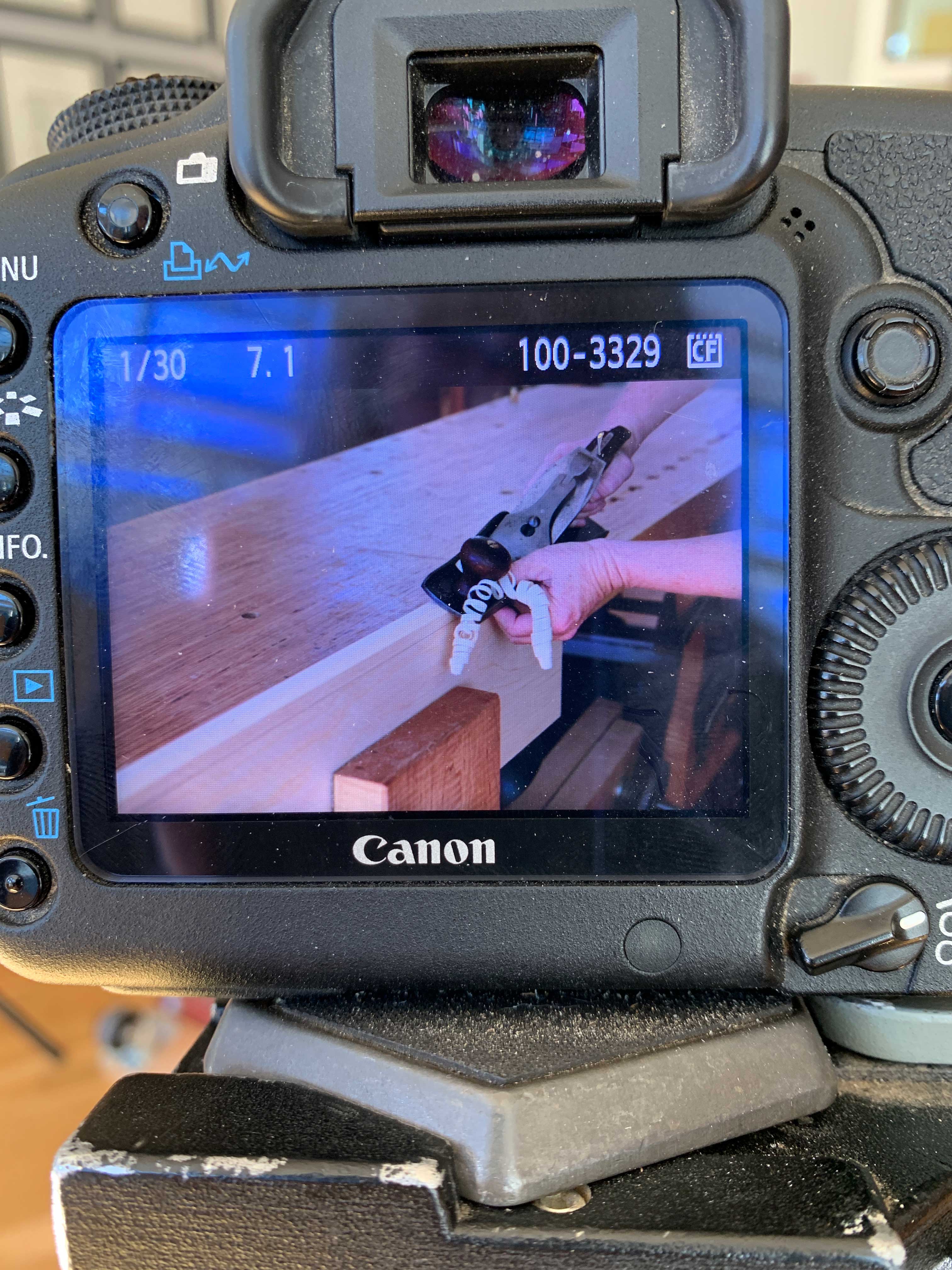
My biggest stumbling block in getting started on my forthcoming Dutch tool chest book was (and remains) the camera. At Popular Woodworking Magazine, we had a fancy camera (we took our own step photos), but I always used it on the fully automatic mode. And I haven’t taken a photo with anything other than my phone since 2017.
