
My favorite instructor, Mr. Williams, always said Anyone can do something right. The real skill is knowing how to fix things that go wrong.
Maddeningly, there will always be things that go wrong. Overlooked abrasive marks beneath your flawless finish? Check. (Scrape the whole tabletop down and refinish.) A brand-new oven front dented by a dropped cabinet door? Check. (Pay to have oven part replaced by manufacturer’s service person.) Etc. The moment of discovery is always a punch in the gut.
My most recent experience with this sickening phenomenon came earlier this week. I was making great progress on a job I’d started that morning—months later than anticipated, thanks to a stack of other work commitments (and also thanks to my clients’ patience). The job involves a set of panels custom veneered with dyed eucalyptus. As I made the first cut, my client’s reaction to the price was still ringing in my ears. “X-thousand dollars? Just tell me–is this like buying a gold-plated toilet?” No, I reassured him; the purchase didn’t necessarily qualify as extravagant. The price reflected the exotic species of veneer, which was dyed in Europe, then exported to the United States.
Around midday I was lifting another panel onto the tablesaw to miter an edge when my eye was caught by a note in my handwriting on the order form: Grain to run horizontally, i.e. parallel with dimensions under “width.” The grain on the panels was vertical.
I got the job folder from my bench and sifted through the records. Sure, the evidence was right in front of me on the order form, but I honestly couldn’t remember which way the clients had wanted the grain to run. It had been so long since we’d discussed it–and the magnitude of the cock-up (to use a charming British term) would be so daunting that I just wasn’t ready to believe it.* I called the clients to check. No answer. I left a message. Next I wrote by email.
By bedtime there was still no response. I hardly slept that night; each time I lapsed into slumber, I found myself in a different subconscious-generated torture scenario involving horizontal versus vertical grain.
The following morning I contacted Max Jeffrey, the salesperson at Heitink Veneers, and let him know there might have been a mistake. He said he would look into it and assured me they would make things right.
And that’s exactly what they did. No prevaricating, no drama; just a sincere apology for having laid up the veneer in the wrong orientation, while noting that this kind of error is exceedingly rare because they take grain orientation seriously. (As a customer of theirs for nearly a decade, I know this to be true.) Tell us what we need to do to make things right for your clients, Max said.
When my client called back, I explained the situation and asked whether he would like Heitink to order new veneer and remake the panels, or would he and his wife like to keep the grain vertical. My personal preference, I added honestly, was the existing vertical orientation, because the island’s stone counter has a bold lengthwise grain and I thought the added linearity of horizontal-grain panels might make the island seem as though it was ready to shoot through their back door. They asked for a break on the price, and Heitink agreed to refund that amount. (The clients had purchased the veneered panels directly and had already paid in full.)
To paraphrase Mr. Williams, Anyone can do something right. What’s truly impressive is making things right for your customer—graciously—when you have made a mistake on their order. When I asked Jan Heitink (he’s Dutch; his name is pronounced “Yon”) whether he would permit me to identify his company in this post, he said yes, adding, “We strive for perfection in our products but in real life there is no such thing and when a situation does not go as planned, how we react to the situation is what will leave a lasting impression.”
