As we near the home stretch on our forthcoming book about kitchens, we thought it would be fun to publish a series of posts about a kitchen remodel on which I’m now working. You can read the first post here. Upcoming posts will discuss aesthetic dimensions, sources of hardware and other products, etc.
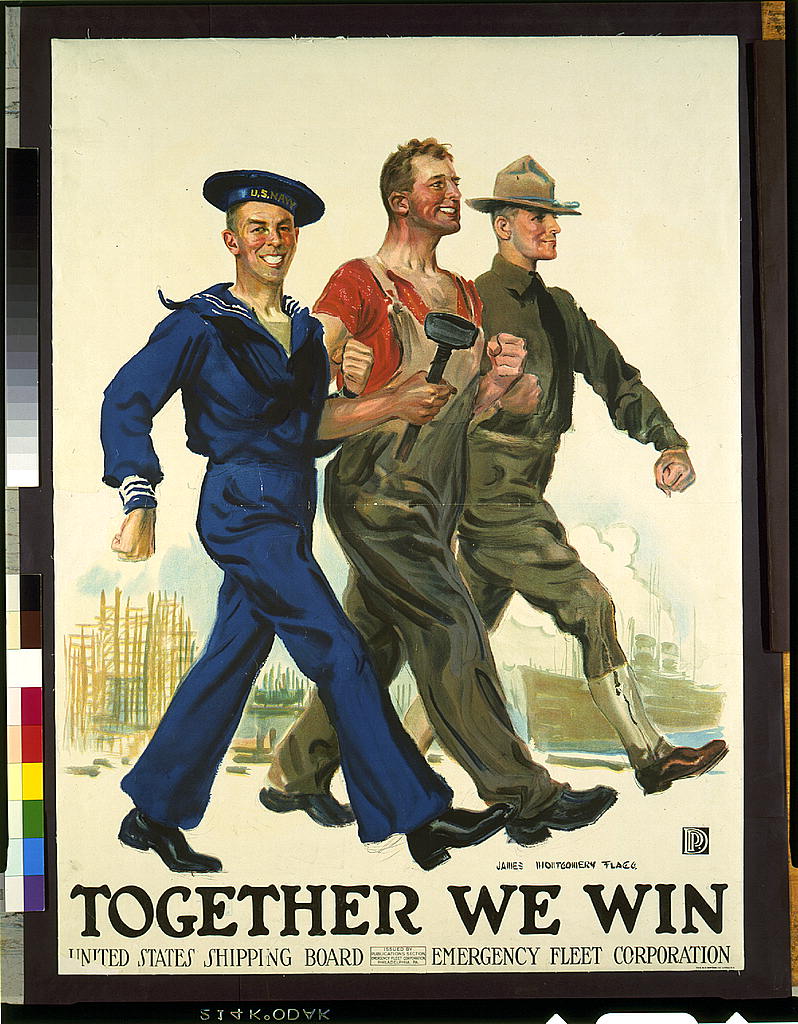
At the start of this kitchen project, the contractor, clients and I scheduled the work onsite for June, when Jenny and Ben would be in Austria in connection with Ben’s job. Then came covid-19. There may be no trip to Europe.
As veterans of many a kitchen remodel done with customers living in their home, Mark and I have ways of minimizing the pain. These include:
- dust collection for power tools
- dust barriers between the work area and the rest of the house (This includes covering HVAC vents to minimize the spread of dust through that system.)
- floor mats (such as this one) that pick up dirt to keep it from being tracked out of the job area
- clean up at the end of each day
- a temporary kitchen set-up with a sink and counter (or table). We move the fridge into another room so it can keep storing food. A hotplate, crock pot and toaster oven will cook most meals. An outside grill will even make cooking fun.
We’re still set for June, though at this point all plans are subject to change if someone gets sick — or if the government imposes a directive to shelter in place. Even without such a directive, Mark and I have changed how we do business in the interest of minimizing contact with others.
