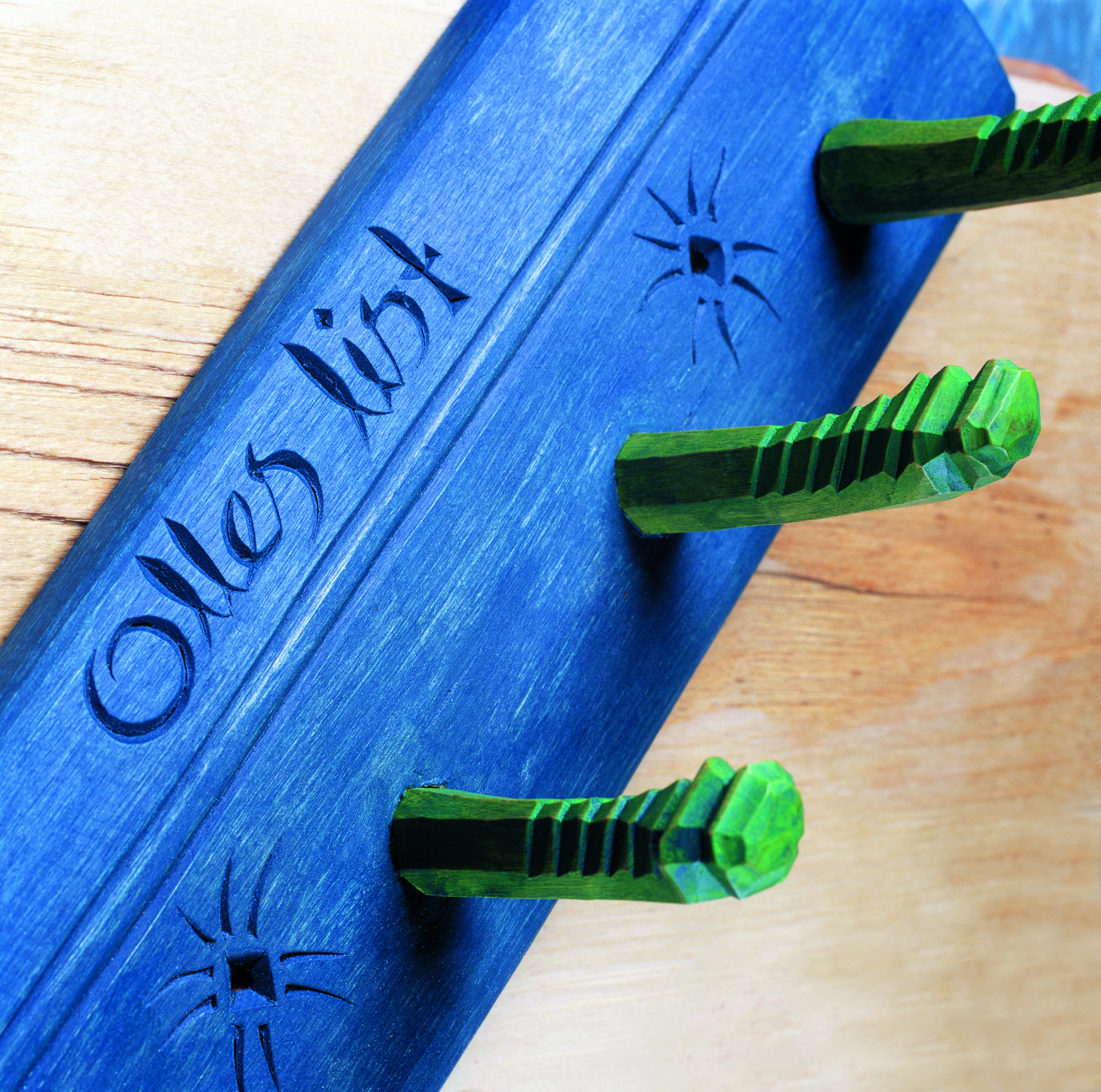
The legend that is Jogge Sundqvist precedes him. I’d heard of him (and of his father, Wille) through Drew Langsner and Peter Follansbee, as had Chris Schwarz and John Hoffman. They’ve had the great good fortune to meet him. I, alas, have not. Yet.
Chris was teaching at the Marc Adams School of Woodworking at the same time as Jogge a few years back, and John was helping out in the class. “I was absolutely blown away by the guy. I didn’t know what to expect,” says Chris. “He’s almost magical when you meet him; he gives off an aura like he’s from another dimension. I got to see his work, and I finally got the whole sloyd thing.”
