In 2007, a lightweight box showed up on Christopher Schwarz’s desk from Joel Moskowitz, who runs the Tools for Working Wood store in Brooklyn, N.Y. Inside was “The Joiner and Cabinet Maker,” a book first published in 1839 on working wood by hand. It was one of a series of books that introduced young people to the basic knowledge of trade skills: baking, coopering, printing, joinery and more.
But it’s not only a how-to; it’s presented as an engaging fictional tale that tells us of young Thomas, a boy apprenticed to a joiner’s shop in a rural English town. He begins his apprentice years sweeping the shop, managing the hide glue pots and observing the journeymen.
Then (plot twist), Thomas is told to build a rough box for a customer who is leaving on a journey that same day. We get every step of the project, from stock selection to construction to delivery, when Thomas brings along an envelope of cut nails for the customer so he can secure the lid shut before his trip.
Thomas goes on to build a school box and finally a large chest of drawers, while he learns the joinery and personal skills to become a journeyman.
Chris and Joel re-published the book in 2009 (it is now on its fourth printing) – and to go along with the historic text (included in its entirety), Chris constructed all three projects, with step-by-step instructions and drawings, and Joel wrote a section that explores the social structure of England in 1839, and woodworking during the period.
It is available in hardcover and as a searchable PDF; it is also the only Lost Art Press audiobook – recorded by Roy Underhill. That project was at the request of a school for autistic children, so that students could listen then build the projects.
The following is excerpted from “The Joiner and Cabinet Maker,” by anonymous, Christopher Schwarz and Joel Moskowitz.
— Fitz
Most modern woodworking texts are silent on the topic of nails. Ernest Joyce, the author of the widely distributed book “Encyclopedia of Furniture Making” (Sterling), put it thus:
“Apart from panel and veneer pins, the furnituremaker has little use for nails except for softwood work etc.”
I couldn’t disagree more. While it is surely possible to build furniture without ever driving an iron nail through wood (just ask a Shinto temple builder), that is neither an expedient nor historically accurate approach to building traditional Western furniture.
Antiques of the highest caliber bristle with nails – you just have to know where to look. Examine the cabinet’s back for rosehead nails. Do you see how the moulding and cockbeading are attached? How about the glue blocks that support the entire case piece behind the feet? In some cases, even the dovetails are nailed. And though some might contend that nails in antique dovetails were part of a shoddy repair job, that’s not always the case.