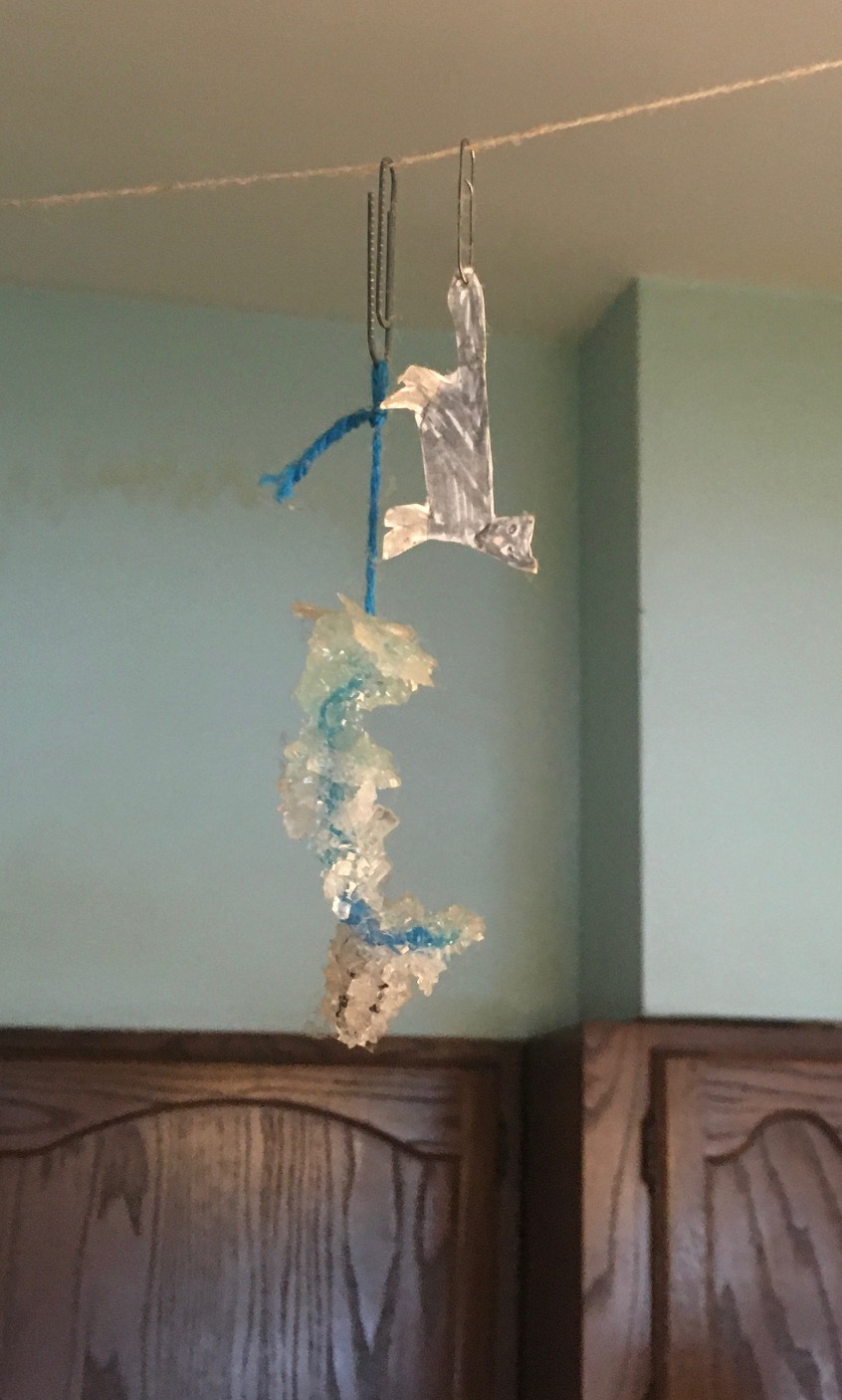
As bars, restaurants and businesses with potential to disrupt supply lines have been shutting down en masse in response to the pandemic, it occurred to me that I should get as many of the materials as possible in hand without delay, in case my suppliers have to cease operations for several weeks. So yesterday, after confirming that Ben and Jenny were ready to go forward, I put together my primary materials orders and called them in — the solid wood and sheet goods order to Frank Miller Lumber, the hinges, drawer slides and blind corner storage unit to Richelieu Hardware, two of my most dependable suppliers for more than 15 years. At least this way I should be able to stay working and keep the job on track.
