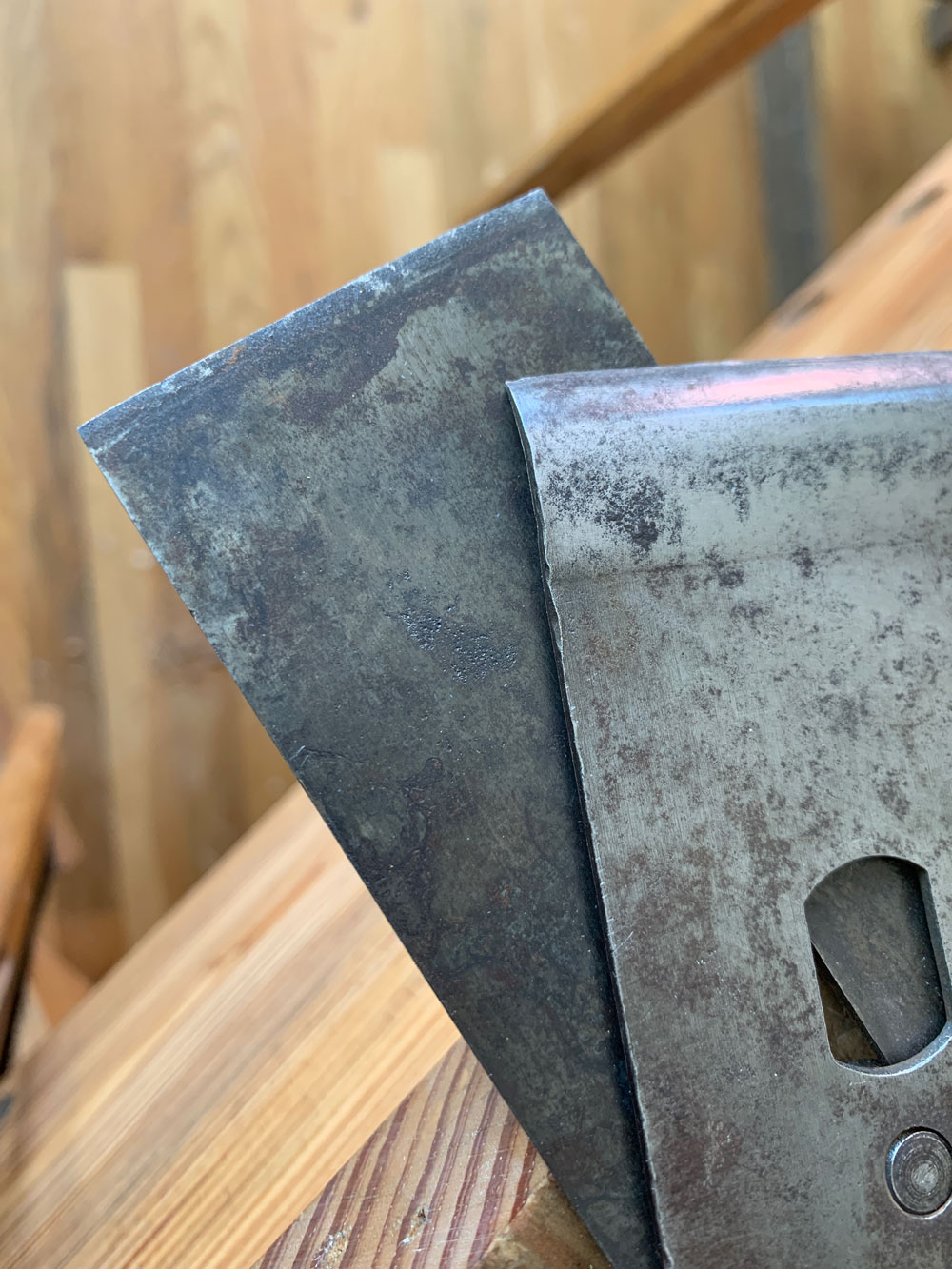
I promise this post is not about sharpening. It is, instead, about what we read vs. what we see.
When I learned to sharpen, the entire first day of my lesson was all about flattening the backs of my chisels and plane irons. I was told to get them all dead flat and then polish them up like a mirror. It was a whole damn day of my life I wish I could get back.
When I started buying vintage tools, however, I looked at the backs and thought: I don’t think those people had the same teacher. I’ve examined hundreds of vintage planes and chisels, and I can recall only one or two that had the backside of the blade flattened or polished.
Sure, some of them looked like they had been pushed over a stone to remove the wire edge after sharpening the bevel. But not flattened and polished like I was taught.
