We use a lot of finishes in our workshop, from soap to shellac, but the one we recommend for beginning finishers is one we mix up ourselves.
It’s what Bob Flexner would label an oil/varnish blend. We just call it our shop finish.
During the last 20 years, I have developed some preferences as to the raw materials I use, but feel free to ignore those. Almost any brand of raw material will work. Here we go:
1 part Minwax Helmsman spar urethane, satin sheen
1 part boiled linseed oil
1 part odorless mineral spirits
Mix up the three liquids in a mason jar and you are ready to go. Apply it in thin coats with a clean cotton rag. Wipe it on and continue to wipe until the coat is as thin as possible. There should not be a visible puddling or pooling of liquid anywhere. You are wiping it almost dry.
Let the finish dry (it usually takes a couple hours). Use an extra-fine sanding sponge (usually #330 grit or so) to remove any finishing nibs. Apply another coat and repeat the process until you achieve the look you want. Two coats is the minimum for me and is what I use for workbenches and shop appliances. Furniture usually gets three or four. I have used as many as 10 for a customer who wanted a more plastic look.
Why This Finish?
The varnish offers a bit of protection against spills and stains. It’s not a thick film such as lacquer or a built-up shellac finish. But it does offer enough protection for a chair, bookcase or cabinet. Tabletops, which live a hard life, usually need more protection.
The boiled linseed oil offers a little color and will continue to add color as the piece is exposed to oxygen and sunlight. I like this yellowing. It’s what old furniture looks like.
The mineral spirits thins the varnish and oil, making it easy to spread the shop finish out to a thin and even coat with great ease.
Why These Raw Materials?
I prefer the Minwax Helmsman spar varnish (satin sheen) for a couple reasons. It’s easy to get at most home centers and neighborhood hardware stores. Its major competitor (here in the U.S.) is Varathane Spar Urethane. The Varathane works fine, but it smells a little stronger and takes longer to dry (usually an extra hour or more in my experience). It also gives a milky appearance to the mixture, though that doesn’t seem to change the look of the finished object.
I don’t have a preference for which boiled linseed oil I use.