Neither fully automatic mode nor phone snaps will fly for a book. I had to learn how to use at least a few of the bells and whistles on Christopher Schwarz’s Canon 5D, make friends with his ARRI LED light setup and, perhaps most important for me, learn how to zoom in on a particular spot to set the focus in live view (I have bad astigmatism and need new glasses).
It’s all so fancy (to me).
Chris was kind enough to give me a crash course and answer many inane (and repeat) questions as I got started. A week later and I’m having fun playing around with depth of field, shadows and blithely switching between a 2-second delay and a 10-second delay as needed. And yesterday, I learned how to hook up and use the remote shutter release! (I realize that doesn’t sound at all impressive, but the last time I used a remote shutter release it was a threaded shutter release cable for my father’s circa-1960 Asahi Pentax SLR that I used in college. And it was about three decades old by then.)
But I think I have it under control. With all but the lid finished on chest No. 1, I’ve managed to reduce the number of not-quite-right shots and the time to get a good one. On day 1, it took me at least 15 minutes to get the “right” image. I’m now down to about 5 minutes per. But at 5 minutes per, it sure takes a lot longer to build things than simply, well, building (a fact I’d managed to forget in my three years since PWM).
My plan is to discuss every reasonable approach to building these chests (and in the offing teach many techniques applicable to all kinds of builds), so no matter a reader’s tool kit, skill set or penchant for pre- or post-industrial woodworking, there will be a technique that appeals. That means I’ll be building quite a few chests (both large and small)…or at least parts of chests for close-up photography.
So I hope to get faster still with the photos – and better at deciding what to shoot and what not to (right now, I’m shooting almost every step). Otherwise, I’ll be done before the book is.
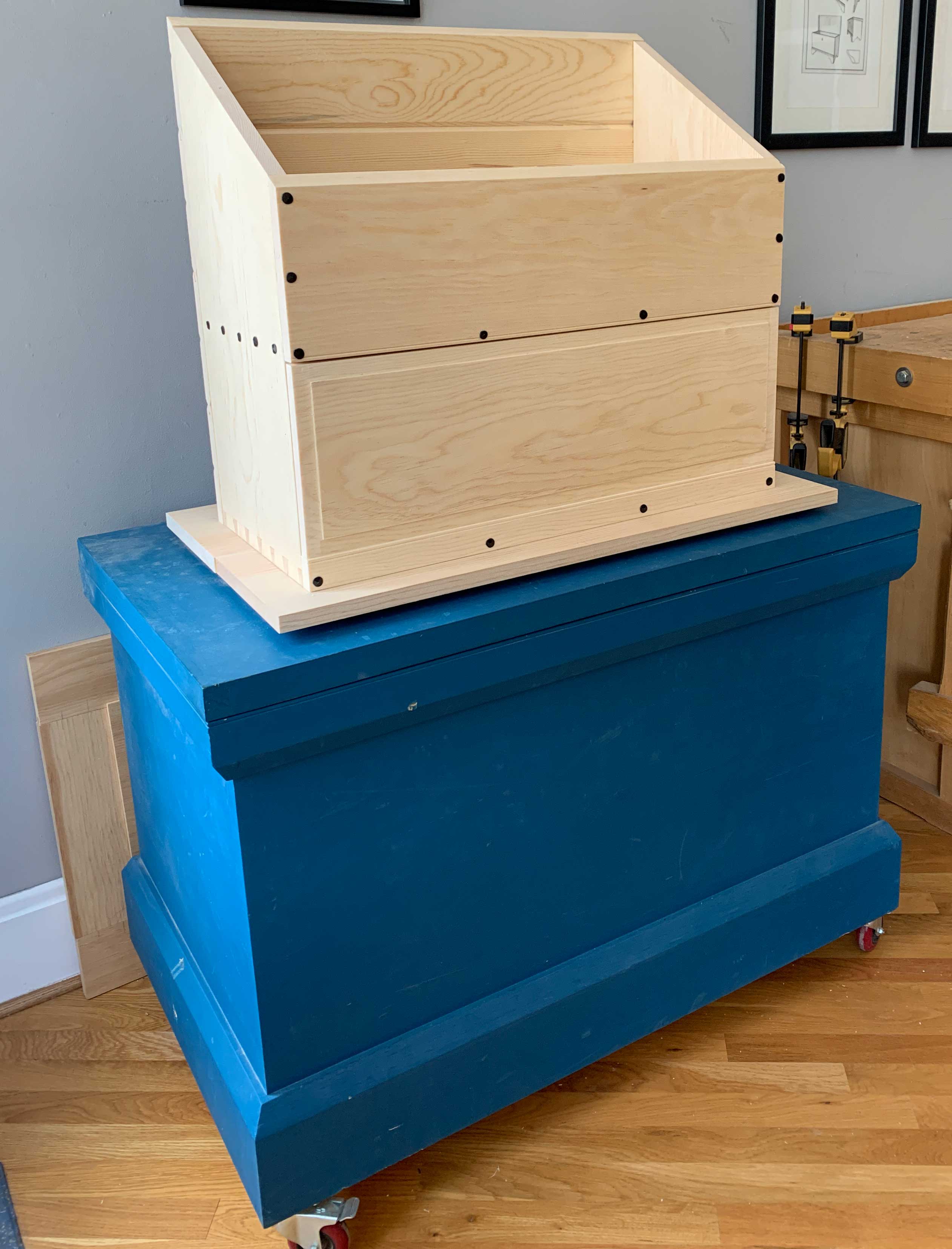
— Megan Fitzpatrick
Looking forward to ‘De Gereedschapskist Van Anarchist’ !
I have bought into the need for a dust seal on the ATC. So why isn’t there a dust seal on the Dutch chest. Is history more important than function?
There will be a chapter on weather-stripping. It will give you an excuse to buy that vintage Stanley 238 you’ve been wanting.
