Thank you to the many of you who have sent in corrections to “The Anarchist’s Workbench” (y’all are fast readers)!
I’ve updated the pdf (even “spit top bench,” though I found that one funny) – the new (and free) pdf can be downloaded here.
If you find any mistakes in this new version, please let me know (my nickname below is linked to my email)! NB: Use Adobe’s Acrobat Reader (a free program) to view the book – it won’t look right in Preview (the default pdf viewer program on Macs).
And if you’re interested in ordering the hardcover book, please click here.
Thanks,
Fitz
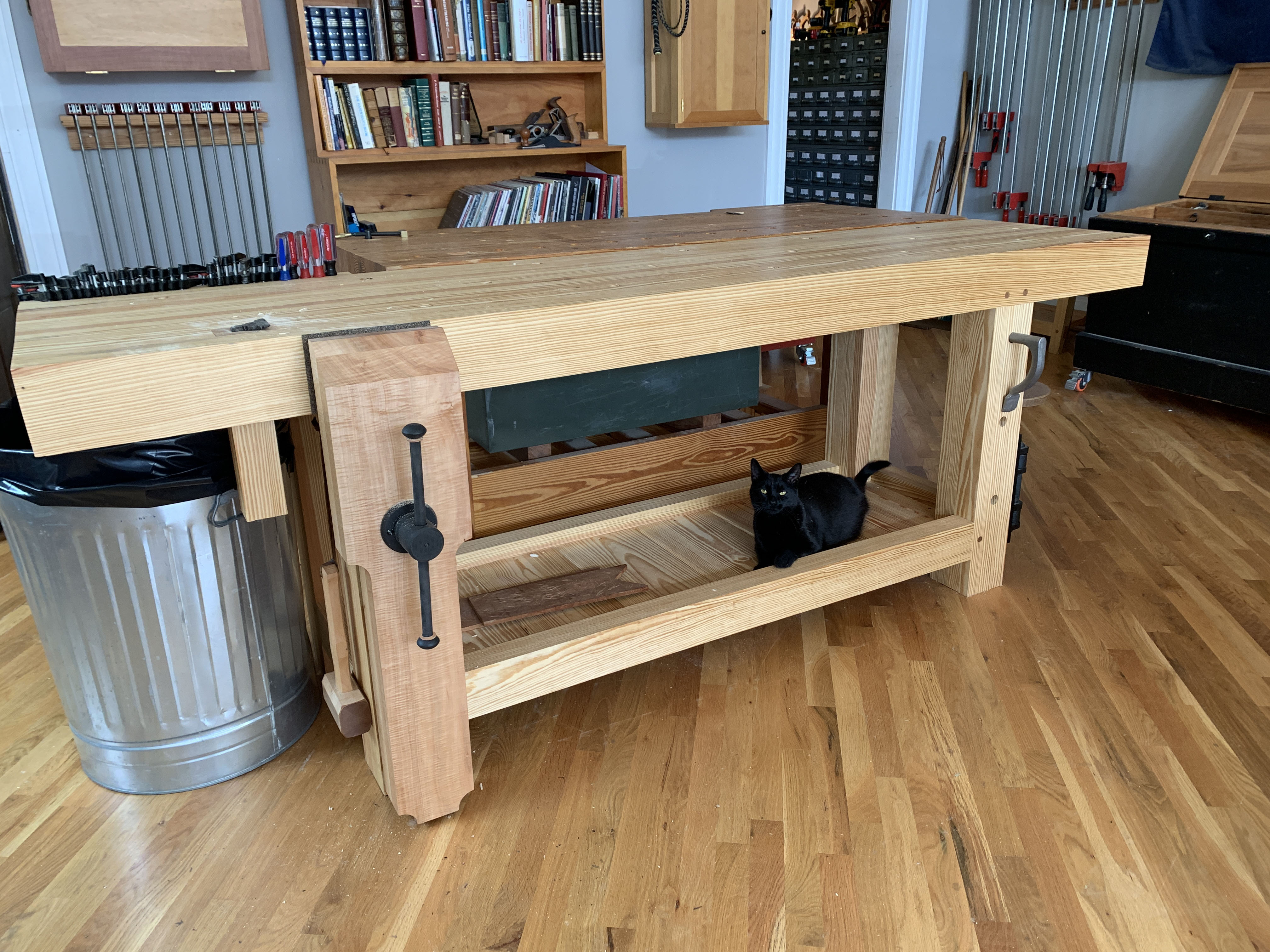
Many many thanks for it — I’m even more looking forward to buying the hard copy! One more question! if I have a big slab with the pith in, and put a sewari kerf to stop random splits (and maybe plug the kerf after a while, and/or just keep it at the bottom of the bench) — is that bad?
