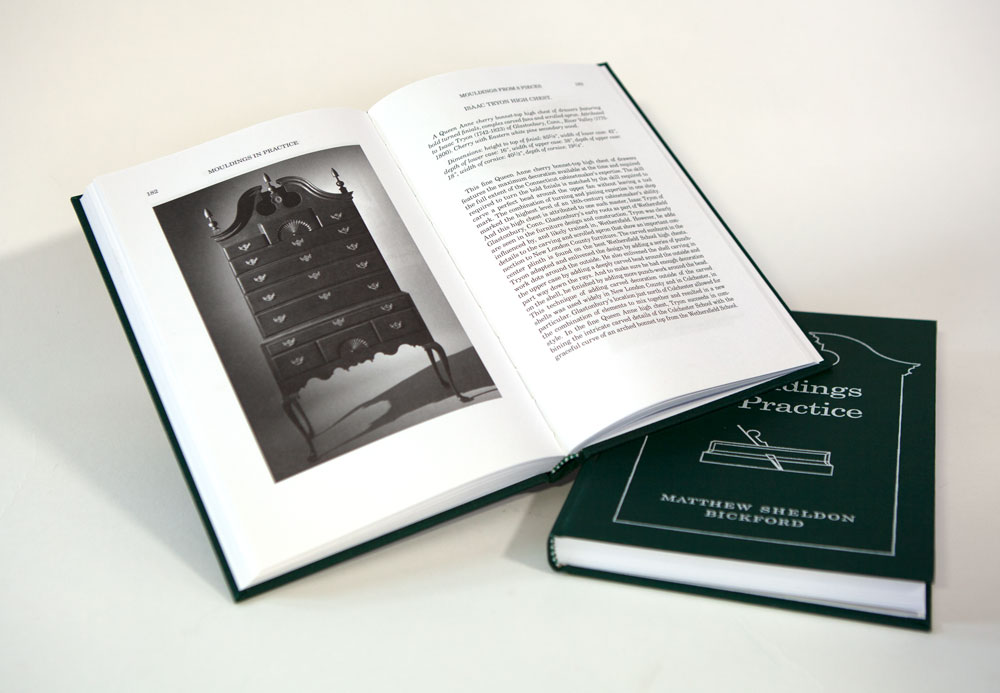
When Christopher Schwarz and John Hoffman started Lost Art Press in 2007, they had a bit of difficultly in convincing authors to write for them. It was an unproven press with a weird business model: share all profits and costs 50/50 with authors, no Amazon or other mass-market outlet sales, books shipped out of their homes (gotta put the kids to work somehow!), no employees…
But at a woodworking show in Albany, N.Y., Chris met Matt Bickford for the first time, and hung out in his booth for a while, talking furniture, woodworking and handplanes. Matt, too, had just started his business, making traditional hollows and rounds and other moulding planes, out of cherry (if you have a cherry M.S. Bickford plane, it’s almost a collector’s item at this point!).
Peter Follansbee was also at the show, so Chris treated Peter and Matt to pizza, and over dinner, cajoled them both into writing books for Lost Art Press. They were the first two outside authors to sign contracts with Chris and John. (I’ll share an excerpt from one of Peter’s book in October).
Matt’s book, “Mouldings in Practice,” is divided into two parts. The first half discusses moulding planes and the principles of how they’re used. Matt shows you how a great variety of mouldings can be stuck with a limited number of hollows and rounds (you don’t need a full set – or even a half set) to get started. Plus he discusses the roles of snipes bill and side rounds, and teaches you how to draw accurate profiles – one of the keys to success.
But what I found most mind-blowing is the use of rabbets in the “workbook” section (the second half of the book). Remove most of the waste with a rabbet plane (or dado stack), and you’re well on your way toward a finished moulding. Not only is there less wear-and-tear on harder-to-sharpen planes, the arrises function as guides for your hollows and rounds. This section includes many common profiles, and how to layout the rabbets to make the work easier. They’re broken down into basic steps that even a novice moulding plane user (me, when this book came out) can follow. What’s below is just the intro.
Excerpted from “Mouldings in Practice” by M.S. Bickford.
— Fitz
When I first became aware of hollows and rounds I read about the heralded “half set.” A half set of hollows and rounds is 18 planes, nine pairs, that incrementally increase in radius from 1/8″ at the low end to 11/2″ at the high end. The half set of planes is generally the even-numbered pairs in the previously referenced chart. (A full set is 36 planes, and also includes the odd numbers.)
