My normal schtick on fixing up an old jack plane goes something like this:
Me (showing a jack plane to someone across the room): “Hey, does this sole look flat to you?”
Student: “Uh, I guess so?”
Me: “Then it’s ready to go to work.”
The above is a bit of hyperbole, but it is mostly true. Jack planes require the least amount of tuning to work really well. The reason? They take a coarse shaving, so the sole doesn’t have to be particularly flat for them to perform their duties. If you are in a hurry, you can usually grind and hone the iron and just go to work.
But I love my jack plane, and so I like to do a little work so that the controls move smoothly and the parts fit together nicely. If you think this is an admirable goal, read on.
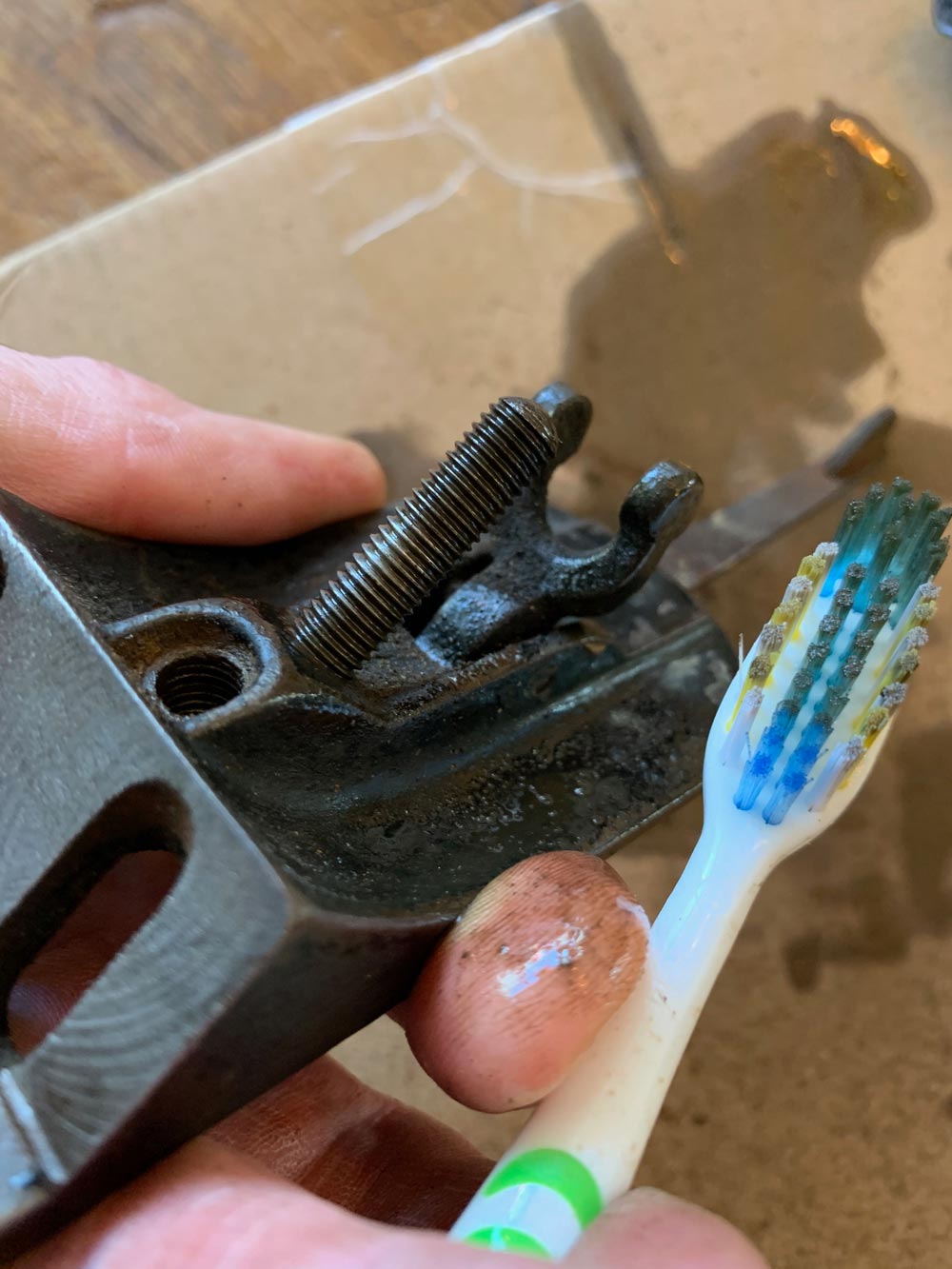
Disassembly & Cleaning
Most jack planes have had a hard life and have had shavings and dust rammed into every possible orifice. A simple cleaning works wonders.
