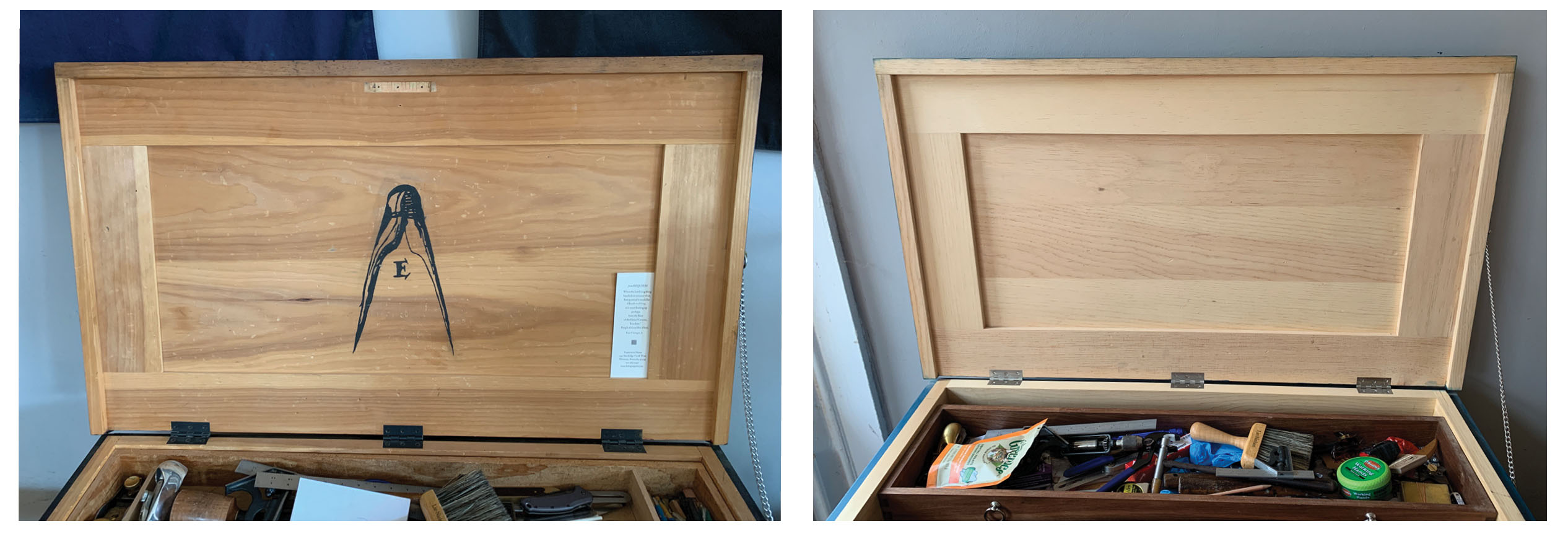
Editor’s note: As promised, Christopher Schwarz and I are writing a series of blog entries that explain how we have improved the construction process for “The Anarchist’s Tool Chest” during the last nine years (and several hundred chests).
Loose-tenon joinery goes back to Greek and Roman times – boats were built using drawbored loose tenons. I start with this fact so as to (hopefully) stave off slings and arrows (which go back further than Roman times).
When Chris built his lid for the first Anarchist’s Tool Chest (the one in the book), and when I built my first one (now in my basement shop at home), we cut through mortise-and-tenon joints for the lid. Now, we employ that loose-tenon joint that goes back to antiquity. Sure, we use a modern approach (the Festool Domino), but the joint is time-tested, and plenty strong enough for these lids (a theory that has been tested time and again by people triple my size sitting on the lid of my chest at the Lost Art Press shop).
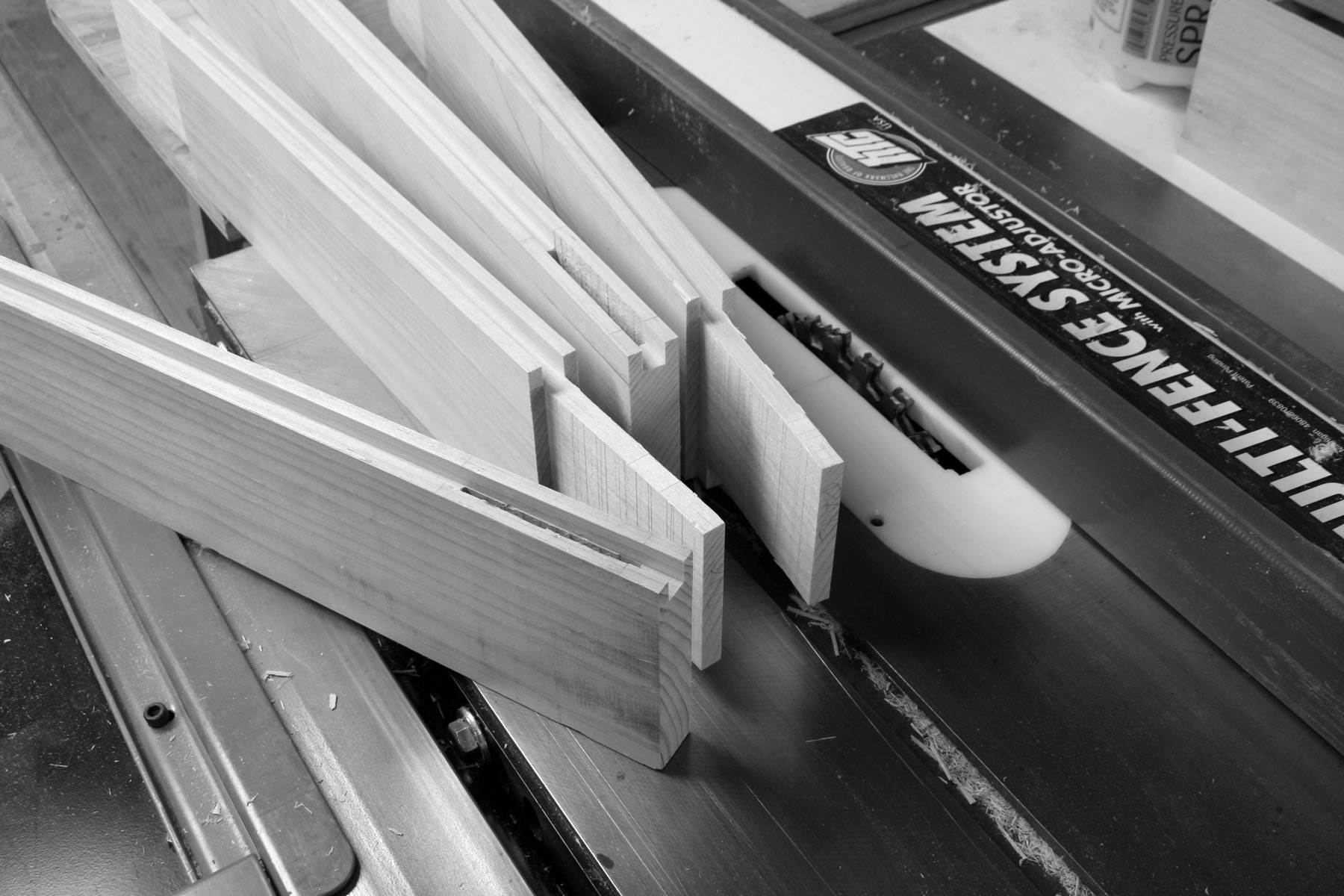
If you’re building one at home and feel the urge, go ahead and cut the mortises and tenons if you like – that joint is the strongest. But also plenty strong enough are two other joints Chris tried out in classroom settings: the bridle joint (slightly easier/faster), then the half-lap joint (easier/faster still). He was on a quest to get the builds down to five days when he tried these out – and they helped to shorten the journey…but not enough.
Now, we pull out the Domino XL, because it’s the only way we’ve found to get the lids glued up before the students leave on Day 5 (and again, the joint is plenty strong). And while at the beginning of the week, we get a grumble or two from time to time when someone asks how we’re doing the lids, by Day 5, everyone is so tired and eager to be done that they embrace the change. And they all leave with the frame-and-panel assemblies done.
