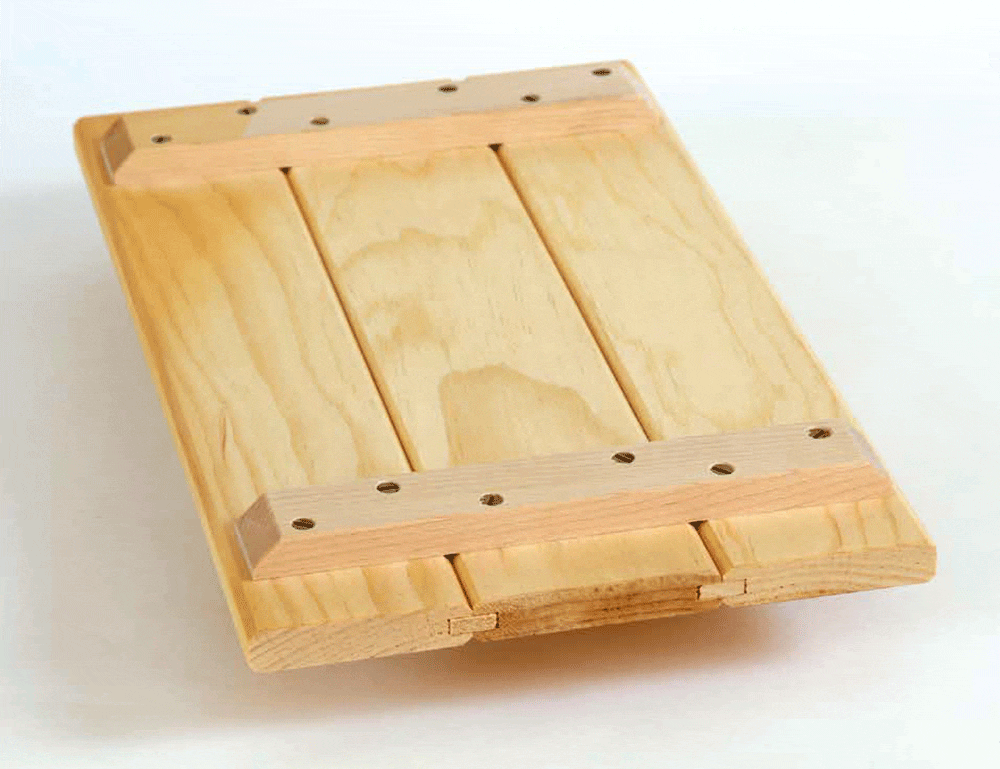
This is an excerpt from “Shaker Inspiration: Five Decades of Fine Craftsmanship” by Christian Becksvoort.
Even before frame-and-panel doors come into widespread use, larger doors had to accommodate seasonal wood movement in one way or another. The most common method was to use a series of individual boards, rabbeted, splined or shiplapped, with small spaces in between to allow movement. These doors, sometimes two or even three layers thick, were held flat with battens on the inside. The battens were nailed, “clinched,” or killed (yes, dead as a door nail). Nowadays, screws are often used instead.
Almost all furniture doors are made with frame-and-panel construction. Let’s go over some of the options. For cabinet doors, a 1/4″ (6.4mm) groove is run into the top and bottom rails, and likewise the two stiles. Panels can be flat, flush on one or both sides, raised, carved, moulded or inset. In any event, if the panel is solid wood, it is allowed to move, or “float,” in the grooves. Some woodworkers purchase small rubber balls to keep panels from rattling. I find that a cheaper and easier method is to center the panel, and drive a small brad (from the inside of the door) through the middle of the rails, close to the edge through the panel tongue, and into (but not through) the front of the frame. A bit of filler, or a tiny wood plug makes it all but invisible.
On fine furniture, the corners of doors are usually mortised, tenoned and pinned, for maximum glue area and strength. On tiny clock or desk doors, a bridle joint can be substituted for increased glue area. Kitchen cabinet shops often use stick-and-cope construction. A moulding profile is run along the stile and coped into the rail end, forming a snug, yet relatively weak corner joint. Alternatively, many woodworkers use dowels in the corners, while biscuits are another alternative. Although stronger than a stick-and-cope joint, these methods don’t have much glue area and are therefore not as structurally strong as a full mortise-and-tenon joint.