Take apart the entire plane. If something can be unscrewed, unscrew it. Remove the frog, the knob and tote. Unwind the blade-adjustment nut all the way (it likely will come off). Remove the screws that affix and adjust the frog.
Now fetch some cleaning tools. I use an old toothbrush, a coarse brass-bristle brush and some sort of liquid – Simple Green, mineral spirits, machine oil, WD-40 or anything else that is metal-friendly. Scrub the parts first with a toothbrush and solvent. Then use the brass-bristle brush (soaked with liquid) to clean the threads of every screw down to bare, shiny, lovely metal.
If the tapped holes in the plane are filled with gunk, clean those out with a bristled brush and some liquid. Bare metal is the goal.
Lubricate the screw threads with a light coat of machine oil.

Check the Frog
The frog of your jack plane is its heart. The bedding surface for the iron needs to be flat or perhaps slightly concave from end to end. If it is convex, the cutter might (or might not) chatter.
Before you get your panties in a wad about flattening the frog’s bedding surface, it’s important to understand what’s important about the cutter. Does the cutter need to be perfectly bedded on the entire iron? No. Does the cutter need to be bedded at two points on the frog? Not in my experience (though I used to think this was true). What’s important is that the cutter, chipbreaker and lever cap are all bedded tightly to the frog in the area right behind the mouth of the tool. If the cutter is secured there, you’re probably going to be OK, even if it’s not in full contact on the rest of the frog.
Lucky for us, the way a plane works helps ensure that cutter is firmly held exactly where it needs to be firmly held. The lever cap presses everything down at the right spot. So even if you have a crap-ish plane, you can tighten the grip of the lever cap to get the tool to work. The problem with that super-tighten-this strategy is that when the lever cap is really tight, you cannot adjust the position of the cutter. That is a pain.
My goal is to tune the plane so you can both easily adjust the cutting depth and the cutter won’t chatter. I have found that flattening the frog’s bedding surface helps me achieve my goal.
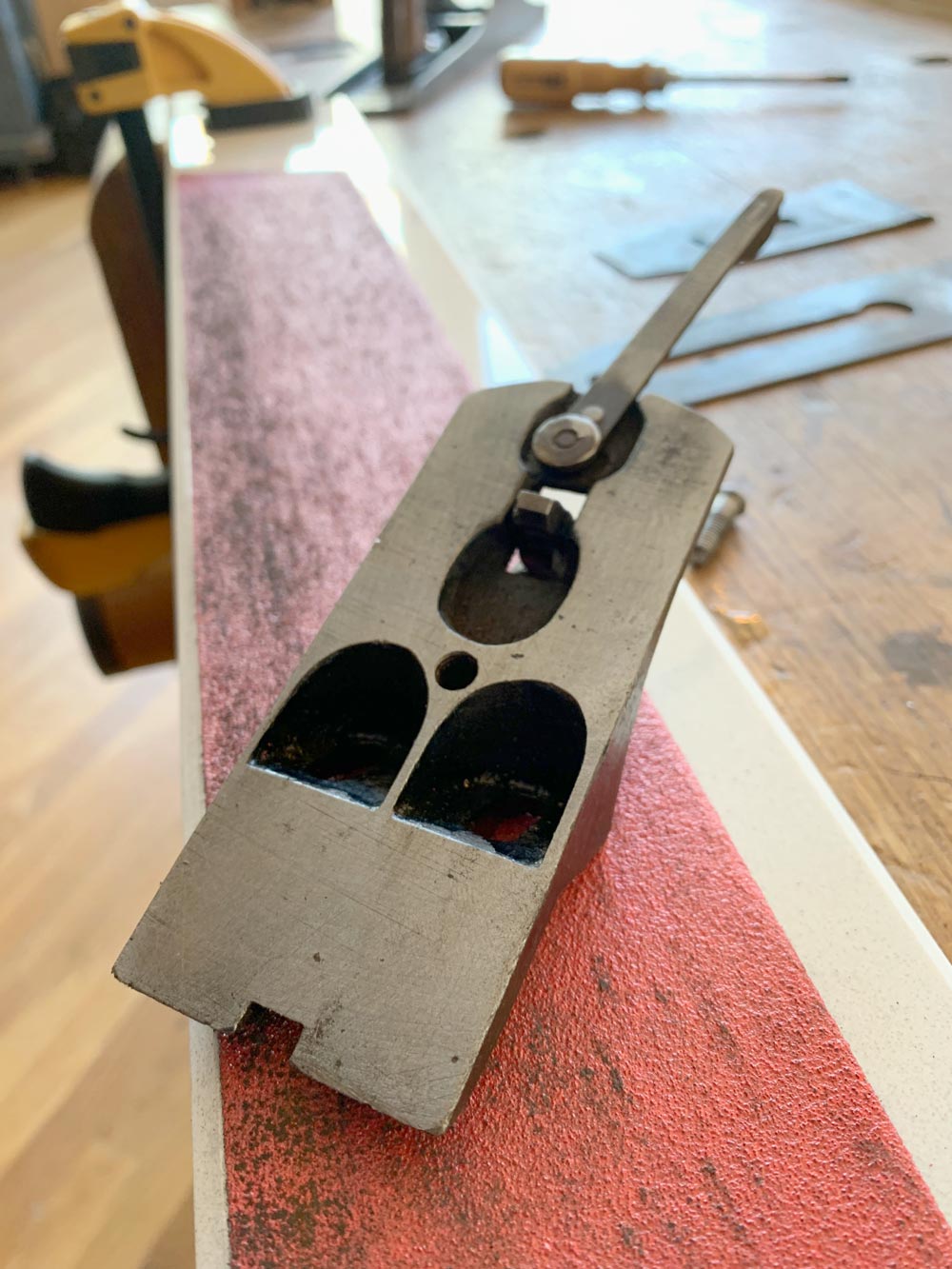