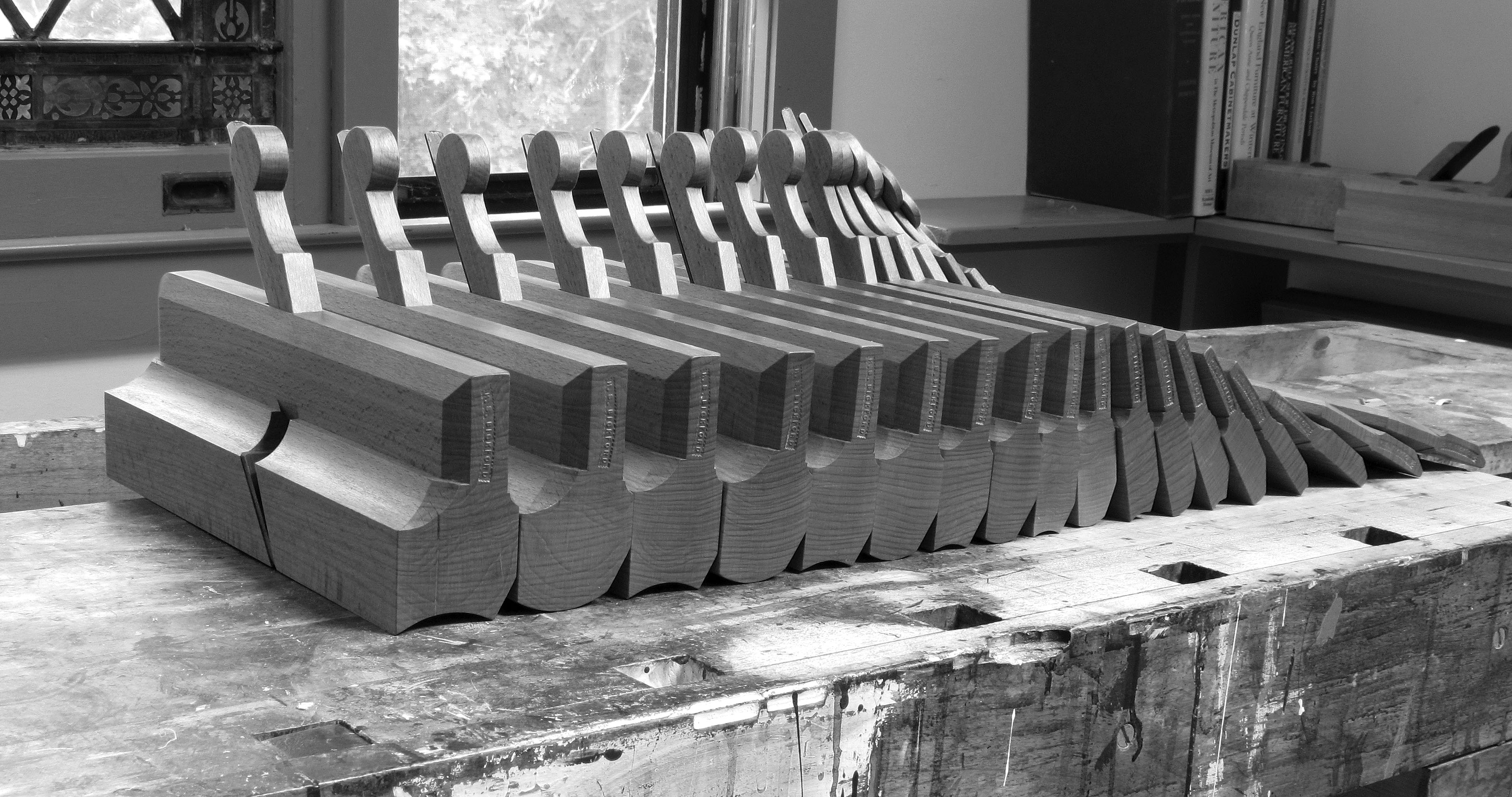
A half set of hollows and rounds is an extraordinarily comprehensive grouping of planes that allows the owner to produce a range of moulding profiles that exist in the smallest spice box and largest secretary. Centuries ago, the half set was often acquired over time.
For many users, myself included, the half set covers an unnecessarily broad range of work, and represents an undue expense. Many woodworkers narrow their plane choice down to match the scale of work that catches their fancy. For example, if you work only with 4/4 stock, then sizes above No. 8 may go unused. Starting with just a single pair of hollows and rounds – and an efficient method to accurately establish rabbets and chamfers – allows the production of dozens of different profiles.