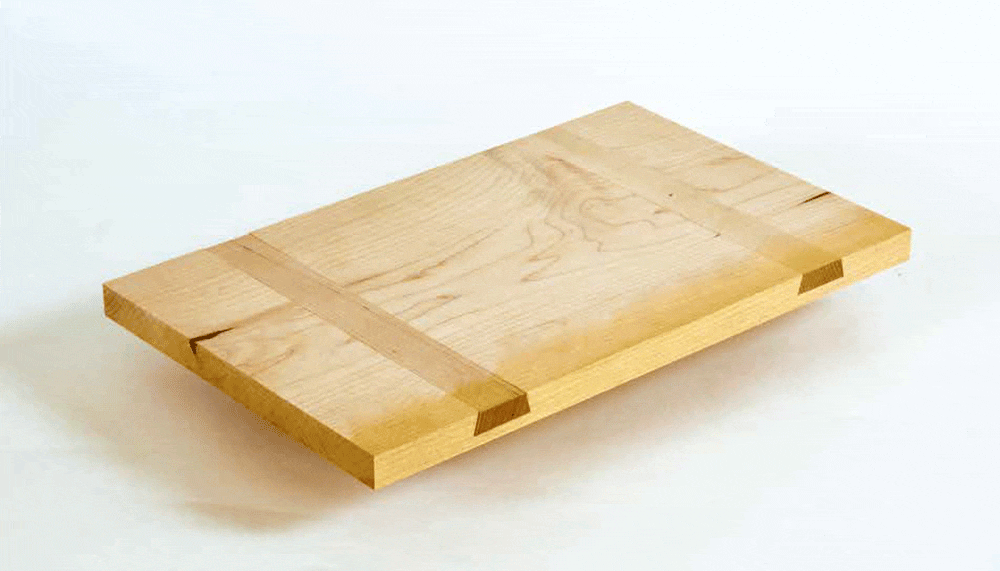
So what about slab doors? As stated above, battens are necessary to keep the slab flat. However, I find them cumbersome and gawky looking, and I have been using several alternative techniques. The first is the fairly traditional fitted dovetail batten. It’s flush with the inside of the door, and anchored with a small brad at the center.
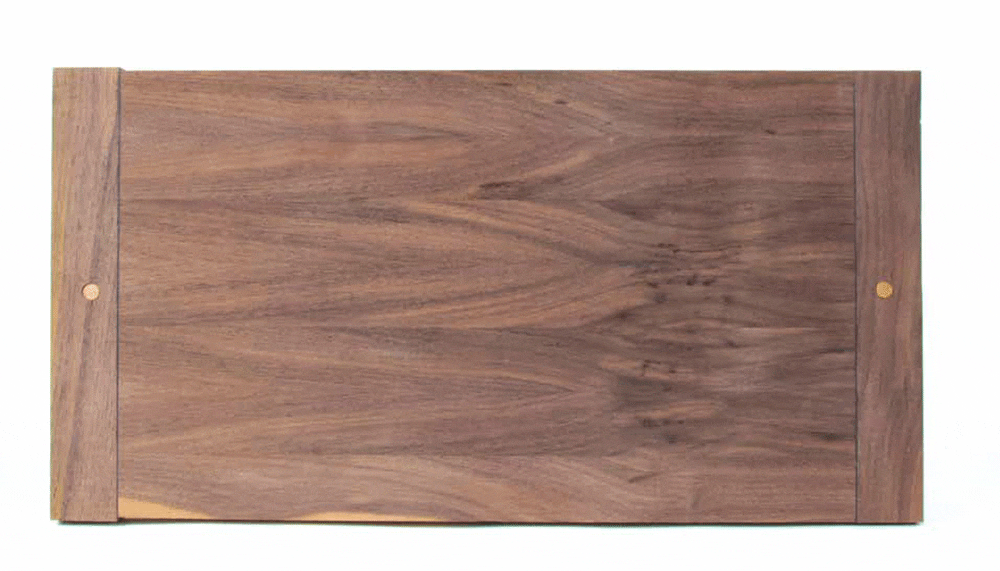
The second is to make breadboard ends. After all, if you can use breadboards on tabletops and desk lids to keep them flat, why not on doors?
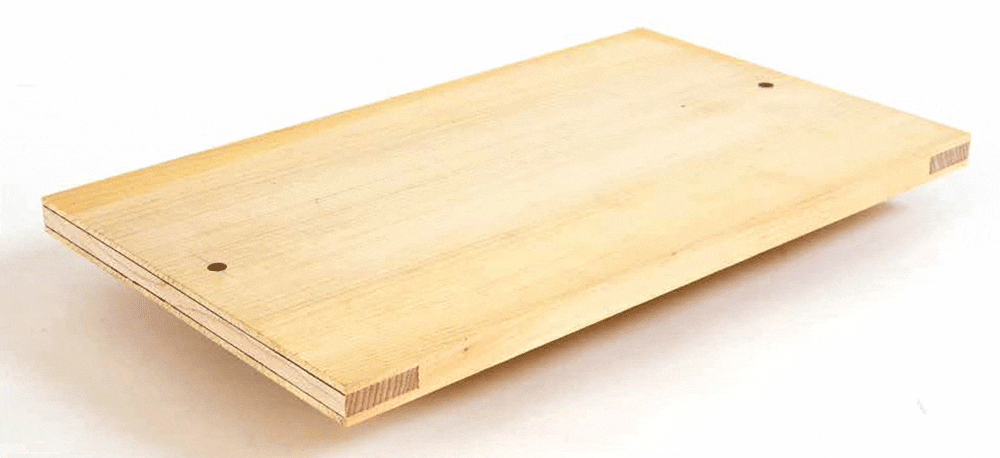
The third procedure is a bit trickier: the hidden breadboard. Cut a groove into the top and bottom ends of the door, and insert the breadboard, or batten, inside the groove. Again, anchor it in the middle.