Remove the screw in the middle of the frog (if you haven’t already). Rub the wide, flat surface of the frog on a diamond stone, coarse sharpening stone or some #80 paper stuck to a piece of granite. Flatten it as best you can (the lateral adjustment mechanism will get in the way of doing this easily). This is quick work – cast iron cuts quickly – and the work can only help the tool’s performance.
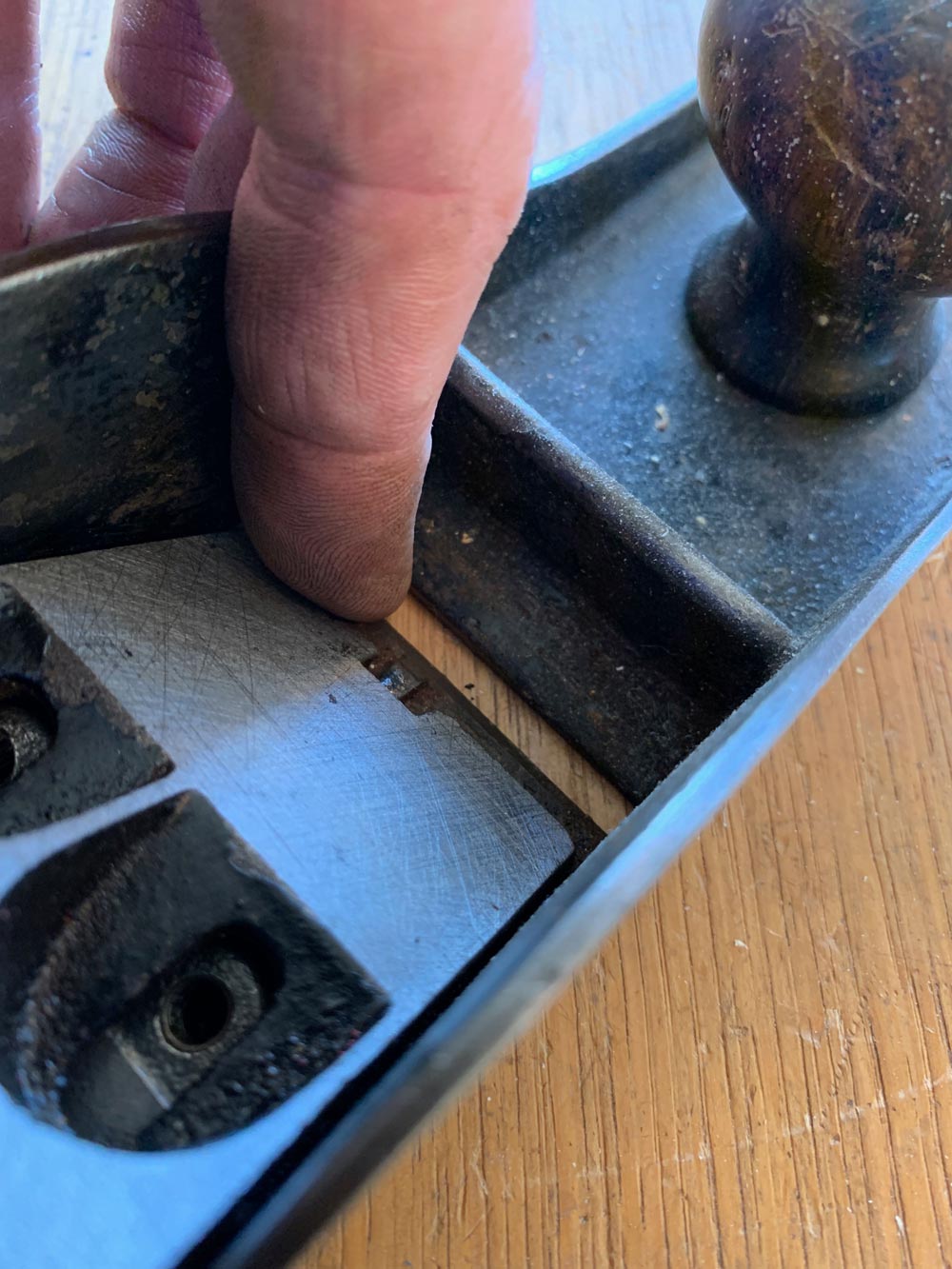
Attach the frog to the plane’s body. Position the frog so the tool’s mouth will be quite open. But don’t position the frog so far back that the plane iron cannot sit flat on the frog. For me, I position the frog so it is in the same plane as the back edge of the plane’s mouth. This position ensures that the iron will have free movement and will sit flat on the frog.
Tighten the frog’s screws tightly. Many people skip this step (by accident). Attach the the plane’s tote and front knob. Assemble the iron and chipbreaker. Secure them with the lever cap. Adjust the adjustment screw in the center of it all so that the cutter will move but is still held tightly.
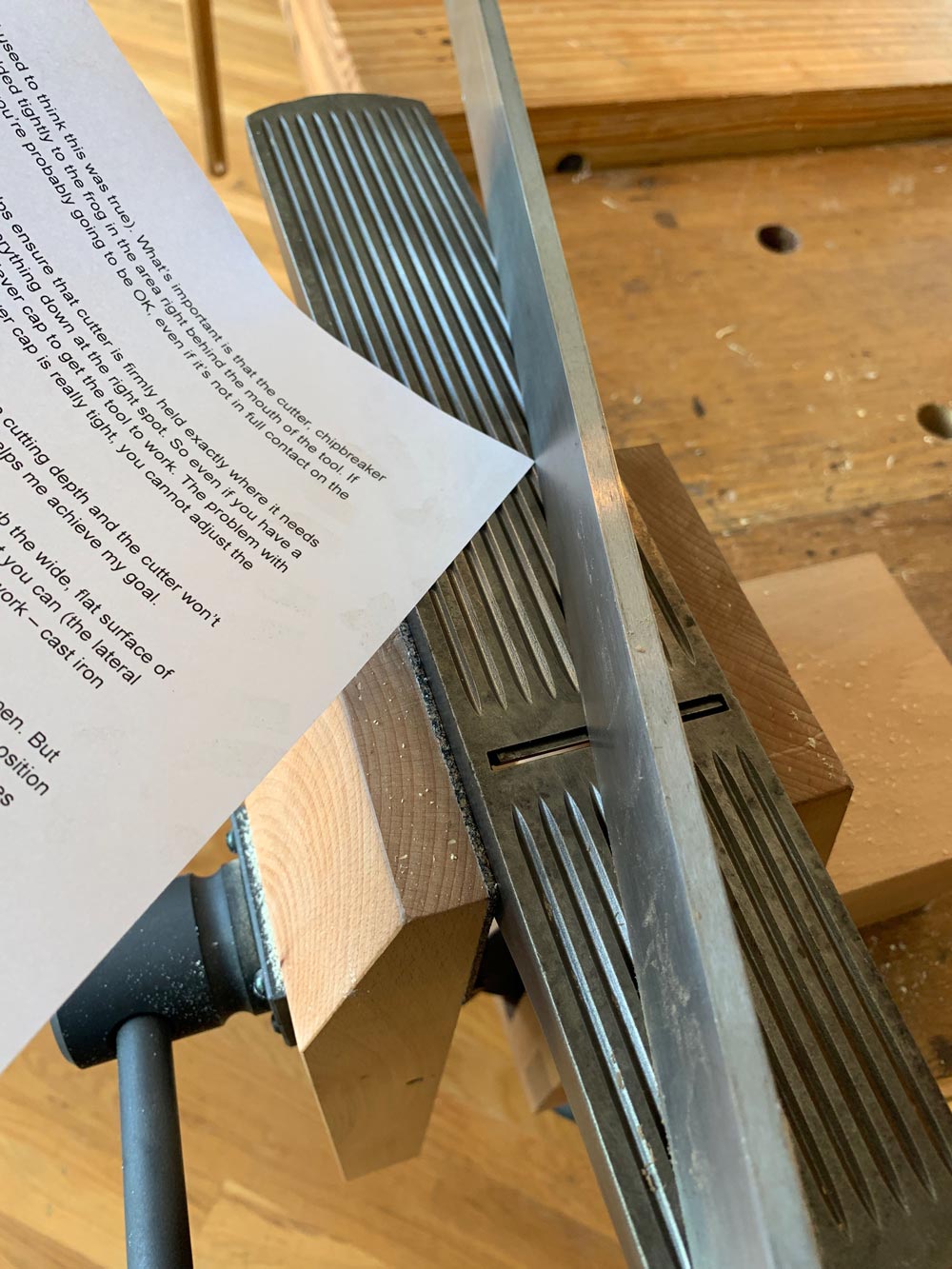
Check the Sole
I hesitate to wade into this thicket. Does the sole have to be NASA flat to work? No. But if I had to choose a plane with a flat-ish sole or an unflat sole, I will choose the flatter sole every time. Bottom line: A little flattening doesn’t hurt. And it might help.
But before you rush out to buy some of the this, that or the other supplies for flattening a sole, give the sole a good gander. Here’s how.
You need a metal straightedge and feeler gauges. Retract the iron so it’s not in the way. Place the plane upside down in a bench vise and squeeze it just enough to hold it in place. Place the straightedge on the sole of the tool and try to fit a .002” gauge under the straightedge at various locations. Move the straightedge around.
After a few pokes with the feeler gauge, you will know what the sole looks like to a .002” feeler gauge.
Switch to a .004” feeler gauge and repeat the test. Then a .006”. Now stop. You now know where the low spots are on the plane’s sole. If you have low spots that a .006” feeler gauge can find (many planes do not) then you might consider flattening the sole a bit.