Chris says he and John would sneak off from their class at every opportunity to hang out in Jogge’s room, to listen to him and watch him teach. “He’s mesmerizing and charming,” says Chris. Jogge says he gets his magic powers from his apron; it transforms him into “surolle,” his artist alter ego. “He’s like a Swedish wood spirit,” says Chris.
After both their classes were over, Jogge asked Chris and John if Lost Art Press would be interested in translating and publishing “Slöjda I Trä.” They didn’t even blink before saying yes.
It took a while to get the contract negotiated with Jogge’s Swedish publisher, but when they did, Chris sent Jogge a note with the good news that “Sloyd in Wood” would be published in the United States. “I’m so happy that if my wife offers me a glass of wine tonight, I will not say no!” Jogge responded.
The following is excerpted from “Slöjd in Wood,” by Jögge Sundqvist.
Peg Board
In my county, chair rail mouldings are common in older, traditional houses. Local people would make peg boards from leftover moulding material. A peg board is a piece of moulding with several pegs. The peg’s tenon must be seated very tightly in the moulding.
If the pegs are very dry, 4 to 5 percent moisture content, and the moulding is 10-12 percent moisture content, the hole shrinks and strengthens the joint. To control the moisture there are pin-activated moisture meters that are handy and time-saving. This construction method, together with the wedge and the shoulder, creates a very strong joint if it is done accurately.
Tools
Axe or froe, drawknife, gouge, knife, chip carving knife, V-tool, brace and bit, and smoothing plane
Material
Dry, straight-grained birch (Betula) for pegs. Hard, deciduous wood for wedges. Green, straight-grain birch for moulding.
The moulding