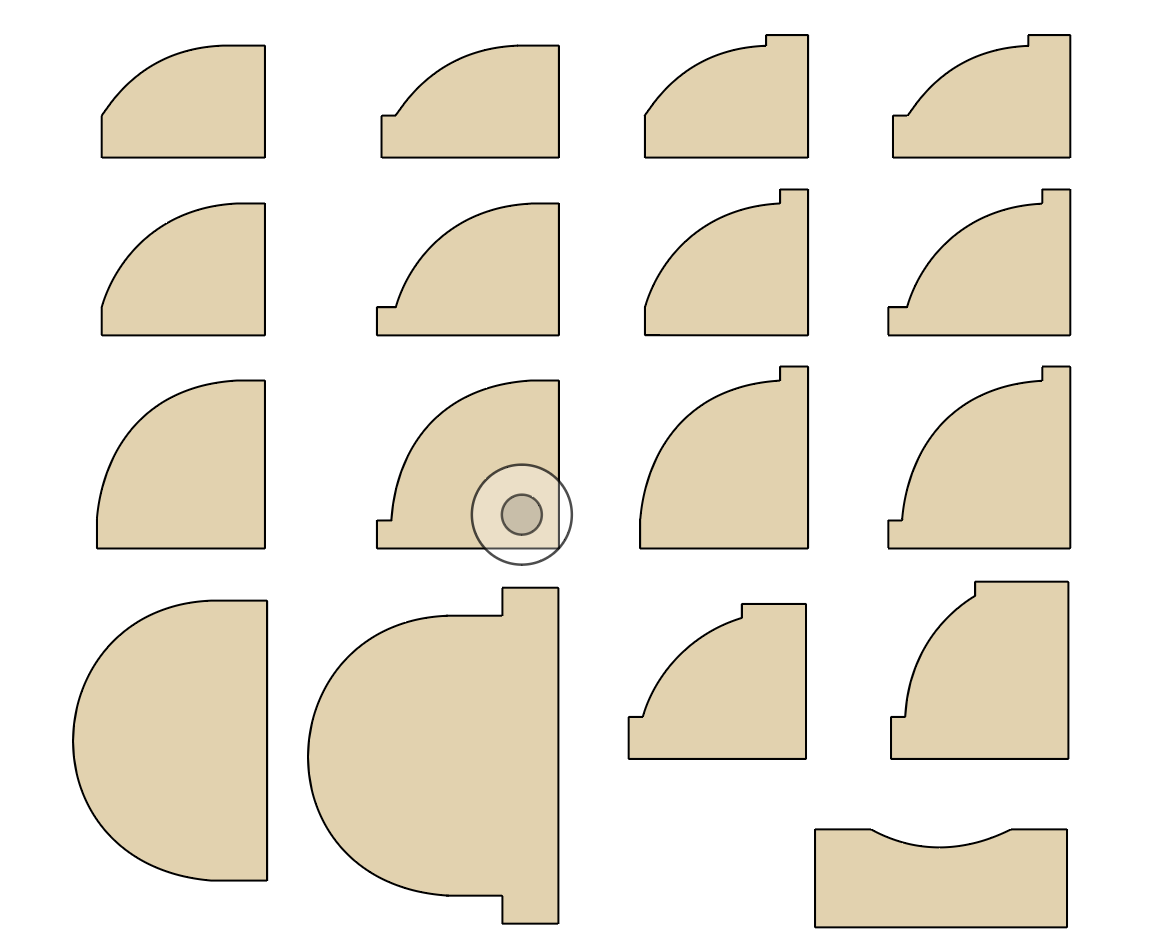

The simplicity of combining only one convex and one concave arc might seem limiting. There are, however, scores of profiles you will be able to produce with just a single pair of hollows and rounds. These profiles will often contain minute differences – adding a vertical or horizontal fillet, or flat, adjusting the size of that fillet, increasing the curvature or changing the general angle of the profile. These small differences are important and are often glossed over or neglected on a router table.
Adding a second pair of hollows and rounds to your tool chest, a step I always encourage, increases the number of possible profiles far more than two-fold. Not only will you be able to create the 41 profiles shown above in two different sizes, you will also be able to mix the concave with the convex to form various cove and ovolo combinations and ogees. Additionally, you can mix concave with the concave and convex with the convex to form elliptical shapes. It is at this stage that you will unlock the true versatility of these planes.