No tool chest book is complete without this chapter.
No reason you couldn’t add one – same approach as on ATC
I have built three of the Dutch style chests and never had a problem with dust. All three lids are slightly different: one has breadboard ends, one has battens on the top, and one has battens on the bottom. What all three do have in common is the hinges are inset so the lid actually falls neatly (mostly) on the entire perimeter of the top leaving very little air gap.
One thing you will both curse and bless yourself over is the lack of a flat top on which to expediently place Stuff.
One other observation is that these chests sit above the normal plane of dust bunny procreation. The top is above bench height when placed on whatever the user contrives for easier access to the lower bay. My experience is that dust is generated at bench height on power and hand tools.
The open faced boxes two of my chests are placed on always need to be cleaned out.
I built the first chest as a stop-gap until I could build the full ATC. I am happy with what I have and am not going to build the ATC. I’m looking for another project to use the ~100 board feet of Sassafras formerly earmarked for the ATC.
I am looking forward to this book!
Megan, please consider at least mentioning the option to hinge the lower panel to the chest. I hate loose pieces, you have to find a place to keep them, not lose them, and not bury them with other things…
I thought I had a photo of mine, and will get one if you’d like. I used simple hardware store hinges at the bottom, and made a toggle to hold it closed. It’s a one-handed operation and I think it is much better.
Just saying.
Certainly worth mentioning!
Step photos? I guess these days even cameras come from broken homes.
Any thoughts on a shallower slope for the lid? The whole point is to make it impossible to store things on top, which I love. I’ve often wondered if 15 or 20 degrees might offer a little more usable space for something like my sliding till.
On the dust seal question, I suspect it’s a case of keeping construction simple and getting back to building furniture as quickly as possible. I can’t imagine that a dust seal would be but maybe 5% better than a simple lid. Not worth the effort on a quick build like the dtc imo.