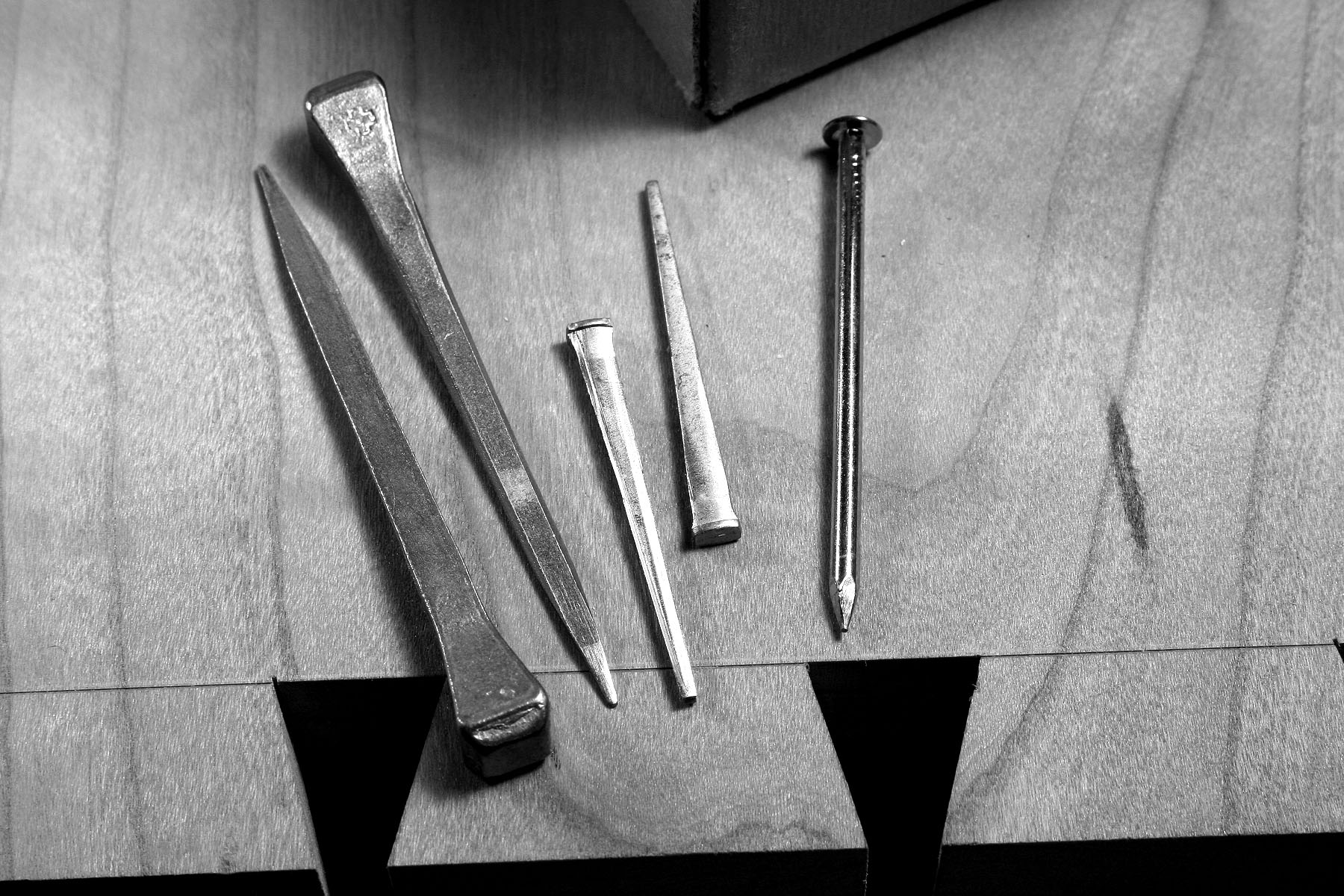
But before you scoot down to the hardware store to pick up some nails, read on a little farther. Those might not be the right nails for you. The first recorded nails are Roman nails, which appeared about 5,000 years ago and had a good long 4,800-year run. Roman nails are basically square and taper on all four sides to a point. They were handmade.
I’ve used nails like this, and they are tricky. You need a pilot hole, and you have to place your nails so they are as far away from the ends of boards as possible because these nails wedge your work in all directions. So splitting your work is easy – unless the wood is green.
In my opinion, the best nails are those that Thomas used in “The Joiner and Cabinet Maker.” Thomas used cut nails, which are much different than both the Roman nails (sometimes called wrought nails) and the modern wire nails used in carpentry today.
Wire nails are made from long spools of wire – no surprises here. The wire flies through a machine that snips it to the proper length, then a machine “upsets” one end of the wire to create the head and sprays the fastener with some sort of adhesive or coating, depending on what the nail is to be used for.
So wire nails are either round or basically square in section (the square ones are used in pneumatic nail guns). They don’t taper in their length. They are incredibly cheap. They also don’t hold particularly tenaciously (with some exceptions), though they are excellent for carpentry or situations where you don’t need a bulldog grip.
Reproduction furniture makers who use hand-driven nails still typically use cut nails, just like Thomas did. Why are they called “cut” nails? These fasteners are sheared from a sheet of steel stock. (Imagine a Kit Kat candy bar being broken up into individual sticks. It’s a bit like that.) However, instead of being round or square, cut nails are rectangular in section; they taper in width but not in thickness.
Like Roman nails, cut nails require a pilot hole, and you want to mind the wedge shape. If you apply the wedging action against the end grain of your top board, the nail will hold well. If you apply the wedge into the face grain, you might split your work.
Cut nails were the nails of choice in the 19th century. They were made in large numbers at the beginning of the century but were driven to near-extinction by the less expensive and more convenient wire nails by the end of the century.
In the “The Joiner and Cabinet Maker,” the reader is advised to learn how to straighten cut nails that have been bent and then discarded. This activity might seem like quaint parsimony, until you’ve bought a few boxes of these fasteners. Modern cut nails are made using the same machines and processes as they were in the 19th century and, as a result, they are expensive.