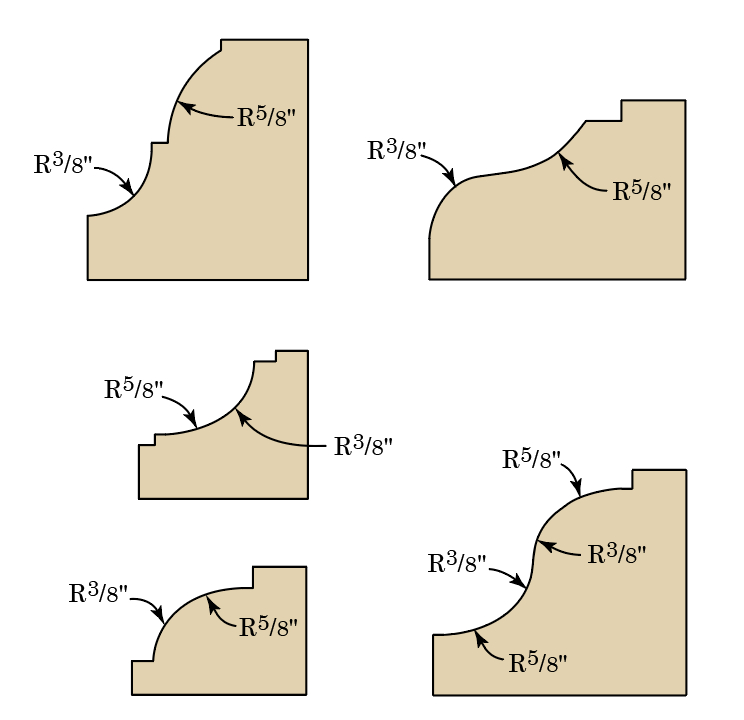
The following are stepped examples of profiles that are primarily made with one pair of No. 6 planes. (A No. 6 was defined as cutting a radius of 6/16″ or 3/8″.) These profiles are a sampling that include the basic shapes, with a few basic modifications. You can combine and scale these to build large, intricate profiles that line and accent a piece of casework or a room.
