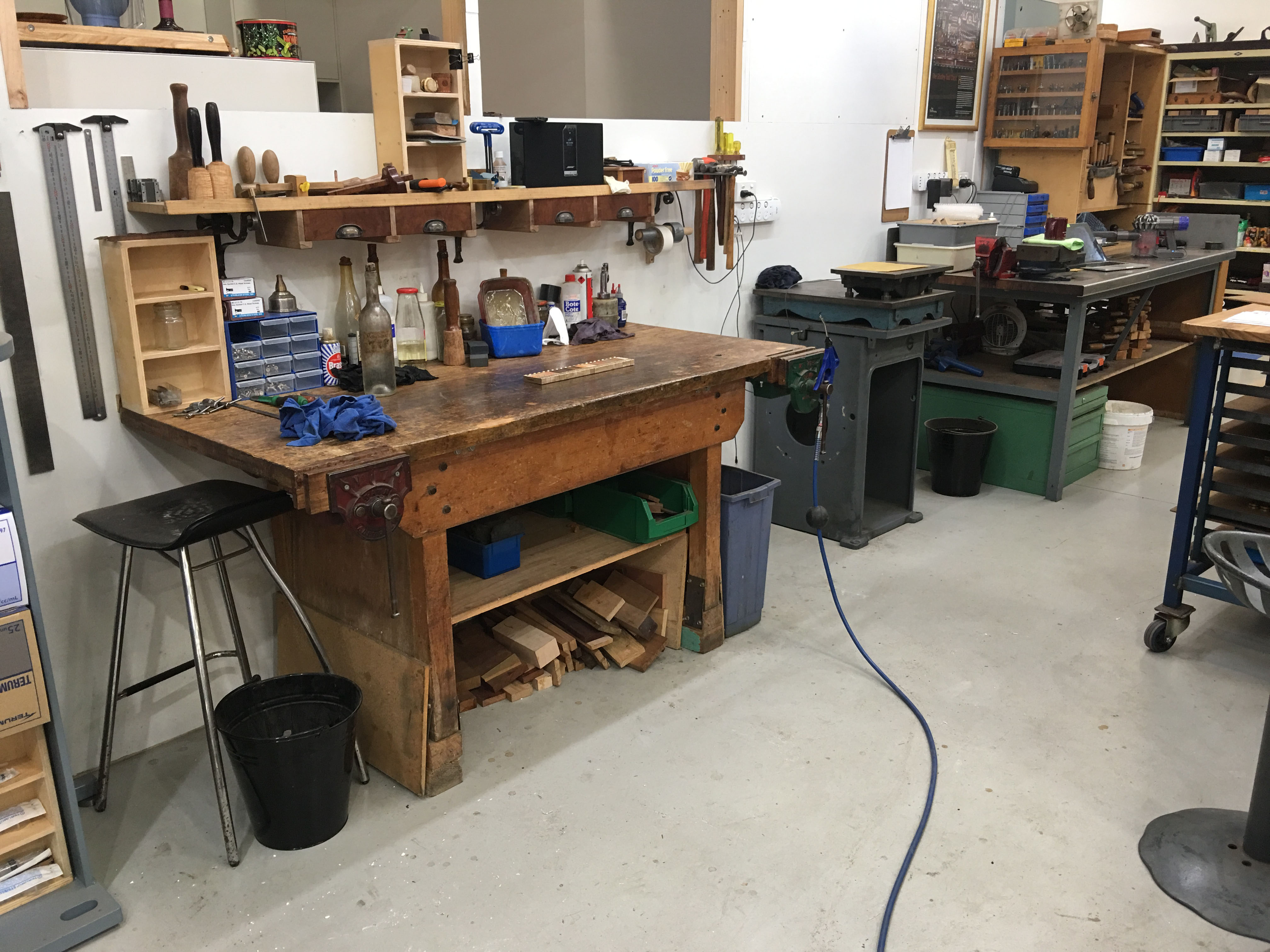
Kara Gebhart-Uhl, Christopher Schwarz and I have selected a few of our favorites from “Honest Labour: The Charles H. Hayward Years” – some have already been posted; there are some still to come. Chris wrote about the project that “these columns during the Hayward years are like nothing we’ve ever read in a woodworking magazine. They are filled with poetry, historical characters and observations on nature. And yet they all speak to our work at the bench, providing us a place and a reason to exist in modern society.”
Our hope is that the columns – selected by Kara from among Hayward’s 30 years of “Chips from the Chisel” editor’s notes – will not only entertain you with the storied editor’s deep insight and stellar writing, but make you think about woodworking, your own shop practices and why we are driven to make. When Australian toolmaker Chris Vesper (vespertools.com) read “A Kind of Order” it prompted him to write a few responses – read the first, “Everything in its Place,” here; another is below.