But the Domino XL is a $1,500 tool, so use one of the three other approaches if you don’t have or have access to one.
After running the mating grooves on the frame pieces and panel (which in all but the most advanced-student circumstances we do with a dado stack on the table saw), dry-fit the assembly to determine the layout of the two 12mm x 140mm loose tenons. We use the same setup for all students in a given class, so we then set two combination squares to the desired settings: one small (the shorter measurement) and one large (the longer measurement).
While you could perfectly align all the pieces and mark across both at once, we find it’s safer (read: fewer mistakes) if we have folks use the squares – with a reminder to always register the stock off the outside edges – to mark the mortise locations on each piece individually. Anal-retentive? You bet. Does it cut down on errors? Absolutely.
To further reduce the possibility of mistakes, we set up stops to hold the work while using the Domino; they restrain the work against the fairly significant pressure required to plunge the tool into the work, and hold the work flat to the bench. If the mortises aren’t at 90°, it causes problems, so everything we can do to help make them perfect, we do.
With the work restrained, it’s simply a matter of keeping the fence on the Domino flat to the wood, so we encourage – strongly encourage – that you grasp and push down with one hand, using your other hand to plunge by pushing on the back of the tool, but not grasping the handle. (We’ve found that grasping the handle results in folks pushing down and tipping the tool a bit during the cut.)
