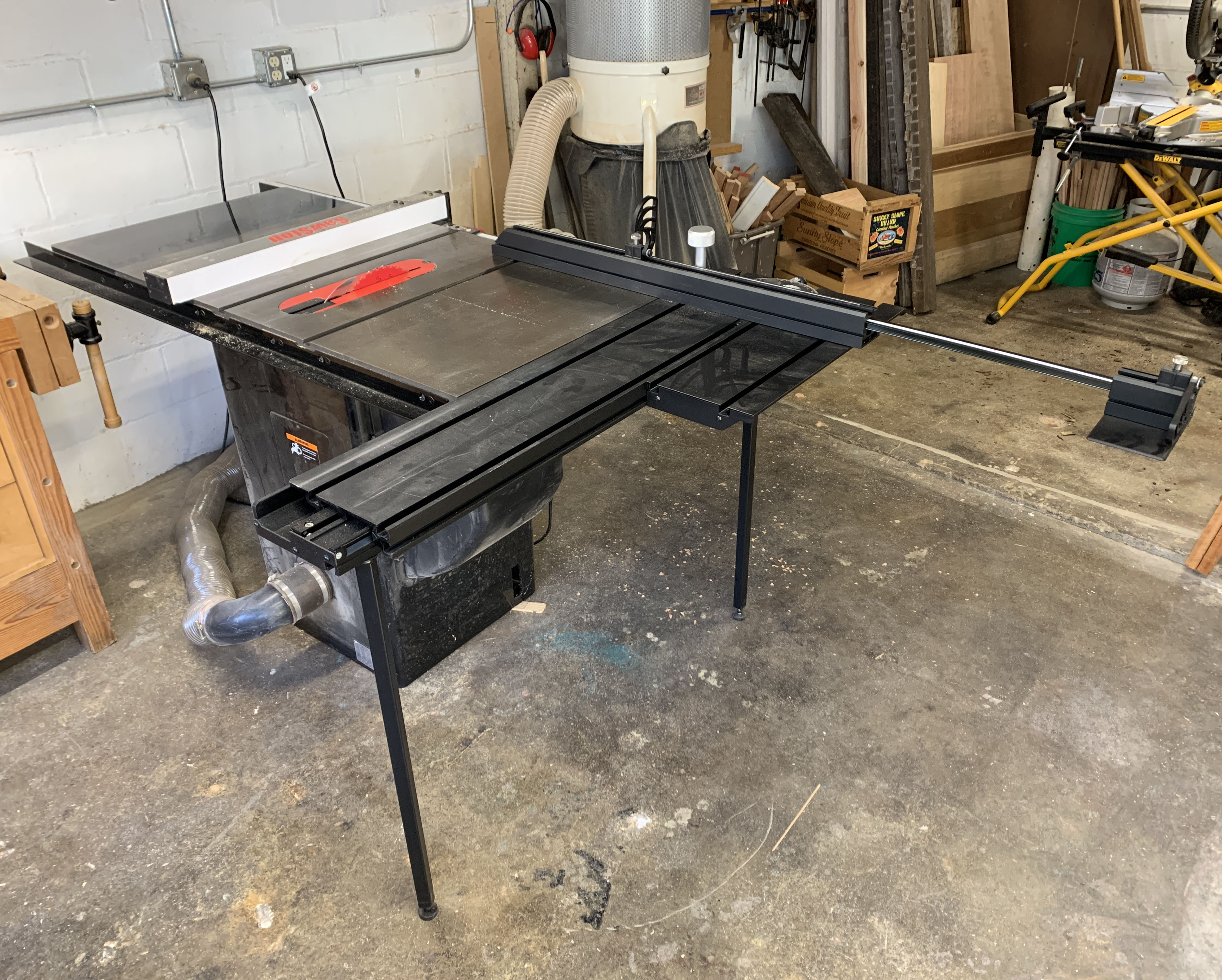
The most labor-intensive part of preparing for classes is, by far, the stock prep – especially for the tool chest classes I teach. For those classes, I crosscut pairs of ends, and pairs of fronts/backs, together so that they’re the same length. That was difficult with our old shop-made crosscut sled. When crosscutting the front/backs, more than half the length of them clamped together was unsupported, so I had to hold them both tight to the sled’s fence and down at the same time. (The only good thing about that was the upper-body workout.)
So Chris – exceedingly kind man that he is – bought (me) a sliding crosscut fence. We looked at a few other brands, but after talking to people who already owned one, we decided on the SawStop slider.
