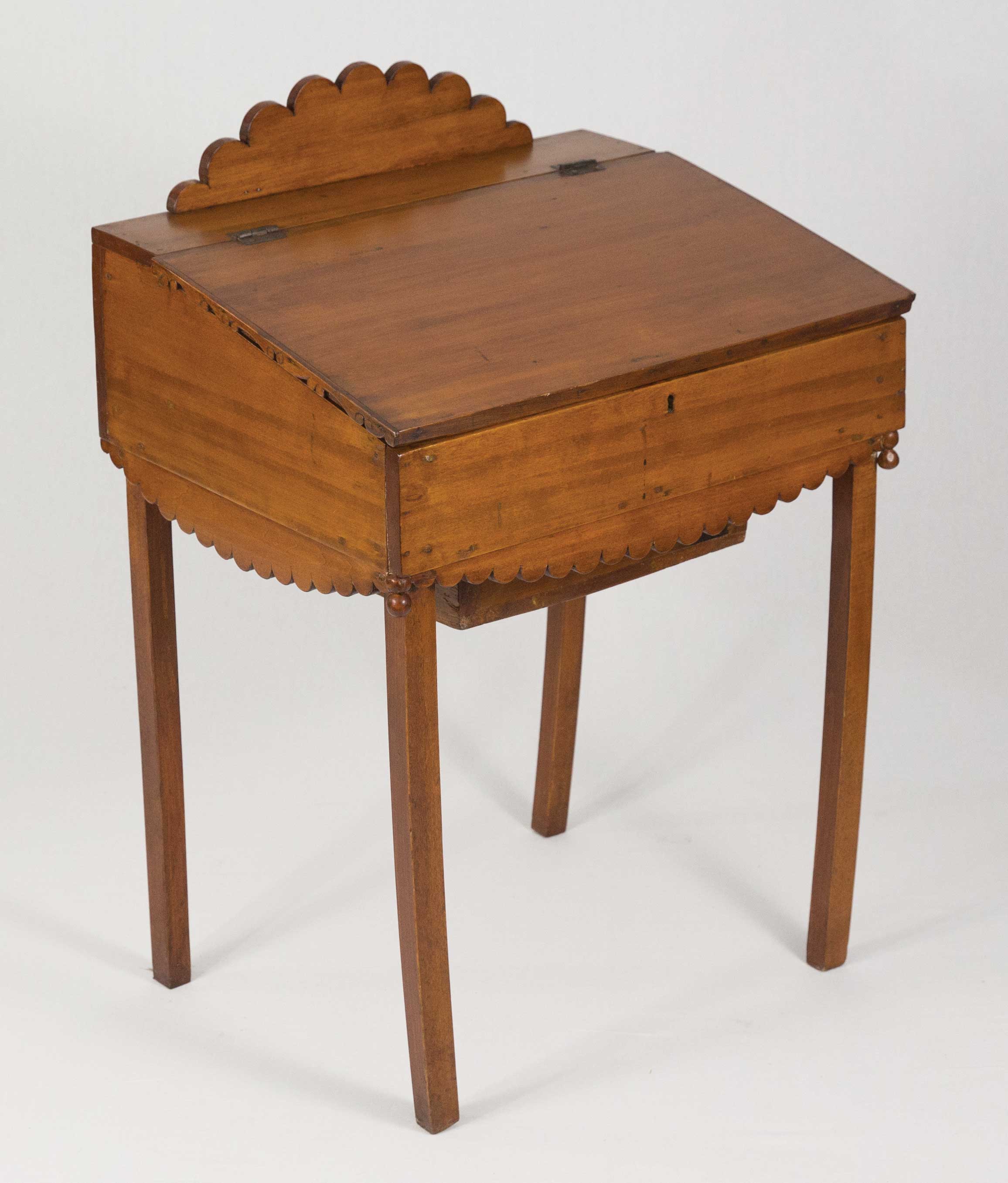
Included in his investigation of the life, tools and a detailed look at the furniture of Jonathan Fisher (1768-1847), a rural Maine minister and craftsman, author Joshua A. Klein also presents an overview of 38 pieces built by this Harvard-educated renaissance man. Below is number 10, a charming child’s desk, from “Hands Employed Aright.”