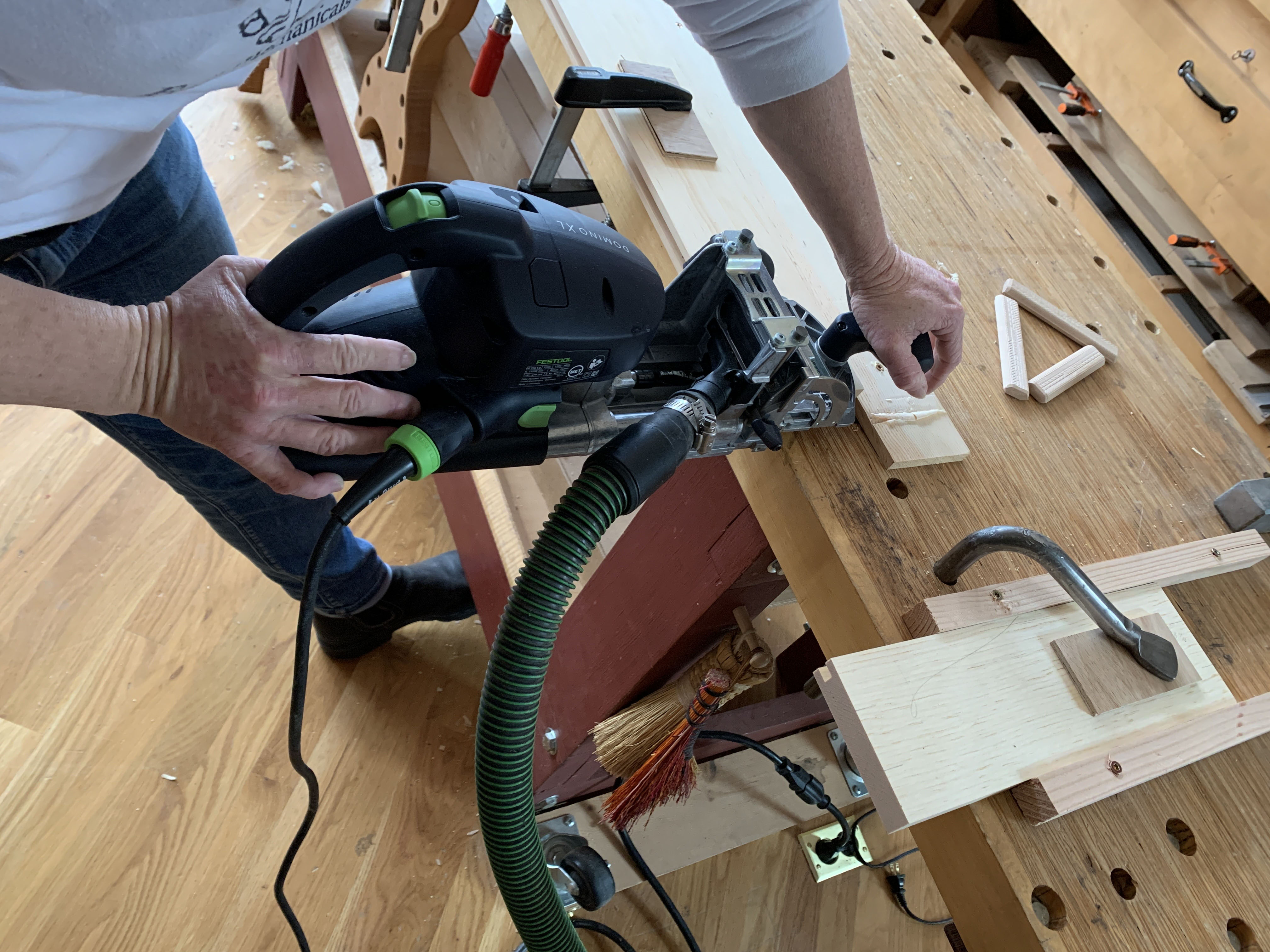
After the mortises are cut, make sure you dump out the sawdust in the bottom of the mortise. Though our dust collection is good, it’s not good enough to clear all the dust from the mortise bottoms.
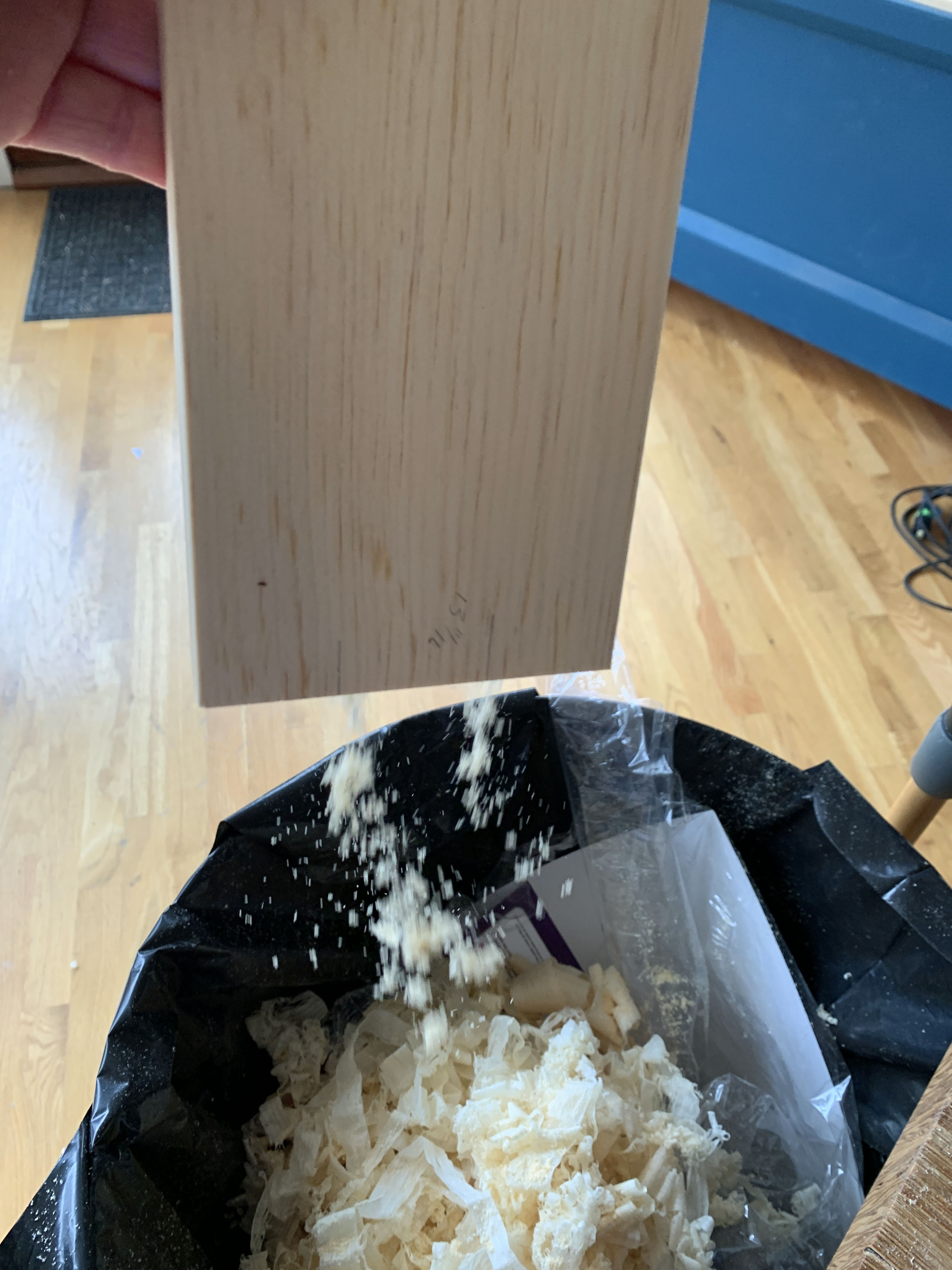
With the mortises all cut, do a dry assembly before opening the glue.