Chris says he’s tried that (Japanese) technique – it’s better than just leaving the pith alone. (Best is no pith, though.)
Thanks for letting me know! sometimes one’s gotta make with what’s available!
So there’s no REALLY good way to get pithed off with your bench?
The Bean seal of approval really puts this one over the top!! Ordering the hard copy ASAP!
I downloaded the *.PDF file and printed it. Should take me a few days to read it. I’ve got a big pile of rough cut, air dried White Oak that will have to be run through my planer, jointed and ripped to width. I’ll laminate the 4 x 1s for the legs, then cut the stretchers. I’ll use the base as a saw horse to laminate the top. I have a drill press that’s been converted into a mortising machine, and an attachment for my table saw for cutting tenons. There will be some scraps from cutting the pieces for the top that I can use for ledgers on the stretchers to support the bottom shelf. Since I live in Californication, I can work outdoors on my patio, at least until December. Don’t know if I’ll apply a finish or not. Wish me luck!
When I was a kid I would watch my older brother work on his car. He chewed tobacco and had a brass spitoon near his work bench. I could see adding a nice brass spitoon to a spit top bench, more useful than a tool well for some people.
I’ve been jumping around to various parts of the book and think it’s great. I even enjoyed the editor’s note in the Afraid of Fire chapter (an in-joke…that maybe isn’t that funny). I’m looking forward to holding the printed version.
“The Anarchist’s Workbench has the Bean seal of approval – so you know it’s good”
I didn’t even know that Mr. Bean was a woodworker!! And all this time I was a big fan of his just for the Mini he drove from the roof!
The bookmarks on V3 don’t seem to work. I keep returning to the Table on Contents.
Fixed. All the links should have v4 with fixed links.
On the cusp of a bench build so this book has come at a good time. Only a few chapters in but have already given up my dreams of a maple bench. You should be on the debating team for Yellow pine. You win.
Adobe is an evil company and creator of bloated software. Seems to be working fine on iOS without them.
In a way it is of course a pity that the “spit top” error was spotted, or the first (print) edition of this book would over time have become a collector’s item on a par with the Wicked Bible (“Thou shalt commit adultery”) and other pearls of the printer’s art from throughout the centuries.
Then again, given my views on collectors, as opposed to *users*, of vintage whatever, maybe it’s all for the best anyway … 😉
That said, I would very much like to first of all thank Chris and the LAP team for a fantastic book! I downloaded (and pre-ordered; that goes without saying, although I just said it anyway) and read it all the way through yesterday.
In my opinion, Chris, this is one of the finest pieces of writing from your pen that I’ve ever read. It strikes what for me is just the right balance between solid information, humorous asides and passion for the subject. On top of that it feels even more personal and unvarnished (“just a couple of thin coats of oil”, maybe?! 😉 ), in a very positive sense, compared to your other books. I thoroughly enjoyed the read as a piece of writing, I thank you sincerely for giving out of yourself, and I am now full-on busy processing and digesting all the information, advice, suggestions and ideas.
As so many others who have commented, and as I’ve already mentioned in other comments on this blog, I’m myself gearing up to a bench build. I acquired the vises (’twill be Benchcrafted all the way: an M-Glide with a retro Crisscross and a tail vise) back in January; after your recent post, I got in touch with Tom Latané about one of his planing stops; and last Thursday I finally set out Northwards to Arnhem in the Netherlands, where I bought 0,425 m3 (≈15 ft3) of 8/4 hard maple that is now stickered up in my workshop to acclimatise.
No. Your advocacy of Yellow Pine did not sway me, nor could it, as I read it only after buying the wood anyway. However, that would never really have been an option in any case. Yes, one can find American SYP on this side of the Puddle, but the price per pound is nowhere near as good as what it is over on your side of said water. For me the main contender would have been European ash, which here costs about half what hard maple does per cubic measure (I haven’t bothered figuring out the difference per measure of weight), and I do like ash a lot. But I love maple. Love the colour, love the tight grain, just love it. So, maple it is. What price love, eh wot wot … ?!