Existing cabinets: Should they stay or should they go?
In an ideal world, x-ray vision would enable us to see through cabinets, counters, walls and other solid materials to determine the location of ducts, electrical wires, gas and water lines and other things with potential to throw a wrench in the works. Locating such objects is especially important when you’re reworking the layout of a room; you need to assess whether your design can in fact be implemented. (While it’s true that anything can in principle be changed, the budget available for a job usually plays a big part in determining what “can” and “cannot” happen.)
To keep the household cooking without interruption for as long as possible, we’re leaving the existing kitchen intact for now. The basic layout of the cabinets will stay the same, so there’s no mystery about rerouting services. But there was one area I wanted to check before I start cutting parts for the new cabinets, the framed-up structure that housed the wall oven housing — just to make sure there was no surprise lurking inside. So yesterday Mark and I took out the wall oven (which no longer worked) and excavated a small portion of the wall to confirm there was nothing there beyond studs and plaster on metal lath. Before pulling the oven, Mark removed the appropriate fuse (yes, the house still has fuses, not breakers; installing a new panel will be part of the project) and covered the wires with wire nuts. After cleaning up the debris, he screwed a scrap of plywood over the over-sized hole to keep the resident kittens from potentially perilous exploration.
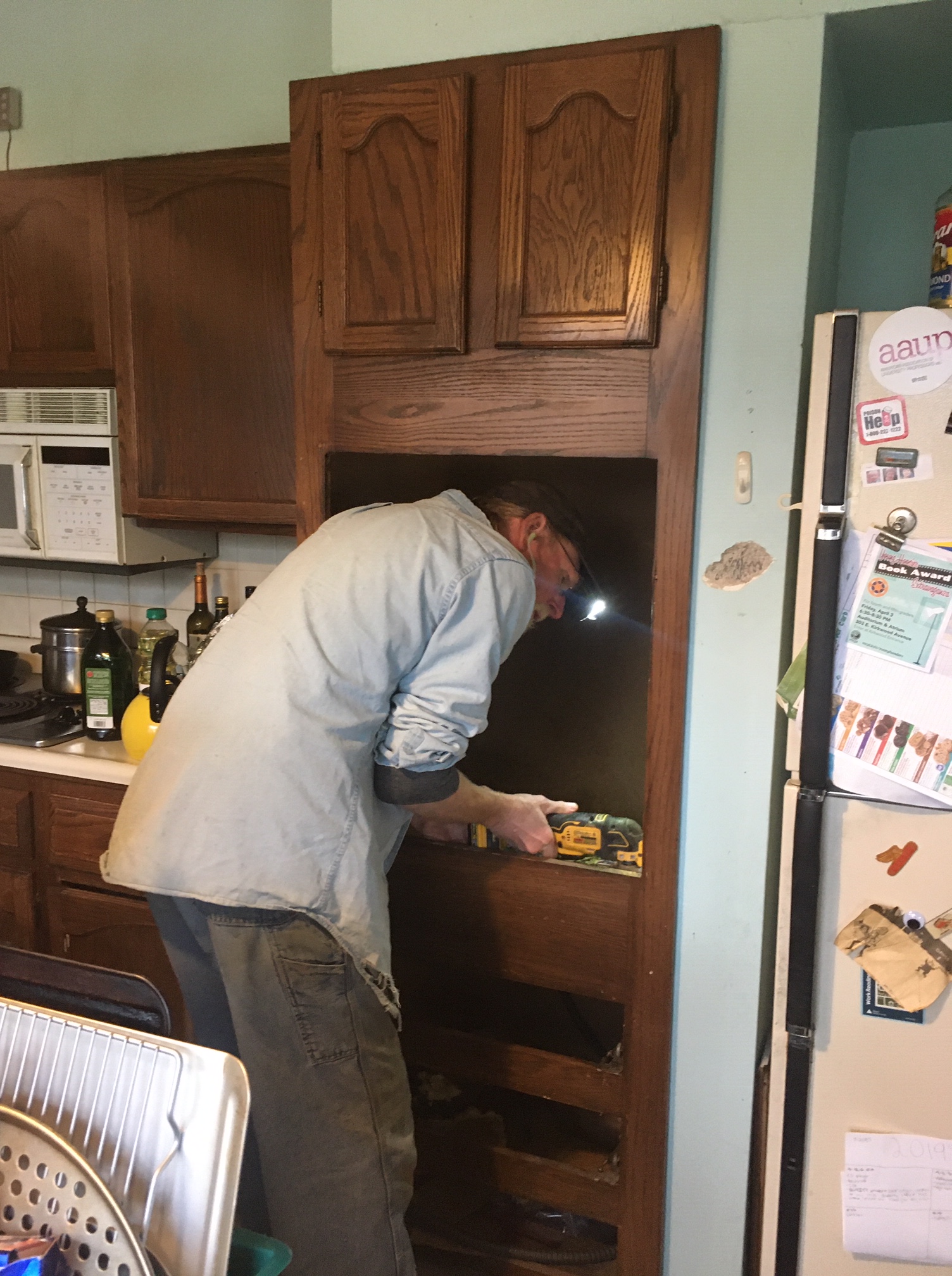