Most 20th century instructions don’t talk much about the backside of the tool. You are supposed to work the bevel and then remove the wire edge by rubbing the back flat on the stone. (The Stanley instructions above are typical, which are from a 1941 booklet.)
Joseph Moxon, who wrote the first English instructions on woodworking, discussed this issue in “Mechanick Exercises or the Doctrine of Handy-Works” (1678). He wrote that after you sharpen the bevel of the tool:
“Then turn the flat side of the Iron, and apply the Stone flat to it, till you have worn off the coarse gratings of the Grindstone, on that side too.”
Basically, you have to stone the bevel and the back. The instructions were clear in the 17th century and they are clear now. So why does the archaeological record – at least what I have seen – seem at odds? Why are there so, so many tools out there that have been sharpened on the bevel but not on the back?
I think about these things a lot as I work at the bench. And I promise I do not have any answers. Only thoughts. Here are a few of the possibilities I’ve considered.
- Perhaps most of the extant old planes and chisels were used for carpentry (in softwood) or by homeowners. So getting the wicked sharp edge needed for tricky hardwoods wasn’t necessary. So the back remained mostly untouched (except for removing the wire edge).
- Furniture makers need a really sharp edge, but that profession has always been a less common one than carpenter. So the well-treated tools are much less common.
- The good tools that were sharpened properly were mostly used up. The tools that weren’t sharpened properly survived because they weren’t used much (perhaps because they weren’t sharp).
- Modern people have a much more extreme idea about what a polished edge should be. We take it beyond what was typical because we have the abrasives to do it. A mirror polish might be better in theory but it might not be necessary in actual practice.
- The user decided to go for a flat and polished back in a gradual fashion – by stoning the backside over and over as they sharpened the tool during the day/month/year. In other words, the tool would get gradually better over the life of the blade.
- We are too precious about our finished surfaces. A few errant grinding marks on the backside that transmitted to the work can be easily scraped or sanded out by hand.
I have a lot of other possibilities rattling around in my head, but the above six are enough for a blog entry. During the last two years I have been experimenting with these different possibilities with my own edges. I’ve learned some things that are definitely not doctrinaire with modern sharpening theory. But I’ll save those for when I’m ready to endure an old fashioned Internet thrashing. Today has been too much of a Monday.
— Christopher Schwarz
I wonder if it’s possible to trace this trend over time through the literature. If one look at books and magazines through the 20th century is there a point when the obsessive polishing became more of a thing?
Chris, there is a tendency, I think, amongst some woodworkers to become overly precious about flattening and mirror polishing the flat side of both plane irons and bench chisels, as well, perhaps of overworking the sharpening process for every job. On the other hand, it is essential for a sharp edge that the two planes of the flat surface and the honing angle meet precisely, i.e., for example, it’s not rounded so that when looking at the edge you don’t see the ‘line-of-light’ indicating a dull blade, being one that has either been dulled in use, or one not sharpened properly.
I think the flat side of the blade has always been there as a requirement, certainly in the more refined work of perhaps a furniture maker. But flattening the whole length and width of the flat side of chisel or plane blade was never something that I was shown by the furniture makers that taught me when I first trained. They only bothered with properly flattening the last 1/2″ or 1″ of the flat side of a new blade. Subsequently, repeated sharpening gradually extended this initial flat surface further back towards the blade’s slot.
I don’t know if my sharpening practice is nowadays unusual, but more often than not I’ll start sharpening a dull blade by working the flat face a bit first before I turn over and hone the the bevel, followed by working the flat face again, and a bit of stropping on the palm of my hand before getting the tool back to work. And I generally only sharpen on one stone, e.g., the finer face of a combination oilstone or a ‘coarse’ ceramic stone (depending on what kit I’ve got to hand wherever I’m working) for most general purpose planing, but I do go up to an ultrafine ceramic stone to get a keener edge for the final polish prepping stage of planing wood. The reason I frequently start on the flat face is to keep that face flat at the tip where a bevel down plane, in use, abrasion on that flat face by the wood being planed can wear that metal just enough to cause a slight rounding over.
Anyway, that’s my theory, and I’m sticking to it, ha, ha.
Paul Sellers has made mention of this several times over the years. I really don’t know which is true. I don’t know how many myths tool makers have created and how many are the gospel truth. All I know is that I have one vintage plane blade that I have not polished the back but have flattened it. The comparison to my other blades after sharpening in terms of sharpness seem to be identical. I cannot feel a difference. Having said that, I do know that there is great benefit in flattening and polishing the backs of moulding plane irons. I can get the blade sharp just by working the back alone.