Right after the box arrived we shut down classes for 2020…so there will be no massive amounts of stock prep until there’s a COVID-19 vaccine. But in the meantime, we’ve had time to put the new slider through its paces.
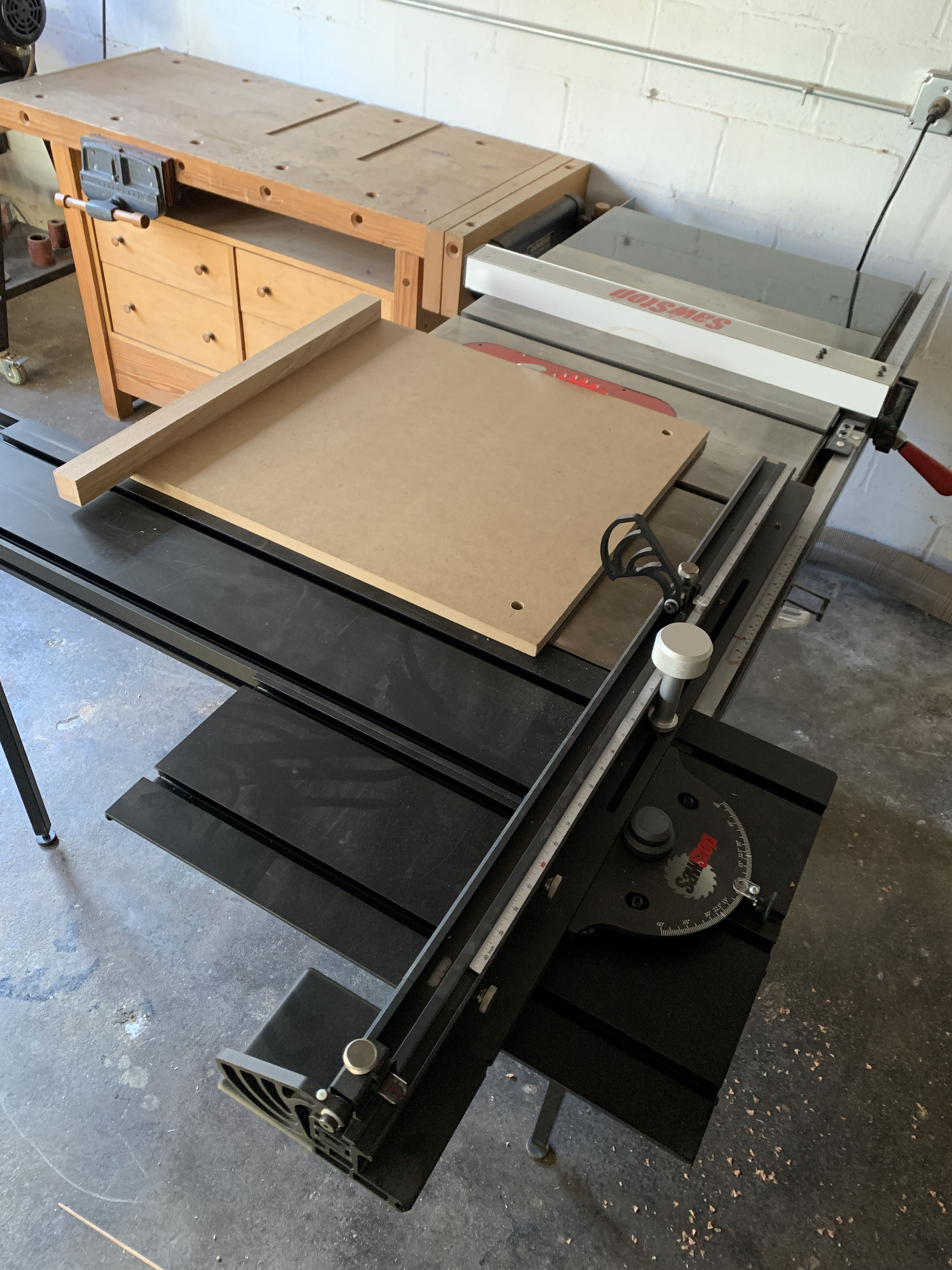
Chris has set up five or six different sliding tables over the years, and he says this one was by far the easiest; he had it up and running in about an hour (my only contribution was helping to adjust the leveling feet – it’s really a one-person job). There’s the option to bolt the slider to the table saw’s wing, or to remove the wing and bolt it directly to the main table. But either way, you almost certainly have to cut the rip fence’s rail. I believe the instructions said to do that with a metal-cutting band saw. But Chris used a recip saw with a home-center carbide blade (you could also use a metal-cutting jigsaw blade), then he filed the cut edges; the cut took less than 5 seconds.