I pick up every nail I drop. I straighten (or try to) every nail I bend. It’s a bit of a meditative skill. Tap the nail with a lightweight hammer while holding the fastener on an anvil or a steel plate. Many small taps are better than one mighty blow.
And one more piece of advice: If you cannot save the entire nail, snip off a straight section and use that as a headless brad for finer work.
If you can’t afford cut nails, the next best thing is to buy cement-coated wire nails (which are actually coated with a heat-activated resin). Furniture maker Jeff Headley uses these, and he modifies the head by beating them with a hammer on an anvil to give the head a squarish shape. When installed, these hold well and look like cut nails.
How to Choose the Right Nail
The number of styles of cut nails is bewildering, and they all look similar and have odd designations for their lengths. Even today, nails are sold using the original pennyweight system.
What you need to know about the pennyweight system today is that a 2-penny nail (and “penny” is typically abbreviated as d) is 1″ long. Each additional pennyweight adds a 1/4″ to the length of the nail on up to 10d nails, which are 3″ long. (Nails longer than 3″ are sold differently. If you need nails longer than 3″, however, you’re not a furniture maker.)
Naturally, you are wondering what length of nails you should stock up on to build furniture. Most of my furniture work requires 4d (1-1/2″ long) and 6d (2″-long) nails. There is a formula you can use, however, to arrive at this same conclusion.
Whenever you nail two boards together there is a board on top and board below. It’s the board on top that you want to pay attention to when selecting a nail. How thick is this board in “eighths?” A 1/2″-thick board is, for example, four eighths. A 3/4″-thick board is six eighths. Convert that number to pennyweight. So to fasten a 1/2″-thick board, use a 4d nail. To fasten a 3/4″-thick board use a 6d nail.
Of course, pay some attention to the board on bottom – you don’t want the nail’s tip to poke out the other side.
So now you know what lengths you need. What about all the different styles of nails? There are three commonly available styles of nails that I use to build furniture. And there is one style of nail that is difficult to find (in the Midwest, at least) but easy to make. Here are the four styles and what they are good for. I’m going to use the names that Tremont Nail Co. (tremontnail.com or 800-835-0121) uses because that company is by far the largest modern-day supplier of cut nails.
