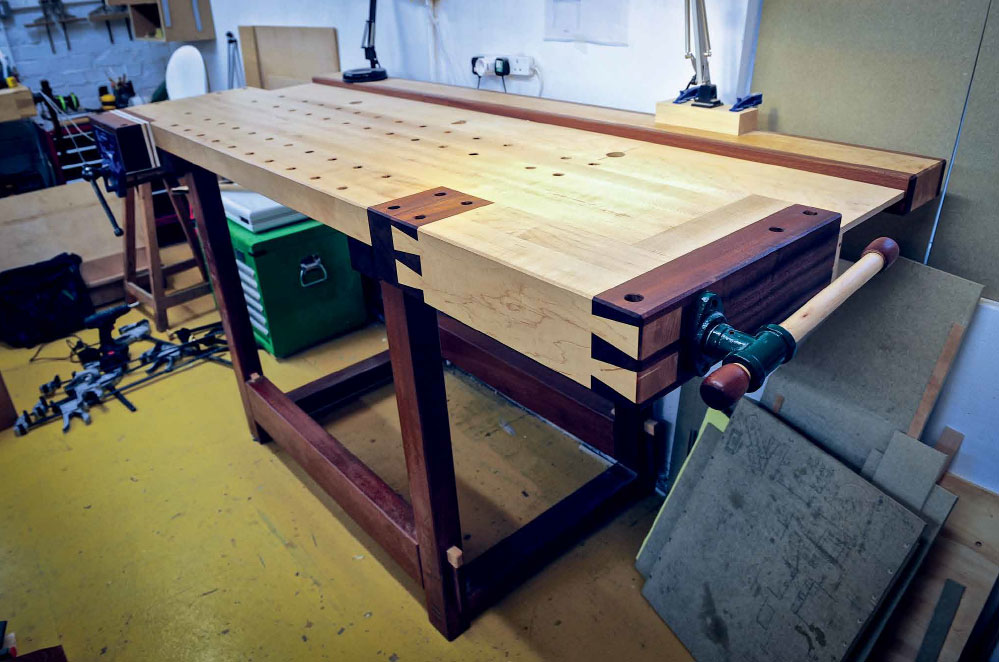
This is an excerpt from “The Intelligent Hand” by David Binnington Savage.
The most important thing the bench does for you is hold a job whilst you work on it. (I remember my early days without a bench, struggling to hold work with one hand whilst cutting with the other. I am amazed I came out without more damage to my digits. The opportunity to saw off part or all of my hand was a daily event.) The bench is just a giant, flat holding device that allows you to get into the correct position to do the work properly. You are then free to concentrate on balance and being in control. That’s what matters – control.
There are a few things a cabinetmaker’s bench has to be. It has to be heavy. You will be exerting horizontal and vertical forces on it, and you don’t want it moving around – so spend some money on timber and make it heavy.
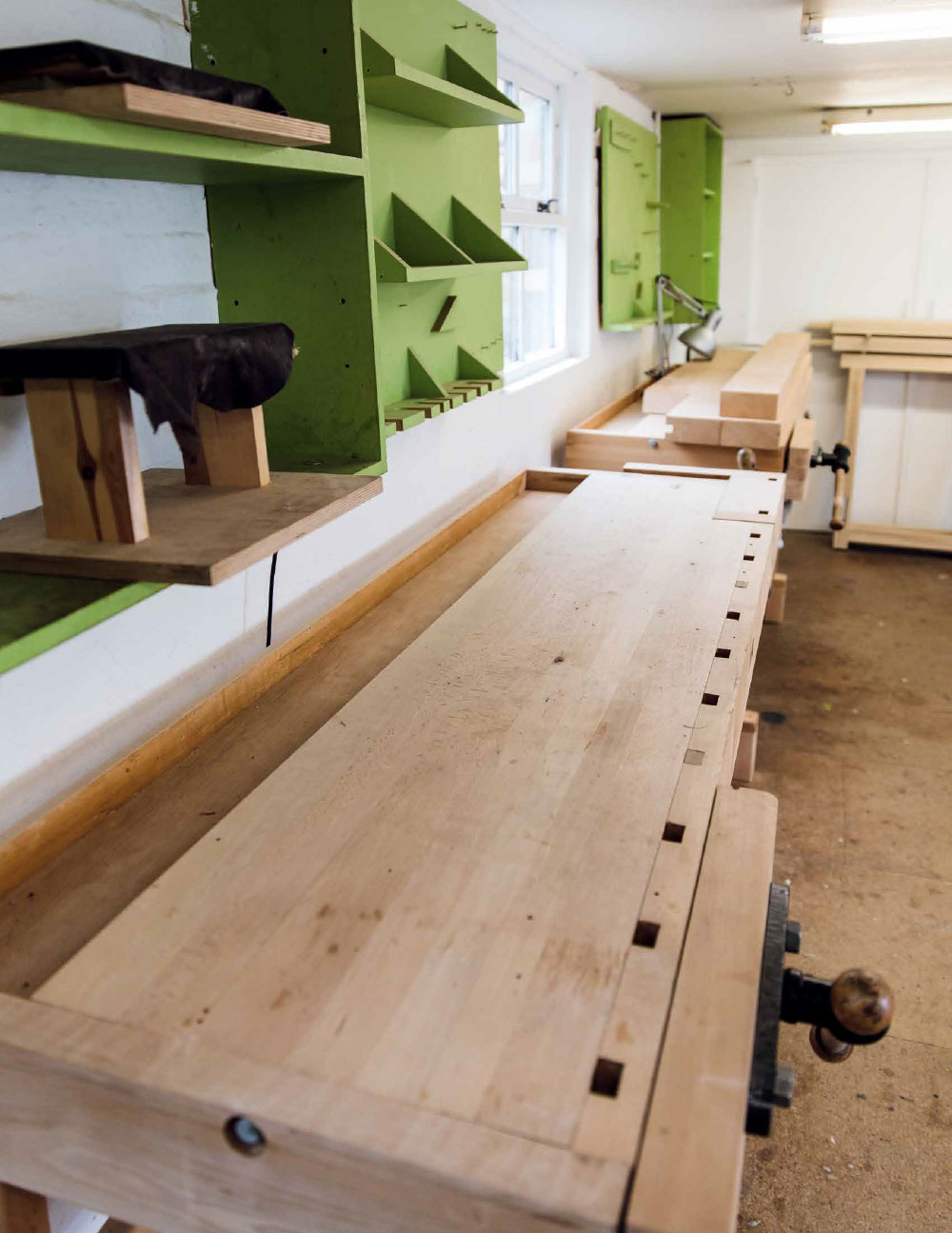