Dimensions: D: 19-1⁄2″ W: 25-3⁄4″ H: 32-1⁄2″; stock thickness 3⁄4″-7⁄8″
Wood(s): maple or birch; legs are an unknown hardwood (possibly beech)
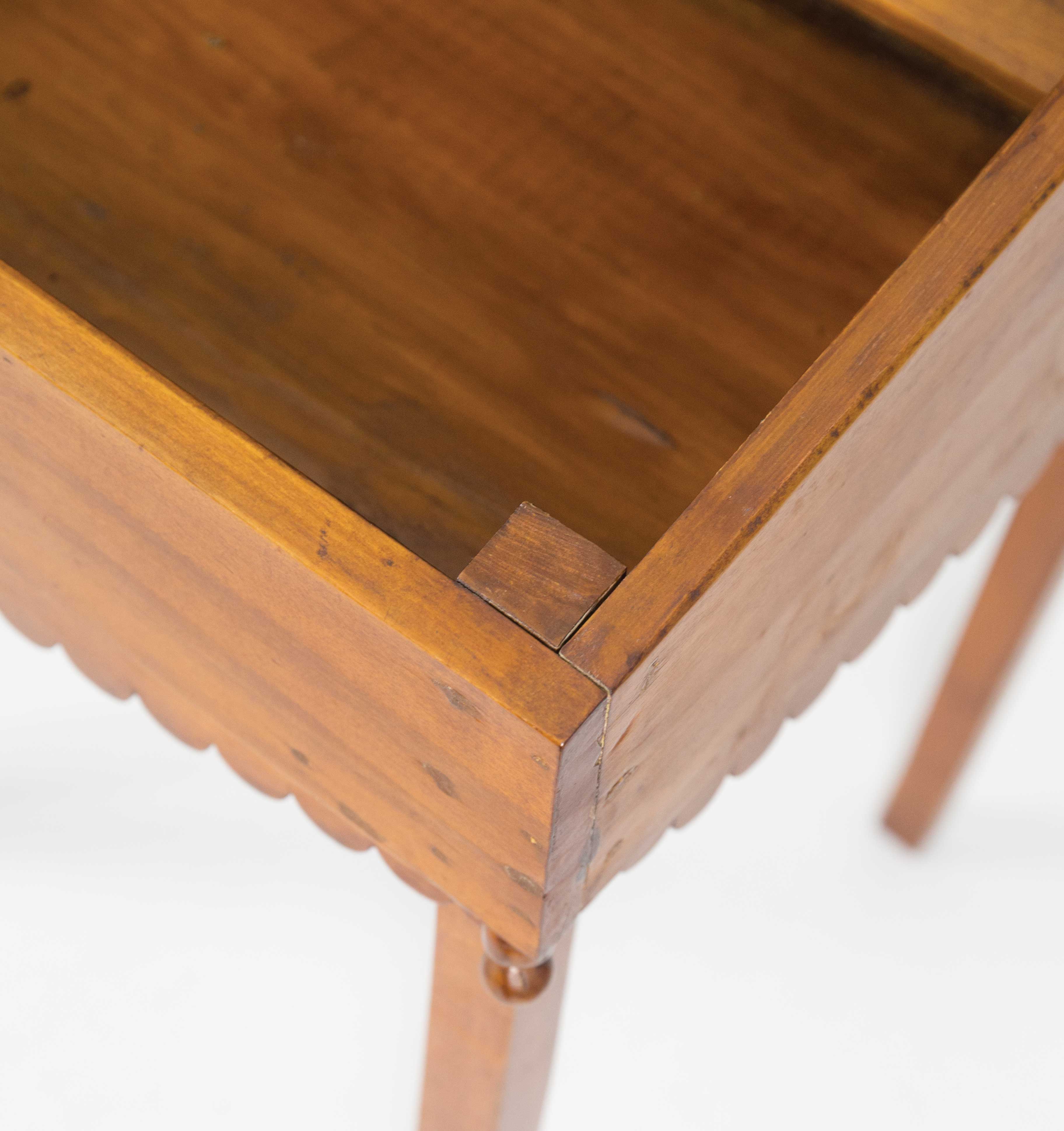
Inscriptions/stamps: sticker on cubby lid “Desk made by Rev. Jonathan Fisher Blue Hill, ME. (1791-1847) Lonnie E. Davis got it in 1948-9 fr. James Fisher bequest to MA Dodge 1955”
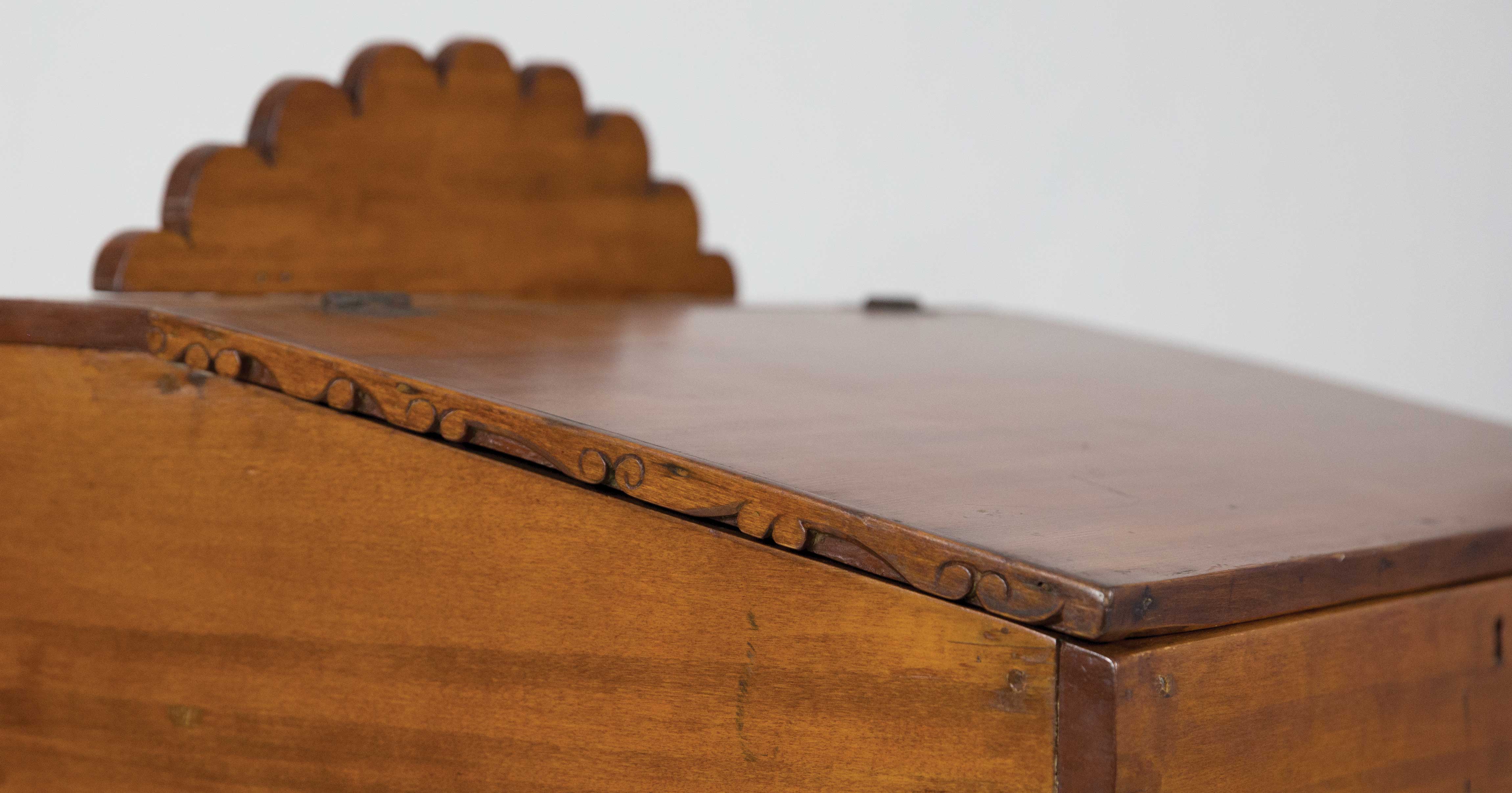
From the collection of: Jonathan Fisher Memorial
Construction: The desk is made of butted and nailed construction. The legs protrude up through bottom as corner reinforcement and were nailed from the outside. Everything is nailed together through the adjacent face. The nail holes appear to have been puttied. The top has a hinged scalloped decoration. The apron