In all honestly, we don’t have the fence perfectly set above the table’s height; it rides up the bevel on the front edge of the table by maybe 1/32″ every time we push it forward. Not a big deal – it works fine, and you can’t hear the fence hitting that edge over the noise of the saw and dust collection anyway (and you get used to the feel of it after a cut or three).
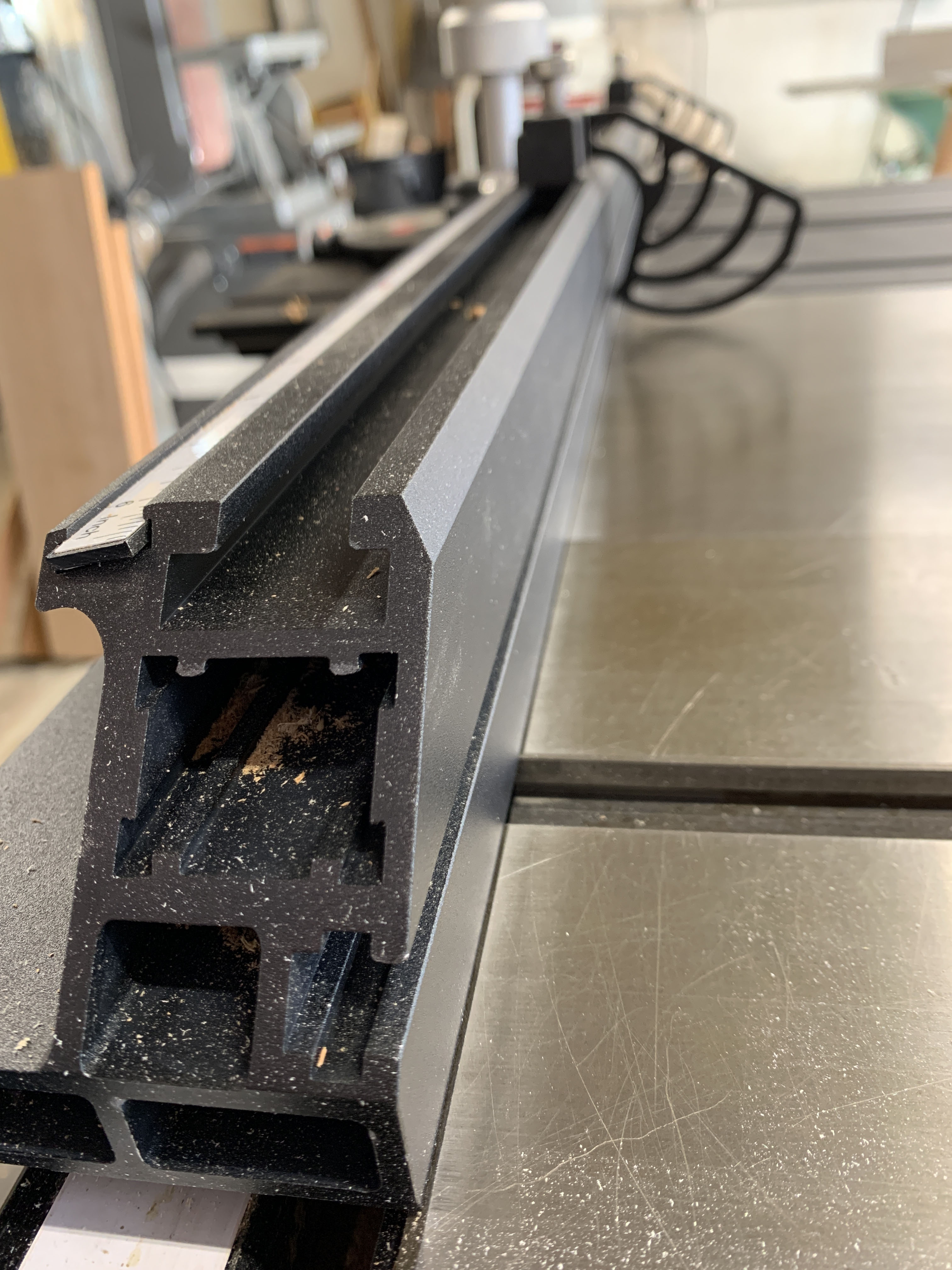
Among the nice things about this sliding table is that it can be pulled back far enough to allow us to stand in front of it for most rip cuts – which means we don’t have to take it out of square to get it out of the way for most rips.