Make your bench to suit your height. This is critical. Many benches I see are very low. The bench height we suggest has rewarded us with strong, undamaged backs. It’s a high bench surface set up for general planing. To determine the right height for you, stand alongside a bench. Bend your elbow. Extend the forefinger and thumb of your left hand. Touch your thumb to your elbow. The point of the forefinger is where your benchtop should be. This will do for almost all work. In case you do need to get on top of a job, keep a small “hop-up box” stored beneath the front rail.
The bench has to have tool well. This is the place to gather the tools in use for a given project. The working surface of the bench should be kept as clear as possible at all times. The benchtop is for the job at hand – nothing else. We know that this game is about skill with speed, and speed is about organisation and picking up and putting down tools fast. Thinking ahead, not being slowed down by a lost chisel in a pile of shavings, is key. We go nuts about such professional practice at Rowden. At the end of day, we put tools away sharp. I know you are tired, but sharpen your tools, sweep the benchtop, sweep the floor – then go home.
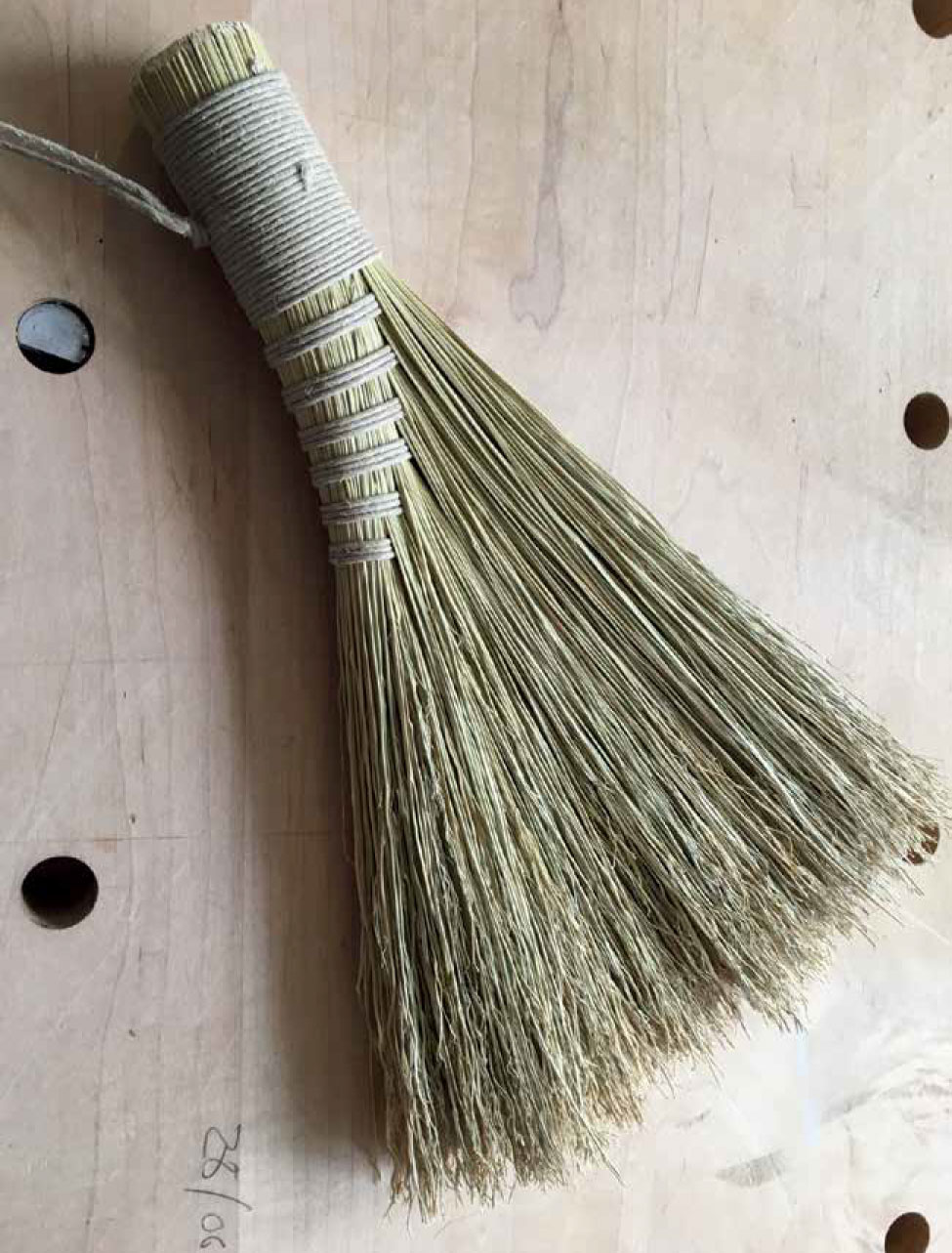
Benchtops need to be swept down regularly to keep them free of dust and shavings. Christopher Schwarz sent me this brush as a memento of our visit to Shaker Village at Pleasant Hill. Just look at the design and workmanship! The ends of the bristles thin down to fine strands, and at the bottom they form not a straight line but a gentle arc. Perfect for this job. Look at the binding wrapping elegantly in groups of three, then a gap, gathering more with the movement of each group of three down the handle. At the base, the full handle is bound with an inexplicable hanging hook, coming from the centre of the binding. How did they do that? This, Chris calls a Turkey Wing, I call it the best bench brush ever to have been made.
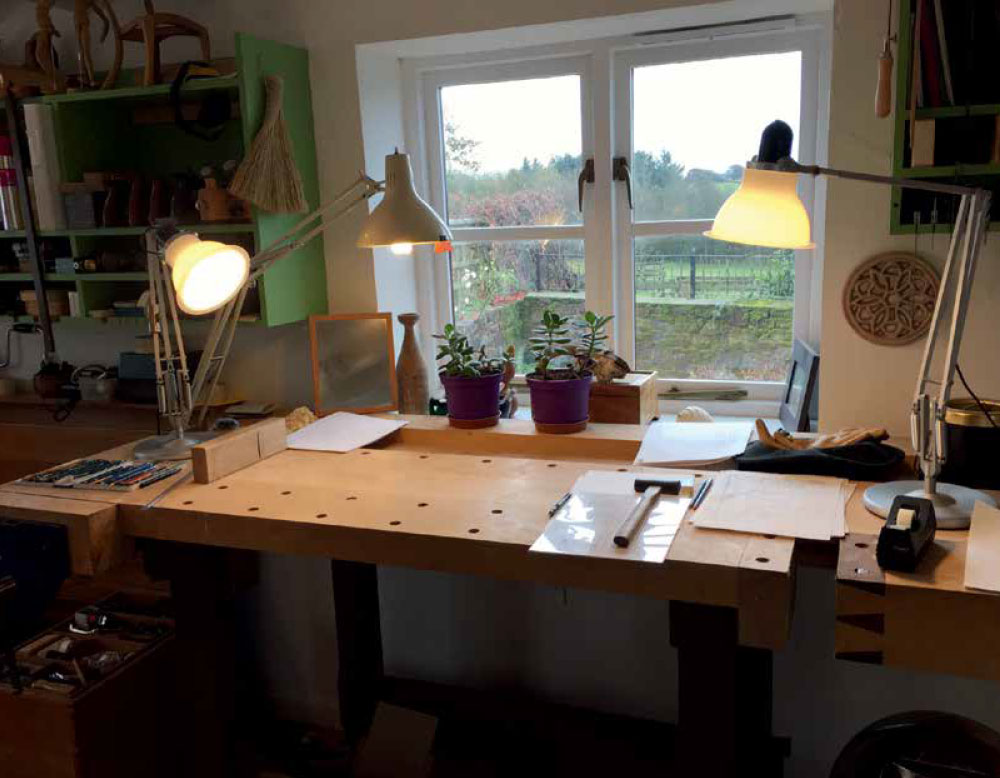
You can go a long way with great bench, a bag of good, sharp hand tools and good bench light. As my eyes have dimmed, the number of bench lights I need has increased – but you will likely need only one, a good one that can be moved around all over the place.
