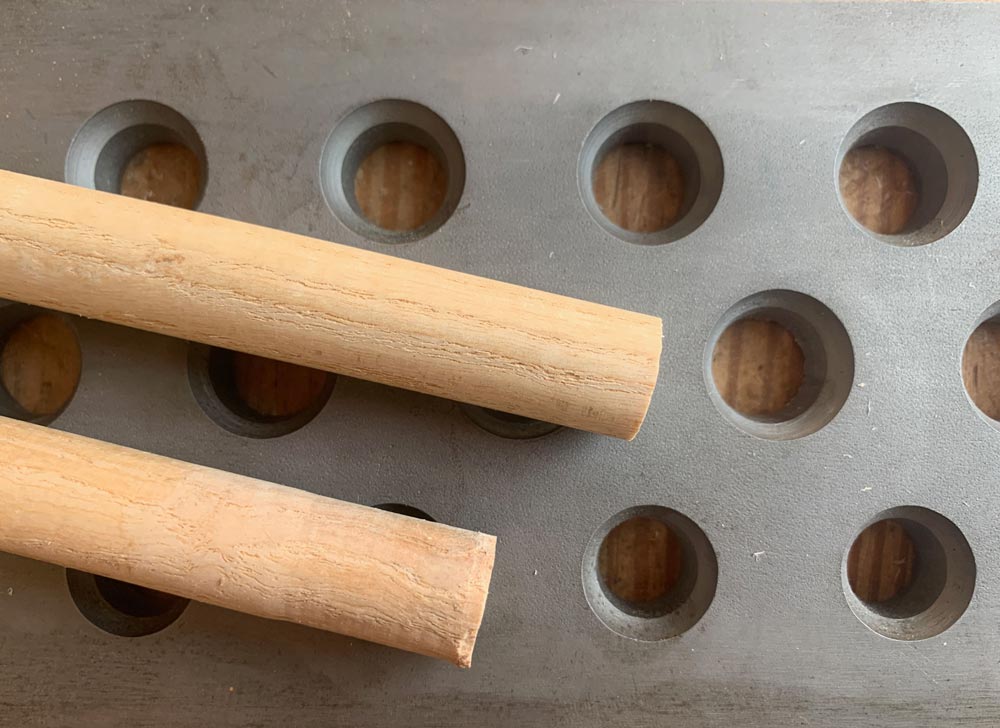
Like chairmakers John Brown and Jennie Alexander, I feel the same pull. Not toward death, necessarily, though that does begin to weigh on my mind during every long project.
Instead, I feel the pull toward making my chair components lighter and lighter. As I look back at my chairs during the last 19 years (going back to my Arts & Crafts frame chairs), it’s obvious. My seats have been getting slimmer, as have my sticks and legs.
It’s been a slight change here and there. But I feel like I’m trying to make the chair disappear as much as possible.
The other side of this coin is that I know I need to cut or rive my material so the grain is perfectly straight for legs and sticks. And the joinery has to be as close to perfect as I can manage.
One example of how I achieve this: During the last year I have changed how I fit my sticks. I don’t teach it this way – it’s just too nuts. (I have a different way to get the fit I want with students.) But here it is for you to mock. Or perhaps take something away from it.
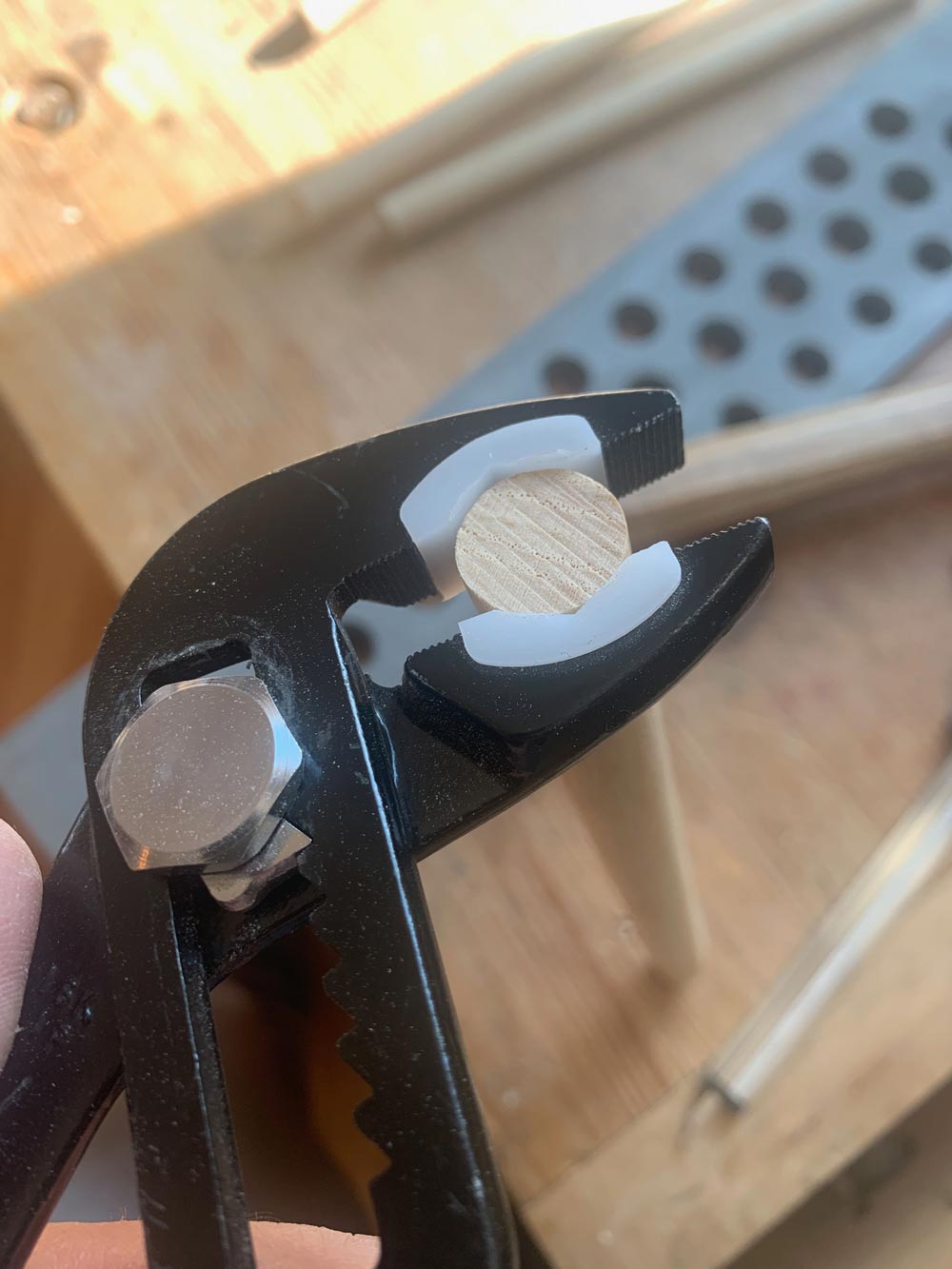
Compressing Tenons in Stages
My goal is to get the tenon compressed so it goes easily into the mortise with light hammer taps and little risk of everything snapping or splitting. But then I use the heat and moisture in my glue to lock the joint up.
Here are the numbers and the process. The sticks I make end up at .635” in diameter after they are scraped. And I want them to go into a mortise that is .600” in diameter (I grind my spade bits to a custom size).
The first step is to take my non-scratch pliers and compress the tenon evenly and as much as possible. This will usually take an ash or oak tenon down to .625”.
Then, and this is the crazy part, I drive the tenon into a wire-drawing plate. The plate shown is a crazy heavy plate used in the jewelry industry. It allows me to size tenons to 1/10 of a millimeter. That’s way more holes than anyone needs. If I had to do it again, I’d get a machinist to make me a steel plate with a couple holes with a chamfered rim.
This is not a dowel plate. I drive the tenon in on the chamfered side of the hole so it doesn’t “skim” the tenon. It simply compresses it.
With my wire-drawing plate I get my tenons down to .600”.