The other structural detail we needed to check involved the staircase. Between the living room and the kitchen there’s a passageway about three-feet wide — plenty of space to move through easily, in theory. But in this case, the stairs to the basement loom like a chasm on one side. While the stairway poses no actual danger, it’s close enough to provoke a slight sense of risk — the kind of distinct yet largely subconscious discomfort that kitchen designer Johnny Grey has argued — convincingly — should be avoided.

It’s not feasible to relocate the staircase as part of this project, but it occurred to me early on that it might be possible to shift the stairs forward by the width of one tread, and so add almost a foot to this narrow passage to make this traverse a bit more comfortable. Shifting the stairs would require raising the wall above the staircase base (see the image below) to gain the headroom code requires. This wall, however, is a major support for the roof, so I wanted Mark to take a good look at how it relates to its surroundings and determine whether he’d be able to modify it. (Before you think about modifying a wall of this sort it’s essential to consult someone who can assess the structural ramifications. I often refer clients to a structural engineer, but in this case, Mark has the insight required.) He gave the green light (which has nothing to do with the green circle of the mobile that hangs above).
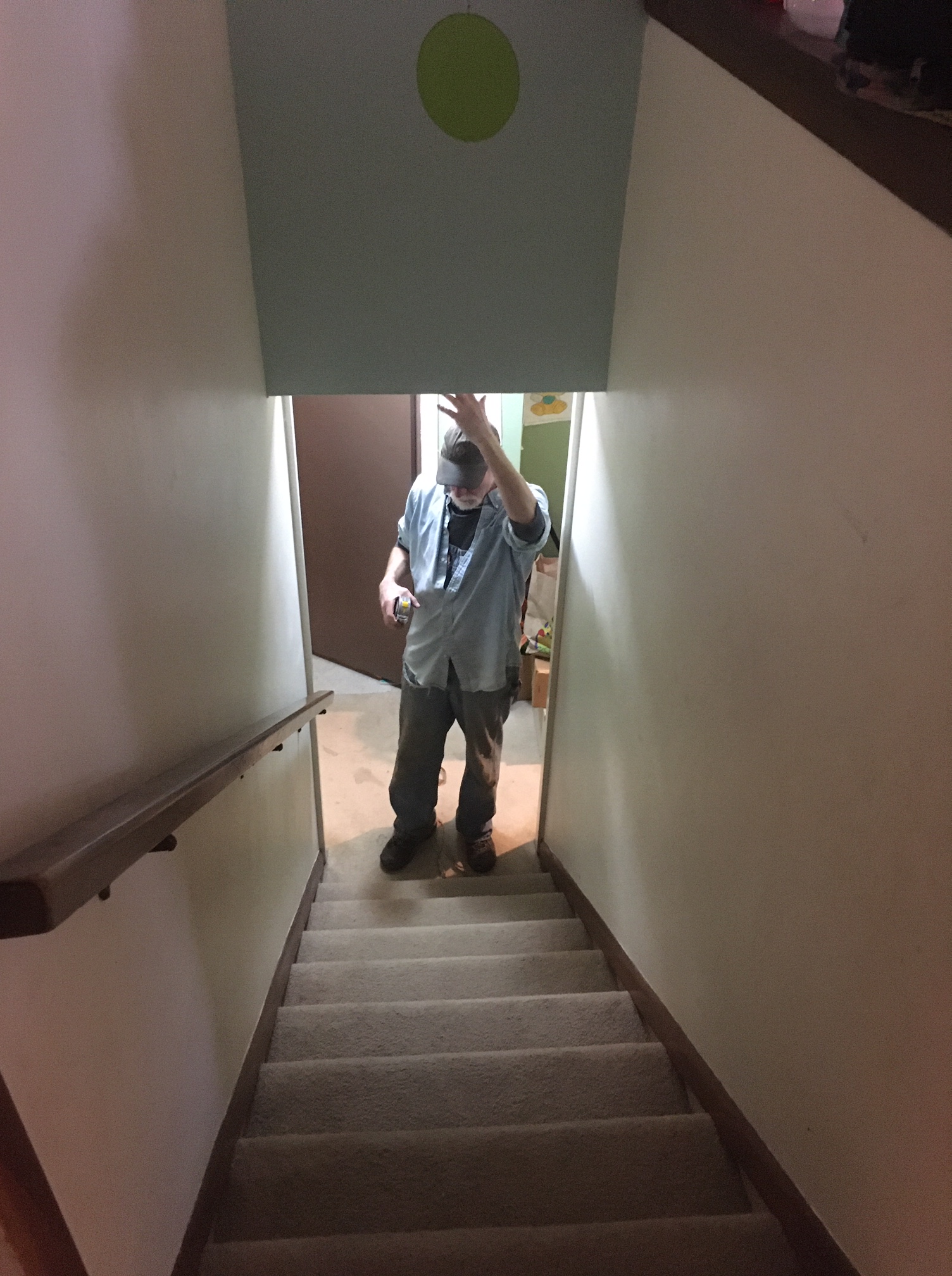
I’m waiting for the lumber delivery as I write this post. Next up: Building the cabinets.
I’m pretty sure the guy in the red shirt is carrying the tool rest from my lathe.