— Fitz
Time Saved is Time Gained
One thing I’ve observed from many years of visiting all types of workshops all over the world: Everyone does it a bit different. There is no right or wrong; it’s what works for you with as little judgement as one can muster. But I have found that certain things can increase shop efficiency and personal enjoyment quite remarkably. Like stepping back once a year for a really good clean up and a think outside the box to re-organise things. Buying or making new storage for your tools (not some latest plastic storage gadget that promises to upend your life with happiness, but genuinely practical ideas like robust drawers, shelving, cupboards, racks etc.). Maybe move the workbench or a couple of machines to suit you better. Chances are if you’ve been thinking for 12 months that you really should move that material rack but haven’t, you probably should have moved it 18 months ago.
One extreme of a workspace is a floor you could eat off during work hours and barely a tool out of place – because everything has a place, and all is organised just so. The other is what appears as mess and utter chaos to the casual observer (hopefully not on the level of compulsive hoarding – that’s not healthy for anyone). But the keeper of said chaos will likely know exactly where everything is, able to reach into the darkness of a dusty corner shelf or bottom drawer and procure quickly any requested item, no matter how obscure. Many people who operate at both extremes (and everything in between) are perfectly capable of producing beautiful work in a reasonable time frame. Some work in an eternal mess; some simply cannot do this. The manners of the brain are an interesting thing.
I prefer the cleaner and more organised end of the shop spectrum – especially working as a one-man business in a very poly-technic workshop (woodworking and metal working, along with a few other tricks like laser marking in house, metrology and some hobby welding, restoring an antique machine). Forget pride or satisfaction – I genuinely find much efficiency is gained from knowing EXACTLY where a certain tool or device is, and being able to lay hands on it immediately – no rummaging through the sedimentary geological layering that sometimes happens.
I ponder my early struggle to separate the precision metal working stuff from the ravages of woodworking dust. Apart from the obvious of using better extraction than in my early toolmaking days, I’ve now overcome this problem completely by simply putting things away and keeping the things that are not like the other separated. This is relevant no matter your shop size. Small shops need to keep ahead on organising lest conditions degrade to the point where one could have difficulty getting in the door due to the goat track having suffered an overnight avalanche (not to mention fire risks and other more serious safety matters). In larger shops it’s also critical as one does not want to waste time walking to the other side of a shop only to realise the item required is somewhere else.
One method I’ve found to be immensely convenient is to have many smallish rubbish bins (trash cans, y’all) placed strategically and unobtrusively around the workshop, sometimes grouped around a specific work area. Nothing fancy. Old paint buckets or similar receptacles mean I am never more than one step – or at best an easy lob – away from a bin. I’ve found it best to have several per area, including one at either end of my benches. So with two benches in my work area and a table in between them, that means I have four bins there alone to cover two benches. Works a treat.