Split out the peg board from the green blank. Shave it flat with a drawknife in the shaving horse or use a scrub plane and a jack plane at a workbench.
The moulding’s profile should be roughly hollowed out with a gouge in green condition because the wood is easier to work. When it has dried to 12 percent, plane and carve the moulding again to remove any raised fibers or distortion. Decorative carving can be added at this point, for example, a V-shaped notch made with chip carving knife or V-gouge. (See page 47 for more on moisture content.)
Use a rubber band for spacing the peg holes. Mark lines on the rubber band with a ballpoint pen at intervals of approximately 1cm (3/8″). Stretch the rubber band so the markings are evenly distributed across the moulding. Mark holes for the nails or the screws, preferably between the two outermost pegs on each end.
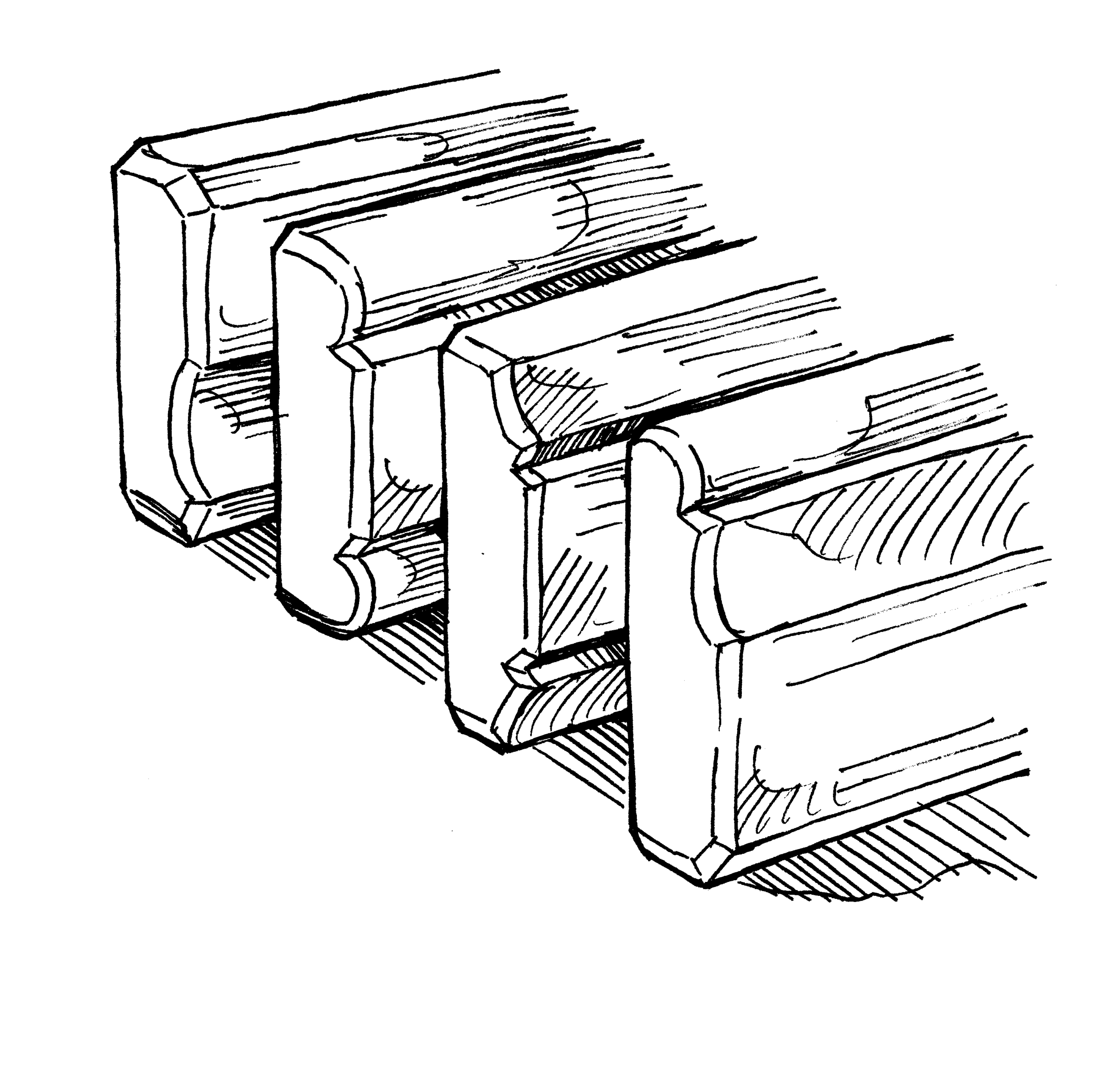
Drilling the holes
Bore from the front of the board, using a brace and bit or a twist drill. In order to bore straight you can tape a line level, which is a small spirit level, on the bit and fasten the moulding horizontally in the workbench. Position your body to align the bit at a 90° angle to the moulding. Bore, checking for level now and then. Stop when the tip of the bit goes through to the back. Turn over the blank and bore from the other side. That way, you avoid ugly tear-out.

Pegs
The peg design can vary. It is a good idea if they are bent up at the tip to prevent the bag or jacket from sliding off. There should be a shoulder on the tenon to make it stronger. If you want, place the shoulder at the lower edge only. If you choose this option, you need a rectangular blank.
You can read more about carving methods and knife grips in the previous chapter. Decorate the moulding before you fasten the pegs. (See Chip Carving, page 96.)