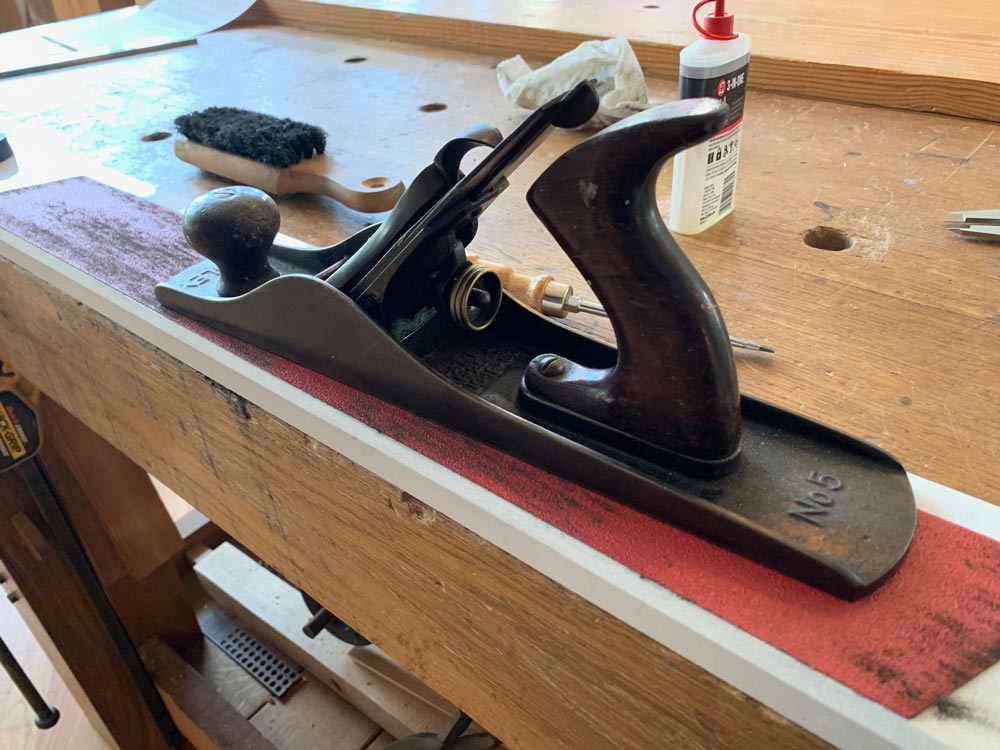
Here’s how I do it. Please note, I am not a machinist or pretend to be.
Go to the home center with a nice straight steel 12” ruler and visit the tile section. Find a cheap pile of 12”-square granite tile (usually $4 or less), or a piece of granite threshold (about $9). Probe the pile and search for one tile that is flat. It won’t take long.
Go to the sandpaper section and buy some belt sander paper intended for stainless steel. Usually #80 grit is good. Go to the adhesive section and get some aerosol adhesive (3M makes some). Pay for it all.
At home, adhere the sandpaper to the tile. Now you can flatten plane soles so they are good enough for woodworking. Rub the sole on the sandpaper. Use circular and linear motions. Check your work with the straightedge and feeler gauges. You should be able to get the sole quite flat in less time than it takes to get a pizza delivered.
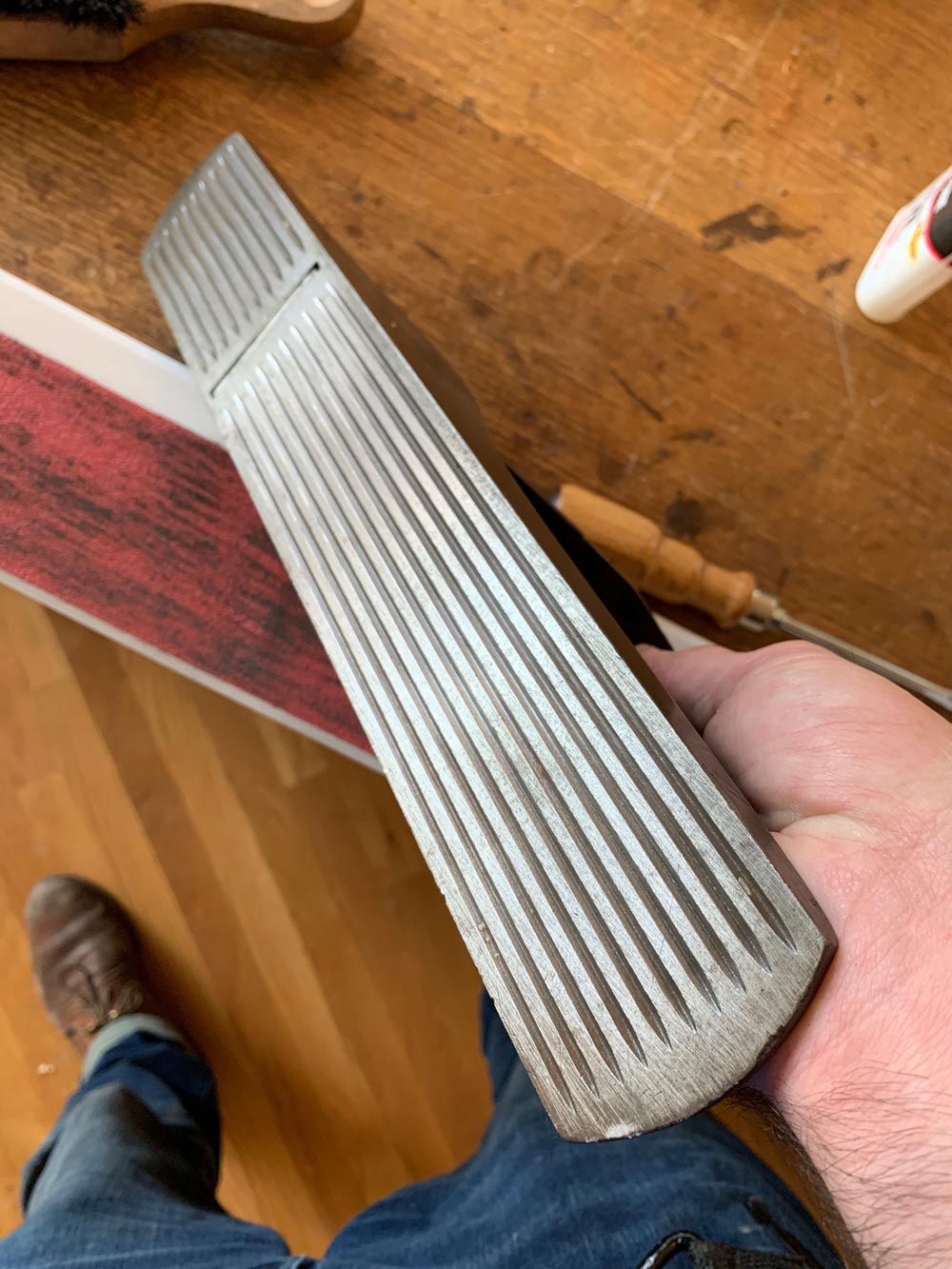
Clean the sole with oil and a rag. You probably have some grit and crap inside the frog now. So take apart the whole tool, clean it and wait for my next installment on sharpening the iron and preparing the cap iron and chipbreaker.
— Christopher Schwarz
The Jack Plane Series
The Jack Plane You Really Need: Part 1
Clean & True Critical Surfaces: Part 2
Grind the Iron & Fit the Chipbreaker: Part 3