FWIW, I’ve seen it argued that the slope is also there to sluice rain. But yes, I suppose the slope could be more shallow. (I find the low front an aid in lifting the thing, though that may be a personal issue.)
I also found a useful addition to the lid was to put a small batten roughly 1/2 – 3/4 inch high horizontally at the bottom of the lid to act as a useful place to rest an open book. Certainly not necessary, but the angle of the lid was just asking for an accessory and it looked too much like a book stand to not give it a try. Then with wheels on the bottom of the chest I can wheel the whole chest over and after I pull the tools I need out I use the top to place drawings or a book.
I did the exact same thing on two of my chests. I use the reading ledge all the time.
It sounds that you are going to give us a great book can’t wait !!!
Megan I haven’t used my Pentax 1000 for pics in many years. I use my phone for all my pic’s and video. You have seen some of my pic’s and videos on my country woodwright FB page. I can feel your pain as you try to get the right shot with all the detail that you need for a book. So I guess your build time is more like 25 hours instead of the 16 hours.
What is that fancy word for making the background blurry and the subject sharp?
Depth of field (shallower depth of field, larger aperture…which is the smaller numbers, e.g. 2.8)
Hi fitz, everything you wrote is correct, I think, except for “greater depth of field”. Shouldn’t it be “shallower depth of field”?
Shoot — you’re right! I’ll fix that.
I was trying to think of a word from the Fancy Lad School of Woodworking Photography. Something Japanese. “Bokeh” perhaps. Ask Chris. He should know.
Thomas, the word is bokeh.
I’ve never heard that word — glad to learn a new one!
bokeh
I used two turn buttons to hold the front panel of mine closed. I haven’t seen this variation. I didn’t need, or want, the locks.
Exactly what I was talking about.
I’m a tool wall kind of guy. I like to see my tools.
But as I have more woodworking days behind me than ahead
of me, I’ve started thinking about the best way to pass along my hand tools to my family.
I’ve decided that the Dutch tool chest is the best vehicle.
Learning photography is on my bucket list. There are chimps that can take better photos. Anything you or Chris shared has helped.
A professor had a favorite expression that got messed up one day. It came out “cropper tighting.” Uproarious laughter from all the students! I still hear the expression today, and use it myself. This is, in my opinion, the most important thing to learn in doing photography. I can’t release the shutter without thinking, “cropper tighting!”
Bokeh.
Looks great to me! One thing you might think about that I see missing in basically ALL WW literature is the thought process behind sequencing steps. I find this the most challenging part of thinking about project execution. And of course, writers lay out the path THEY followed. But rarely do you see a moment of “Hmmm… I picked this first, because if I didn’t, it would be nigh-on impossible to do XXX later.” Just a thought!
Fitz,
Every time I pull out my phone to snap a step pic I’m happy there are people like you who take the time and energy to spend hours on lighting, f stop settings, composition and a hundred other things that I don’t have the patience to do. What you do inspires me to get in the shop and simply work wood.
A banal question, I know…… what are the black things? Are they black screw heads?
Cut nail heads. These are by Rivierre.
Theyre Nails!
https://blog.lostartpress.com/2016/05/08/the-most-tenacious-nails-ever/
I used cheap steel hardware from the big box store (wish i had bought nicer stuff). After stripping the zinc, I “seasoned” them the same way you season an iron skillet. I rubbed oil on the pieces then baked them in an oven at 350 for about an hour. 6 months and haven’t done anything else to it and haven’t noticed any rust.
Phone cameras produce photos that are good enough for the cover of Time (Hurricane Sandy in 2012 was an iPhone). I imagine it’d be cumbersome to use a phone for documenting the build though. Remote shutter alone is probably worth it!
Mine does take pics that are high enough resolution – but I can’t control the depth of field (much), plus the tripod sure does make things easier! (The only iPhone tripod we have is a tiny one, meant for use on a desktop or the like.)