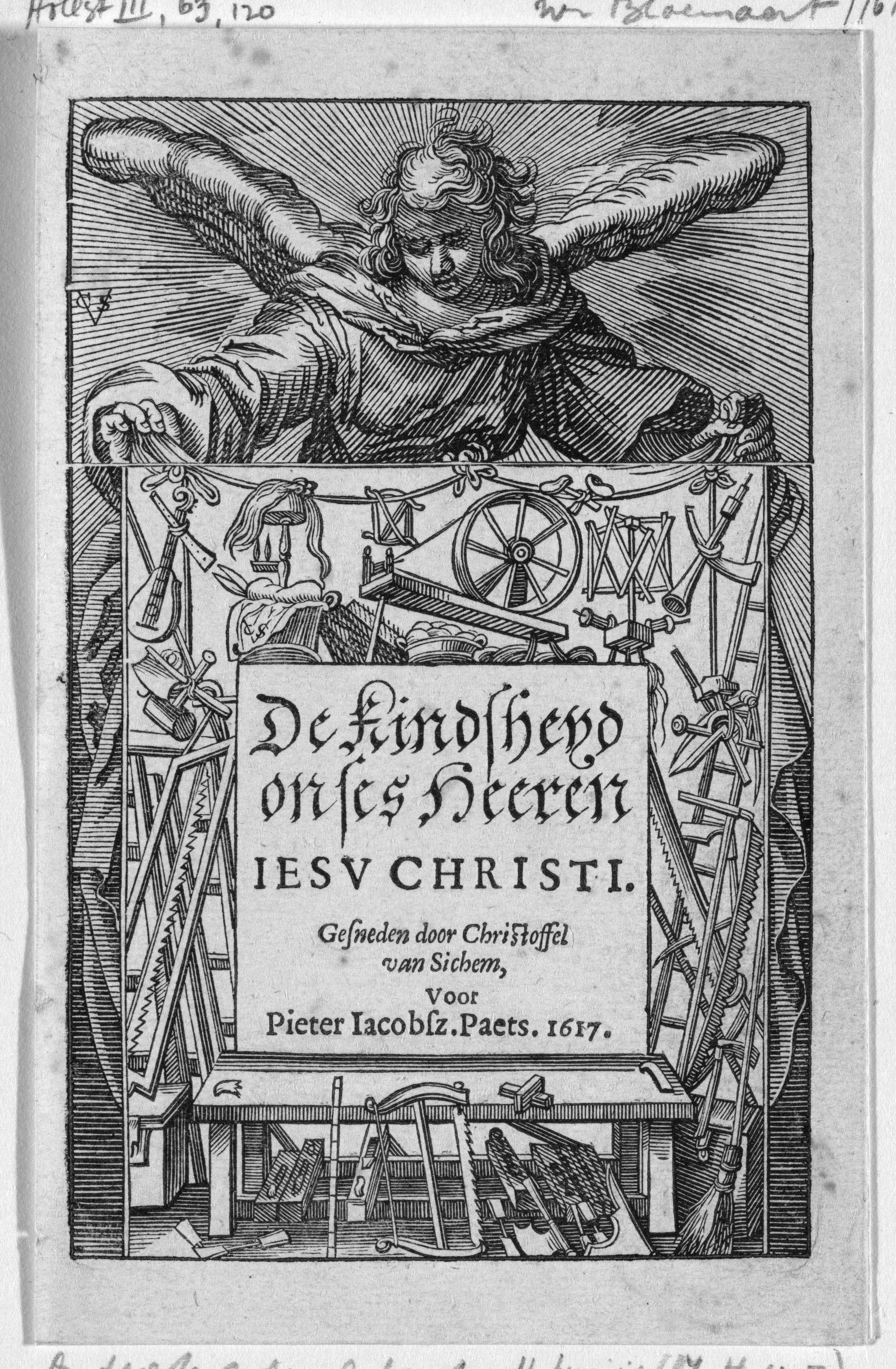
The following is excerpted from Christopher Schwarz’s “The Anarchist’s Workbench” (which you can download for free on the store site; see the penultimate paragraph there for a link) – it’s Appendix A. I’m posting it because Chris gets dozens of questions about workbenches…even though he has no public email. And I get hundreds of workbench questions…because Chris has no public email.