also has scalloped decorative pieces nailed to the undersides of the front and sides. The desk lid’s hinges are face mounted. The writing surface end grain is covered by a 1⁄4″-thick decorative carved strip. There are turned balls on the front corners. The top-hung drawer is butted and nailed with cut nails. The drawer runners are nailed from the bottom up into the desk with cut nails. The inside cubby is divided into four compartments. The small hinged cubby door is on wire cotterpin hinges. The writing surface has a lock attached with nails. The bottom is nailed in place from all sides. There is yellow paint residue in cracks and dark yellow putty in the nail holes. On and around the hinges are remnants of red paint. Red pigment is visible on the drawer underside. The desk underside has pink chalky residue.
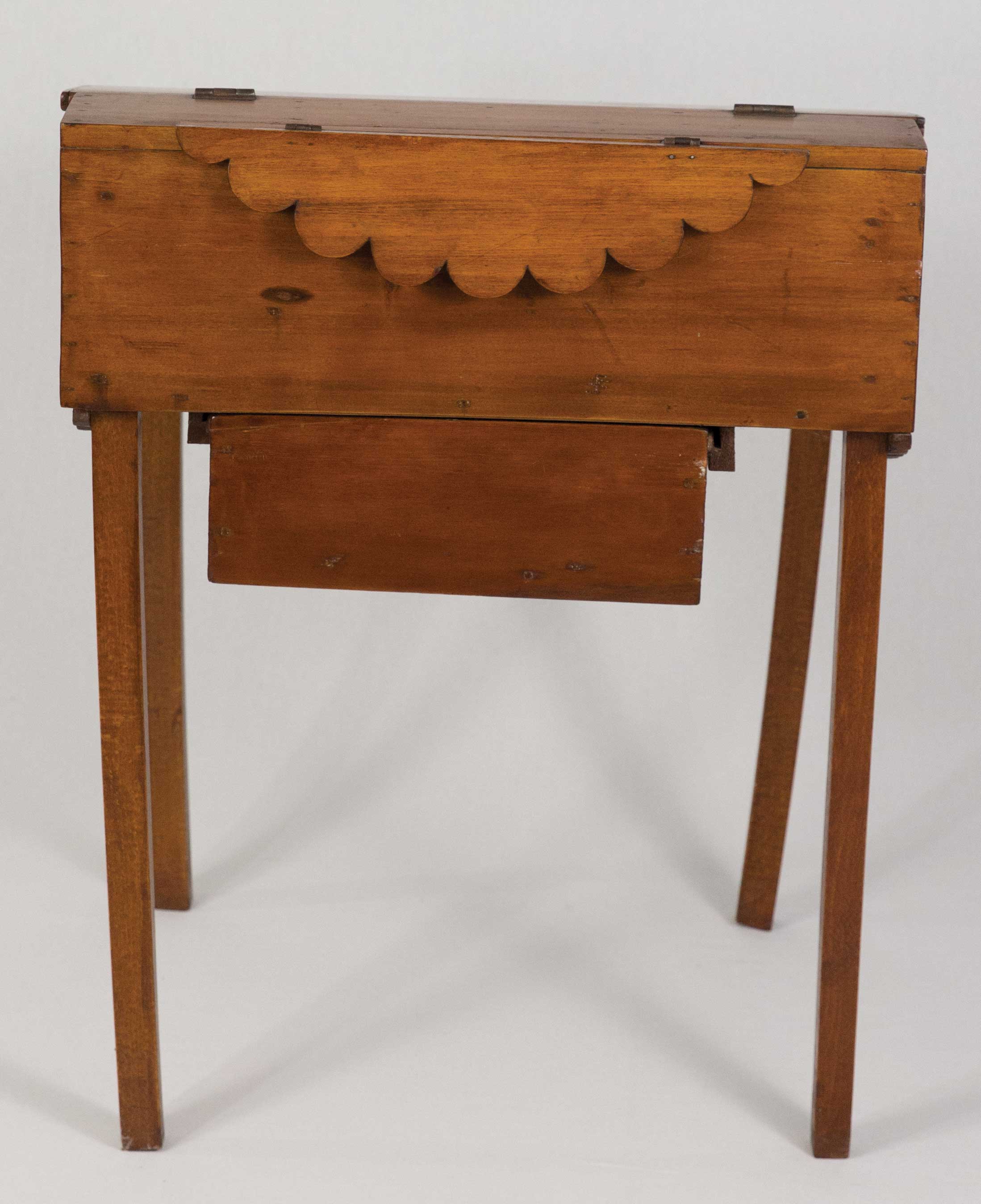
Tool Marks: There is considerable tear-out on the inside of one of the legs. There are some sash sawmill marks on the desk bottom. The bottom was planed with a fore plane. Most surfaces are smooth (perhaps due to later sanding during refinishing). The apron scallops have chisel facets and there is a saw kerf visible between scallops. There are divider center points on the scalloped details on the aprons. There are fore plane marks on the drawer face. The drawer bottom is rough and irregular. There are chisel facets on the top scalloped detail.
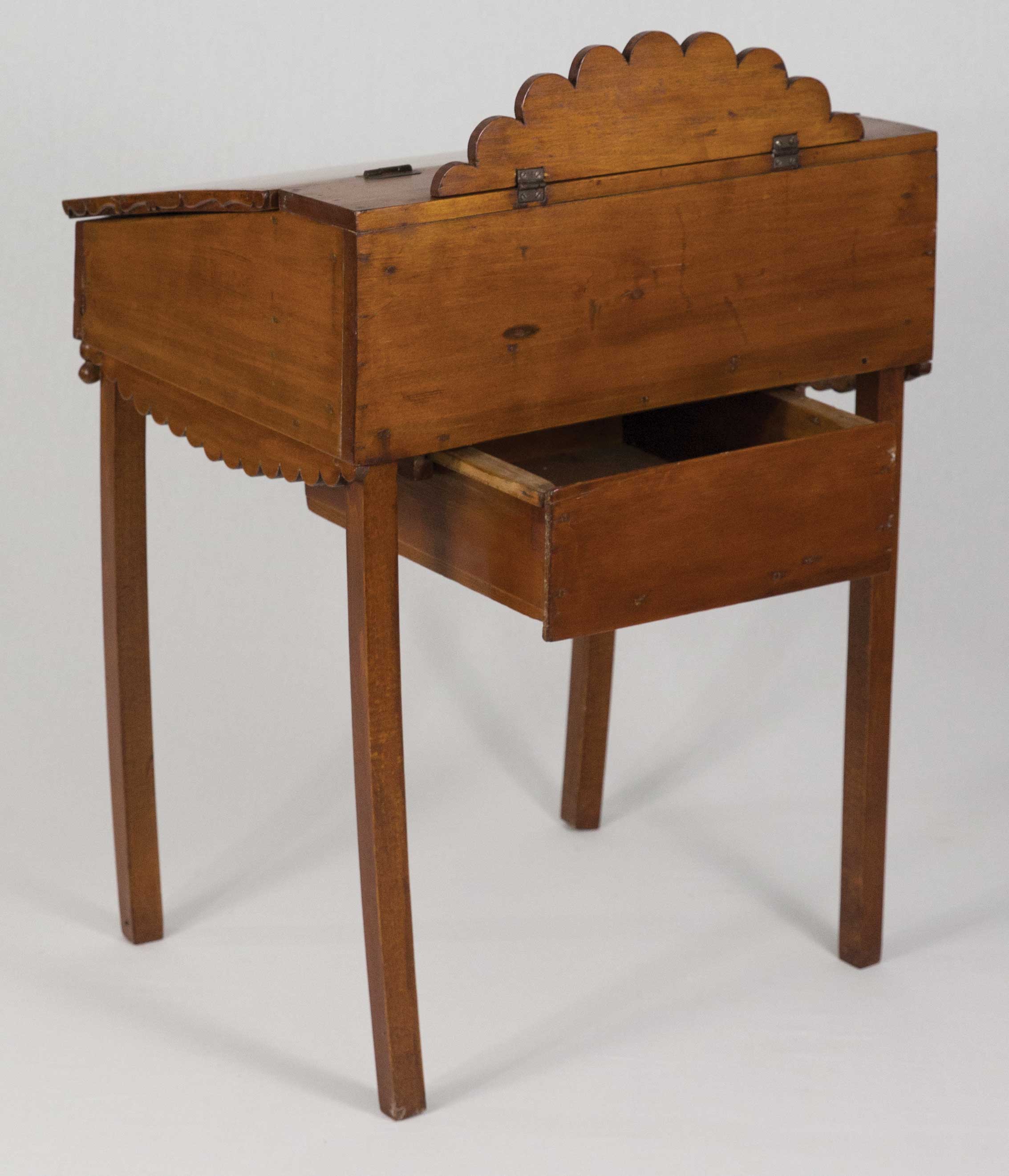
Condition: stable; the legs are extremely warped