The tool well collects everything from shavings to dust, tea mugs to half-eaten sandwiches. That’s what it’s for. The bench surface is golden territory – keep it clear and clean; do it no damage. When making this surface, you will respond to the timber that you actually have available. But don’t be tempted to make the bench surface too wide. You need to keep this surface flat, and if it’s very wide, you will need very long arms to flatten it…and the task will be tiresome and not done as regularly as it should. There will come times, usually when developing third-scale prototypes, that you use this bench surface as a datum reference surface – so it’s important to keep it spot on. Our practice is that at the end of every big job, the surface is dressed lightly with a bench plane. Just a shaving all over gets it clean, flat and new – ready for the next job.
— Meghan B.
A sketch of the author’s technique for establishing bench height would be helpful. As written, I get a wide range of heights depending on the position of my arm and where I point my finger!
Yeah, I had to retread that a couple of times. Here’s my best guess. Bend your elbow to 90 degrees. It doesn’t really matter the angle, just enough to differentiate the upper arm from the lower arm. Take your thumb and forefinger of your opposite hand and extend them into a “L” shape. Place the extended thumb horizontally at the bottom of the bent elbow with the forefinger pointing down to the floor. The distance from the tip of the forefinger to the floor is the height he likes. Just a guess.
From basic ergonomics, the ideal surface working height is the distance from the floor surface to the bottom of the bent elbow joint, less 150 mm (6 inches). This applies to 95% of the population. Don’t forget that as you age your spinal system compresses and, eventually, you become shorter by about 50 mm to 70 mm. (I prefer to think that the floor level is slowly falling.)
I used to be six feet tall but I’ve compressed an inch and a half in the past 20 years. I’m gravitationally challenged.
I’m also not exactly sure what the author is describing. But it does seem to point to a higher ideal height than most methods. I’d be really interested to get more insight on this topic. Maybe Chris discussed this with the David at some point?
This bench height would seem to be much higher than the benches that I have encountered (granted, I am very new to woodworking). It seems as though I have heard the first thumb knuckle rule to set the height. I am a couple of inches over 6 feet and would think that this higher bench would make sense for my back. Does “The Intelligent Hand” discuss this more in depth? Is there another of the multitudes of bench making books that may give me more insight to this?
Paul Sellers blog
Here is a great treatise in primary bench height:
https://www.theenglishwoodworker.com/workbench-height/
The true solution is multiple benches for different types of work. I don’t mean six Roubo behemoths filling up the shop. Your basic bench, plus a couple of sawing benches, and then appliances for the main bench. You can add a smallish Roman workbench if you want to join Chris in rediscovering their usefulness. 🙂 I built a sawbench in the style of a Roubo with a small leg vice that I use ALL the time; call it a French Roman mongrel?
As for appliances, Chris’ blog at pop wood talked about twin screw vices (often called Moxon vices after Chris popularized them), but I just searched the new site and got this link: https://www.popularwoodworking.com/product/moxons-bench-vice-download-2/
Anyway, the vice is great to put on top of the bench for joinery (cutting dovetails, etc.). Here is a perfect example from Benchcrafted: https://www.youtube.com/watch?v=yJzYAaHKDvc
Sawbench: https://blog.lostartpress.com/2008/02/10/this-year%e2%80%99s-model-the-2008-sawbench/
Cheers!
It does seem to imply a higher bench than I am accustomed to. I find tall benches to be insufferable for planing. When I need to get close to the work for details, I pull up a stool and take a seat. It’s the opposite of what David suggests.