Ever wonder why we call the leading edge of a plane iron the back?
I do think we can more easily go overboard with sharpening today, given very fine diamond grits and even finer waterstones. And, for many of us this is a hobby and our first goal is not to finish a job quickly.
Personally, I use diamond and finish with waterstone. A well polished back on a plane iron makes it easier for me to quickly resharpen the edge. But, on the back, only the surface from the cap iron to the edge really matters. Beyond that area, a good polish is nice to have for future sharpening, but matters not today.
None of the used tools I ever purchased ever had a polished back. Some of the chisels I bought were half beaten to death and all my planes clogged because of the poor fit between the chip breaker and the iron. Today it’s much easier to polish and flatten the backs with all the abrasives at our fingertips, I actually remember not being able to afford a set of diamond plates with all the grits I could ever want. Today we are bombarded with different sharpening systems and you can just order them on the internet with easy payment plans.
I personally like the look of a polished chisel, some times it reflects back enough so I can see that I’m in my knife line. Other people don’t care, opening paint cans isn’t any easier if the back is polished. For me it’s really about maintenance, if the back isn’t shining back at me there is gunk. ( probably glue) I forgot to clean off.
As an old guy who has worked with a lot of older Craftsmen, I think the answer is simple. All/most of these old guys are Very practical. They don’t/didn’t have the time to sit for an hour or two and polish the backs of their plane blades. They were manly interested in make chips. In other words, the work. Does it cut? That’s really all they cared about. Now days you hear conversations about angles and how fine of an edge. Like one old guy said to me, “Your not polishing the family Sliver. As long as it cuts your good.”
I knew an old boatbuilder who had a single piece of old cryistalon as a stone for his side axe. With that and spit he created ultra sharp edges. He claimed it was technique, not stone, that provided the ultimate ingredient.
Perhaps today’s woodworker is much more vain than yesterday’s. The mirror polished back allows another opportunity to gaze at ones own reflection.
Here we go.
Do we know/can we tell if small imperfections in otherwise perfect period furniture (or house fittings) were from the maker or from time? I mean some tool marks would be obvious but others? Im not a “good enough” person, but at some point it doesn’t matter. Think about the room you are sitting in, guaranteed its not square, nor the walls exactly plumb or flat. The room still seems so to us so therefore it doesn’t matter.
Serrated knife edges are actually a real thing – this is in effect what results if the bevel is quite polished and the back is not. There are limits to this backside roughness of course, and a few swipes to remove the wire edge each time a sharpening occurs would get the job done – especially over time, as in your #5. Think about it; a “micro-serrated” plane iron pushed at a skew to the work is sort of like a saw with teeth – maybe that’s part of the reason skewing works so well to ease the effort of a cut.
I agree with your #4, modern craftsmen, likely being a majority hobbyists, have very different notions of what a polished tool edges are, as well as what a smooth finish-ready wood surface is, than did craftsmen whose dinner table depended on production. This is a distinctly modern and 1st world compulsion. That doesn’t mean we can’t have fun with it though!
Chris, you are a brave man. LOL!
Chisels and plane irons warrant different approaches. Chisels are self-jigging and should have a flat back. The back of a plane iron need only be flat enough to seat well on the frog, infill or bedding. BUT both chisels and plane irons must have burrs removed to work at all, and coarse serrations should be removed for them to work well. How far you go down that road, using finer and finer abrasives, determines how fine the finish they produce, how strong the edge and how long it stays sharp. Multiple microbevels are easily established and minimize the effort required to sharpen and maintain an excellent edge. Bret Beach has illustrated the rationale for this, and the methods for achieving that. This improves on the so-called Scary Sharp method.
http://www3.telus.net/BrentBeach/
When I buy a new/old and abused tool, I flatten the back. but only the first inch or so then I take the bevel to were it should be about 25deg. Then after that I only take it to the stone for 10 strokes on the bevel and maybe 5 on the back.. I would rather work the wood than waist time standing at the sharpening station. if it looks right it is right. There are some people that spend $1000.00’s on sharping equipment. me a 3 sided oil stone and a slip stone.
I think you need revise your sharpening strategy. Just as there are people who over do the process of sharpening and I believe I am guilty of that, but you my friend under do it. I don’t believe unless your steel is in an annealed state you achieve any level of sharpness with such few strokes. You probably rely mostly on your strop.
I don’t use the strop much and my system works great. if I feel that my plane or chisel is dragging a bit I reach for the stone. I tell my students if you think it needs sharpening then go hit the stone you don’t need to ask. I do woodworking as a job so my tools are always sharp.