Set Up & Use: Part 4
“Tighten the frog’s screws tightly.”
‘Ah. That would explain why my iron shifts in the mouth. I blamed the lever.
More Wheaties on the screwdriver! Aye Aye!
Thanks.
A suggestion, but only for rusty threads. You can grasp a bolt in vise grips and clean the threads using a wire wheel. You don’t want to do this unless there really isn’t any alternative, because the wire wheel will take some base metal as well as the rust. But if toothbrush, brass brush and Naval Jelly and elbow grease won’t answer, then go with the nuclear option: the wire wheel. It’ll shine your threads. Albeit slightly thinner. And make sure you have a good grip on the bolt—the wire wheel will fling it at very high speed into the darkest corner of your shop.
Brass wire wheel is the secret to quick clean up without losing steel. A real brass wheel, not the ‘brass coated’ steel wheels often sold today; though I’m sure they’re better than just a raw steel wire wheel.
A real brass wheel is not cheap, so don’t expect to run out and buy one to spruce up that 10 dollar plane. One more reason to always take a magnet with you to the flea market. 🙂
Excellent point. Thanks. (Ditto the magnet suggestion).
Okay if we also post your PW video that accompanies this? I found it to be a great help in the past:
https://youtu.be/RlYDipD_5s4
I’m really enjoying this blog post series. Thanks Chris!