Cavetto (Cove).
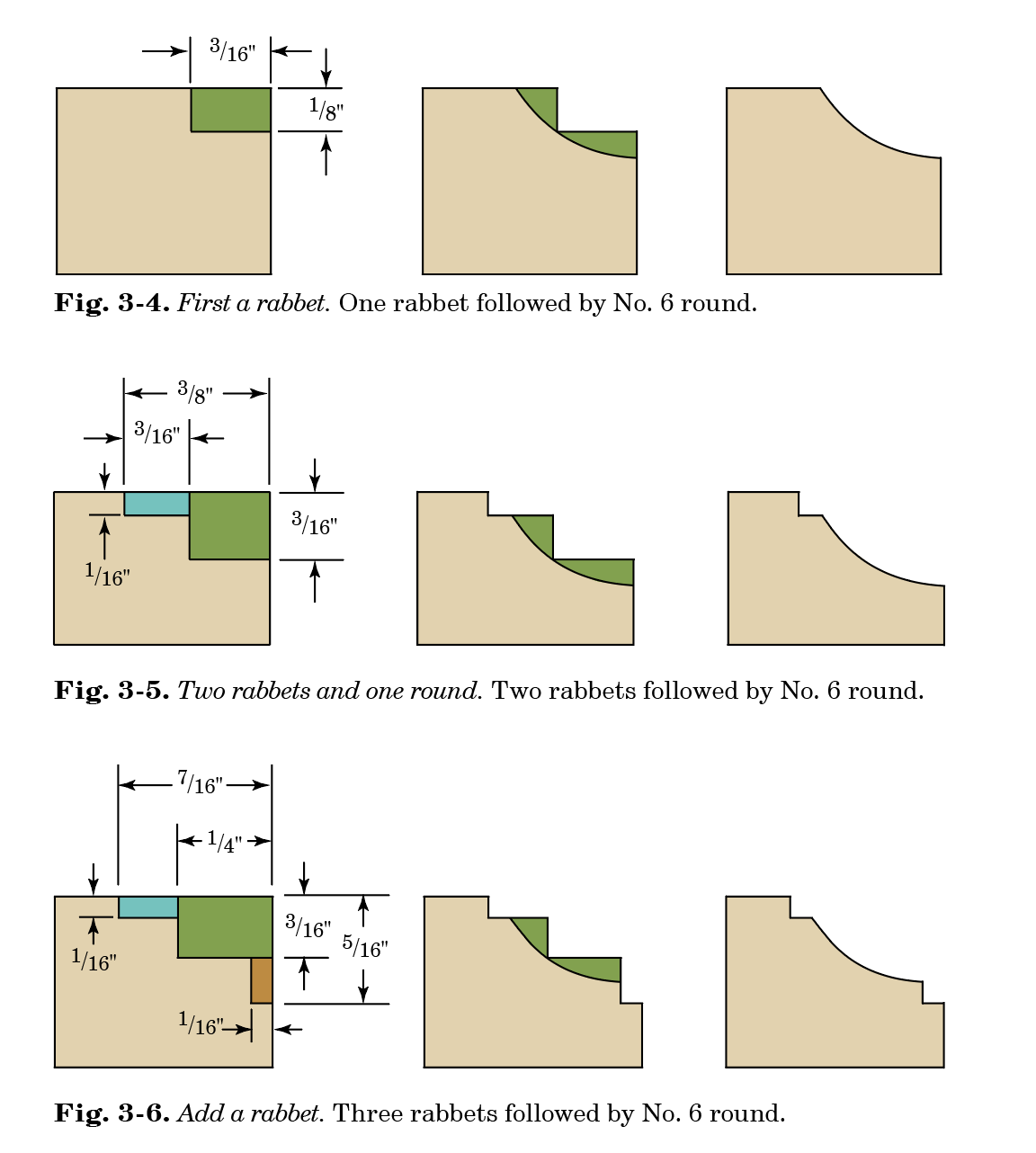
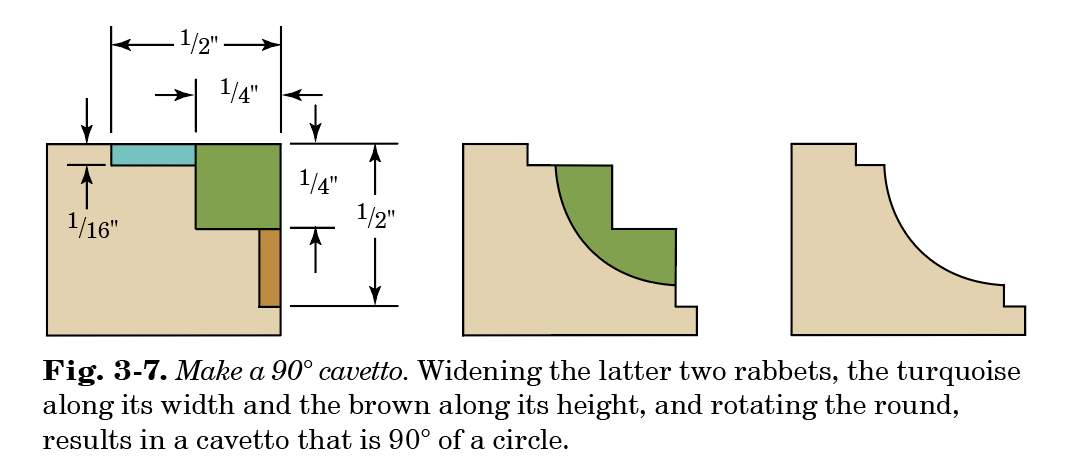
A cavetto, or cove, begins with a rabbet, which acts as both a guide and depth stop for the work with the round plane. The layout and execution of the rabbet will be the focus of much of this book and is discussed in great detail beginning in chapter 4.
Ovolo.