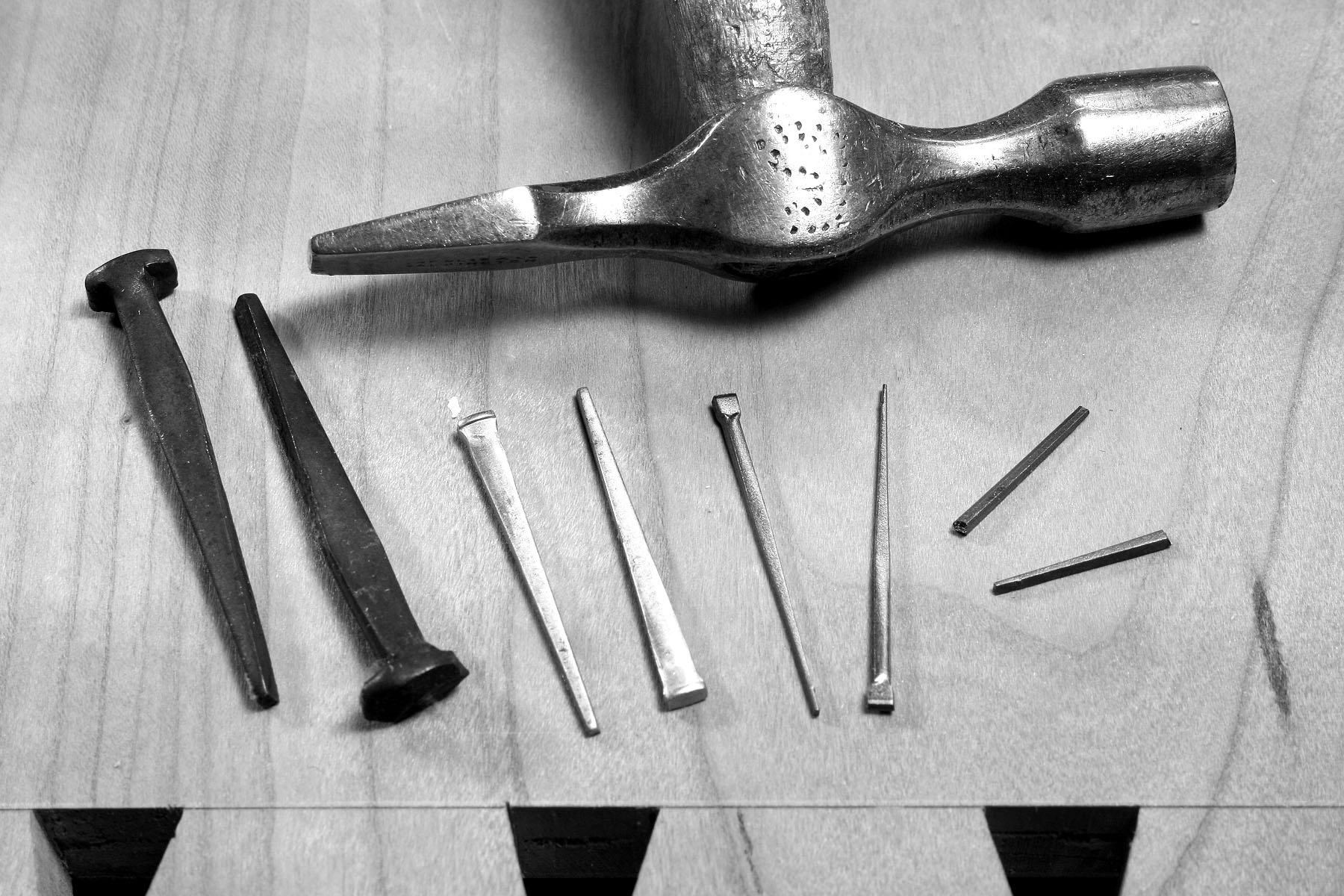
Fine Finish Standard Nail: This type of nail holds carcases together. It has a pronounced taper and a large head, so it will wedge up your workpieces well and hold tightly. Its strong wedge is a two-edged sword. It also will readily split your work if you aren’t cautious.
Cut Headless Brads: These slender nails are excellent for attaching moulding. They don’t have as pronounced a taper and are skinny things, so they aren’t suitable for full-scale case construction. But their scrawniness is ideal for jobs where the nail head will show, such as attaching face frames (with the assistance of glue). I typically add a 3/16″ bead detail to my face frames, and these nails sneak into the quirk of the bead nicely. Note that the maker says these brads are headless; that’s not entirely true. They have a small head.
Clinch Rosehead Standard: Rosehead nails are great for attaching cabinet backs or anywhere you want the nail head to shout, “I’m a nail.” There also is a version of this nail (that is more expensive) called a “wrought head nail” that has a black finish and a head that looks hand-finished. Use this nail when you want to shout, “I’m an old nail.”
Sprigs: You’ll see this nail mentioned many times in “The Joiner and Cabinet Maker.” Sprigs are headless nails or nails that have a head on only one side of the nail – they make something of an “L” shape. I have yet to find a reliable source for these nails, so I make my own by clipping the heads off of the cut headless brads listed above. Sprigs, as you will find out, are great for attaching delicate mouldings or for lightweight structural applications.
Using cut nails involves some know-how and a special shopmade tool, which we’ll cover in building the Packing Box, the first project in “The Joiner and Cabinet Maker.”
Does anybody know of a source in Europe? Shipping from the US is quite expensive…
https://www.goodsandchattels.com/
Here is a website in Australia, just look under Fasteners & Screws. The sizes are in mm even though they are from Tremont nails. All prices are in AUD and therefore it work out to be very cheap for you.
https://forgednails.com/ These are the same ones that Lie Nielsen sells.
Right! Rivierre. Those are sold at Dictum as well, the blued variant – at least they look really similar. Those are machine forged, which is a good compromise. The blued just look a bit… Strange.
But no cut nails, scroll down for a link to those, shipping from Sweden (tusen takk @Mattias Hallin, det hjelper masse!)
Väl bekomme, Joe – nöjet var helt på min sida!