Your book, however, has already convinced me to change my plans in certain respects. Those plans were (and to a certain extent still are) based around the Benchcrafted Split Top (sorry, Spit Top) Roubo plans. After the chat I had with you about split tops in London last year, I’d already decided to go for a solid top instead (I once worked a bit on a split top Nicholson, and didn’t care for the way the split wanted to swallow up smaller tools and stuff, and the way it neatly deposited a lot of the shavings on the shelf below, turning it into a huge hamster nest). And yesterday’s read settled for good an argument I’ve been having with myself over the last 12 months: I will not use the knock down bench bolts I bought, but draw bore all the joints on the base. The jury is still out on whether or not to do the same for the top. I do know for certain that we will move at least once in the next six to eight years or so, and being able to detach the top from the base might make such a move rather easier. In particular it might make all the difference between getting and not getting the work bench into my next workshop. Then on the other hand, solid and permanent is rather nice … Yup. The jury is deliberating, yeronner.
For the rest, what really stuck in my mind yesterday was your phrase “You should start simple and go from there”. This makes so much sense. What this means to me is that I will take all the information that I now have: the Benchcrafted plans. Your books and plans. Other stuff. I will think about what bench I want, and why, and try to bring it and its construction down to as simple as possible. I will then think about what complications or fancies or less simple methods I might nevertheless want to apply. By which time the pile of wood should be nicely acclimatised, and I will start building!
Once more, you have made me think, constructively and for myself, and for that I thank you most sincerely!
Mattias
Having read about 60 pages or so I would have to venture that providing this for free is the best way to ensure an actual purchase. It is simple for me, the content is the same off my screen or via the printed page, but I prefer reading an actual book and I enjoy the content a great deal. When available in Australia through the distributor here, despite your best intentions, I will have to purchase an actual copy Chris. Then make another bookshelf for lack of room – hang on you are a marketing genius! Maybe some whizzbang prize for whomever spots the best typo such as a cast bronze of Bean the cat to put on your own bench, or a pencil, can’t get enough of those.
…cast bronze of Bean the cat…
Could we settle for a nice water color image instead? We’d have to wait a long time for a natural demise before casting the bugger. Unless you suggest we don’t wait, in which case I’ll let you deal with fitz on the concept. 😉
ps, I vote for “spit top Roubo” as the best typo.
I know Chris has used slabs for workbench tops before, have seen some of the old pop woodworking videos. Just thought you’d be interested, Matt Cremona (youtube woodworker with a sawmill) is starting to sell vacuum-kiln dried quarter sawn slabs for workbench tops.
https://www.youtube.com/watch?v=NB9rJa65tNw
I have no affiliation with Matt, just thought this would be interesting to you all.
The book is a great read so far. I use a Nicholson bench and working the edges on long boards is really easy using a leg vise in combination with a holdfast on the front. I’m struggling to see how this bench would handle these kinds of boards. If one end of the board is in the leg vise and you were planing the other end of the board, wouldn’t that pressure lever the board downward? Is the expectation that you would position the board in a central position on the leg vise with this bench to minimize the levering action?
The benchcrafted vise can hold an astounding length of wood tight, but on long pieces, the best solution is to use the holdfast holes in the leg to support it.
So I’m taking this book was given away for free out of spite? Lol
So I just finished the book, do you have to pay royalties for your updated version?
If so I’ll just send you a check, call it a gift for the knowledge you have given me.
I had been waffling about the wood to use, first it was hardwoods then after seeing what it would cost I’m going with fir. Can’t seem to find yellow pine in the northeast but we do have the best pizza in the world up here along with real ice cream.
I too quit the corporate world, I had my fu* money and just up and quit three years ago, similar reasons as you.
I bought my benchcrafted leg vise and bought two Hovarter end vises for my future bench build.
Yup two vices that as far as I know have no reviews and I’ve never seen anyone who had two on the end of a bench. It just seems worth the experiment to see if two quick acting vices can be useful. This will be my fifth bench build and I have had the usual issues as you, thanks for what you do.
It seems Chris Schwarz and Paul Sellers have irreconcilable views about work-holding, protruding vise, bench height and workbench drawer.
Although, if one so chose, nothing prevent one to install a leg vise, a wagon vise, a wooden planing stop and to bore dog and hold-fast holes in a Paul Sellers Workbench.
So let us only speak about the intrinsic qualities of the basic Paul Sellers workbench.
This workbench has in my view great qualities which are superior to the traditional Nicholson one.
The P.S. workbench :
– has a thick laminated top (as the Anarchist workbench but contrary to a Nicholson workbench);
– the front apron is glued to the top, which makes a very rigid L shaped beam resisting to torsion;
– the two leg-frames are rigid (nothing special here);
– contrary to the Naked Nicholson workbench, no shrinking of the legs will compromise the left-right rigidity because the leg-frames are wedged in housings in the aprons and doesn’t rely on keeping bolts snug;
– the aprons are laminated which minimise cupping risk;
– it can be knocked down if one has to move.