As to the mineral spirits, I always strive to use odorless mineral spirits. It costs more but has fewer volatile organic compounds (VOCs) and almost no smell.
The Results
Aside from the protection that this finish offers, I like the low-sheen, hardly there aspect of the finish. It looks like wood does when it has been freshly planed. To your fingers, it doesn’t feel like the wood is wrapped in plastic. And it’s difficult to mess up when applying it. I’m sure it’s possible to mess it up, but I haven’t seen it happen yet.
— Christopher Schwarz
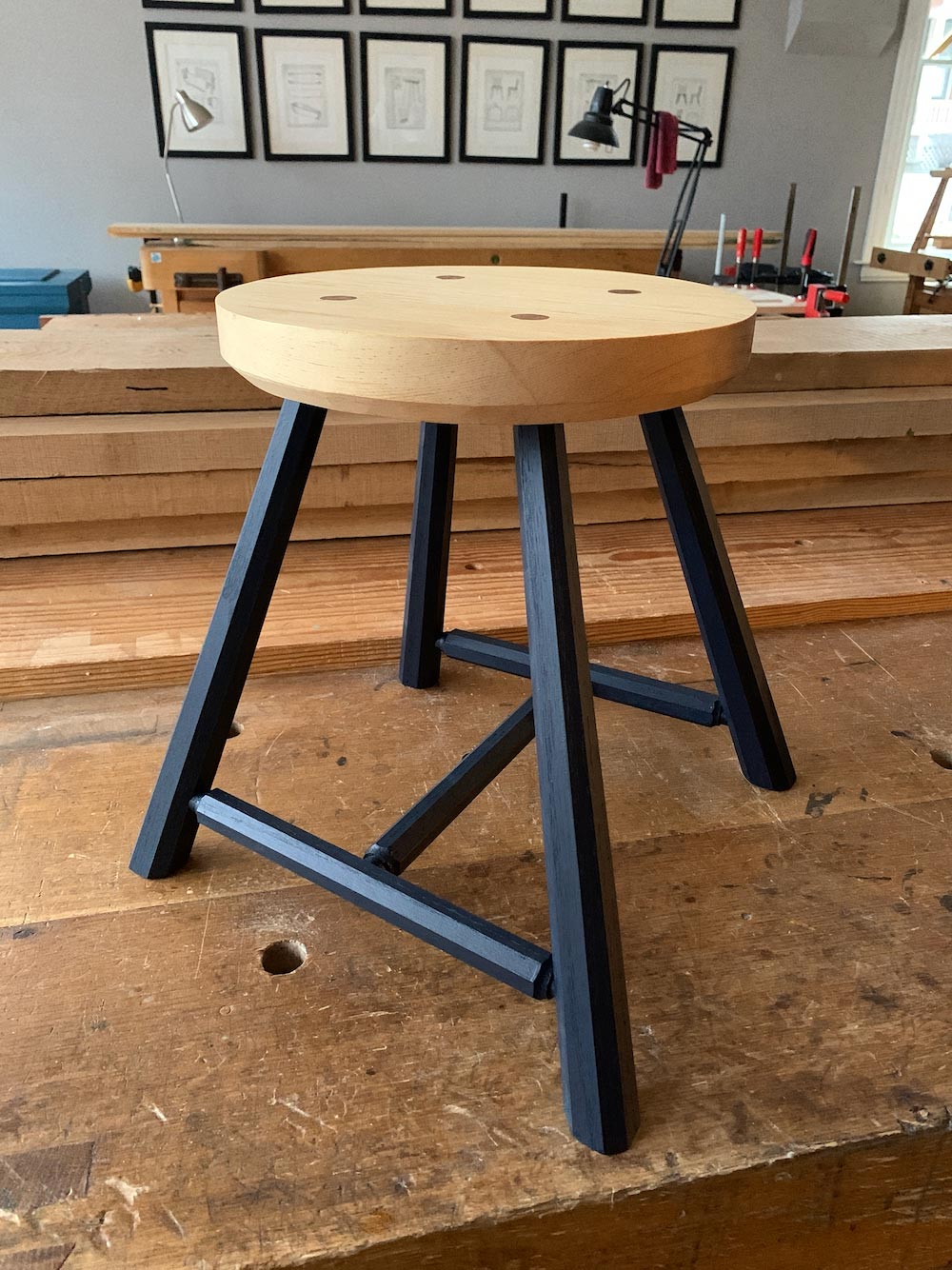
Helpful post. Any advice on how this compares to using Danish oil (for a Nicholson workbench I’ll be finishing soon)?
Danish oil can be anything. It can be a wiping varnish, an oil/varnish blend or something else. It’s not a distinct finish, it’s a marketing term.
So the answer is: I have no blinking idea.
Nonsense. Next you’ll tell me Betty Crocker wasn’t a real person.
I’ll give the shop finish a try, thanks.
What kind of rags do you use? The ones I get at Lowe’s or Home Depot always leave little specs when I use a wipe-on finish.
I always use the bag of rags that’s made from old t-shirts. Before I use, I snap them like a towel in a locker room, that seems to get all the loose threads off
My experience is that anything new is susceptible to dye bleed off. I echo John’s comment about using old cotton. T-shirts, bed sheets, whatever. There aren’t enough naked bums around here for me to snap test all of my rags, but I do give them a final hot water wash with only some bleach. They go straight from the dryer (no dryer softener sheets!) into recycled store plastic bags that I store in the shop.
In a pinch, I have used yellow or white dollar store microfiber towels, too.
I just use a commercial white paper wiping rags. Cheaper and you don’t have to spend time looking for quantities of the right type of rags. I also use lots of nitrite gloves and when I go to take them off I always wrap my wipers inside of them and 1 glove over the other and if Leary about it will pull other old gloves over top. This makes nice compact item. Doesn’t permit oxygen to get at the wipers and eliminates spontaneous combustion.
My favorite is old t-shirts. I wear simple white cotton undershirts daily so I have a fairly regular supply of ones with holes.
