I wrote about the following trick to reduce splitting when nailing in “The Anarchist’s Design Book.” Since then, I’ve caught flack from people who say it’s not true. So much so that I’ve been doubting my own shop experience.
Here’s the problem: When you nail together a piece – especially using cut nails or Rivierre nails – it’s easy to blow out the end grain, reducing the holding power of the nail. Driving a tapered nail is a delicate balance. You need the nail to bite hard, so you don’t want to use a huge or too-long pilot hole. But if you use a pilot hole that is too small or short, the nail will split the work and ruin everything. Oh, you also have to account for the wood species and how thick it is.
It’s a balance of factors to get a good joint. (And that’s why I recommend you make a test joint before nailing together anything – especially if you’ve never worked with a particular brand of nail or species of wood.)
All this is a lot of set-up for…
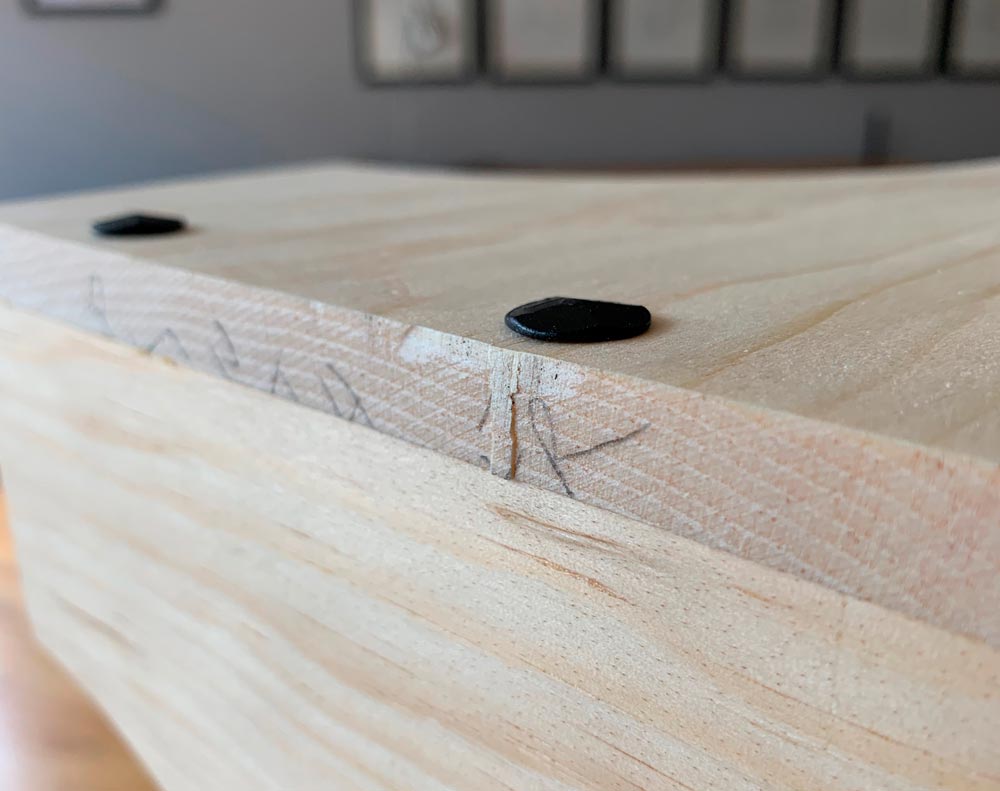
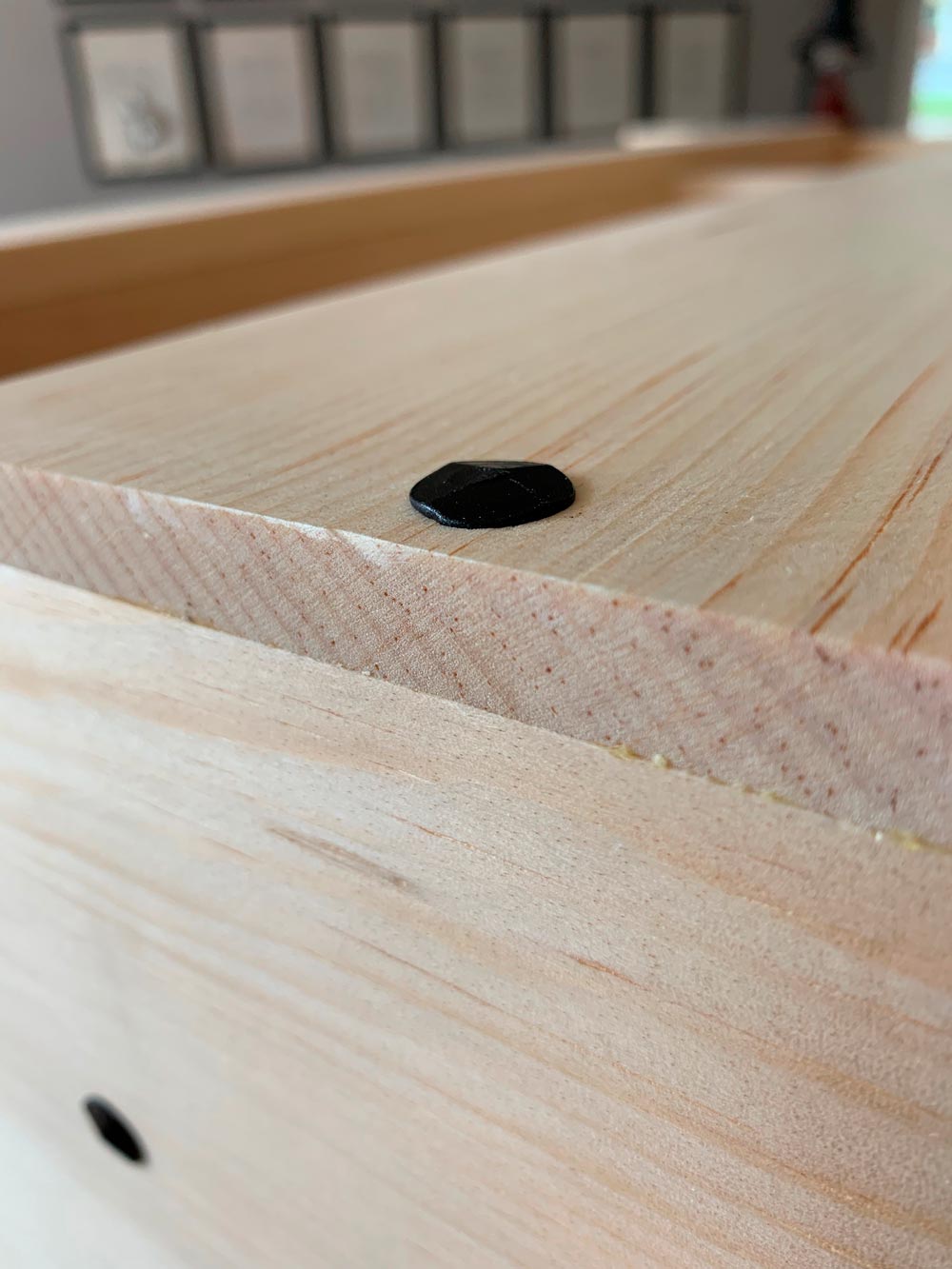
Here’s the Trick
If you apply a bar clamp across the end grain of the joint, you can reduce the tendency of the wood to split out the end grain. The clamp has to apply significant pressure for this to work.
Today I tried a variety of strategies as I nailed together a mule chest using 40mm Rivierre nails. All the joints were in Eastern white pine. All the pilot holes were the same diameter (7/64”) and depth (7/8”). And all the holes were located the same distance (7/16”) from the end of the board.
Without a clamp, about half of the joints busted out the end grain (good thing I started at the rear of the chest). When I added a clamp and applied hard clamping pressure – what you would use to close a joint – the failure rate dropped to zero.
I wondered if I needed to have the clamp at full pressure. What if the clamp’s pad simply acted as a wall to prevent the end grain from fracturing? Nope. Clamp pressure – lots of it – was important to keep the joint intact while driving the nail.