Chris doesn’t like paneled workbenches because it would interfere with clamping. Although it seems that a long enough sash clamp allows easy clamping between the piece on the top and the lower edge of the panel.
The P.S. leg-frame wedging system could be retrofitted to a Naked Nicholson.
Sylvain
To each his/her own — whatever works!
A couple things about the sellers bench. I built and worked at one for four years. Its limitations became very evident to me. I only had room for a bench just shy of six feet. I live Pauls work but he leaves out a lot of crucial information. First is how many record vises he goes through from wailing on boards while in the vise. Not a good practice. The second is how inconvenient his bar clamp in the vise for holding long boards is. The does foot and planing stop is so much faster. I agree that clamping things to it is pretty easy, but no doubt it is easier on Chris ‘s bench.
The bench even with properly fitted wedges tightened down as much as possible the bench has a bit of rack to it. I built a nicholson english joiners bemch this past winter based on Richard Maguire’s plan and the bench has absolutely no rack. It is likely I never will build another one.
The Sellers bench is fine iand has a special place for me and I can take it places and set it uo quickly like at a job site but it never quite satisfied all my needs. Might be different for you.
You will notice I expressly left work holding means and practices out of my description. Because work holding is customisation of the basic workbench structure.
Sorry the wedges don’t work for you.
Sylvain
The hole for the bolt which maintains the apron against the leg-frame must be slightly larger then the bolt diameter to allow some lateral movement of the leg-frame. Otherwise, the wedge will only push the leg-frame against the bolt and not against the other side of the housing.
When the Covid-19 hit and I started to work from home back in March, I ordered the revised version of Chris’ old Workbench book and read it. I’d been frustrated with my old bench for a while, and found many things in it to be very illuminating. I’d seen a friend’s angled leg Nicholson style bench in January, and had been impressed, especially since it was a only break-down portable version and not a fully stabilized permanent version.
I decided to go with the Nicholson, but made numerous adaptations: Left-handed instead of right, not enough room for the angled legs so I used straight, wood that I had on hand (red oak top and sycamore frame) rather than SYP, vise hardware from Home Despot (Benchcrafted is great, but two vise screws for $90 rather than $600 was what I could tolerate), Benchcrafted Crisscross for the leg vise, a secondary shelf to hold two sandbags for extra weight (similar to the cherry Roubo door shelf), front apron only 6” instead of 12 so that I could reach under and push up the dogs, and a few more. The bench has been working great so far.
Then last Thursday a friend sent me the link to the Anarchist’s Workbench, and I proceeded to read most of it on the first day (including during breaks from work). When I got to the part about the long-term usage of the Nicholson I had to chuckle about the issue with clamping stuff to the top—I’d been warned about that. Otherwise I’ve been very happy with my bench, with no issues of top bouncing or anything else.
I will say that among the best attributes of both books is that they cover “why” as well as “how”. This let me make the many changes required for my circumstances with few regrets.
There is a whip in the picture of the workbench (hanging from the wall cabinet). I though LAP did not resort to these methods to get employees to work harder and faster… I though the Anarchist credo was for real! Because this is the internet, I am joking.
That is the “encouragement whip” that we have to use on occasion when teaching tool chest classes.
Seriously though, I have two technical questions that are not answered in the book. The first is because I live 61 North, in the middle of nowhere. The nice industrial bar clamps Chris refers to are not that common and not easy to get: I saw *one* on the local ‘ebay’ (we do not use ebay here), 64 North, pick up only. 10 euros, but the trip is not worth for one. I noticed that on page 224 the image has a buttload of industrial bar clamps + one I beam clamp made by a current manufacturer (that’s my guess). Those clamps I can order from Germany — would they do in a pinch? It might take me 2/3 years to get 10/15 industrial bar clamps otherwise, and cost much more than I beam clamps.
The second question is about laminations. For the legs Chris mention putting the planks bark to heart no avoid delaminations, but said precaution is not mentioned for the top — am I missing something or the bark to heart lamination only matters for the legs?
The parallel-jaw clamps are usually not strong enough to close up all the gaps when you do six boards at a time. So you’ll want to do fewer boards at a go if you use other clamps.
On the top lamination: I couldn’t get the top looking like I wanted with the heart-side-touching-bark-side approach. So I (foolishly) chose aesthetics over function.
I spoke to a friend and I was using the wrong word — I needed to use ‘kiskopuristin’ — which are I beam claps with holes drilled at regular intervals in the I beam. Cheap and still widely available. This is a random piece of info for non native Finnish speakers in Finland. Other European woodworkers might want to get them from the frozen North if they cannot get the stuff Chris mentions in the book in their own backyards.