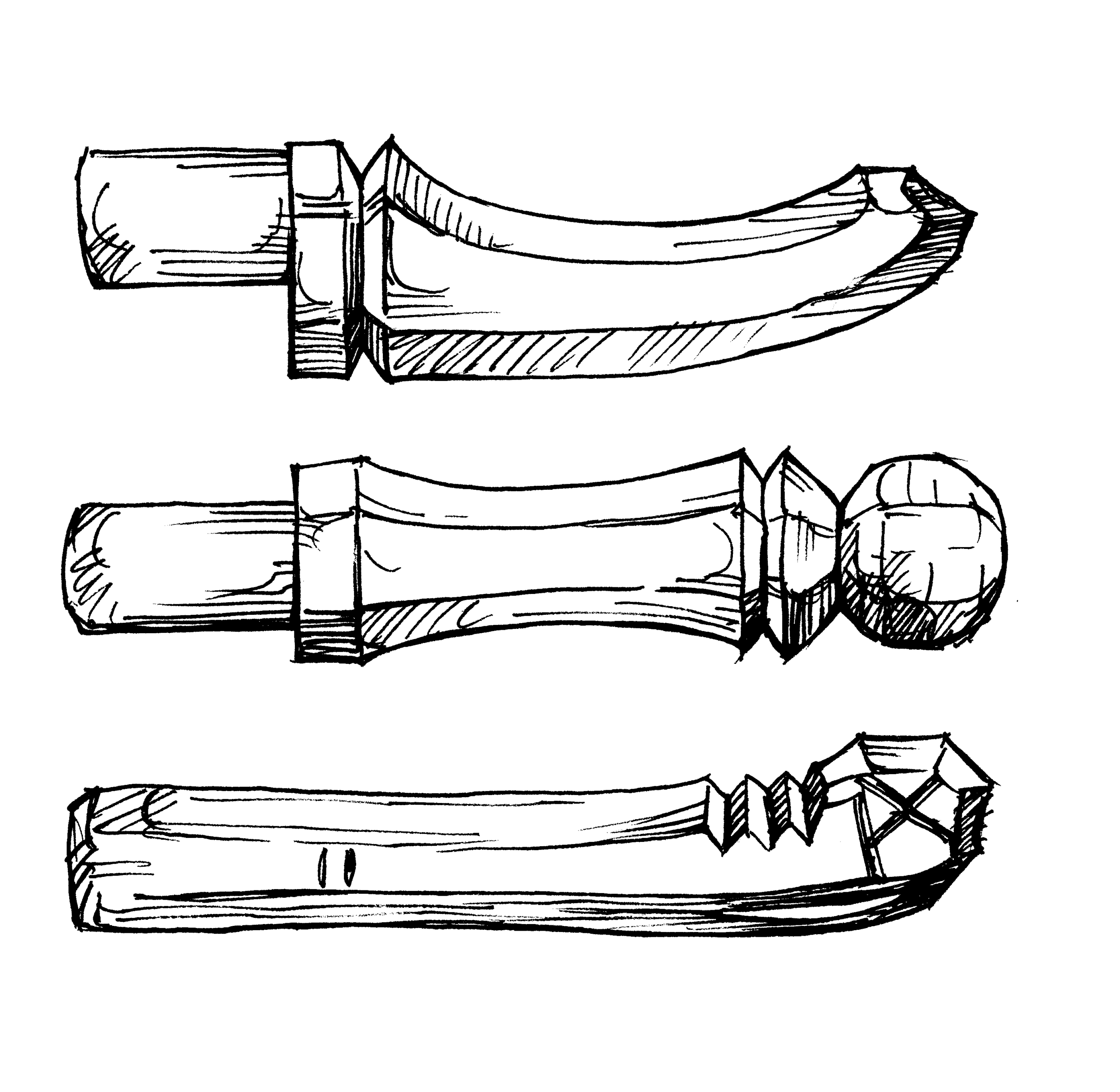
Wedging
Cut out the wedge material from a piece of hard deciduous wood (see page 43 for the properties of woods). The wedge angle should be between 3° and 4° with a secondary bevel at the tip. The wedge mustn’t be concave or convex.
Saw off the tenon, flush with the backside of the moulding. Make a scoring mark on the tenon with the knife at a 90° angle to the fiber direction of the moulding. Make sure it “responds,” that is, that the tip of the peg supports itself on a firm foundation. Add a small dab of wood glue near the tip of the wedge and drive it in firmly until it doesn’t go any farther. With the tip of the knife, scribe a line on each side of the wedge and break it off.
If the tenon is too small, there is a risk of splitting in both the moulding and the peg. Cut the tenons flush to the moulding with a knife or a flat gouge. Carefully choose colors and take the time to paint your peg board using a thin coat of artist’s oil paint.
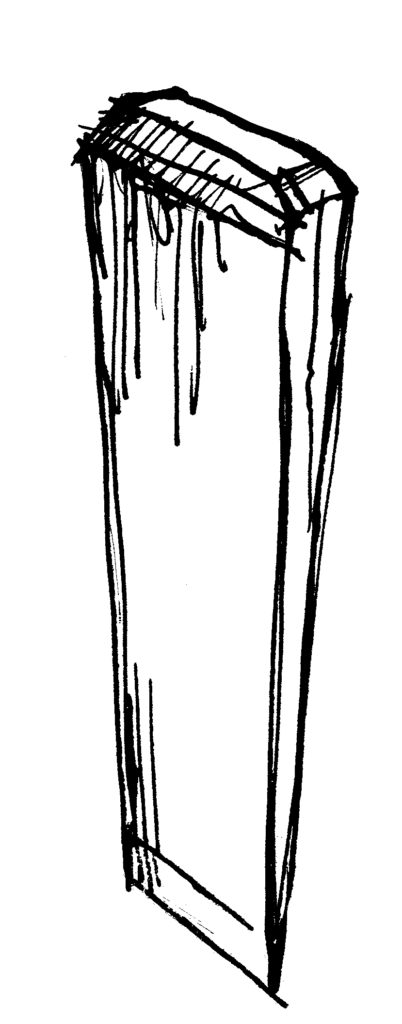

This book is a trove of color-filled inspiration.
guess what I will be making in the shop today…….looks fun.
I got the chance to see Jogge at the Fuller Craft Museum a couple of years ago. I really have no words. He’s more colorful than his book. He’s . . . a rockstar. Incredible show? demonstration? concert? I’m not even sure. But he’s perhaps the only other person I can think of that would be on the opposite end of a stage from Roy Underhill, and cause your head to explode from trying to soak in both.
I was re-reading Wille’s “Swedish Woodcarving Techniques” last week. I saw lots of photos with Jogge as a teen (or earlier) throughout the book.
Jogge has a bunch of tutorial videos on the Morakniv youtube channel.