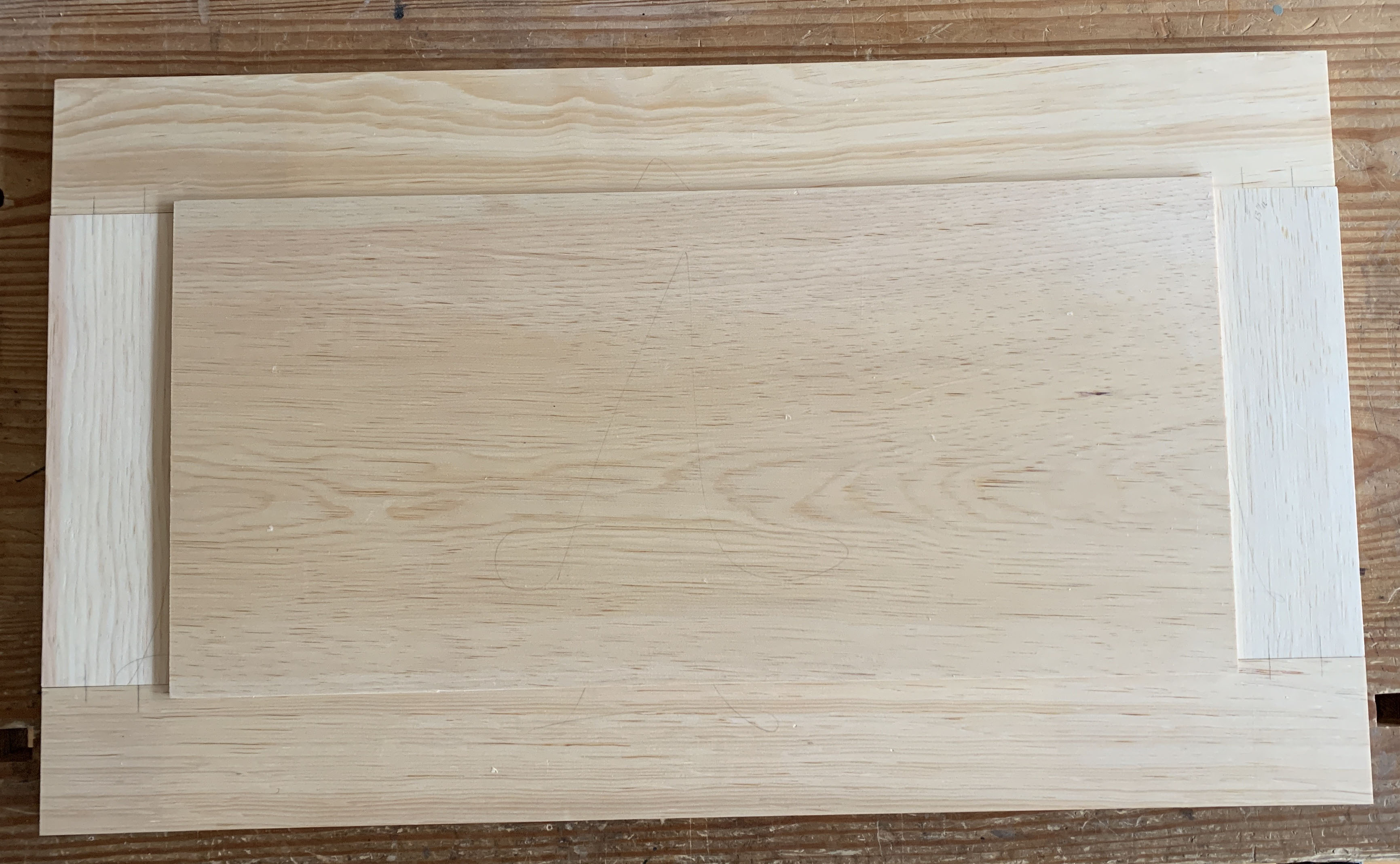
Once everything fits together, cut a 30° bevel on the top edges of the lid (or just soften the edges, per the book) before glue-up.