Mattias
I use these: https://www.oldhousestore.co.uk/product/fine-shank-rose-heads/
(but even shipping UK to Belgium was quite expensive 🙁 )
Joe,
Yes, there’s a selection of Tremont cut nails available from Rubanks AB (https://www.hyvlar.se/en/cut-nails?search=spik) in Stockholm.
It is not quite clear from their website in what quantities they sell them (i.e. how many or what weight you get for the quoted prices), so you might want to get in touch with them first and ask about that, should you wish to compare cost with ordering straight from Tremont
Cheers,
Mattias
Thanks! I’ll check that out.
Thanks for this on nails! I have a cherry grandfather clock (8’ + height) I recently inherited from an older cousin (still living) who had no children. It belonged to the Hamilton family, the wooden works made by a famous maker in 1800, and the case made by a country cabinetmaker around 1810 (good records on this). My cousin’s cat knocked this tall clock over during the night a couple of years ago, so it needs repairs, the head knocked to pieces but unbroken, not even the original glass in the door was broken, the works undamaged. Your photo and text allow me to identify the various cut nails used. It is a plain but elegantly proportioned piece. If you or anyone know a reputable clocksmith capable of working on wooden works, I would appreciate the information. It kept excellent time until someone messed with the adjustments about ten years ago; has not worked since. Clockworks are not something I know much about, so I need a professional.
A note of advice: don’t stand a tall clock on carpet, or do secure the clock to the wall if you have pets, rambunctious children or live in an earthquake zone.
I was just reading this last night and wondering what sprigs were. I had only heard the word before related to trees. I kind of deduced they were some type of brad but its good to see the pic of the various type. Also, the only “cut nails” i have seen in person were labeled as masonry nails. Are those the same?
They are the same, but they are hardened, and thus won’t clinch. There is a more common style of masonry nail that is round, like a modern wire nail, but is also hardened.
Ah interesting thanks. Makes sense after reading what you wrote.
I’ve found that annealing cut masonry nails will soften them significantly, probably enough to clinch. I just heat them to red hot with a propane torch and let them air cool. Dropping them into some ashes will slow the cooling and maybe get a softer anneal…
Lie-Nielsen, oddly enough, sells French wrought nails. You have to search on their site to find them, but I just checked and they’re still there. Not cheap.
As does Lee Valley
Compared to the garbage mass produced wire sinkers, perhaps. But compared to the alternative in the same league they are fantastic and reasonable. For example, rockler sells cut/ forged nails that are too short, half the size and more expensive than the revierre. Oh, and the rocklers are just powder coated and rust immediately.
Fitz, do you have a source for a box of 6d cut nails you can share? House of Antique Hardware. Timely post btw putting the Dutch tool chest together.
https://www.tremontnail.com is the direct place.
Thanks, I’ll give them a call
I recently did rehab on an old English oak piece that had been modified in the 19th C. The 19th C work used various sizes of oval-shafted wire nails and I’m wondering if anyone knows and where when such nails were used. They held tenaciously.
Judging from the videos by Richard Maguire these seem to have been common in the UK. I got a package from… I forgot. They hold well enough, but mine don’t seem to be the real deal.
Back in the sixties , working as a chippie in London , 6” X 1” floorboards were always fastened to the joists with cut nails , kept them in place more so than the more common wire nails
So glad to be among adults. No one here childish enough to mention that horrid meme, punched it, or hammered it or whatever it is.
There is a book on nails by Chris How that is really detailed. Hand forged nails continued to be used long after cheaper cut nails were introduced because forged nails clinched so well. The grain in wrought iron (silica slag between fibers of iron) runs lengthwise in a forged nail and crosswise in old most cut nails. For this reason straightening bent cut nails often results in breakage. Modern cut nails are steel and have no slag inclusion. There are blacksmiths all over who can make forged nails for projects that require the authenticity.
You may find this article about hand making nails in the English Black Country interesting. If you Google “Black country nail makers Sedgley.
For sprigs, try looking under “shoe nails” , which I have heard them called. I see a shoemaking supplier has them in quite a number of sizes (and one of their warehouses is in Cincinnati, though not their order house). Here’s a link to their page https://www.southernleatherco.com/product-p/nail30.htm