I couldn’t have put it better myself.–Nancy Hiller, author of Making Things Work
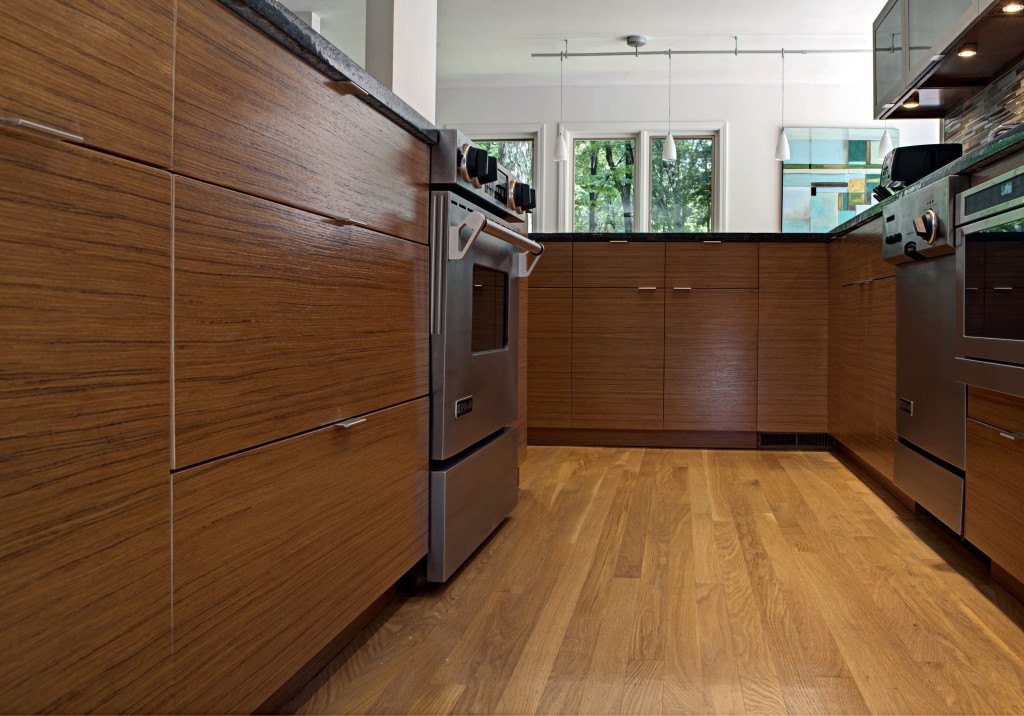
*This is why I put everything in writing. But even so, in this case, I wanted to consult the clients to make sure I had ordered what they wanted.
This is why, in a reply to one of your earlier blog entries, I suggested you teach a class on business and morality in business. It could be a one day overview of what all is needed to start off on your own (besides an understanding of a profit/loss statement): a strong moral compass is very important in early days as the lack of one will mark you forever, not only with customers, but vendors!
I appreciate your suggestion, Tony. I have done one seminar (in the grad school sense of the word) on related topics and am open to doing others.
Nice article, Nancy.
I realised today that my latest batch of bookends have sanding marks that are quite noticeable under strong overhead light. So yeah, those are being shoved to the back of the stock cupboard until next Christmas, when I’ll have to figure out which distant relatives haven’t already received a pair…
Zounds. Once I discovered what had happened, I’d have been crapping bricks. Heitink sounds like a first-class outfit.
I’ve watched a number of world class woodworkers demonstrate their skills. 90 percent of the way through, their efforts look pretty much identical to my own. Then in the last bits, they finish a magnificent work, where mine ends up — not. I guess what I’m saying is, I would amend Mr. William’s “The real skill is knowing how to fix things that go wrong.” To include turning something almost good into something excellent.
“If it isn’t written down, it never took place.”
Such a pleasure to hear this positive recognition when something could have been disastrous. Noteworthy is the response back from Max Jeffrey (Jan Heitink’s Mgr of Inside Sales), “Tell us what we need to do to make things right?”. Cradled in accountability, It simply says, “let’s do what’s best in the eyes of the end user”, and is founded in Jan Heitink’s basic philosophy that “the job isn’t finished until the owner smiles”. I know this tenet well as an example of the empowerment that Jan gives, and expects from all his employees, …. “to right all wrongs, and to make things happen”, because as he also says, “it’s my name on the door!”
Bill – VP Architectural Sales – Heitink Veneer
I really like your posts, nearly everything you write strikes a chord with the me, your book is Making Things Work is great too.
I’m happy to say that’s how my company operates also. It hurts to lose the money but the loyalty from the clients is priceless and has certainly accounted for a better overall bottom line for us.