Another plus, it’s easy to refresh this finish in the future with another coat. One down side in my experience is the tendency for the finish to turn gray when exposed to water. Fortunately, a little dap of this finish brings it right back. It’s nice over milk paint also. Bob Glenn
Thanks, I was wondering how it would do over milk paint.
This is all I have used for the last 40 years. Always works, always looks great.
Precisely why LAP is so great. I’ve seen this mixture spelled out on many forum threads over the years — never with this precision, never with photos, never with explanation, and certainly never with this authority (“it just works, see?”).
Love this place. Thank you so much.
Love this type of finish! I’ve used Minwax Wipe-On Poly instead of spar varnish, keeping the same 1:1:1 ratio. I’ll definitely have to try this with spar urethane – I imagine it offers a bit more protection than the wipe-on polyurethane. Thanks for posting this!
Wow!
Thank you so much !
Damn: you and Mortise&Tenon are really on another level.
Merci pour tout.
Cordialement
Hugo
I have always thought that urethane was a chemical cure and you shouldn’t thin it down. Cause I have done that in the past and it wouldn’t dry.
I’ve never heard that. Sorry I don’t know how to respond
You can thin urethane almost indefinitely. Perhaps you used a water based product. Or perhaps you used an oil/varnish blend but left too much product on. Boiled linseed oil takes FOREVER to dry if you don’t remove the excess.
Maybe you are thinking of epoxy? The 2-part epoxy/resins are chemical cure and you want to follow manufacturers instructions on those.
I have been rehabbing the windows and frames in my 110+ year old house since the early 1980s. (Wait-hold on a second. That’s almost 4 decades!! That can’t possibly be right.) For these (as well as other earlier projects) the Minwax spar urethane has been my finish of choice. Right out of the can for the most part, but periodically thinned out; sometimes 1:1, other times more so. I have never had a problem with it not curing hard. Perhaps you were using outdated products. You know; the one that’s been sitting around on the shelf for about 15 years. Knowing your experience, I’m sure that it couldn’t have been human error. That’s the kind of thing that I would do. 🙂
Sounds like the “Maloof recipe” i used recently. Only for that i used minwax wipe on poly. I’ll give this shop finish a try since I already have 2 of the ingredients and am usually at Lowes and/or HD every day anyways. Now I just need a better labeling/organizing system for all my mason jars…
I was sitting here admiring that stool. Thinking to myself how the wood top looked good with the black painted legs. Then I read the caption! It still looks black with “glare” to me even though I read the color.
Very helpful. If you have a need to renew this in a few years…light sand and recoat?
Yup
Do you apply the finish over other coatings? Like paint or stain, or do you just use it on the bare wood part of a piece?
Sure. You can apply almost anything over almost anything else. Try it on a sample board.
Can you apply other things on top of this shop finish?
Butt wax. Might be too ‘EWWWW’ for some though.
I’m afraid to ask what kind of pad you use with butt wax . . .
…and we are Back to the T-shirt. 🙂
Beeswax Under Turpentine & Tung oil
This has been my go to finish as well for about 20 years with a couple of variations. I use pure tung oil mostly but have used linseed. I use minwax gloss spar varnish because my understanding is that gloss varnish is harder. Ths other ingredients and the application process negate the gloss in my experience.
I often warm the oil for the first two coats.
It thins it and that seems to help it suck into the wood more efficiently. I apply generously let it sit for 20 minutes then rub very thoroughly. I typically wet sand a puddle of oil on the third coat. The slurry created packs into the grain. Wipe off thoroughly.
Lots of possibilities. A really easy finish.
Brian Greene – Ottawa
What a great looking stool! That’s coming from a guy who was in Endoscopy lab all day yesterday.
Yep! Great stuff! It simply works!
One warning: be careful of the oily rags – spontaneous combustion has claimed more than a few lives with unexpected fires. Spread ’em out til bone dry. Better yet, keep immersed in water until you can burn them. Yes, cutting the linseed oil with varnish reduces the risk. Yet, I like to ensure zero risk.