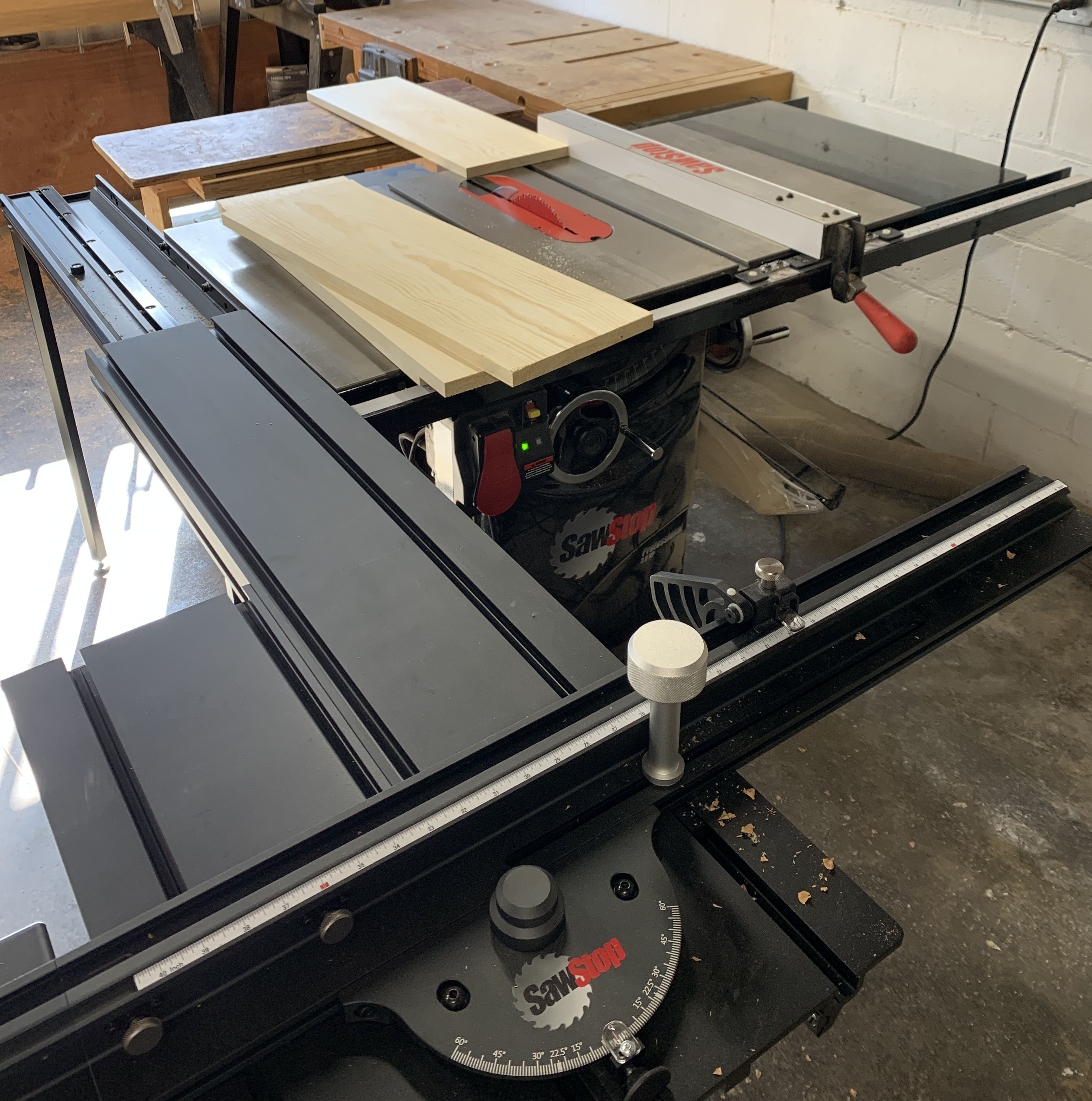
Getting this one back to square is a lot easier than on my JessEm Mast-R-Slide at home, which requires Allen wrenches to adjust the setting blocks. This slider locks in place not against a block, but in the T-track. So all you need is a framing square to set it square to the blade. Still, once you have it square, why move it unless you have to?