— Fitz
During the last 20 years, I’ve been asked a lot of questions about workbenches. Most of these questions I’ve answered 100 times already. That’s OK. When people first get focused on building a workbench, they usually haven’t read years of blog entries or the five or six books that are available on the topic.
And so they send an email asking what’s the best wood to use. Oh, and could I also compare and contrast all the different forms of benches? You know, like, just real quick?
We get these questions almost every week.
Below is a list of the questions I am asked constantly – plus my answers. A lot of this information is covered elsewhere in this book. But this format – question and answer – seems to help some people work through their own doubts.
This chapter also gives me something to cut and paste when replying to emails and letters. Here we go.
Questions about Workbench Materials
1. What wood should I use?
There are only a few woods I wouldn’t use for a workbench: white pine (too lightweight), expensive exotics (too expensive), rotted wood (too rotted). I recommend you use the heaviest, cheapest and most readily available species in your area. In the South and Midwest, that’s yellow pine (the cheapest), followed by poplar and soft maple. Don’t worry about the stiffness and other engineering factors. If you overbuild your workbench, it will be plenty stiff and strong.
2. Should the benchtop be a slab? A lamination? Plywood? LVL? Which material works best and survives the long term?
All of these have trade-offs, and all of them work well – both in the short and long term. The choice is less about engineering (all are heavy and stiff enough) and more about aesthetics, economics and the tools you have available. You can make a plywood bench using a table saw and screw gun. A slab bench requires far more (including a forklift). But which looks better? That’s your call.
3. What’s the best glue for building a workbench?
All the common glues are strong enough – hot hide, liquid hide, PVA, epoxy. Choose one that suits your wallet and the way you work. PVA is cheap and easy to get, and it sets up fast (this can be good or bad). Hot hide glue sets up very fast (again, good or bad). Liquid hide glue might be difficult to purchase in your area and sets up slowly. Epoxy is very expensive, but it fills gaps and can have a slow or fast curing time depending on its formulation. For most woodworkers, PVA (plain old yellow glue) is an excellent choice.
4. Can I use green wood? How green?
Yes. But it’s risky. Drier is better. You have no idea how much the components will move as they dry. Benchtops, even thick ones, can twist more than 1″ at the corners. If you do receive a fresh slab and need a bench today, build the bench quickly and use stretchers between the legs. The undercarriage and the joinery can help hold the top in place as it dries, reducing its tendency to warp. Also, it’s a good idea to orient the top so the heart side of the board faces up.
5. Is it OK to include the pith in my bench components?
I don’t recommend it. No matter what your local sawyer might say, a board with the pith included (sometimes called a “boxed heart”) will split. The split might be minor, or catastrophic. It depends on the tree. Why risk it?
6. Is air-dried wood better for a bench? Or is kiln-dried OK?
Either is fine. And I can’t say that either is better for a bench. Just use the heaviest, cheapest wood that is readily available. For me, the more important question is if the wood is at equilibrium with its environment. If not, let it sit a while. Then build the bench.
7. If I can’t find Southern yellow pine in my area, can I use….?
Yes.
8. What’s the best finish for a benchtop?
Probably no finish is the best. You don’t want your benchtop to be slick. You want the work to be easily restrained. If you want to make it look nice, some boiled linseed oil will do that (and give you a little protection from water spills). Or an oil/varnish blend. That will give you even more protection, but it might slicken up the benchtop a bit. Avoid waxes and thick film finishes, unless your workbench is a fashion accessory.
Questions about the Form or Structure of a Workbench
9. What style of bench should I build if I use only hand tools?
I think the easiest bench to build with hand tools is an English joiner’s bench, sometimes called a Nicholson. If you buy dimensional lumber, there is almost no wood to plane to thickness. It’s just cutting boards to length and fastening them together with simple joints, screws or nails. Mike Siemsen’s video “The Naked Woodworker” is a good place to explore this.
10. Won’t wood movement in the benchtop wreck a Roubo or Nicholson workbench?
I have never seen it happen. The top shrinks and expands, and the base contorts a little. It doesn’t affect the working qualities of the bench, and the benches don’t pull themselves to pieces.
11. Is it OK to use mixed species of woods when building a workbench?
Sure. There is no issue with strength, longevity or (realistically) differential wood movement. A hardwood top and a white pine base might be an economical way to build a bench. The only real concern is aesthetics. Sometimes a benchtop with strips of walnut and purpleheart through the middle make me throw up in my mouth.