It saves so much time and eliminates double handling when cleaning up your own mess, even in a small workshop.
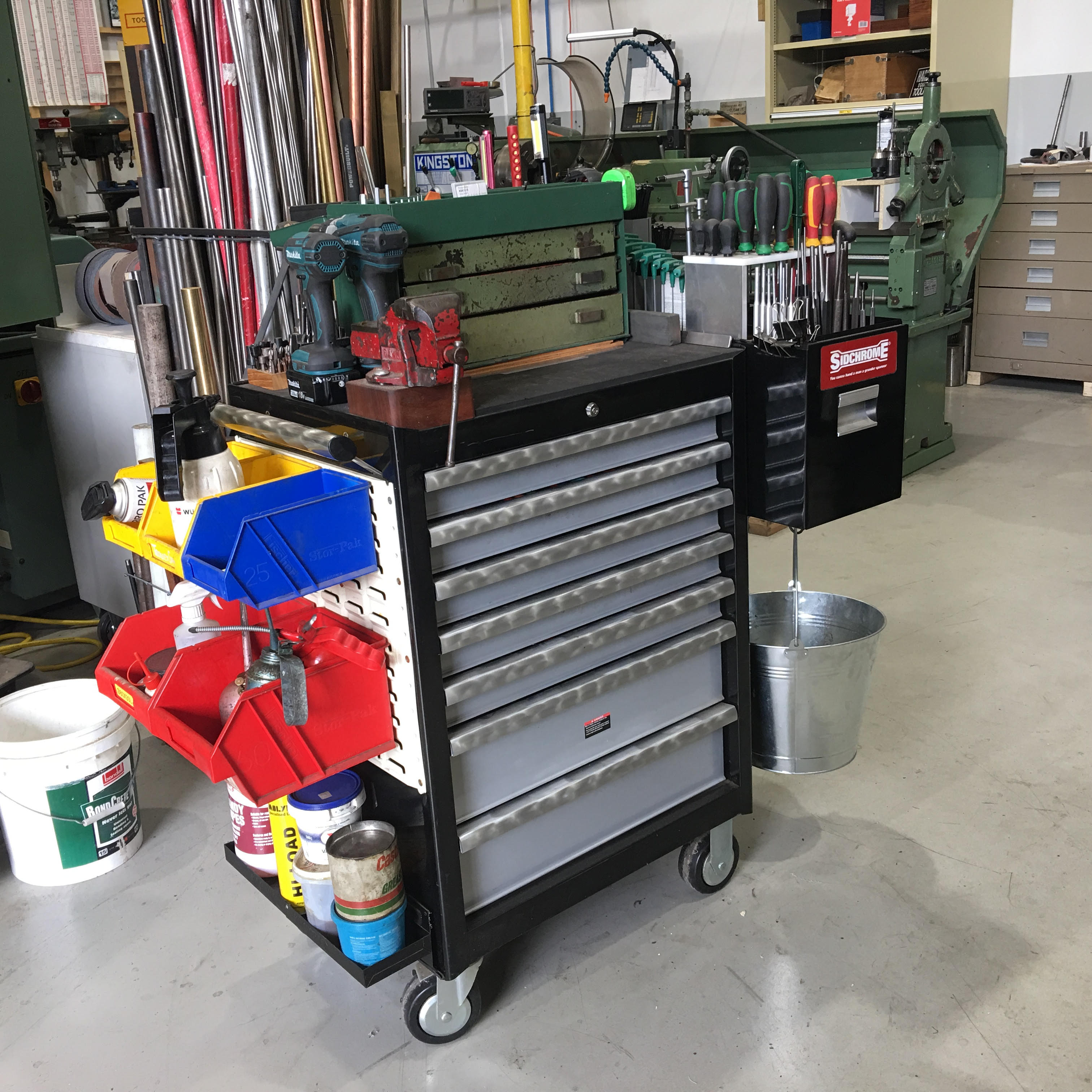
This ethos was hatched one day whilst I was absorbed in a job and needed to chuck something in the bin. I had to walk several steps to chuck it, walk back and make a second trip (and I likely dropped something along the way).
Think on how many steps you walk to throw out a rag, or the packaging of something you just opened. Consider if you can turf it with little care or precision into a bucket probably less than one meter (about one yard, y’all) away from your body, then not give it a thought until you empty all the smaller bins into your main bin (which I do perhaps once a month). Sure that part takes a little time, but is a small investment in your own time compared to what you’ve already gained.
“Goat path” and “rubbish bins” really resonate with me for different reasons.
For just over a year I lived with a snaking goat path in my garage shop due to storage of raw material and incomplete projects. I finally gave myself permission to not complete those three large projects; actually finish one on a less grand scale and abandon two. I have already broken down the two for more immediate needs. I can now walk from the door to the bandsaw without break dancing.
I long discovered the utility of the 5 gallon bucket. It all started when the kids were young. The bucket(s) were handy transport and instant toy when needed. Every tool and work area in the shop has a 5 gallon bucket within arms reach. I empty them into the large cans, or fire pit, as needed. Often I reach into one for a useful scrap, too.
My shop is by no means living in a state of cleanliness, but the above are two key things that make life in the garage happier.
Congrats on letting go of some old projects you finally realised you weren’t going to complete. I should take a leaf out of that book I think… 🙂 Interesting you also discovered the 5 gallon bucket everywhere trick too, good to know I’m not the only special person like that out there…
I didn’t actually need the translation for “rubbish bin” and “meter”, but what the heck is a goat track? A misspelled coat rack? A tracked storage thingy? Whatever perverse thing Urban Dictionary made up (I refuse to look).?
You have to be nimble and jump on and over things to navigate it, was my take.
I take it to mean a narrow and winding path (such as goats might make across a mountain side) in between heaps of stuff and piles of junk and what have you, when the shop is so chock-a-block and/or disorganised that that is the only way to make one’s way through it.
Mattias
Visualise an access path that will quite likely cause injury if unaware and requiring great dexterity. The workshop could also look like a ‘ dogs breakfast’ , a mess.
Yes the other folks are right on it, goat track to me means a narrow perilous track through questionable terrain for human passage.
After 9 years of planning and saving we recently remodeled the other work area in the household, the kitchen.
All the things you mentioned here hold true in every workspace we deal with.
The refrigerator, sink, and stove correspond to the workshops main workcenters. Not a direct mmatch but the anology h