The method I use to build kitchen cabinets is simple, strong and quick. This allows me to put more time into special details than many commercial cabinetmakers consider justifiable. This post, which responds to Eddy, who submitted the following comment on an earlier one, covers a couple of examples.
“I’m very taken with the cabinets in the 4th photo, the same photo that graces the cover of Kitchen Think. I would love to know how they are constructed. Maybe they are the same as the process you outline except for the cabinet on the right.”
1.
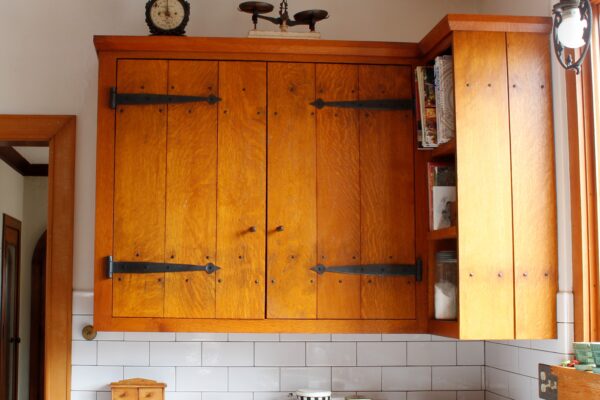
Eddy is correct that the main cabinet with doors is built according to the same basic method outlined in Chapter 3. The finished panel at the left end is applied to the basic cabinet built of 3/4″-thick veneer-core plywood; it fits behind the face frame, as shown in the drawing on p.43. At the client’s request, we made the end panel look the same as the one visible on the right side of the photo here, and it’s screwed to the carcase from the inside of the cabinet.
The narrow open cabinet at the right of the picture was designed to hold cookbooks and jars of dry goods. As Eddy suspected, it’s constructed somewhat differently, though the differences are slight. Instead of building a plywood carcase and applying a finished end, the cabinet is built of solid quartersawn oak. To get the look of separate boards, as our client requested, my employee at the time, Daniel O’Grady, who was the principal cabinetmaker on this job, constructed a cabinet side by nailing the two boards to cleats. You can see the location of the cleats from the nails. I wasn’t concerned about wood movement because the boards are only about 6″ wide and quartersawn.
I don’t recall what the other side is made of. It could be a 12″-deep piece of solid quartersawn white oak or a pair of boards. The point is, once the two-board panel was assembled, Daniel treated it just as he would a piece of veneer-core plywood. It and its mate on the opposite side are joined to the solid top and bottom of the cabinet by the same means as I describe in Chapter 3. One other anomaly of this cabinet: Being open, it has a shiplapped oak back to match the general character of the cabinets.
2.
The suspended glazed cabinet here, in the kitchen of Fritz Lieber and Donald Maxwell, is another anomalous example. I originally designed this cabinet to be attached at the wall and have its finished end extend down to the counter. The general contractor, Bert Gilbert, suggested that instead of blocking off part of the counter with the cabinet end we could hang the cabinet from the beam you see here. It was my first experience with all-thread rod, but not my last! Kudos to Bert for this suggestion.


This one is built quite differently – more along the lines of a showcase fitted with a “window” on the public side and two doors at the front. The basic case consists of three frames constructed with mortise-and-tenon joinery. The end at the wall is veneer-core plywood. For more of a furniture look than that of basic kitchen cabinetry, I mitered the stiles of the three frames at the finished end so that they would show quartersawn figure on all sides. I then glued the frames together at the mitered ends and reinforced the joints with brads.
Here’s a plan view drawing. (It’s intended to show the principle, not the actual dimensions.)

Every kitchen I do has multiple anomalous features. They keep me sane, always providing new challenges.
– Nancy Hiller, author of Kitchen Think and Making Things Work
Editor’s note: “Kitchen Think” is now at the printer and will ship in early August. We are now taking pre-publication orders for the book. If you place your order before the book ships, you will receive a free pdf of the book at checkout.
Staying sane is good!
Beautiful work, as always.
Very helpful. Thanks Nancy!