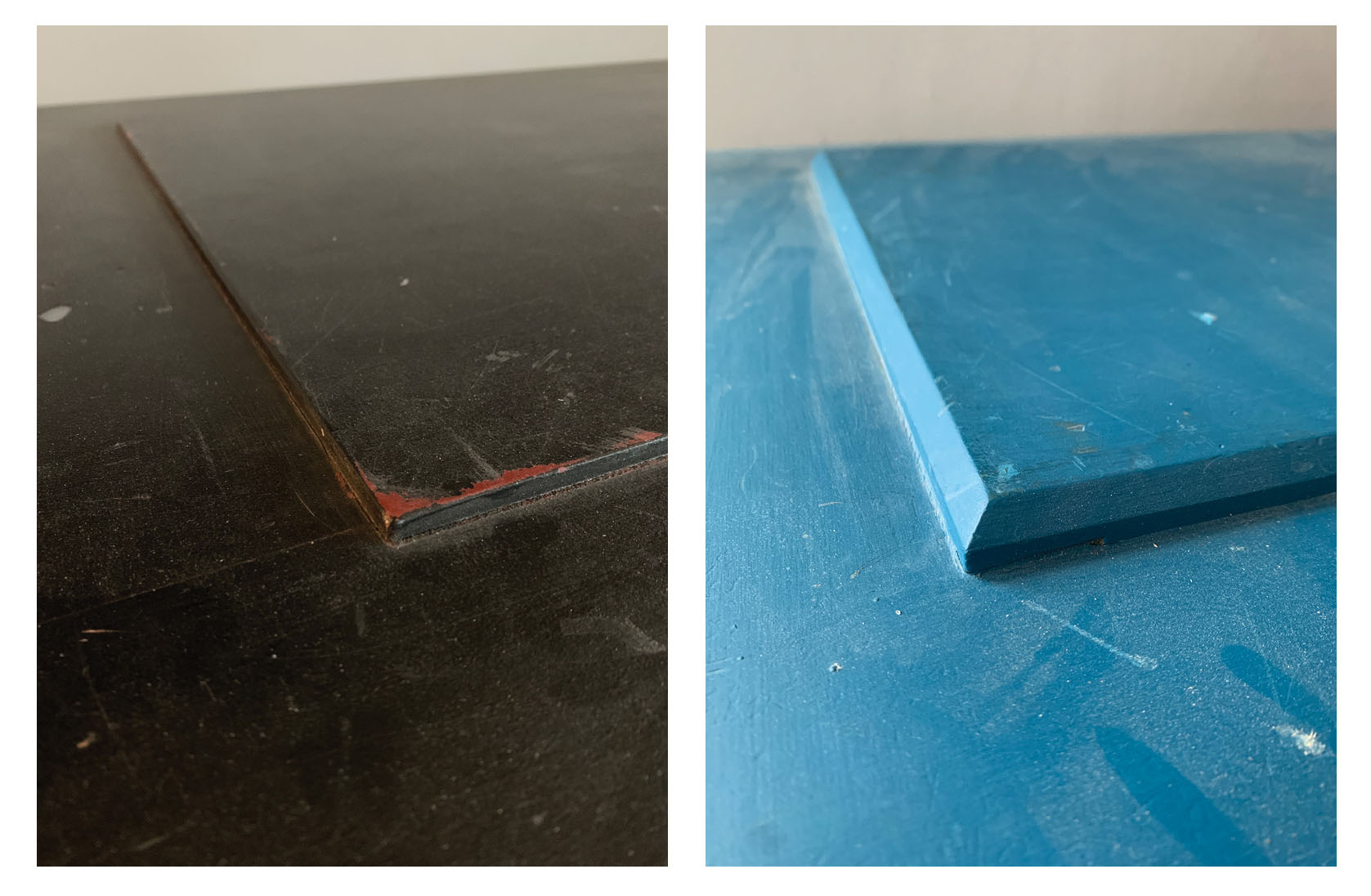
Arrange the rails (the long pieces) with the mortises facing up, and squeeze in a healthy amount of glue, spread it all around and up the mortise sides with an acid brush, then stick the loose tenons in place. Put glue in the stile mortises (move quickly now, as things will get drippy) and slip them onto their mates on one rail. Slide the lid panel in place (remembering that the lid panel lips over the rails…not under), then put the second rail in place and clamp until dry.