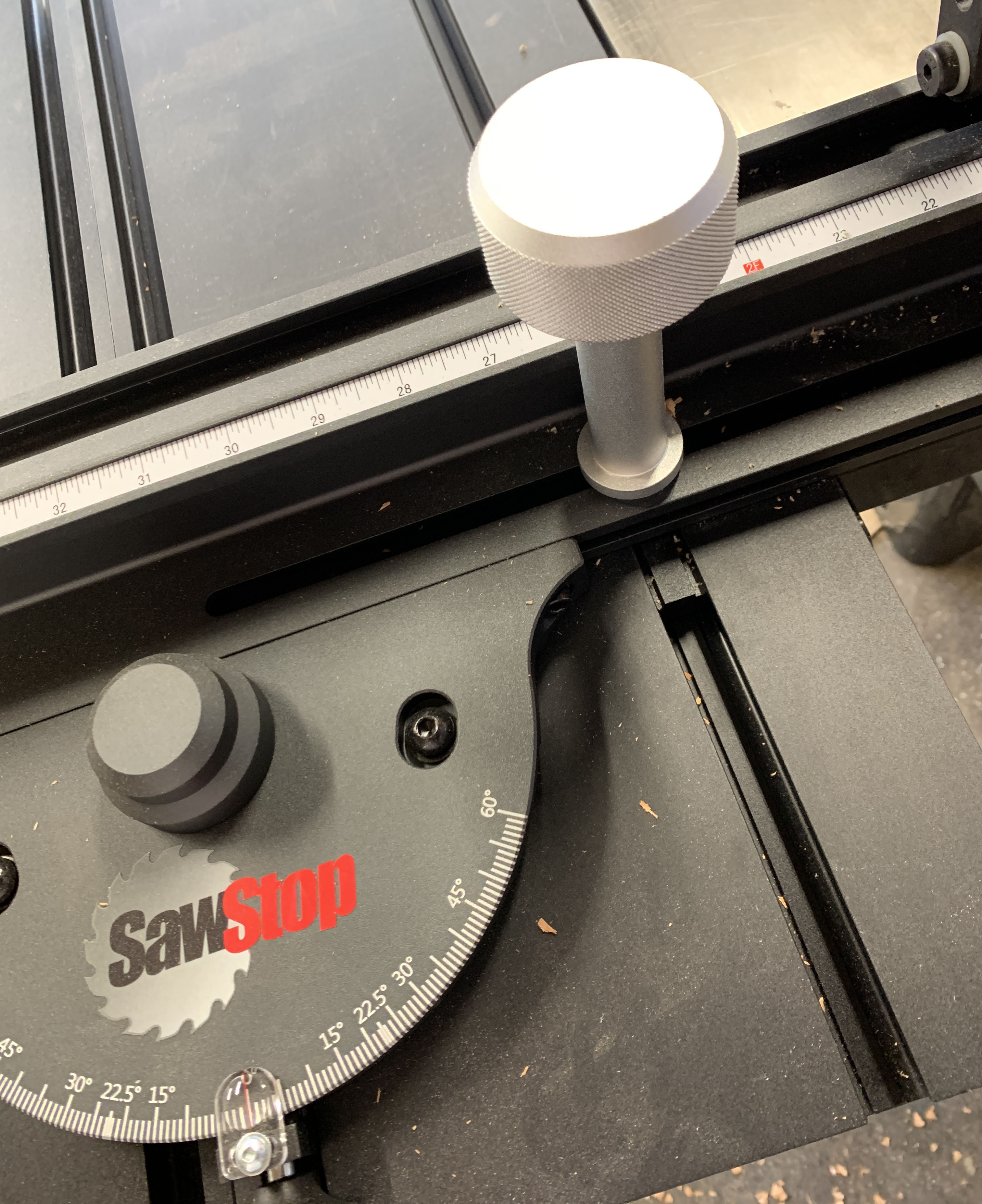
I’ve heard a few complaints about the flip stops on the fence slipping or bending, but I was taught to always gently push my stock again a stop, so I haven’t had any trouble with the stops losing their settings so far. I also had one person mention that if you have a substantial angle set, the end of the fence is far away from the blade. Ninety-nine percent of our cuts are at 90°, so we’ve not yet had to tackle that issue. I imagine that whomever has to make that first 45° cut will make an auxiliary fence that fits in the fence’s T-track.