I have all sorts of thoughts on why this hard clamp pressure works. But I am weary of theories. If you’ve read this far, give this trick a try yourself in the shop before pontificating in the comments.
Confession: I was greatly relieved that this trick still worked. The internet had made me doubt myself again.
— Christopher Schwarz
So you have to move the clamp for every nail or can you just use a caul?
I have not tried a caul.
Blue tape. Collate a bunch of Rivierre nails. Feed them through your roofing nailer. The speed and impact of the pneumatic keeps the nail from splitting.
I think I need to see video of this to convince myself it works safely. Plausible, but the thought makes me nervous.
I would think adhering some sandpaper to the clamp faces may be beneficial also. Basically keeping the end grain together via friction so the path of least resistance is the crushing of the wood fibers instead of the splitting of the endgrain.
I don’t think that Chris is interested in building pallet furniture.
I had a old boss that made me work that same way. One morning he was on the other side of a breeze way we built and had his hand on it. I was shooting decorative nails into the inside top when i heard him yelp, he was stuck to the roof frame.a nail lost its head and travelled quite a distance to reach his hand and the nail had clinched to a boomerang shape. Be safe
Nailing your boss to the roof — that’s living the dream.
Ditto screws, especially countersunk.
Chris this maybe a crazy question but is the clamp vertical or horizontal. Are we squeezing the end of the board or clamping the board to the board we are nailing to? Jay
Sent from my iPad
>
Squeezing the ends of the board.
Thanks that makes sense now.
So clamping pressure is applied on the end grain, parallel to the long grain?
We are asking for the details on the clamping direction in part because the the first photo seems to show the clamping pressure arranged along the grain of the board, but your comments seem to indicate the opposite direction.