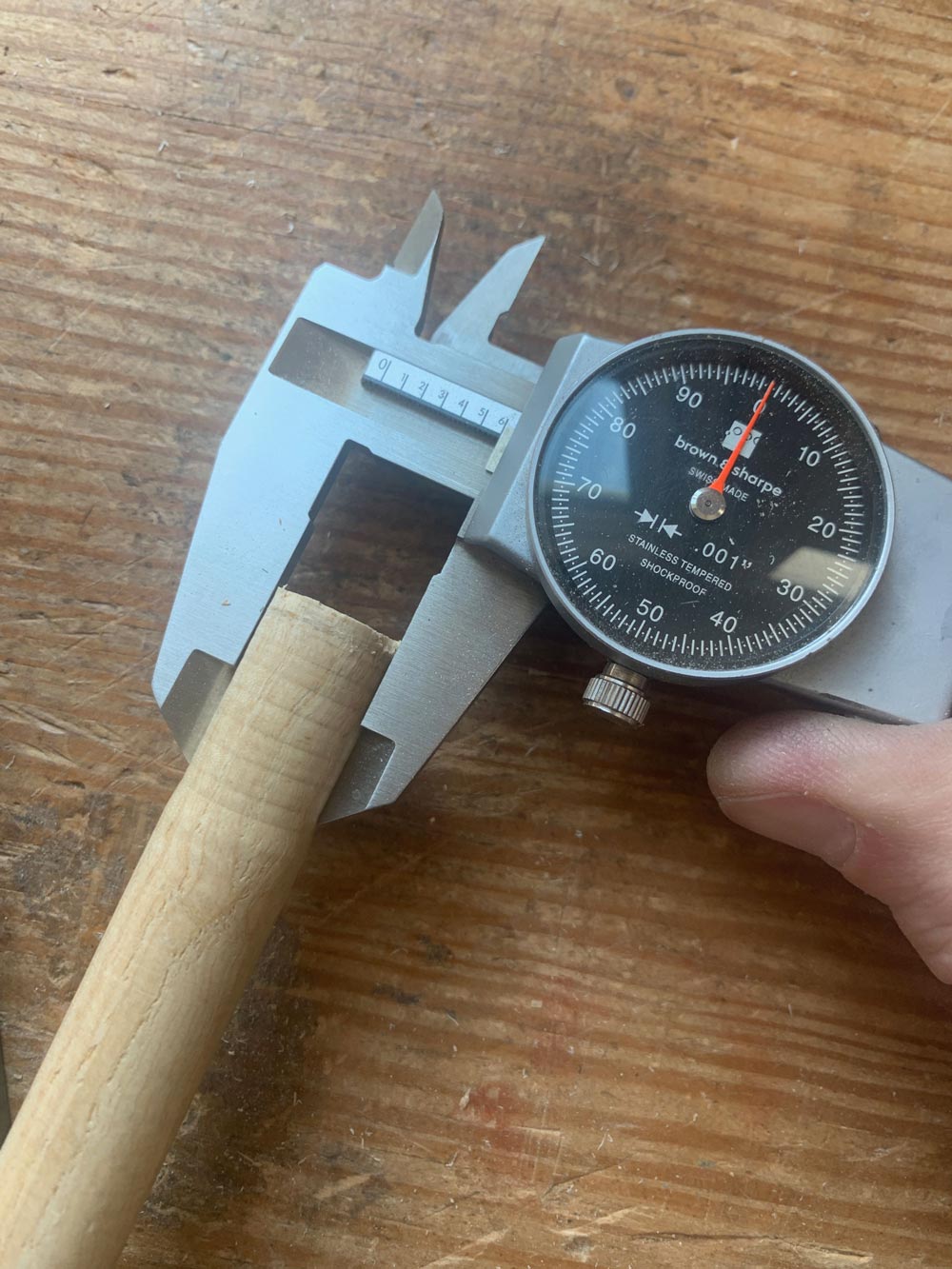
Now it’s time to assemble. I’ve done some experiments by adding hot glue and water to these tenons and they swell up initially to .610”, which locks the joint. Then, after a few hours, they settle down at .615” or so (yes, they continue to expand a bit).
That is a great lock, and I have yet to have a mortise split apart in the last year.
I’m not recommending you go down this route. If I were you, I’d probably get the non-scratch pliers and simply compress the tenons with that tool alone. Then tune the diameter of a spade bit to give you a good lock.
But that’s where I am these days.
— Christopher Schwarz
Is there a benefit here over the wetter seat, dryer leg shrink/expand technique to lock legs?
You don’t always have a wetter seat to work with. In fact, that can be the hardest thing for me (personally) to source.
Also, this is more predictable than the moisture in a board at any given time.
But historically, yes, they used a wet seat to lock things.
Makes sense. Guess it’s variation how Japanese joiners fitted tenons by hammering faces.
I just did a quick look for a large drawing plate and came up dry. I looked at Rio Grande, Amazon, etc. where did you source yours. I really like the approach since sourcing green is tough for me.
https://contenti.com/round-drawplates
If you are using SYP from the home centers, it’s pretty wet when you get it.
When you push anything to the margins it starts to become hard to explain to those not on the journey. I found the pine chairmaking to be the most credible part of the movie “The Patriot”. I delight in the edges of the crafts and seeing how/why they overlap in places. I feeds my brain in ways that studying in the middle area never does – my brain only operates in metaphor?. I will note that you are using machinists calipers again.
Good sounding idea, i’ll be trying it soon.
I use them only to explain myself. I developed the technique without them. Today I put some numbers to my method. But I have nothing against them. They come out when needed.
That makes me feel slightly better about relying on mine.
There’s nothing wrong with taking an idiosyncratic practice and polishing it, and I would even argue that it’s necessary and correct to do.