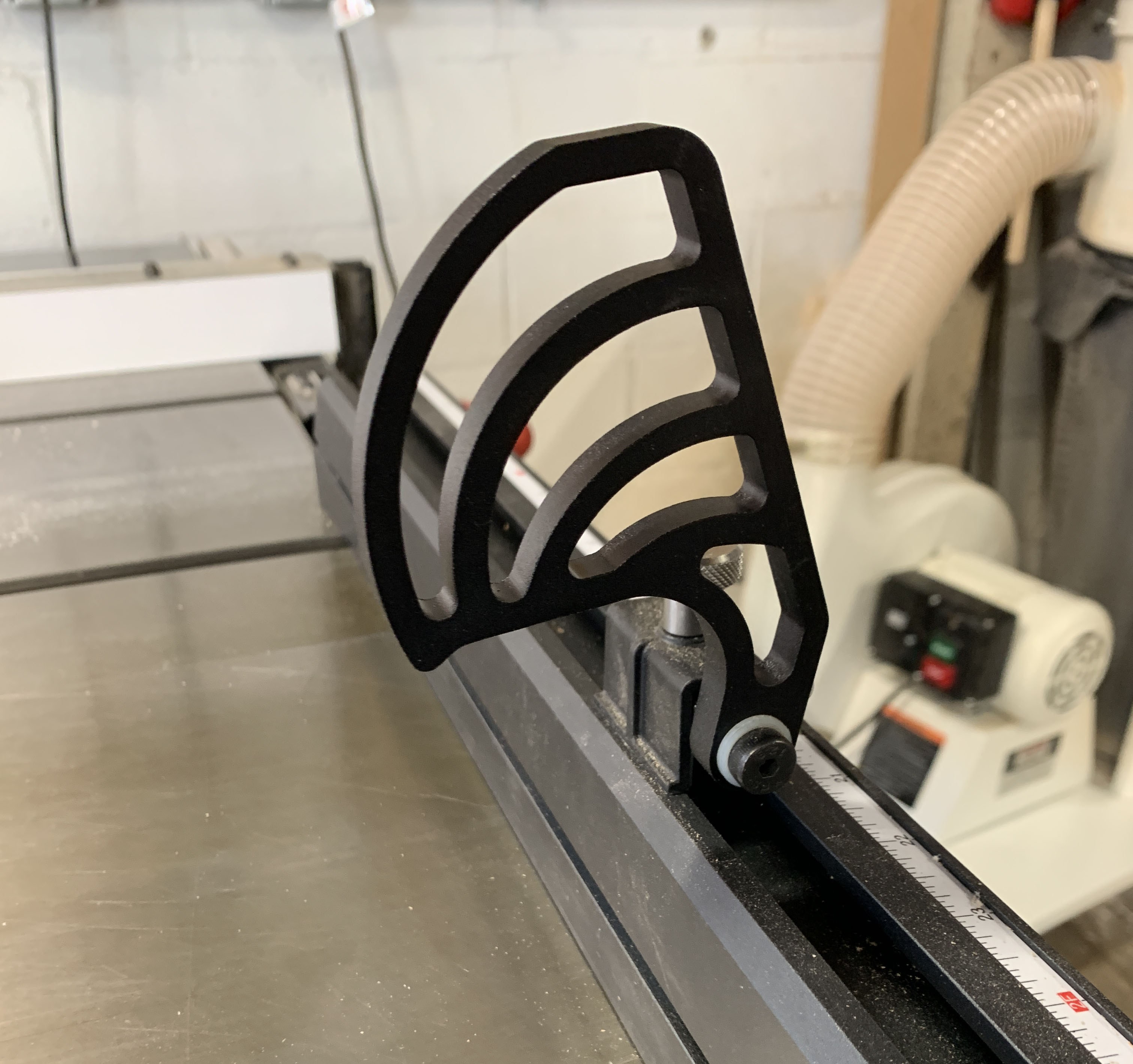
In addition to the extra support and ball-bearing sliding action, what I like most is the flip stops. It used to be I would crosscut one end of all my stock, then clamp a stop to the sled to cut it to final length. I save a lot of time now by simply flipping the stop up to square one end, then flipping my stock, and putting the stop down to cut the second end. Heaven. I’m very much looking forward to finding out – hopefully in the near future – how much easier this new setup will make cutting stock for seven tool chests at a time!
Nice! Could we get a short video of it in use to show its benefits?
I know you use machinery, but it’s always weird to see them in your shop.
I wonder if you could acquire/make an extra T shaped piece of bar that firs neatly into the table’s channel as seen in your fifth picture down, or second picture up from the end. Bore and thread a hole in your newly acquired piece of T bar, and fit an allen headed grub screw through from the bottom of the ‘leg’ of the T (which is ‘upside down’ in use, if you get my drift). Then get the fence square and lock it in place with the knurled knob, slide your new piece of grub-screwed T profile bar up to the bar the knurled knob is attached to and lock it in place with the grub screw, or screws if you can fit more than one.