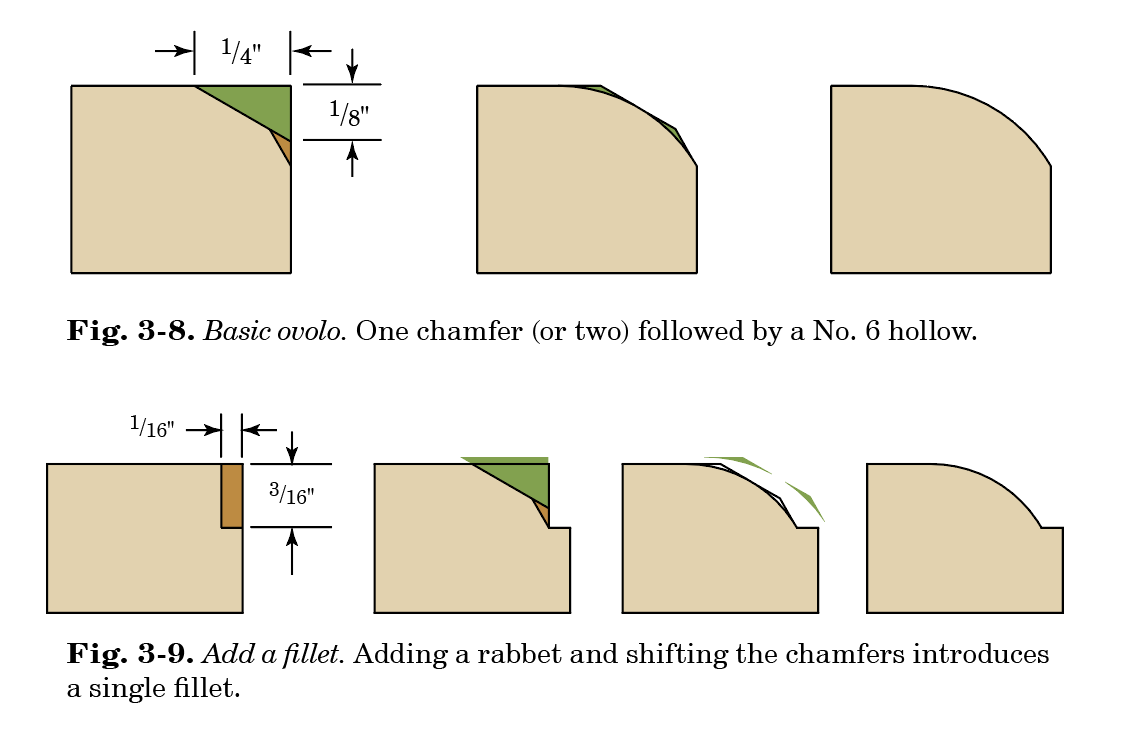
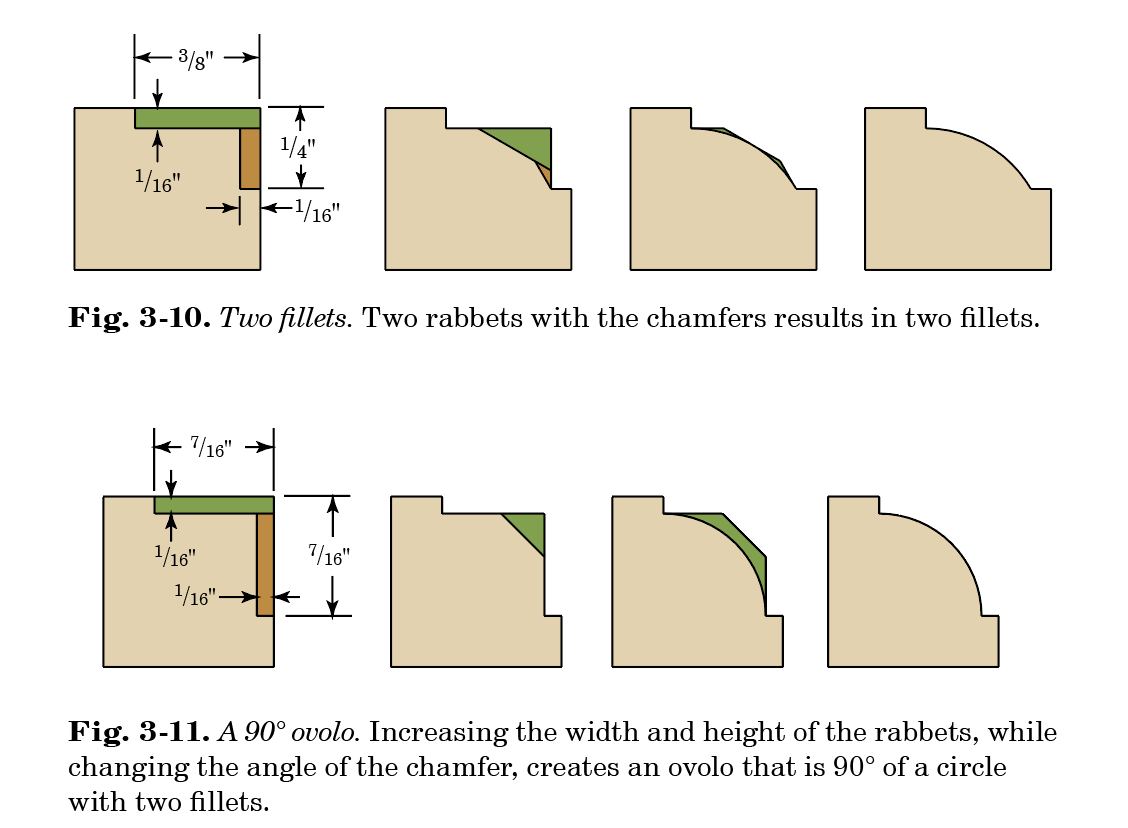
An ovolo, like all instances when you use a hollow, begins with a chamfer. The chamfer, like the rabbet above, serves as both guide and depth gauge for subsequent work with the hollow plane. Again, the precise placement and execution of this chamfer will be discussed in greater detail beginning in chapter 4.
Torus (Bullnose).