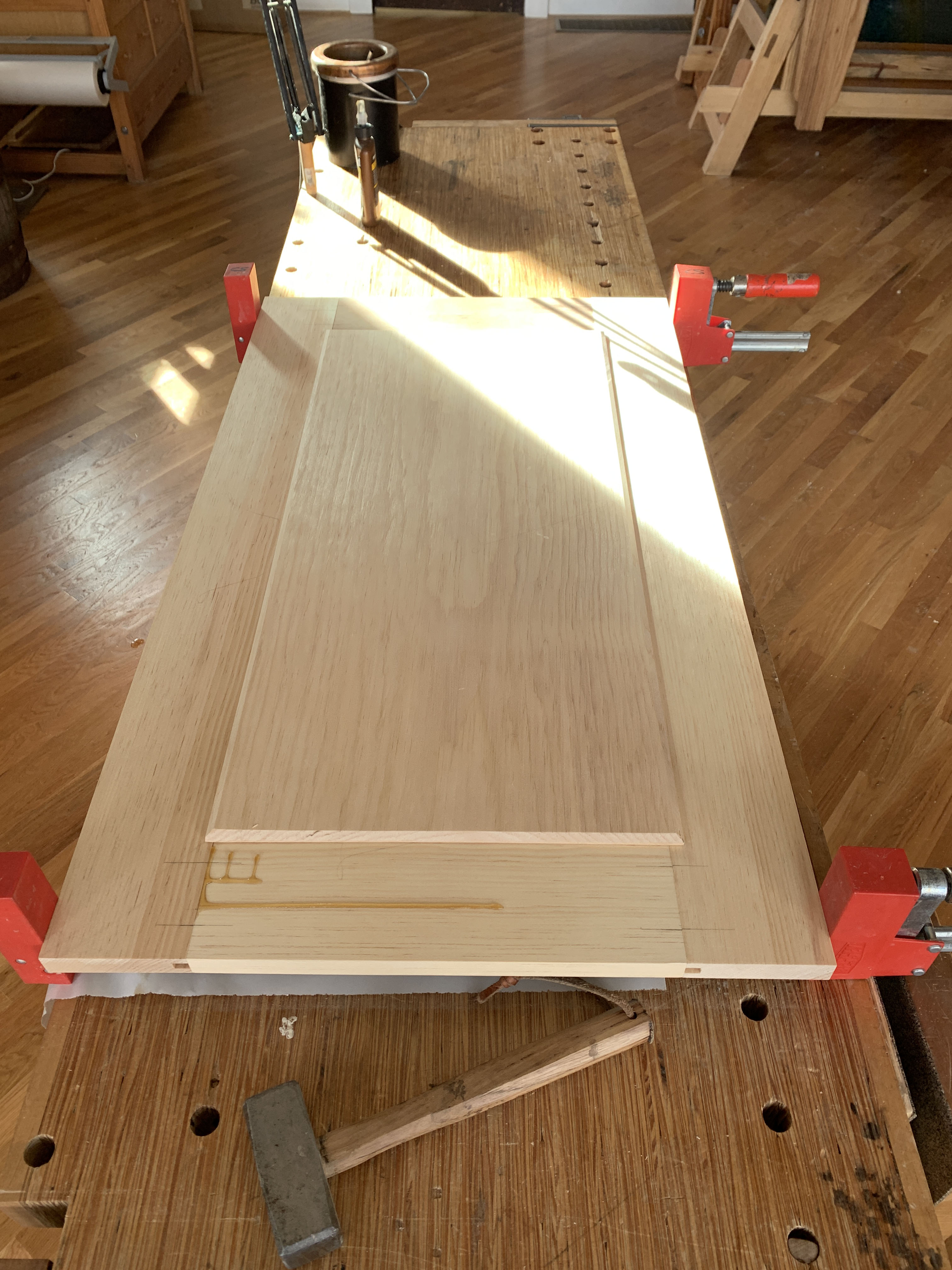
Now, just as it says in the book, cut dovetail joints for the dust seal (one tail on each side piece) and glue the dust seal to the front and sides of the lid. Then add some nails for good measure. The dust seal will see a lot of opening and closing action.
There’s one last difference – and this one is motivated by experience, not by a classroom setting. In “The Anarchist’s Tool Chest,” Chris writes to cut a bevel at the back ends of the dust seal to act as a stop when the lid is open. The bevel can break off with repeated use, so now, we cut these two sticks flush with the back edge of the lid’s frame-and-panel assembly. The wall makes an excellent lid stay.