12. What’s the best workbench for…
…a beginner?
Probably an English joiner’s bench (aka, a paneled bench). It has the fewest joints and is the fastest form to build in my experience. However, any beginner can build a French bench or a fancy German bench. It just takes a little more time. Don’t let your lack of skills snuff out your dreams.
13. …an apartment dweller?
I would build a small yellow pine bench like the one in this book with nice vises. It would have mass because of the pine and all the features of a full-size bench. Then, when you get a bigger place, you can build a bigger bench and use the same nice hardware. The small bench could go to a friend or become a kitchen island in a Manhattan loft.
14. …a garage or barn without HVAC?
I would use softwoods, such as yellow pine, fir or hemlock. These woods move less in service than hardwoods. So, if there are wild swings in humidity, you’ll see less wood movement.
15. …a person with very little money?
A bench made with yellow pine or any heavy construction timber. Pound for pound, construction woods are the cheapest and easiest to get.
16. What do you think of a torsion-box benchtop? Or the New-Fangled Workbench? Shaker workbench? How about this other workbench that you’ve never seen or heard of?
At times, I feel like I’m being baited with this kind of question. You can answer the question for yourself if you think about it for a minute. Your bench needs mass. How easy is it to work on the faces, edges and ends of boards with the bench? Can you modify the bench as your woodworking changes by adding different vises or holdfasts? Does the joinery seem impossibly robust or one step above a slumlord’s birdhouse?
17. Should the benchtop be assembled with loose tenons?
This is an ancient way to assemble slabs (made popular by Greek and Roman boat builders). It certainly adds long-term strength. Drawboring these loose tenons can help pull boards together without clamps. If you lack clamps or faith in your glue or edge-jointing skills, this is a good technique to fix those shortcomings.
18. Can I glue 8/4 material face-to-face to make a thick benchtop?
Yes. You also can laminate a large quantity of toothpicks to make a benchtop. The trade-off is you need the equipment to do a seamless job. Or you need to be OK with a few gaps. There is a lot of surface area that needs to be glued when you laminate boards face-to-face.
19. Why shouldn’t I buy a Lie-Nielsen, Plate 11 or Benchcrafted workbench or a high-end Sjöbergs or Ulmia?
I like building my own workbenches in the same way I like building all the furniture in my house and making pizza from scratch. That doesn’t make my furniture or pizza better than store-bought. It’s just what I like to do. In fact, I cannot do things any other way because my head is that stupid. If you would rather buy a workbench and spend more time building jungle gyms for owls, do it. As always, caveat emptor with tools and woodworking equipment. I’ve used Benchcrafted, Plate 11 and Lie-Nielsen benches and find them to be great. Sjöbergs are not my favorite. And I haven’t tried a recent-vintage Ulmia.
20. Could you evaluate all the workbenches you’ve encountered in your career and explain to me the best one for my work?
Sure thing. Wait right here.
21. What’s your favorite workbench ever?
Probably the one in this book.
22. Which workbenches do you regret building?
None, really. Even the ones that were less successful taught me important lessons. The bench I miss the least is the door on sawhorses.
23. Should I tooth my benchtop like veneer?
Sure. I’ve tried it. The rough resulting surface seems to help keep your work in place, but that might only be my perception and not an engineering truth. The best reason to do it is that every time someone tooths a benchtop, the internet poops its inter-pants.
24. Is there any case where you would advocate for a tool tray?
Yes, when the tool tray is a box with a lid and three sliding tills. And positioned off to the side of your bench where all your tools are at hand.
25. What’s the best way to make my workbench mobile?
Push it. Commercial “mobility kits” don’t impress me. I’ve seen engineered solutions that are more complex than a Jarvik-7 artificial heart. Simple is best. Most benches can be slid across a floor easily. If you want to protect the floor, put a moving blanket under the feet. Honestly, I own workbenches that are almost 400 pounds, and I can move them myself with my scrawny bird-like arms.
26. What’s the best height for a workbench?
I think it’s somewhere between the historical heights of 28″ and 36″. Plus, remember that you can endure working in a range of about 3″ around your ideal. So, if you can’t decide, make the bench a little taller than the internet tells you. Then saw the legs down bit by bit until you find that your work becomes easier. Second piece of advice: Sit down at your bench to do detail work with carving tools, chisels or a router.