Been my go-to finish for over a decade. I enjoy the process and appreciate how visitors feel compelled to touch my work. Easy to apply and to freshen up when desired. I cut the BLO in half as I found equal amounts were too tacky for my tastes when applying and slow to cure in my cool (not cold) environment. After first coat, I lightly wet sand before wiping/buffing. I give eight hours between coats. Process takes time compared to faster drying methods/materials.
I typically use general finishes arm-r-seal as my shop finish. Seems to be the same concept as you describe here, so what benefit would this offer over that? I’m kind of a one trick pony finisher. Find what works and stick with it, but am curious what the difference (if any) would be.
As for that particular stool, did you prefinish the base and top then assemble? I know me and it seems to me like I’d get paint everywhere I didn’t want it to be. Haha
I used this type of oil/varnish blend on a much-abused surface in the kitchen – it does offer more protection than oil only, but only to a limited extent.
You could also define this finish as a technique to put on very fine coats of varnish/poly – fine enough to prevent a “plastic” look. A decent compromise if you will – having *really* good protection against physical abuse is almost impossible to obtain without a thick layer of plastic-looking material.
Am I right that you can leave the mason jar alone for a couple months, shake it up well, and then reapply? Or does the mixture degrade over time such that you have to make a new batch job by job?
It lasts a long time in the jar. A little of the varnish will cure thanks to the oxygen in the jar and sink to the bottom. But the remainder is usable.
Can one use turpentine instead of odorless mineral spirits? Up here in the Great White North, “odorless mineral spirits” is very hard to come by. The only places that seem to have it is art supply stores where they sell it in fancy packaging for $27 CAD/litre.
Yes. Any standard paint thinner will work as well.
Would you use this finish for a kitchen table that will be ground zero for breakfast, dinner, homework and whatnot? I don’t like the plastic film feel of poly but it is durable and I don’t want to be refinishing every 3 months. Looking for a good alternative
As I mentioned in the blog entry, no. It’s not ideal for tabletops.
What IS ideal? I’m a father of five who once made one of those “farm tables” and coated it in polyu. Pretty sure the kids ingested a fair amount from testing their teeth-grip-strength out over the years. Damage done – is polyurethane really the standard goto on tabletop finish?
No. It depends on what you are after. I like to use finishes that aren’t terribly durable but are easily reparable: lacquer, shellac, oil, soap. With wax on top at times.
Poly is not easy to repair (in my experience).
Appreciate the response.
Looks tasty, like maple syrup.
I’ll have to mix some up to try.
Hoping you mean to try on a project, not as a maple syrup substitute. 🙂
Thank You Chris.
I’ve been experimenting with this in three ways:
1) Alternating the resin type of the varnish component (e.g. urethane, alkyd, phenolic).
2) Subbing ‘citrus solvent’ for mineral spirits.
3) Adding a small quantity (.25 – .5 parts) of pine tar for better mildew/fungus resistance – plus I am strangely addicted to the smell.
The citrus solvent has the feel-good-eco-groovy thing going on, but makes my eyes water. I personally find the harder resins (alkyd, phenolic) give a quicker build.
I encourage others to try out these things. Totally unnecessary if your goal is just to find something that works and get to it, but an interesting learning experience.
– Joshua
This looks great but is there a generic or alternative name for spar urethane? I’m trying to find something availble in the UK without massive import fees.
David
Its got to be over there somewhere. The boatbuilders use it for wood parts that otherwise aren’t painted…hence the reference to the “spar”. So if you get no other leads, check in at a wooden boat shop and ask there locally.
David,
I know Paul Sellers uses products made by “Ronseal” over on that side of the pond. Check for a varnish or poly made by them and should be very similar.
Sounds like a good recipe. Just thought I’d add that we have always used boiled linseed as a finish on our mountain dulcimers. We have to spread the rags out as suggested above until they are dry or can be burned. If you leave them crumpled up they may burst into flame. Also don’t leave them where critters can get at them, for some reason they seem to think it is some kind of food.