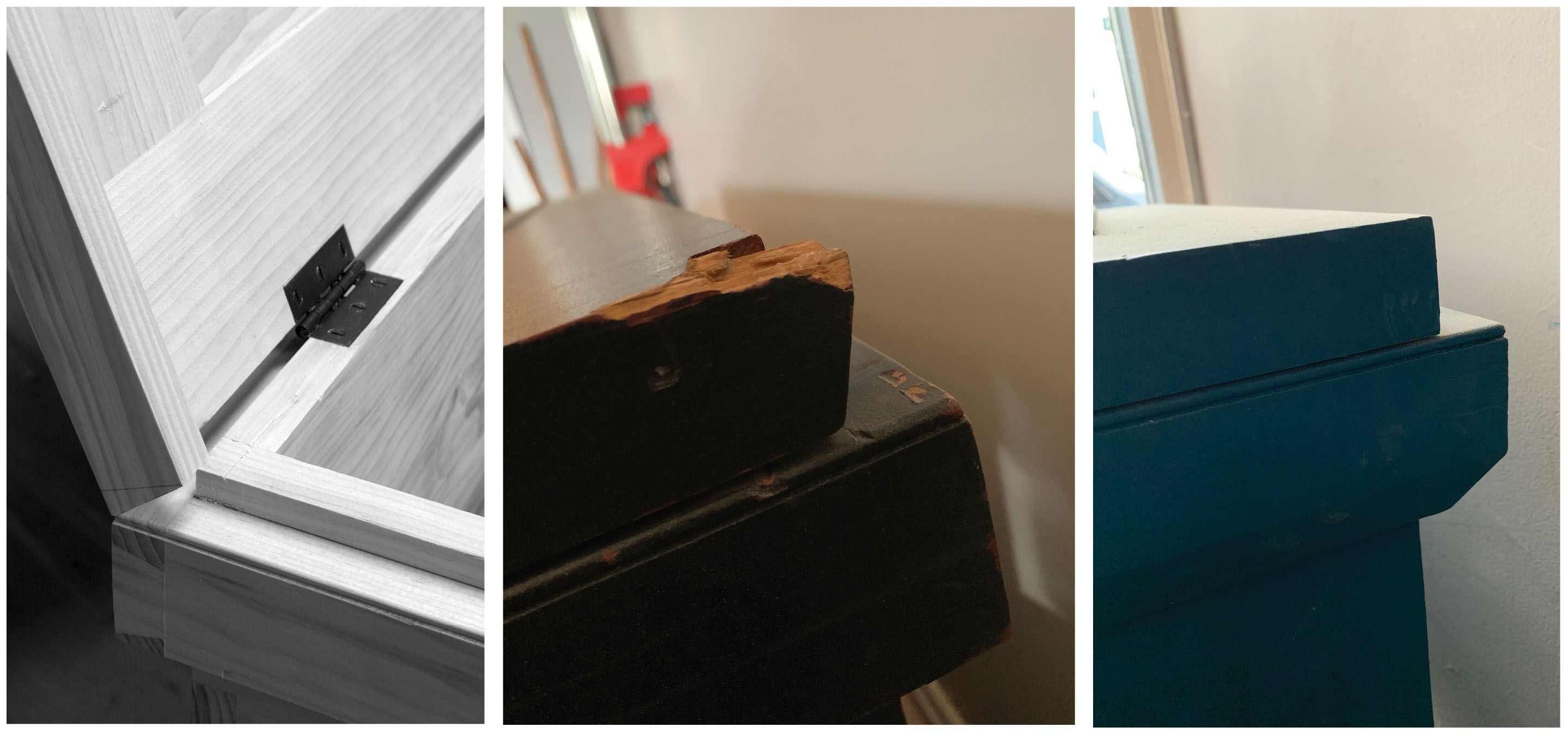
The journey of Chris Schwarz follows the history of woodworking from that which was more Woodwright to that which is more Woodsmith. And in that journey, I think we learn that power tools are not necessarily better in process, just faster in procedure.
Chris, Roy Underhill, and the Woodsmith crew all have mad skills; and have demonstrated that with hand powered tools and tools powered by tortured electrons (well maybe not Roy, or a driver-drill at home?). I have been buying more traditional tools, and will probably move away from most of my low-class power tools as I get older. So, kind of an opposite track, but I’ve never had to worry about production schedules either.
This is eye-opening, and thanks for sharing this journey and the rest of it to come.
What a beautiful blog and life.
When I watched Chris’s video and him endorsing the use of a chisel mortiser, I immediately thought (guilt free) of my DominoXL for this step noting it was pretty much the same thing. Good to know it has now been officially sanctioned. I wonder how the domino dock would work for the narrow pieces – it looks like it may be useful also.
using a $1000 power mortiser to build a traditional chest to house hand tools for joinery seems odd.
Why?
Surely that’s not the only thing it will be used for over the life span of the tool? What is your point, that only hand powered tools are to be used? If so I applaud your commitment to authenticity but will unashamedly power up my limited number of electric tools in rge interests of time and my arthritic joints.
The Domino sees significant use around here (neither I nor Chris has even claimed to be a hand-tool purist). I use it for the tool chest lids in classes, of course, but it’s also how I did all the joinery in the two pieces I recently built for my bathroom. And if/when I get around to renovating my kitchen, the face frames will be Dominoed together. On freestanding, moveable furniture (that’s period or period-inspired), I’m more likely to use a mortise-and-tenon joint…because beyond authenticity, bashing out a mortise or four is a good stress reliever.
Right!
I sure appreciate electric lights in my shop! I’m retired, but still like to do some woodworking in the evening, too.
That ship construction isn’t lapstrake (aka clinker), where edges of planks lap one another and fastened, traditionally with copper rivets, often nowadays with epoxy. What you’re talking about is a kind of carvel planking, where plank edges butt up against one another.
You are correct. Fixed.
Not wishing to invest in a 1500 dollar tool that will get limited use and not looking forward to chopping deep mortises, I think the half lap is the way to go, for me anyway. Bob
The lid has always been the most daunting step to building the Anarchist’s Tool Chest from the book. A 4″ through mortise? Yikes!
Thanks for these updates. All three have been wonderful.
Can i ask, what size dominos are those?
12mm x 140mm (that’s kind of buried in the post).
Oops. Thanks.
I have the baby domino, and use it very little. I wish I had waited for the XL. I end up using the Powermatic hollow chisel instead of the loose tenons.
I was at the museum and saw loose tennons secured with wooden nails on Egyptian sarcophagi.
In the spirit of offering time/work saving alternatives only. You could probably reduce the time requirements and not have to transfer your 401k to Festool if you used something like Beadlock. Still not hand tool but it’s more than $1000 cheaper. I am not in anyway associated with Beadlock. I used one once several years ago.