The timing of your blogs is exquisite. We have been talking with our general contractor on totally gutting out the eighty year old second floor “master” bathroom (which is about half the size of your clients’ kitchen) in our 110 year old house. Drywall covering the actual ceiling, three layers of flooring, plywood cabinets built in situ. I’m sure there won’t be any surprises to be found here. (Know what I mean…hint, hint, wink, wink.) Still designing and hope to begin work in early to mid May. Unless, like you, we cannot. Good luck and I look forward to your future blogs. (And thanks much for introducing me to the Osmo Neutral a couple of years ago.)
Sounds like you’re in for an adventure! Here’s hoping things will go as smoothly as possible.
My last kitchen remodel was an easy demo since Hurricane Harvey did all the work for me with 5 feet of water on the main floor. This also provided for a Master Bath replacement and the Grand Stairway replacement. These folks had been living in the upstairs part of the house using a garden hose at the back door for water a hot plate, toaster oven and a microwave for almost a year until I could get to them. Now they have a beautiful first floor and we have friends for life.
The one I’m on now will be the hardest of my life since it is in my own house and I have to make my wife happy……
What an experience, that hurricane-prompted job! I feel for you on pleasing your spouse. 🙂
There should be some sort of ode written for the benefits of the multitool, which, while not incredibly great at everything is incredibly great at enough to make it indispensable for certain tasks. That, and the lack of care needed on cutting edges once you realise sacrificing a blade will save you hours of messing about with other methods. Hope the job proceeds without too many logistical factors due to the virus.