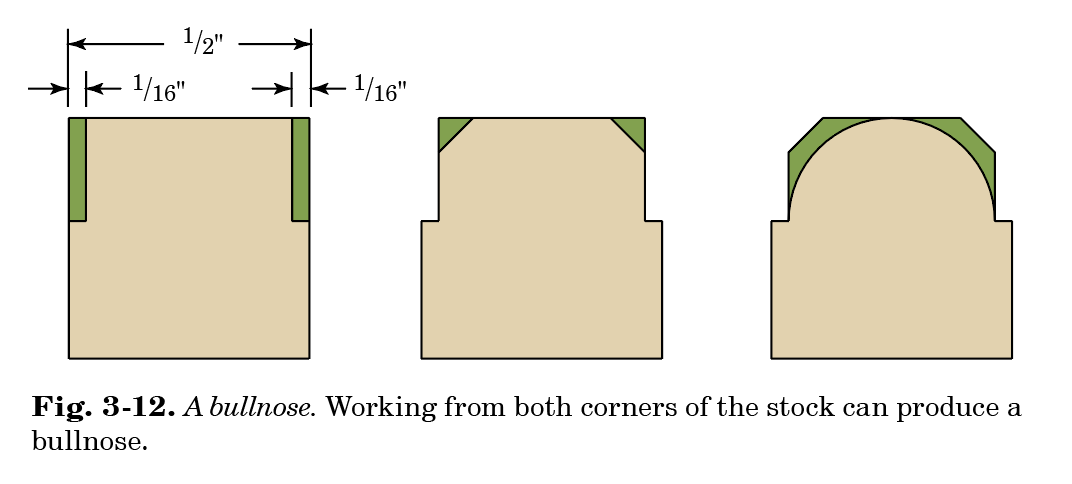
When laid out in this way, two rabbets, two chamfers, and a No. 6 hollow create a bullnose.
Ogee (Cyma Recta).
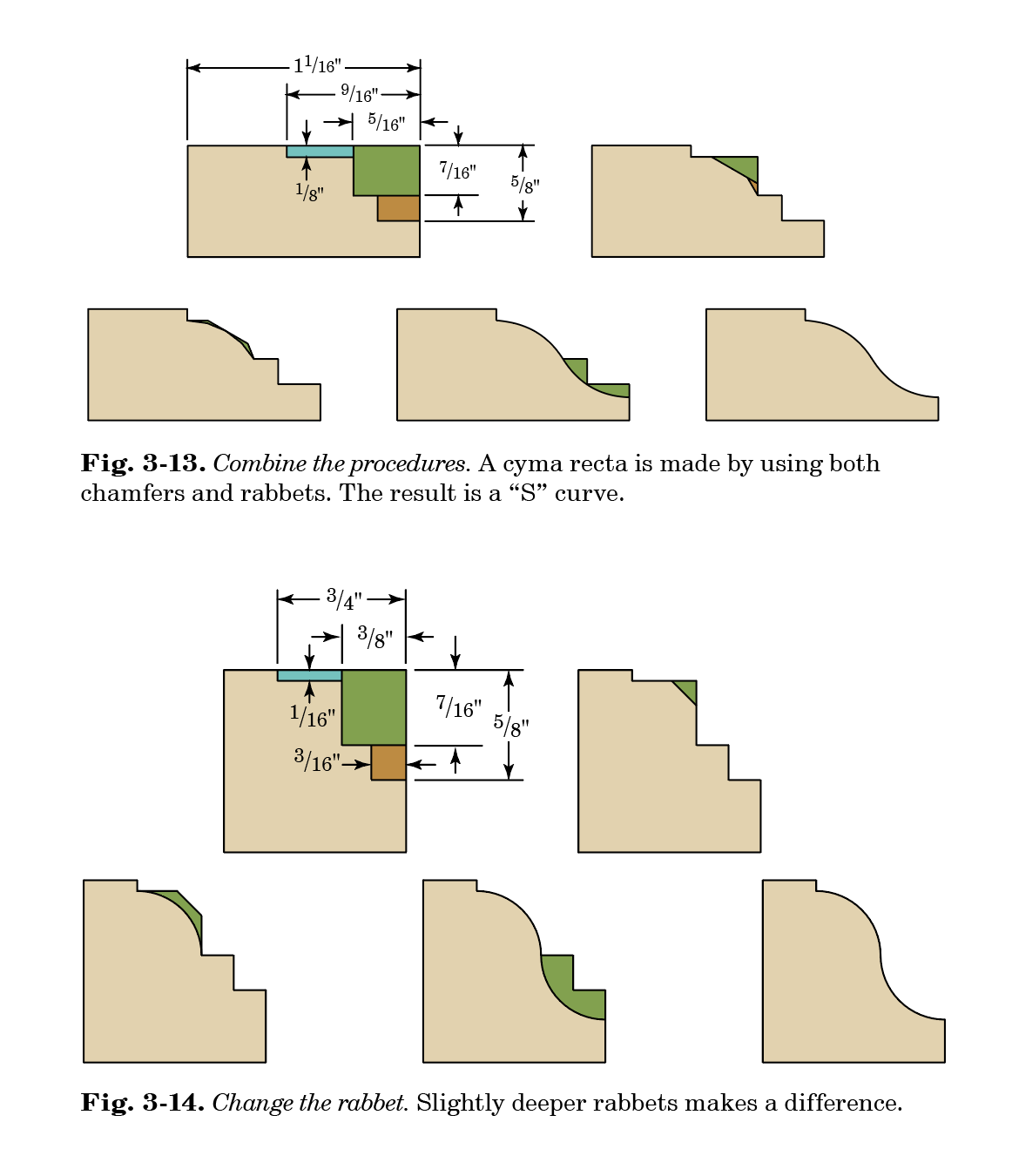
An ogee, or cyma recta, is achieved by combining the procedures for a cove and ovolo.