I’m intrigued by the carved and applied ends of the lid. I’ve never seen another piece with that detail.
Ditto.
appropriate even today for stay-at-home education
Program this into a CNC, and you could sell a million of these right now.
I guess this is what shopping cart caster killers did before there were shopping carts–randomly choose one leg and bend it.
In your research into desks of this type, how typical is it, for hinges to be surface mounted, such as on this one? Were the hinges mortised into the top surfaces?
Thanks!
T
The book is about the man and his body of work, not desks in particular. Not affiliated in any way, just some random internet troll. 🙂
It’s funny how the warped legs look almost intentional, except for that one back leg.
I wonder if the sash saw marks on the bottom are from his wind sawmill?
Its funny, when I first started woodworking 30 years ago, i wanted my work to look perfect. As my skill improved, and I started using more hand tools, i started appreciating the tool marks much more. Walking through antique shops, and being able to tell what tools they used on which parts, and the character it adds. Whereas when i first started, i was trying to make my work look like ikea furniture, lol.
I like it. That an educated man went to the trouble to build a child’s desk allows me to surmise, without a bit of proof, that this was a caring daddy or grandpa. Perfection can be the enemy of very nice. In spite of what the chattering class might say, I say “well done”. Or in Navy parlance: BRAVO ZULU.
Thanks for posting this.
Don