You are the one who is wrong here, Salko Safic. On any edge tool, if a primary bevel is ground really close to (and there’s no point going right up to, that’s a waste of time) the cutting edge, literally a handful of strokes on the secondary/final bevels can suffice. I am blessed to own some amazing ‘old steel’ tools – mostly through the sheer luck of inheritance – and (when I get my sharpening process just right, which is not always) I can raise a fine wire burr in less than 10 strokes on 1000 grit wet&dry. The steel they’re made from is definitely not in a relaxed state. 2 or 3 strokes on the back of the blade removes the burr. 10 or so strokes on the strop & I’m done.
We need to remedy that a sharp edge is simply an intersection that has a ‘zero radius’ curve* to it between 2 surfaces. The angle of intersection and the flatness of the surfaces are irrelevant to whether or not the intersection results in a sharp edge – and the burr is the best symptom we’ve got that we’ve brought two surfaces together with as close to a zero radius curve as we need. How one gets there is just mechanics. It matters less than that those edges are brought together with as close to a zero radius curve as the work we’re doing requires.
A pair of *flat* surfaces intersect to produce a geometrically *straight* edge. The angle of the intersection affects a) how easy or hard it is to get the edge tool to penetrate the work piece’s surface, and b) how long the edge remains sufficiently sharp for the purpose it’s being put to when in use (this in conjunction with the quality of steel the tool’s made from). A straight edge and an intersection angle within a particular, highly defined range are very desirable in some edge tools – but they don’t of themselves make the tool sharp.
And please don’t confuse ‘smooth’ and ‘flat’ with each other either. Smooth/polished only affects what proportion of the 2 surfaces truly intersect at the limit of the edge between them. Highly polished surfaces can intersect in a blunt edge. Scratched surfaces can produce edges that are sharp along their entire length, although not all of that edge will lie along the line of the extreme limit of the intersection.
And Paul Sellers is right (for instance) when he says that properly sharpening even only as far as 250 grit will actually do for the vast majority of woodwork – even fine furniture work. Going to 10,000 grit & beyond is nice – it is even necessary, sometimes – but it isn’t totally, absolutely necessary each & every time. Whatever we ‘modern’ wood-botherers have got into our heads. “Sharpen the tool *enough* to do the task we *need* to do with the ease and to the quality with which we *want* to do it. Then get back to doing the task. Sharpening is a means to an end, not the end itself.”
——————————
*A theoretical concept only, as even atoms have a radius, so no 2 surfaces can ever come together with a truly zero radius curve. But we can get close enough for jazz.
😡 Bloody predictive text!
“We need to remedy that a sharp edge is simply…” should have read “We need to remember that a sharp edge is simply…”
Sorry!
While I do not wish to argue over sharpening, I do wish to end with this statement. I have never experienced sharp with ten stroke or less straight from the plane. I have however achieved sharp with minimal strokes after I having put the blade to the stone direct from the grinder which coincides with what you said above. But fresh off the plane with a full bevel, I fail to see how it is possible. Please note I am referring to the difficulties in sharpening modern A2 blades and not the thin Stanley O1 blades. Watch the toolmakers jump in now.
😁
Similar trend among Asian woodworkers?
I say 4. and 6.
Do you know if the plane irons in the Henry O. Studley cabinet were flattened or polished?
I just ordered the book and maybe the answer is in there but the suspense is killing me.
Long time reader of your blog, thanks for all the great information.
I have the book but loaned it to a friend so can’t verify. As i recall, he did not polish the backs of his plane irons.
I have the book, but it’s on loan to a friend so can’t verify. As i recall, none of studley’s plane blade backs were polished.
I used to think woodworkers were overly obsessive about sharpening/honing until I started shaving with a straight razor and had interaction with that community. “Do you know the provenance of your stone? Where, when, and by whom it was mined in Japan…?”
My theory is a bit more cynical – for some woodworkers (and an even greater percentage of internet woodworkers), playing house in the shop – be it building the “ultimate” work bench, polishing their machines, building adjustable and over engineered jigs, or polish iron and chisel backs – is their true hobby/profession. These people tend to build very little furniture. How could with all the time spent playing house?
Hi Chris,
Have you seen the same thing across vintage plane irons used for different tasks? (i.e. smoothing planes, scrapers, mounding planes etc used for “finish” work vs irons in jack and other “roughing” planes)
Thanks,
Patrick
Chris, what is it about a blog on sharpening that attracts so much attention and interaction and flogging? Such a strange topic to get all exercised about. I do like and appreciate your musings, and can see merit in all of your proposals. I think that for most professionals, the tool is not something to be loved – it is a means to an end. When the tool no longer serves the purpose, it is set aside for one that does the job. This is unlike many amateurs who love their tools because they are in love with the idea of being a woodworker, but haven’t had to make it work financially.