27. What’s the best way to make my workbench height-adjustable?
I know this sounds snarky, but it’s not. Sit down at a shop stool if you need to be closer to your work. Stand on the same stool (or a raised platform) if you need to get way above it for some reason. Adjust your height – not the workbench’s.
28. What do you think of these commercial benches that adjust in height?
I am impressed by the engineering, but I don’t see a need for them in my workshop.
30. Should my workbench be in the center of the room or against the wall?
Either works, as long as you can move the bench for oddball operations. I shift my bench all the time here and there to do different things. I prefer to have my bench in the middle of the room so I can go around to its backside to take photos. But most people don’t need to do that. One caveat: If your bench is lightweight, having it against the wall (or secured to the wall) can make it more stable.
31. If I put my bench near a window, which direction should that window face?
The classic shop uses only the beautiful northern light. The real shop will take any window facing any direction.
32. Can I drawbore a bench together without glue to make it knockdown?
You can do this once. After you disassemble a drawbored joint, it never goes back together as tightly as it did the first time.
33. How lightweight is too light?
If the bench moves across the floor during normal planing operations, you have a problem. Bolt the bench to the floor (or wall), add weights or build a heavier bench. After experimenting with commercial benches that were on the featherweight side, I’ve found the typical 60 lb. bench is too light. At about 150 lbs., things begin to work. Above 250 lbs., I don’t notice the workbench.
Questions About Workholding
34. Won’t the toothed planing stop cut me?
It’s unlikely. I’ve never cut myself after 15 years of daily use. Can it happen? Sure. Have I heard of people getting cut? Only once. Is it mentioned in early texts, which detail many of the possible gruesome injuries in the shop? Not that I recall.
35. I don’t want to cut a mortise for the planing stop in my beautiful benchtop. Are there other options?
Sure. You can fasten a moving block to the end of your benchtop. But I think that’s lame compared to just chopping a hole in your bench and doing the job right. I totally understand that some people have a mental block about some things: grinding an iron, filing the mouth of a handplane open, doing the Ruler Trick for the first time. The barrier is all in your head. Close your eyes and jump off the tire swing. You’ll be glad you did.
36. Do I have to have a face vise? Can’t I use just a crochet? Or is that a dumb idea?
Screw-driven vises didn’t show up until the 14th century. So yes, you can do excellent work without a screw-driven vise. Yet, the screw-driven vise is enormously convenient. (There’s a reason that Record never made a iron crochet – painted blue – for workbenches.) And vises are readily available and inexpensive. (But for the record, I enjoy using a crochet.)
37. What is the best arrangement/placement of holdfast holes?
Three rows. The back row is 3″ from the rear edge of the benchtop. The middle row is 10″ from the rear edge. The third row is 17″ from the rear edge. The holes are 16″ away from each other. And the holes are staggered on each row by 8″. You might have to adjust these dimensions if you have a very narrow benchtop, but this is the general idea.
38. … of dog holes?
Dog holes should be close to the front edge of your benchtop – usually 2″-3″ or so. This allows you to use handplanes that have fences that drop below the benchtop (such as a plow plane). I like to keep my dog holes close together – about 3″ on center.
39. What’s better: a wooden vise screw or a steel one?
Neither. Both can close quickly and ferociously on your work. Both can last several lifetimes if cared for. Both can be trashed by abuse.
40. What’s the best material for lining the jaws of a vise?
I like suede and a cork-and-rubber gasket material (Benchcrafted sells this as Crubber). Avoid cork alone as it’s too fragile. Some people like neoprene, but I haven’t tried it.
41. What glue should I use to affix the liner for the jaw?
I prefer epoxy. Full stop.
42. Should I install a patternmaker’s vise? In the tail vise position? The face vise position?
If you are a patternmaker, yes. And it can go in either position on the bench, according to the historical record. If you are a regular-head furniture maker, this vise has downsides. It’s expensive and a trick to install. Most furniture makers don’t need one. But dammit, I own one.
43. Why won’t my holdfasts cinch down?
Your benchtop might be too thin, so the holdfast cannot wedge itself in place. Or the hole is too big for the shaft, so the holdfast can’t wedge in place. Or the hole is not plumb. Or the shaft is too smooth. The least likely reason is the holdfast is poorly made and doesn’t have enough spring.