I have used that tool quite a bit back in my days of Popular Woodworking. I found it fussy
I went from mortise and haunched tenon to a table sawed bridle joint. Much faster and just as strong. I now prefer a two mortise floating tenon approach and have built lots of very strong doors easily. If you are going to purchase a $1500 machine to implement this method, have you considered a horizontal mortiser (boring) machine? Same price range as the domino and much faster. It’s just not portable.
OMG, you put screws in the workbench top! 😮
Oh wait, it’s a tool, not an alter.
—
I guarantee if the ancient Egyptians had a Domino and electricity, the Sphinx would be sitting on a dust collector with one paw on the Domino. Chuckling at my own visual; been inside too long methinks. 🙂
Chris using a Domino what’s next?
Fire and brimstone coming down from the skies! Rivers and seas boiling!
Forty years of darkness! Earthquakes, volcanoes…
The dead rising from the grave!
Human sacrifice, dogs and cats living together… mass hysteria!
As a way to practice some of the joinery in the ATC I built a small saw till box. I thought about using my domino 500 (the smaller machine) for the lid joinery instead of through mortises, but was concerned that the smaller loose tenons wouldn’t be strong enough to use on the larger ATC. I decided pegged bridle joints would be faster and easier to make using my table saw and tenon jig than chopping the mortises. I cut the tenons for the stiles on the table saw with a dado stack, and the bridles into the rails with the tenon jig. After the bridle joints were assembled and glued I drilled two 3/8″ holes diagonally through the face of each of the four bridle joints and glued in cherry dowels. I like the look of the contrasting cherry pegs in the surface of the lid frame and I think the pegged bridle joints will be at least as strong as the through mortises, if not more so.
Could dowels be used for this joint?
They’d be too weak; a dowel or two won’t offer enough glue surface or support – unless you used a bunch – maybe 6 – at each location…at which point it wouldn’t be any faster.
I forgot to ask- did you use the loose or tight setting on the domino for the mortises?
I use the tight when I’m building stuff, but we use the looser setting (just in case a little wiggle room is needed) in classes.
I appreciate and thank you for these updates. I’m currently building my own ATC chest and have vowed to traverse the entire project with hand tools only. Electricity is limited to my radio, fluorescent lights, and plug-in heater (I’m in Canada). I reached a critical moment of self-doubt and irony yesterday evening when, winded while rip-sawing an eight foot board in my cramped shop, I banged my elbow against the table saw. Stupid table saw.
Great job getting some exercise! Keep it up.
Ironically, this is the book that inspired me to sell my domino to buy a bandsaw. Most ardent hand tool folks tend to have a couple gray boxes with green latches getting heavy use. It seems the mentality is hey, if I’m gonna keep my lie nielsens in their scabbard and use power tools, they better be nice power tools.
Sorry folks, the Shakers would have used electric tools had they been available at the time.
Would they have used CNC? I don’t ask this facetiously. I’m currently learning Solidworks (a CAD program) and experimenting with using CNC to make traditional furniture projects. If we can justify using a table saw, band saw, or a Domino, why would we object to CNC to shortcut our process? I’m interested in finding the line between modern convenience and traditional hand tools. My gut feeling is that they are not mutually exclusive and that there is much still to learn.
My understanding is that Shaker women invented the circular saw although that is in some dispute. Nevertheless, they would use whatever technology they had available, even 3D printers.
Shakers were using power tools from at least the 1830s. They were often on the cutting edge of powered tool use.
The difference being, in part, the answer to: Production or Hobby?
For the Shakers (production), you are likely correct. For a hobbyist, the answer could reasonably be different.
For want of discretionary funds, I don’t have a domino yet. I almost secured a really good recurring commission gig which would have essentially necessitated the domino purchase just to get the quantities out that I needed in the timely manner. Meaning when time is of the essence (as is your case in the classroom setting), it’s just the logical choice. It’s not sacrificing anything other than time, which is the point you were after. So it makes total sense. And anyone who thinks differently is trying to sell you something, in my opinion. When time is of the essence, be efficient while not sacrificing quality. Plain and simple. Not everyone has a domino nor access to one, as you mentioned.
When I’m in my normal mode of hobbyist woodworker, I particularly enjoy the hand skills and meditative process of hand cut joinery. But when I’m in production mode, I’m no monk. Meaning I don’t have time to meditate. In so far as the class setting is concerned, good on you for figuring out ways to get the project completed. There’s plenty of hand work you have accomplished for the students to fee they have gottentheir money’s worth. At that point, it’s malpractice not to let them see the finished product before they leave (innards aside).
And also, while we are on the topic of throwing stones, we’ve all seen the posts as evidence of what should already be common knowledge of what goes into teaching a class…mainly loads of prep work by the instructor to get the materials ready before the class. I think we all know that the jointer, planer and tablesaw have already been fired up to that end. So what’s the big deal? I just don’t understand people (not necessarily here, but elsewhere online) getting bent out of shape about the use of a purpose-built, quality tool that produces a quality joint in a fraction of the time. If time is your luxury, do it how you want in a way that brings you the most enjoyment. If you’re racing against the clock, do it the way you can get it done well in the time allotted. That’s my 2 cents.
Jeez – next thing you know, Bob Dylan will go electric…
When using the Domino approach, do you fill in the groove gap (normally filled by the haunch on the tenon) with a spline or just leave it since the dust seal will cover it?
Just leave it and let the dust seal cover it.
Thanks!