If the idea works, you now have a fixed point to which to set your fence for a 90º cut. To be honest, I’ve never used either a SawStop saw, nor their fence, but thought I’d throw the idea in to see if it’s got legs. Setting stops of this type, or similar, are common/normal on saws I have used, such as Altendorf, SCMI, Wadkin, and the like.
That’s sort of how the stops on my JessEM slider at home work…but they go out of square with some regularity, I think from simply pushing the fence up against them every time I need to take it back to 90° (which is after every rip cut – you can’t get it enough out of the way to leave it set).
Well, it was a thought, but a small modification might be an additional threaded hole in the channel of the table into which the grub screw of the additional piece I suggested screws. That way, the new 90 degree setting stop can’t move, but can still be removed if required. I know how irritating it can be if it’s not possible to easily set a fence to a required position, in this case to 90 degrees to the saw blade.
Good report! Question, does the sliding table bolt to other cabinet saws, or just the SawStop? How about the Jessem you have at home?
Thanks in advance!
The SawStop is made to fit only the company’s saws. The JessEM is no longer available, but yes, it does attach to most cabinet saws (as do many other aftermarket sliders: Shop Fox and Grizzly are among them).
Thanks for the update. I’m very close to upgrading my old Emerson-made Ridgid to a Sawstop. I doubt I’ll have room to add the slider, but it’s still good to learn more.
Only problem is the slider is not next to the blade, suppose if you already have the saw and don’t want to start over then your stuck with that solution but for the about same money you can buy a proper used slider and for about the same you could buy a hammer slider which does everything with perfection.
I still feel like this kind of slider only makes sense if you already own the saw and would like to add the slider to it. If you’re buying brand new, you’d be better off with a Hammer or Minimax which doesn’t have the inherent design weakness of such an extended sliding mechanism.
Hammer will set you back big bucks.
I have the same combination and am very happy with it. The only thing I feel Sawstop missed on is the configuration of the flip stops. I put a sacrificial fence on the front of the sliding fence that lets me move the fence to the left a bit and still reach the blade. The last couple of inches are only about 3/4″ high so it’s easier to use the dust collection blade guard.
The problem is that with the sacrificial fence the flip stops don’t reach the table anymore which makes them useless for 1/2″ stock on down. You can get around that by fabricating a larger piece that fastens to the front of the stop. Since the sliding fence is obviously designed to mount a sacrificial fence I would have thought that Sawstop would have designed the stops to work with one.
One observation/clarification. If you are leaving the side wing on, with newer sawstops you do not have to cut the fence rails.. I did not have to on my new saw.
Also I reversed the heads on a couple Bessey clamps and placed one end on the floor and the other on the slider. I was able to set the slider height and level to spec.
Good to know re the fence rails on the new ones. Chris’ table saw is a few years old.
Seven years to be exact. It’s a PCS SawStop purchased in August 2013. If you Google “schwarz” and “SawStop” you will receive a crap-ton of misinformation. And so I’m going to take a second here to say a few things out loud again.
I have not sold my SawStop. This is the same SawStop from August 2013. If you want to know my opinion of the saw, here’s my account after 33 months. https://blog.lostartpress.com/2016/04/16/33-months-with-a-sawstop/
I do not have any connection with Highland Woodworking, except as a customer of theirs. And they are a customer of LAP. I buy their tools and they sell our books. I don’t get a discount; neither do they.
I think that most people who read this blog know that I am not for sale. And I never have been. I put this comment here in the hopes that some poor soul from SawMill Creek or Lumberjocks might find it.
Chris
Question for you having read your 2016 blog post: How do you feel about the ICS vs the PCS?
I haven’t used the range of saws you have, but I’ve got a fair amount of time on both McMinnville 66’s and Unisaws of various vintages along with both PCS and ICS SawStops. I’m wholly in agreement that the PCS compares unfavorably to the vintage iron, but I think the ICS pretty well holds its own.
As I see it, ’til you put the 3hp motor in the PCS and upgrade the fence (I see you didn’t; I’ve never used one with that fence, so I can’t compare), you’re only $1,000 short of the ICS.
I’m sure you did your homework when you made the purchase, and I’d be curious to know a little more about your choice.
Thanks,
Eric
I’ve set up and used a lot of ICS saws. They are much better than the PCS line. When I bought mine, I was way too poor to afford the upgrade to the ICS line. I needed a saw to make sure I kept my fingers. And make a living.