44. How flat does my workbench have to be?
The bench has to be flat enough so your work doesn’t spring in low spots to the point where you cannot flatten boards with your handplanes. If you work with handplanes, you will know when the benchtop is too wonky because your planes won’t do their job. If you don’t work with handplanes, flatness is rarely critical.
45. How often should I flatten my workbench?
I flatten a benchtop when I make it. Then I flatten it again when it has become disgusting from glue and abuse. Or when it stops working (as per the previous question). Some people flatten their benchtops yearly. Some do it after every big project. I ain’t got time for that. And I haven’t found it necessary.
46. What’s a vise garter? Do I need one?
Garters are a part of a screw-driven vise that links the screw mechanism to the vise’s jaw. With a garter in place, the jaw moves in and out when you move the screw in and out. Without a garter, the jaw moves forward with the screw, but must be pulled back manually when you retract the screw. Do you need one? They’re convenient but not necessary.
47. Will I regret not installing a tail vise?
The best path forward is to build a bench that allows you to add a tail vise immediately or in the future. That way you and your work can answer the question (instead of a dumb Kentucky woodworker).
48. Which is better: square dogs or round ones?
Neither. Square dogs don’t rotate; round ones do. Your work might need round dogs if it’s odd-shaped. Round dogs are easier to install. Both forms are traditional and go back centuries.
49. …steel dogs or wooden ones?
Steel dogs hold better but they will mess up your handplane as soon as you hit one. Wooden dogs don’t hold as well, but they don’t hurt your handplanes. The choice is yours.
50. What sort of woodwork requires a tail vise?
If you plane up a lot of boards that are similarly sized, a tail vise can be nice. They can also be nice for disassembling a frame that is tightly dry-fit. They are convenient for traversing wide boards with a jack plane or working diagonally with a jointer plane. We have several benches with tail vises or wagon vises. I use a tail vise once every few months.
51. Do I need a board jack (either integral or freestanding)?
These are helpful when you have very long boards (longer than 8′) or a face vise that has a poor grip and cannot handle an 8′-long board by itself. They are also handy for edge-jointing long tabletops and mortising doors. If you do big work, they are a godsend. If you don’t, they are occasionally useful but are mostly a storage facility for holdfasts.
52. Finally, what wood should I use for my bench?
Oh, do sod off.
I downloaded and read the book. Thank you, as it is an excellent read. The best part is the the answer to question 52…. I loved it!!!!
A hidden reference to an English post punk band.
I found the book to be such a help, and a nice summary for the series.
Is a 53rd question allowed? If LAP or the group have any thoughts, I’ve just built an English joiner’s bench and don’t know the best place for the planing stop. Must it go behind a leg for stability, or is the 2 inch top thick enough to support a stop on its own? It’s Benchcrafted in a 2 1/4 piece of ash.
Thanks again for AWB.
On the English joiner’s bench here, the stop is not over a leg. It’s 9″ in from the end, and 4″ back from the front edge. And that’s on a thinner top than yours.
So helpful. Thank you, and hopefully you reschedule your classes at PTSW next year!
Me too! I miss teaching, and I adore Port Townsend!
Richard Maguire (theenglishwoodworker.com) puts his next to a leg, but mentioned it does not matter to much and depends on the location of the face vise (screw, guide,…). Mine is in a 40mm picea abies plank and the most used and best working work holding device.
And I have another question, relating to what kind of wood. I have read the book (and ordered a copy), and was thinking about local availability for lumber. SYP is not very common around here (NJ), but some of the local home centers are now stocking New Zealand grown radiata pine, including some 5/4 thick (finished size) boards. They are the clearest, straightest pine lumber available in these stores. So, is radiata pine considered white pine, yellow pine, or something else entirely? The few pieces that I bought feel heavier than the common white pine that is readily available, but I don’t know how it compares to SYP. Any thoughts?