Chris, will the lighter prices maintain strength over time? I’m wanting to tackle my first Windsor and let’s just say I’m a really “BIG” fan of chairs! OK I’m obese..
Any thoughts/suggestions?
Tom
Hi Tom,
I work for customers on the entire range of the BMI. A chair such as this is built for someone who is (at most) 220 to 230 lbs. To ensure the weight limit on the chair, I use a seat size (15″ x 20″) that would make it difficult for a larger person to use the chair.
For bigger customers, I increase the size of the seat (16-1/2″ x 24″). I taper the legs only slightly. I add an undercarriage. And I reduce the rake and splay of the front legs. I don’t make any changes to the structure above the seat.
Hope this helps.
Thanks Chris!
I need to make one to your specs and use it for a few months before trying to sell it.
Cheers,
Tom.
I’ve used the technique you describe for a long time when I used to build wooden ship models. My declining eye sight brought me to making furniture which I enjoy even more than the models. I used a jewelers plate to make the wooden treenails (trunnels) to keep the various parts of the ship model like hull planking and deck work together. Worked great. I see you’ve had the same success.
Cheers
A 3D printed custom jaw for the pliers would be a good way to get the precise size without the draw plate.
Math nerds will note that if you take the limit of your dimensions, you will end up with a chair with a non-existent seat and sticks.
I keep trying for this but my guests complain.
Oh, my advanced calculus days. And number theory days where I learned 0.999999…. = 1
Signed, fellow math nerd.
I keep trying for this but my guests complain.
True, but they leave sooner. 😎
Interesting technique. Did you try a PEX Crimping Tool used by plumbers? I think the hole for the 1/2 inch pipe used with a copper crimp ring cut in two so you could put it over the tenon, would give you something very close to your numbers. Those crimps are very powerful and apply an even pressure on the whole surface of the cylinder shape they’re compressing.
Never seen one. I’ll take a look. Thanks!
I was curious so I tried my crimps on a maple dowel and it works great. At Home Depot: https://www.homedepot.com/p/SharkBite-1-2-in-and-3-4-in-Dual-PEX-Copper-Crimp-Ring-Tool-23251/202270489
The higher end pipe fitting compression tools are designed to apply force on the entire diameter at the same time. They’re designed for gas fittings where there must be a complete seal. It’s the first thing that popped into my mind when I thought of other tools.
You should glue size the tennons first; dip them in a heated solution of thinned down hide glue, let dry, then crimp. The dried glue will be deep in the pores of the tennon. It will be reactivated durring assembly when it contacts the fresh glue in the mortise. Luthiers always glue size their parts before assembly. It makes for a strong bond and helps controls excess glue leakage.
I already size all my joints. You are correct.
I could never get a spade bit to work well, at all. I really, really hate them. I have happy moments when I put them on a grinder and try them on a dartboard.
I adore spade bits. To be clear, I’m not using them in a brace. I am using them in a battery drill run at high speeds. I run up the bit to full speed before plunging. Works great.
All things equal, I strongly prefer using an auger or spade bit in a brace. But I discovered making my first continuous arm that boring mortises for spindles was either going to be 1) grinding my own spade bit, 2) trying out spoon bits, 3) using a spade bit in my power drill.
#3 cost me about $3 from any local hardware store, it worked great, and I had a dry fit uppercarriage within a couple hours (including time to and from the hardware store).
All to say, anyone that’s like me and prefers a brace, give this a try anyhow, you’ll probably be glad you did!
My dad has never been a woodworker, per se. But his entire adult life his job has been to fix things, primarily major machines for automotive R&D. He’d be the first to say, he’s not an engineer, but he is a troubleshooter. He knows how to dig up the information on just about any mechanical situation, diagnose what went wrong and how to fix it, and then give the team instructions on what they need to do.
I don’t know what specifically from, and I doubt he would remember either, but when I was showing him a chair I was in progress on sizing spindle tenons, you could tell his head was off thinking. And a few minutes later in the discussion, he went back to spindle tenons, and made essentially this same suggestion (channel locks with a piece of heavy fabric/thin leather/something of that nature).
Funny how different backgrounds can lead people to get their hands dirty and come across the same concepts and ideas.
I’ve yet to try this because by that time that chair was already a couple spindles away from dry fit and glue up. But next time, I’ll give it a go.
I’ve always thought a sure sign of genius is to take a solution from one technology and apply it to a completely different technology.
Just stumbled over a Japanese gentleman making little sanding blocks on YouTube –
https://www.youtube.com/watch?v=KFFl1HBlEs8
At 4:38 he uses the same technique on the ends of dowels, but uses a neat rolling technique.
Just thought you may be interested.