I can’t compare the ICS with an old Powermatic 66 (or other old iron) because the ICS is a moving target. We had one for a year, but that was when they first came out. They have gotten a lot better since then. But I don’t know how much better. I’ve worked on all the ICS saws at MASW. They’re great. But they have also seen a lot of loving maintenance.
Bottom line: Today I would buy an ICS in a heartbeat. The finger-saving tech works. And the saw is definitely good enough for professional work. Hope this helps.
Thanks for sharing your thoughts, and sorry for resurrecting a 6 day old comment chain! I was catching up after coming back from vacation and didn’t realize it 🙁
No problem. A six-day-old thread is nothing when you’ve been blogging since 2005….
If you don’t mind my asking, am I missing something regarding SawMillCreek and Lumberjocks?
There is a lot of speculation and misinformation that gets spread on all messageboards (not just those two and not just woodworking boards). It’s just the nature of the medium – most of them don’t think to ask the person they are gossiping about to answer the burning questions of the day. My hope is that by putting out the answer here that someone might find it.
All tools or addendums to tools are labor saving devices. Before tools we gnawed things apart. Makes my jaw hurt thinking about it. Sliders of any kind whether store-bought or cobbled together are there to ease the pain of our work. Some just do it exceedingly well. Bravo SawStop!
Hi!
I’ve got the grizzly slider, which is the same extrusions but different features.
I take mine on and off frequently and made some modifications to make it square up every time I do without a square. It works so well that I can do the 5 cut method and be within a few thou over 60″ after months of use.
https://youtu.be/RNef69nAtqI
Crappy one handed video, but it’s really a great upgrade. I doubt a similar mod is worth the time for you guys but I love it.
I looked at it but there were a lot of complaints about a lack of a positive stop at 90 degrees. People found the fence could slip out of square ever so slightly without that indent in the adjustment gauge to ensure a locked position.
The current models have detents at 90, 45 and a number of other settings that I don’t remember. The only time I have to double check is when I’ve taken the fence off and put it back on.
Thanks I wasn’t aware they had added the feature. It’s been a few years since I had considered one
Good to know re the fence rails on the new ones. Chris’ table saw is a few years old.
This post makes me happy. Not because I have or desire to own a slider, but because I like stories about high quality tools that do the job they were intended while making life easier and most important put a smile on your face.
For anyone who cares, I don’t own a table saw. I do all my ripping on my powermatic 14″ bandsaw and cross cutting with a scms. Anything larger I use a festool track saw. As a professional musician I felt the bandsaw and track saw to be the safer option though seriously considered a sawstop. I’m glad I didn’t get a table saw cause my shop is only 10×14, and am really enjoying hand tools.
Fitz, have another look at your Jessem. I take the fence on n off mine 10 times a day and never have to square it. The blocks are locked in the channel. The 2 big knurled knobs top middle are undone to remove it and tightened to replace it. No adjustments required.
Maybe mine needs a new block, then. It goes out of square every couple of months. (But I will also say it takes me some fumbling to find that darn hole EVERY time I need to screw the right-hand knob into working position. You’d think it would be second nature by now, but no.)
Do you change the blades from rip to crosscut, or, just use a combo blade?
We use a Freud combo blade. We have a rip blade that I use for some joinery applications.
A million years ago when I had to work with sheet goods (a lot) we also had a blade for that.
The way I work is that I do not ask the table saw to produce a finished cut. Every surface gets subsequently handplaned. All the ends get shot. We want our machines to produce surfaces that are flat, square and parallel. The planes take it from there.
Great to hear they made some updates. I have had slider mine for maybe 5 or 6 years when I got my first saw stop. The slider is just awesome. Its no altendorf but is really versatile. I use a sacrificial fence almost always, just simple plywood with two F clamps. It is really fast and easy to square up with a framing square, I leave one hanging on the right side of the rip fence rail. Better to check it than rely on some kind of stop that could go out of adjustment.
The flip stops are garbage at least on mine. No manner of adjustments makes them not wiggle side to side. If I use a stop block I just clamp one on.
My slider fits to the wing as well. I added a spacer so that I didn’t have to cut the tube (I wasn’t sure I was going to like it). Mine clicked as well, but I found a fix that at least works for me. Undo the two screws that allow you to adjust the length. Lift the right hand end as much as possible and tighten the two screws. Make sure the knurled knob is loose and see if you clear the table. Hopefully you will. Now make sure that the screw that attaches to the knurled knob is screwed all the way in from the bottom. Now tighten the knurled knob and hopefully you’ll clear the table from now on.