From the Wood Database (https://www.wood-database.com/radiata-pine/_:
Average Dried Weight: 32 lbs/ft3 (515 kg/m3)
Specific Gravity (Basic, 12% MC): .41, .51
Janka Hardness: 710 lbf (3,150 N)
Modulus of Rupture: 11,480 lbf/in2 (79.2 MPa)
Elastic Modulus: 1,458,000 lbf/in2 (10.06 GPa)
Crushing Strength: 6,030 lbf/in2 (41.6 MPa)
Shrinkage:Radial: 3.4%, Tangential: 6.7%, Volumetric: 10.7%, T/R Ratio: 2.0
Radiata is a white pine. But if it’s what you can get, use it. It’ll just be a little on the lighter side (easily fixed by heavy stuff on the shelf underneath…which is what I do with my featherweight bench at home)
Thank you. I checked a few other pines there, and it looks like it is heavier that eastern white pine, but not as heavy as the yellow pines. So it has potential. I’ll keep on looking for yellow pine. I have a workable bench for now.
Actually as a member of the genus Pinus, subgenus Pinus, P. radiata (Monterey pine) is a yellow pine, actually quite closely related to the Southern yellow pines like loblolly (P. taeda) and longleaf (P. palustris). And it’s actually harder than loblolly pine, the most common of the Southern yellow pines.
In my corner of the country, there is no southern yellow pine in lumberyards. The spruce and pine they have aren’t great for benchtops. But many do have Douglas fir, which is a much better substitute for SYP than other pines. Can you get Douglas fir?
In NJ you should be able to find a proper hardwood dealer… get prices on Ash, Soft Maple, Hard Maple…. you might be pleasantly surprised.
Radiata pine is a yellow pine, it’s just native to California so it’s not a “Southern” yellow pine.
Am I the only one that saw the title and quickly scrolled down to see if there really were a full 52 Q&A’s in a single blog post? I think I’ll read one a week for a year. Maybe make a calendar from them. My desk has seemed pretty empty since my last Far Side calendar in 1998.
You do know Larson is starting to publish (online) new Far Side, right?
What about “Will my wife be mad at me if my workbench turns out nicer than the dining room table I made her.”
But if you actually use the bench, it won’t stay nicer.
Not if you let her eat at it!
I’ve built 2 roubos, with your guidance, one white pine and one red oak, and surprisingly I prefer the white pine, gets dented like crazy, but grips better flattens better easier to move, but plenty of mass to stays put. Benches are very rewarding and very time consuming
I think you opened the flood gates. I did not see my question so.. my chop blank is red oak at 3.5” thick x 10.5” wide. Is there any advantage/disadvantage to leaving it this wide?
Thanks
That’s a monster! You might want to make sure your vise hardware can support that much weight.
Well it might get in your way while working on the benchtop. I run into my (much narrower) chop all the time when I’m planing. It hurts.
That is two good reasons to trim it.
Thank you both.
If the legvice is in the way of the planing stop why not place the stop “before” the leg ? I am aware the maximum lenght of a board will be shorter but how often does one use the planing stop for boards longer than 5 feet ? And no i dont use a planing stop so have no practical experience
Well, it also takes up room on the benchtop — and I don’t want one sticking up into my main working surface to the right of the chop (unless you make it so it can be tapped below the bench surface, I would leave it at the far end)
You might be disappointed. The first and last are duplicates. But let’s try to make some lemonade. Remember when Chris would have the occasional contest on this blog? Maybe Megan and Chris will have a contest to see who can come up with the elusive 52nd bench question that Chris has never heard before.
I’ll start it off: Chris, where is the best spot in my shop for my bench? (Inspired by Stumpy’s rearrangeritis post.)
But the answers are different 🙂
Yup.
My prior post was supposed to be a reply to Stumpy but WordPress stuck it at the end. Makes more sense up there. As this was supposed to be a reply to my own post.
I wondered if there was a missing chapter on how to install the tail vise (just kidding!)? It’s a great book.
At first glance, I thought this was going to be the start of a new project called 52 Workbenches in 52 Weeks, a la Matt Kenney… I guess questions and answers are OK, too.
But, what kind of sod?
Zoysia? St. Augustine? I’m guessing Kentucky Bluegrass.
Good grief. Just build a workbench already people. Try it and see what happens. If it sucks build a different one. At least you’re building something. Too much over analyzing for workbenches(fancy workbenches are cool to). Why should people think their first workbench should be a double extra precise balanced and blueprinted zero tolerance mf’er. Just build something! It’s ok.
Regarding the use of green wood for work benches – you should’ve advised against its use because its been reported to have been the cause of fatal woodshop accidents.