Alternatively, mock up a bench to determine a height that works for you. Set up saw horses, crates, boxes, etc; grab some 1/2″ or 3/4″ stock to vary the height; and grab your favorite 2-handed plane or two and practice “dry” planing using a proper stance. Remember to factor in footwear and floor mats/stall mats if applicable. Try this many times over a period of days at least to account for variability in your stance and arm angles, even energy level. Keep records. At some point, the most comfortable and useful height will probably jump out at you.
It’ll be worth it in the long run.
I concur. This is the process I use as well to determine my bench height.
On the point of bench height, Jim Tolpin has one of the best solutions I’ve seen. Very straightforward:
https://m.youtube.com/watch?v=bBS5-AV81lg
Yesterday, I had occasion to flatten one side of a 16/4 x 12″ piece of clear Doug Fir. I put it on my 34″ bench, and thought of this video. My handspan is 9 and a 1/4 (At 6’2″, my boot heels have gotten taller over the years. 😉 ). 4 spans comes to 37″. I think the original article suggests 38″. 38″ on the push stroke is too high, but it could be just about right for pull stroke planing.
I suspect that body geometry – all of it, not just handspan multiples – accounts for bench height preference. There are different ways to get to 74″ total height. Distances from floor to knees to hips to shoulders to elbows to wrists are as different as DNA. Now toss in the circumferences indicative of muscle mass. But how do you ignore personality, blood type and lung capacity?
In short, we are deep into complexity where cause and effect is not known, and where “experts” just get in the way.
Interesting. My bench has been slowly getting taller over time. Converting to metric to match the images here, my current bench started out at about 36″/915mm. I’ve bumped it up twice, in 3/4″ increments, and it’s now about 37.5″/950mm. I’ve recently been thinking about moving it up again, to see how I like it.
According to most of what I’ve read, making it higher than that is crazy… the recommendation I see most often is that it should be between the knuckles and wrist of one hand hanging loosely. That’s way lower than I have it now. On the other hand, this article seems to suggest 40-44″ (1016mm to 1115mm) depending on how I hold my hand. I’m not sure I’m willing to go that high in one jump, but I’ll certainly be trying it!
A little talked about bench design criteria is: Maximize Flexibility. Flexibility is something that I have always cherished. Put another way, I hate when I have no other choice. Think about that in the bench height disucssion. Personally, I like to get close to the work during layout steps. I can sit down on a stool. With a higher bench that just makes things a little too close.
With the crochet, leg vise and deadman, I can put the edge work wherever I want it unless the bench is already a little high. I can’t get it lower than the top. On the other hand, if a fella doesn’t have clue about a height that works for him, then making it tall let’s him trim to fit. Although, it’s more likely he’ll live with it, until one day he goes “postal” on his workbench.
In my experience, a good pair of leather lasted packer boots keeps a back happy. White’s, Nick’s and Drews’ come to mind.
I’d add Wesco, Role Club (if you don’t mind spending and waiting), or even good ‘ole Red Wings if you’re on a budget.
Agree with Wesco.
The key is knee geometry when standing. I wear a pair of Nick’s (fully rebuilt twice. Over the long haul cheaper than Red Wings.), and I have no back discomfort after 8 hrs in the shop. They put my knees in the right position.
As a scientist, I’d love a study that would come out and say “a bench 0.37x your height” is the absolute best bench to have. Unfortunately that will never happen; in part because no scientific institution will ever fund such a study but also because there really isn’t one best bench height. My bench height is ok for planing; good for chisel work if I’m seated on a stool and poor for sawing. I suspect that this is the case for most hand-tool woodworkers ie. there is no one consistent bench height that is perfect for every task.
In fact, I think the “right” bench height is one number today and something different tomorrow. What we do on our benches changes. Our bodies change.
To use a formula like 0.37*height would only work for 1 standard deviation, at best. That is the best a study could do.
Love benches made out of nice woods, but I’d worry after building it about spilling things or dropping a hammer etc. Much prefer to make it from cheap wood then not such a big deal. Same thing applies to classic cars, if its restored to perfection you dont want to park it anywhere and leave it.
His explication to bench height is the same one we get as apprentices here in switzerland.
The best book on benches that I have read is The Workbench Design Book. That book covers all the relevant topics on workbenches. All other books and articles that I have read are judge by that one book. I read the intelligent hand and the only gripe I encounter was the comments on honing guides. I can free hand for sure but my LN honing guide is a treat to use. If he does not want to hire me for that guess what; I would not want to work for you anyways. Other than that he has some interesting stories. I think what I appreciated the most was his explanation on how to tune Stanley bench planes by putting a relief on the mouth so the chip can curl easier.