I really really appreciate these posts on the plane. Thank you, thank you. I look forward to more.
Very helpful.
80 grit is just the starting point, right? Do you need to go all the way to 1500 on the frog, to get a nice polish?
1500? Add two zeros!
Don’t chicken out: Moore pattern scraping or go home! If it isn’t hand scraped to half a tenth (of a thou) at 40 ppi, then you’re just not going to be at the lunch table with the cool kids.
This is sound advice. I have a premium No 6 (LN), which I love. It was actually my first plane and I recall reading a similar article (I believe it was by Fitz, but might be wrong) noting the benefits of having 2 blades for this one- 1 setup as a Jack with an 8” camber, and the other setup for jointing. I have implemented this approach which (in my mind) justifies the premium purchase. It is a great versatile plane. Just in case you’re wondering- no, I have never used this plane for slicing goat meat.
After reading chris’s handplane essentials and both anarchist’s books, I threw a premium thick blade into my old stanley no 5 for smoothing and put a hefty camber on the old thin blade for rough work. I set the frog way back so the thick blade would fit. This had the nice side effect of leaving it nice and tight when smoothing and really open when hogging off material without needing to adjust the frog everytime.
Incidentally, Rob Cosman suggests creating a 20 degree back bevel on a third blade which effectively gives you a 65 degree high angle smoother. Haven’t tried it yet but will as soon as i hit a patch of stubborn grain.
I recently found a Stanley #5 1/2 with 2 1/4″ blade; Its hefty. Have you ever used one? What were they made for?
To compete with panel planes in the U.K. David Charlesworth in Devon adores his. He uses it for everything (and with great precision), such as edge jointing, flattening panels and smoothing.
Thats good to know!
This was a barn find with ages of crud. Now I’m inspired to clean it wile following this blog.
Your technique is top shelf.i clea ned and oiled up two jacks and a mini while listening to your methods.tip of the hat my friend. El Tejano
The new improved Tool Time? 🙂
Do you still maintain that a No. 6-sized plane is easier for people to learn to jointing?
It seems as though since it’s worth saving towards a new premium No. 7 / 8 jointer, an old No. 6 could serve as a hold-over all the while affording the opportunity to practice.
(Although I’m not a strict minimalist, I don’t want to own more tools than necessary. So I’m worried how hard it is to get rid of an No. 6 afterward, or if it would still have a worthwhile role).
Dave, I don’t remember writing that (without a ton of caveats), but I think the No. 6 is fine for jointing and can be a bargain.
In a PW blog post from Feb. of this year, titled “Understanding Bench Planes,” you mentioned it was “easier to teach someone to joint an edge with No. 6’s than one of the longer planes…”*
I guess what I should be asking is, does the No. 6 flatten the learning curve for enough time to justify owning one or is it simply a good teaching tool only in the very beginning.
*I conduct research reviews somewhat regularly in my profession – I think that’s led to a fair portion of my brain being dedicated to citing sources/remembering where I read something.
That wasn’t from this year. They reposted that from a million years ago.
Yes, it’s easier to learn edge jointing with a No. 6. Your work will determine if it’s the right plane for you long-term. If you joint 8′-long tabletop edges, you might prefer a longer plane.
My advice is to try out the planes at a store or a friend’s house. Your hands, your personal mass and your strength all contribute to what you will use in the end.
Thank you – I appreciate the input.
I really enjoy these plane posts. Thank you.
A, perhaps horrible, question. How do you feed about doing rough grinding of plane soles etc on a belt grinder to speed up the process? I can’t imagine you would do such a thing, but how bad is it that I do it?
It takes real skill to do it. Try the belt sander paper on granite. It is remarkably fast
Thanks for this! I bought a Buck Brothers jack plane about 30 years ago at Home Depot, it worked so poorly that I used it a couple times to gouge and tearout a couple projects then threw it in my toolbox. where its been sitting since. I have been using an old Stanley now that works 100 times better. Following the instructions here, I found that the the frog surfaces on the Buck were painted, both parts, and very poorly where they mated. The sole was really really bad too so that I mostly flattened – good enough-ish. But I think it was mainly the paint on paint contact of the frog that caused most of the issues. Its actually a usable plane now.