“ If I can’t find Southern yellow pine in my area, can I use….?
Yes.”
Bet you’re kicking yourself for not just saying 2x4s in the book.
So what your saying is Don’t Worry, Be Happy, be like Nike and just do it?
speaking of workbench, Page 22
“Is rib eye ritzier than hamburger?”
assuming that’s a typo or I could just be dumb…
Sorry. What is the typo?
“ritzier” but like I said I could just be dumb and it actually have a meaning.
“ritzy” means “fancy.” And “ritzier” means “even more fancy.” Sorry it wasn’t clear.
My workshop is too small for a sizeable bench and most of my work is done outside. That means a bench that can be packed up and pulled out easily. I have used the ‘door on saw-horses’ a lot and it leaves much to be desired.
I have some design ideas, but I don’t think I can get away from the separable top and legs. Much of the problem is that a heavy top is difficult to move about and light one doesn’t provide the support necessary.
Any suggestions for something that is actually portable rather than just moveable? Uneven ground means wheels aren’t really practical.
Are you sure white pine is unsuitable for a bench top? My local lumber might have been marginally harder that W/P but not by much. Over the past couple of years I’ve beaten the hell out of it, and a couple of times even thought I’d dented it to the point that planing it flat again would remove too much material to have a sturdy top anymore. The thing is steam by way of a wet dish rag and an iron is a very powerful reset button. Over the past couple 2ish years I’ve steamed it out 2 or three times. Haven’t resurfaced or reflattened it since I built it, and even some of the original toothing has survived. Also, even with the steel face vise I’m pretty sure it floats, but hope never to get the chance to test that.
Hi Ric,
Of course white pine works for a bench. I think even balsa can work. It’s just not my first choice if I can get something that’s heavier and cheap with great ease. If that’s what you have, love the one you’re with.
I love it when SYP splits to a line.
Question No. 53
Do you apply the Clubber jaw lining to both sides of the vise or do you prefer Benchcrafted’s recommendation to only apply it on one side of the vise?
I put it on both the jaw and the benchtop.
I think the workbench dilemma is a product of our generation. We have more money, more information and more options than any other generation in history. We can afford it, so we seek the best and some spend months reading, watching youtube, etc, trying to maximize every step. This is because we have the money and the time. What’s the perfect style, perfect wood, etc? Let’s find out. With the workbench, there’s some fundamental designs that are important, but none are absolutely critical. And this is a problem. We can’t maximize it because there’s too many options. So we ask really specific and for the most part, meaningless questions, like round dogs or square?
If my grandpa’s generation were around today, they would have built all their benches from Ash. It’s dying all over the midwest and is basically free. In a few generations, we’d all look back at those benches and say, that generation must have known something because all their workbenches are made of Ash and mine will need to be too. Of course by then, Ash will be a rare wood and very valuable so of course it was the best.
Bottom line, find some cheap wood and build a bench (Ash would be good). Mine is a fir base and a laminated solid door because that’s all I could scrounge up 15 years ago when I started. It’s got cabinets underneath full of tools so it’s heavy and doesn’t slide. I make stuff on it. I drill holes where ever the heck I want. The kids just got gobs of hot glue all over it. I put greasy engine parts on it and use carb cleaner to clean up the grease. Someday, I’d like to build a pretty bench but I just don’t know if Ash is the best wood.
Hi Chris,
I have a friend who’s offered me a 4.5″ x 25″x 7′ slab of holm/evergreen oak, think its only been stickered in a barn for 2 n a half seasons, so probably is a bit wet still. Plan is to use it for a solid workbench top, though im concerned by how much sharpening ill have to do as iv heard that its really tough to work with
I’ll be hopefully getting a bench top that is 24″ x 6′ out of this
Question, would you recommend;
a) moving the slab to my unheated shed and let it acclimatise whole (though the conditions should be similiar) – before trimming the ends and ripping to square it up & then plane it before assembly, or
b) cut to length then leave it do its thing for a while before jointing it? Perhaps cutting to length, then resealing the end grain?
Also, I know one end has a check in it. Would you recommend adding a butterfly ASAP to stop it getting worse or after i have jointed the slab?
As Im assuming its going to move when i start working on it, im planning on assembling the legs and stretchers with whatever dried timber I can get my hands on, then get it on the base ASAP to help restrict the movement
Cheers
Ollie