Reverse Ogee (Cyma Reversa).
Minor changes to the rabbets can result in major changes to the profile.
Ovolo & Cove.
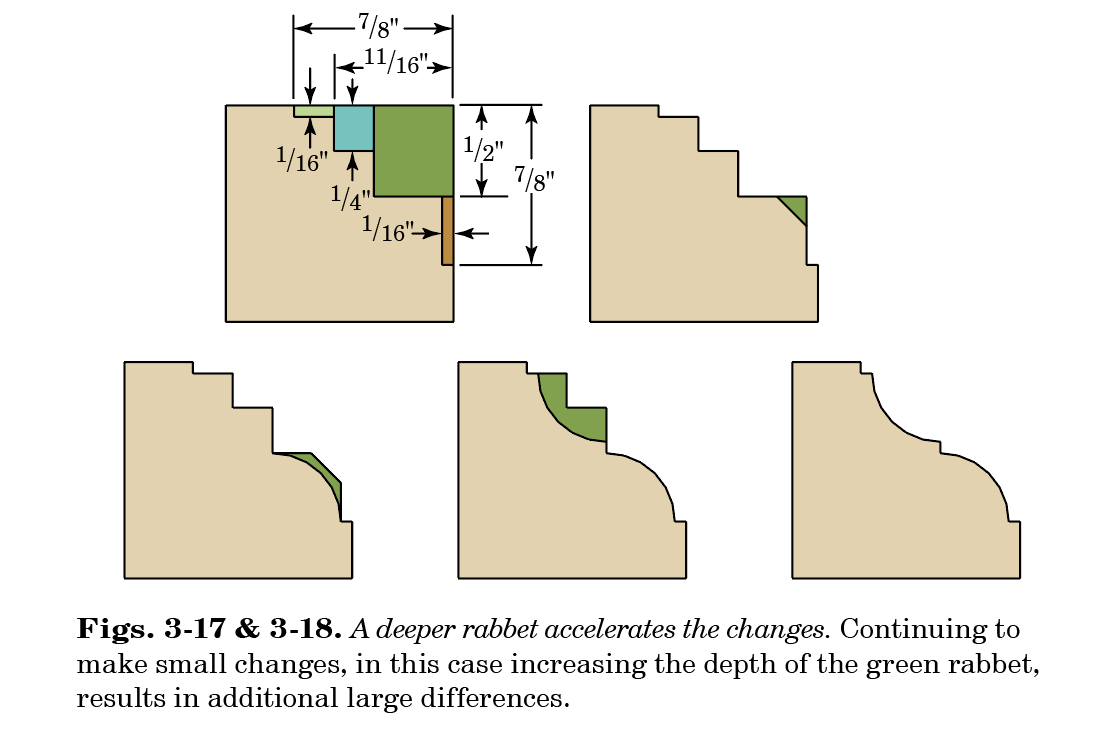
Side Bead.
A side bead starts with a snipes-bill plane that follows a gauge line, and it ends with a hollow.
More fascinating temptation….
This is a really important book. Probably the most significant book for hand tool woodworkers there is, given that it is the only one that contains this whole range of material. Everyone should have this book.
I agree. There is no other work that spells out profiles like this book.
I ordered this book when it came out. I have always done molding with my 1/2 set of H/R. they were ok, a little hard to keep strait and true. After reading this book and doing a couple practice runs my moldings are perfect. The real magic is the blocking with that rabbet plane. it made all the difference in my moldings. Now I can make any molding you can draw. Thank you Mr. Bickford and Mr. Schwarz.
Love this book great information not readily avaiable
Reading Matt’s book is like opening a box of secrets! You’ll never look at hollows and rounds they same way again!
Ive been looking at how to properly use “my obsession” for wooden “user” planes! I need to get this book!
I have mixed feelings about this book. I find the methodology absolutely fascinating, but as somebody with OCD , the sheer number of options gives me terrifying anxiety. I would prefer a cliffs notes on how to do 3 options that will work for most x style household furniture. But it looks like a wealth of knowledge on a subject that is almost a lost art.
You wrote, ” … how to layout the rabbets to make the work easier.” Woudn’t “lay out” be better, because we write “laying out” rather than “layingout”, no? (We would of course keep “layout” as a noun, right?)
You are correct—we’ll fix that on the next printing