Thank you so much for this article. This has been a frustration for me with some Japanese toolboxes I’ve built.
The clamp’s bar runs along the grain. The large red pad is always on the end grain, because that’s where the rectangle of wood gets split out if it isn’t supported. In the second picture, titled “A common split,” you can see the rectangle of end grain that the nail pushed out the end of the board because it wasn’t supported by the clamp pad.
You definitely nailed that trick. You also hit the nail on the head by demonstrating the internet is sometimes full of crap.
I think the clamp prevents the wood from moving, and, therefore splitting. So the wood surrounding the nail compresses. I suspect this trick may not work as well with a species that is less compressible, such as oak.
Question: Does the nail actually have to grip in the top board in this case, or is it sufficient (as with a straight sided screw) that it grip in the second board? The latter is what we generally ask of screws, and if that’s all we need we can make the upper part of the pree-drill larger and remove the risk of blowout that way.
Clamping is a nice truck, but if we can avoid provoking the problem in the first place, so much the better!
I like to have a little bit beneath the head of the nail. I’m always pushing to squeeze a little more strength out of a nailed joint.
But yeah, if you drill a large clearance hole, you avoid splits.
Chris, Two things:
What is the thickness of both pieces of wood?
I fell with that pressure from the clamp the force of the nail take the least resistance so the clamp is giving more force to the end grain, the force of the nail is distributed in (equal) directions.
Think of nailing a lath for plaster, they would split, sometimes across the lath to both sides.
I could be wrong, Ralph
Since you’re gluing, these are decorative?
Not at all. No glue is permanent.
I always get nervous with modern building construction methods. Everything relies so much on adhesive. I know I won’t be here 100 years from now, but someone will have to deal with a lot of adhesive failures, I’m afraid.
My dad installed that fake cherry wood paneling (3/16 thick, cherry veneer on top) going up the stairs to the second floor of our house with “Liquid Nails”. Fast forward ten years and it was popping off the walls. Fixed with real nails.
“The internet had made me doubt myself again.”
No!! Fuck the Internets! Don’t ever give it that power.
I regularly doubt myself. I have a terrible case of Impostor Syndrome, as it relates to both my day job and my woodworking.
In both cases, I’m able to overcome it with determination and focus and little lists of tasks I can use to check off accomplishments. It works for me.
But I don’t ever let the Internets have that power over me. I know what it is and I’ve looked into its eyes. It is weak and easily defeated and hardly worth my time.
The results is your ultimate answer, ‘it works’. The nail acts essentially as a wedge. When clamped, the wedge can splay the needed space to fit and hold. When unclamped the splayed fiber will transfer that space as far from the point of ingress. Hold a bundle of drinking straws at one end, stab a pencil cross grain, watch the unheld end splay apart. Hold both ends of the straw bundle and the the difference. I hope this isn’t just repeating what others have posted. Happy woodworking.
Clamping pre-compresses the material, and forces plastic deformation around the nail as it goes through the wood, so there’s no elastic springback that would split the wood. I is a engineering per-fesser!
This I think is the correct explanation.
The clamp 8s running the length of the board, end grain to end grain. I think it’s impossible to apply enough hand pressure to a clamp to compress a board lengthwise, and if you could, the end of the board would show a dent where thge clamp pad was.
Across the grain, a good clamp and smallish pad can compress and crush fibers. But not length wise.
The clamp forces the wood to become compressed when the wedge shaped nail forces the fibers apart.
I have used the clamping trick successfully on the DTC using the Reviere nails…it works! Deformation of wood fibers proximal to the nail while supporting the outside with a clamp makes sense. The thing I wonder is why then doesnt it blow out on the inside where there is no clamping pressure? This is fun!
Didn’t see the photos earlier. I was thinking of the potential for splitting action in the bottom board. How significant is the potential for splitting of the bottom board?
Have you tried blunting the nail? This is a trick taught to me by an old wooden boat builder. He would hold the nail against a hard surface and tap on the head to square off the point. His assertion was that the sharp corners created would cut the wood fibers rather than dividing (splitting) them. It was a technique that he used at the end of all his hull planking.
Probably works, but for a different reason. Smaller crack radii create greater stress concentrations.. larger ones less so. It’s why one drills out a hole at the end of a tenon one is going to wedge.
Probably works, but for a different reason. Smaller crack radii create greater stress concentrations.. larger ones less so. It’s why one drills out a hole at the end of a tenon one is going to wedge.
I have been using cut nails from Tremont for quite awhile now, but I use a tapered pilot hole drill bit, and a hand powered reamer to “top dress” the hole. I very seldom ever have a problem with splitting. One observation if I may. I think that sometimes too much zeal in trying to “sink: the head causes the material to split. I have never used your method but I may give it a try.
Would cut nails work for plywood cases? I should think so, but there might be reasons not to that I can’t think of?
Used them many times with no problems. Always do a test joint to make sure you have the right pilot hole. Sheet goods can have some wacky guts….