Your first three reasons came coming before I got to your list. I know a full time handtool woodworker who says he burns through a plane iron in a year or two, he prefers thin irons. I also agree that most modern hobbyists take certain aspects of the craft to illogical extremes.
My spellchecker thought the word ‘coming’ was better than the phrase ‘to mind’. Not my idea.
Your mother was a hamster, and your father smelt of elderberries! Wait, am I too early? Either way, I’m too fed up with this report I’m working on to make an original flame post.
I’m with woodworkerme above, if it cuts it’s good.
This was refreshing to read your thoughts, experiences, and/or opinions on a subject that so many tout their perceptions as archival fact.
Thank you for nudging the conversation.
My go to bench planes are infills made by Spiers. I have had probably 40 or 50 over the years. They were expensive in their day and were used by cabinetmakers, who took good care of their tools. When I get them they might not have been used for 100 or more years. The backs of the irons are always polished. They might be tarnished from sitting for years, but they are smooth and clean to a high polish with very little work. They are rarely dead flat, mostly high in the middle, from a stone with a slight belly in it. This didn’t matter to the original owner as he always used the same stone so the blade would wear with the stone. The same with chisels and molding planes that were used by cabinetmakers. I believe the degree of preparation of blades depended on the grade of work being done.
Look at the stones they used? Small, slow, and the good stones like Arkansas were $$… plus you had to have oil.
Today we have many ways to flatten backs, and over flatten backs too.
Navnet ditt … Norsk ?
Wicked sharp is fleeting. But, I can’t tell you how much joy I get from hand tools that are wicked-sharp. I personally think that if the old-timers had the stones we have today they would have used them. I also think wicked-sharp and polished backs means that I can spot damage or realize out-of-square, just better inspection and understanding. I don’t know if everyone does this but I do the back polish first even on new tools. I have no regrets for the work put in to keep my tools nice. I’m a “legacy apprentice” as I call myself because I come from a submarine engineering background and my dad gave me his power woodworking tools late in life. I threw away his one hand plane. He had destroyed it to say the least. He was a power tool guy that built sport fishing boats. I was about 53 years old before my cabinet/tool maker friend gave me a card scraper. So now I saw for economy and then look to my well-maintained hand tools for prep and finishing. Keep polishing those backs.
I’ve been a professional furniture maker for 25 years ( I do a fair amount of hand-work) and I used to sharpen / hone free-hand on diamond stones. I thought it worked OK. Last year I started experimenting with an Eclipse honing jig and 3M-abrasives on glass (‘scary sharp’). Now I use micro-bevels both at the front & back and I repeatedly & consistently get a level of sharpness I did not know existed before. I spend a little more time honing (and I’m getting faster as I gain experience!), but the edges last several times longer. It works for me 🙂
Sharp or not sharp. Set that aside for a moment.
What if you just like it to be shiny?
Well, this might kinda sound silly, but here goes…
When I started WWing 32 years ago, as a consolation for not getting to live in the back of my pickup (I had a real job at last) I started cruising around buying antique tools. I was raising money for the university, so I would occupy my time in between those calls for begging with cruising antique shops. Inevitably, I’d find a $25 rush, buy it, and squirrel it away for my collection.
No one was either really WWing, or collecting hand tools, so it was always about $25.
I came home with all these tools, and well, being a Catholic, I started feeling guilty. I’d look at all those planes (I have over 90) and think “well, those should be sharp. And the first step is to flatten all their backs.” So I developed a meditative practice of polishing the backs on Japanese waterstones (finishing with a 8000 King stone) while I watched TV. This was back when TV was still a thing.
I ended up with 90 planes that I can pull off the shelf (spoiler alert — you only need 4 planes) and they are lovely. I also had a granite flat I flattened the bottoms of the soles. I pulled a Stanley 605 out the other day for righteous reasons, and it worked beautifully.
I actually build furniture — I am a tool collector, but I really do build furniture. Is it probably stupid that I have 90 planes with mirror backs? Well, yeah. But it’s stupid to have 90 planes anyway.
At the same time, I don’t smoke nor chew. So, consider it as my own affliction. The upside? You can give me a blade and a stone, and with no effort at all, after all that practice, I can give you a hair-shaver in about 1 minute. So there’s that. So glad I banked that skill. Most of us waste far more time than it takes to flatten a back. Assume the role of meditative practice. It’s good for the brain! And your planes will work great. Well, the four I always actually use!