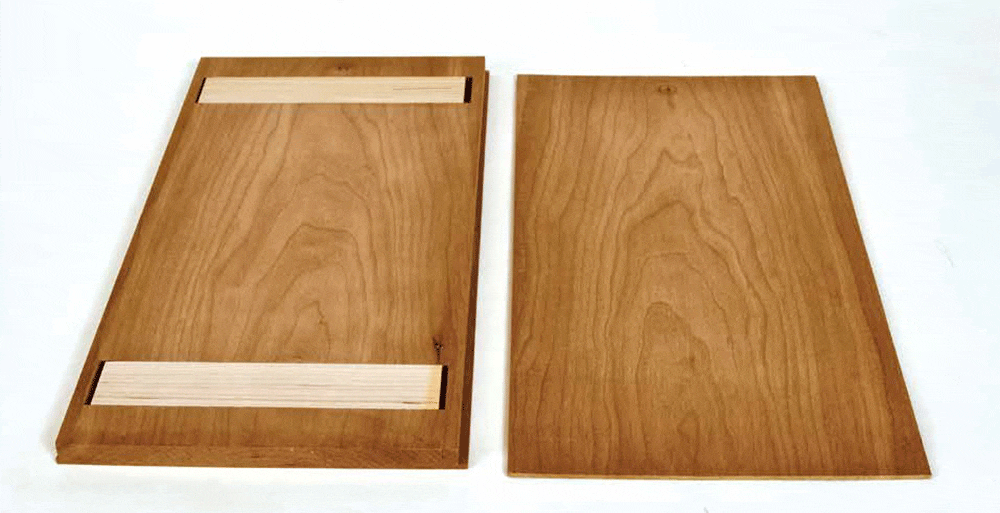
Finally, the coolest of them all: the totally invisible batten. Make a core of the same wood as the rest of the door, and rip off strips on both sides. Then cut off both ends of the center section, and groove the edges you just cut. Make a batten of the desired width with tongues along both long edges, and cut it slightly shorter than the center of the core. Glue the whole back together and flatten it. Then glue a face veneer, 1/16″ to 1/4″(1.5mm to 6mm) thick, depending on the size of the door, to both sides. Edge all four sides and you have a stable slab door. Nothing showing.
— Meghan B.
I’ve never seen the dovetail batten or the invisible before. Bother are very cool, although I actually prefer the the former. Thanks for sharing.
This is the coolest email/blog post I’ve seen in a while! Loving all these alternatives.
When I first started woodworking, a local church had suffered a fire in it’s adjacent school. They were clearing all of the pews from the lower church to use that space. They were throwing the pews in a dumpster, and I dragged as many home as I could.
The pews were all oak, and from the late nineteenth century. The seats all had dovetailed battens every few feet.
Can I please get a little clarification on the dovetail batten choice from somebody who has used it?
I tried using it on a lid cleat on a blanket chest in place of screws; I figured it would make for a cleaner look without the screw heads. My experience was that I had a hard time fitting the sliding dovetail so that it was tight enough that it would hold the lid flat against movement, but also be possible to fully install it. I put the other two on with screws, being concerned that the dovetailed cleat wouldn’t be able to hold the lid flat.
I got dovetailed cleat as tight as possible over the 14″ length of it, needing a mallet to get things all the way together. This winter, it showed gaps between the lid and the cleat as the lid moved with the seasons.
Tapering the batten/cleat, as I understand it, isn’t an option: either the taper prevents the cross grain movement as it tightens with the seasonal movement (if it’s anchored at the skinny end), or the whole thing loosens, preventing the batten/cleat from holding the panel flat (if it’s anchored at the fat end).
I cut my dovetail with a router and a 7 degree dovetail bit. I’m wondering if I’d have been a bit better off using, say, a 14 degree bit. The larger included angle should (in principle) mean that the cleat tightens against the lid and holds it flat with less movement, but I’m curious to hear what other people’s experience has been.
I should note that I did all this before I got a copy of Christian Becksvoort’s book, figuring it should work. Having now read his book, now I know it does, I just haven’t figured it out yet.