It is some kind of food, just not food grade usually for us humans? Linseed and flax oil seem to be interchangeable terms to a degree but from the small bit I understand the different manufacturing/processing techniques used suit different uses. If timed right you may get cooked critter. Bit like natural fast food. Right, I’ll stop now.
Re BLO; the blo of today is not the same as the blo of yesterday. The smell and the colour of certain it has changed over the years. I have been around it all my life and that will be 7 years in another week. I questioned it about a dozen years ago with a rep from Record Chem who seems to be the main manuf of it in Canada and of course no comment, we’ll just give you a fresh gallon. In the past it was made from prime NA flax and it had that nice orange colour to it. It now comes from a much lower grade flax and is grown mostly in countries with “Stan” on the end of them and seem to have a green tinge in it. I have always used it and still do. It still enhances the colour of the wood over time. My biggest concern is drying out esp when used with varnishes. Nothing stays the same.
Is there a trick to keeping the mason jar covers from being glued to the jar? More often than not, the finish dries, and I can never get the lid off.
Put a piece of waxed paper on the jar mouth, then put the lid on. You may have to replace the waxed paper each time, but it won’t stick.
Smack my head. Thanks.
I like to call this the “Schwarz Negroni.”
I’ve used this mixture for two years now. What I like about it is that it dries quickly and that makes dust not a problem.
I generally don’t have much sandpaper sitting around, wood shavings should work well on this one to remove the nibs, correct?
Yup
I could eat that with biscuits.
where would you use a soft wax opposed to this varnish?
Hi Alden,
This is a bit like asking when to eat chicken vs. fish. The finishes have similar properties. Both are easily applied, low-protection finishes. Both are easily repaired. Both are fairly matte in appearance. The shop finish offers a little more protection with the varnish and adds a little more yellowing over time.
When I use this on my milk painted windsor chairs, I mix the first coat with more mineral spirits. I think this carries the oil and varnish deeper into the paint and wood below. I usually apply three coats and increase the varnish with each coat a bit to give it more protection. Nothing magic about thirds. Bob Glenn
I’ll put this concoction in my list of finishes. Maybe I’ll try it in the future. I do try to stick with odorless finishes when possible.
Nice looking short stool
I have a small (very small) difference of opinion. In the pro training I got on finishing, I was told to never use a satin finish until possibly for a top coat. The reason for this is that satin finishes contain light defusers mixed in which will cloud the look of the wood, slightly (very slightly.) I usually finish the process, whether a poly mix or an oil varnish mix (depending on the moisture exposure and protection needed) is knocking down the gloss with steel wool and then a coat of paste wax. Just my two cents.
Anyone know what “USA mineral spirits” is named over here in Australia/New Zealand? From memory, what Aussies/Kiwis call “mineral spirits is a totally different chemical liquid.
Probably depends on where exactly you are and the companies that sell it there, but have also seen “white spirits, Naptha , or Stoddard Solvent. Here are some other names:
https://en.m.wikipedia.org/wiki/White_spirit
Made a jar of this stuff yesterday. I’ve christened it the ‘shop slop’. Very much looking forward to experimenting with it. I’m soon finished, and have been for over a year, making a proper bed for myself. Fairly trad. beech bedstead, but much higher than usual so that you don’t ‘get up’ from bed, but rather sort of pivot yourself upright — mattress is about arse-hight. The beech will be a perfect testing ground for the slop.
Thanks for a very interesting blog, Mr. Schwarz. I’ll be ordering a small lathe soon, thanks to your influence, and I’ve got my eye on a majestic leftover slab of 3″ white oak we’ve had in storage for years that nobody knows what to do with. Well, I do : It will become the mother of all shaving horses ! So … this old dog is nearing 50 and still learning new tricks 🙂 When I get too old to do the heavy work I’ll have a corner in the shop where I’ll make chairs. Beautiful, intricate comfortable chairs. Looking forward to it already.
I like the looks of this. Would this be ok to use on hand tools? Specifically a couple old levels that I’m looking to restore, cherry and mahogany. Thanks again for all the knowledge you give us.
We use it on old hand tools quite a bit. Another good option for vintage tools is paste wax applied with a 3M grey pad.