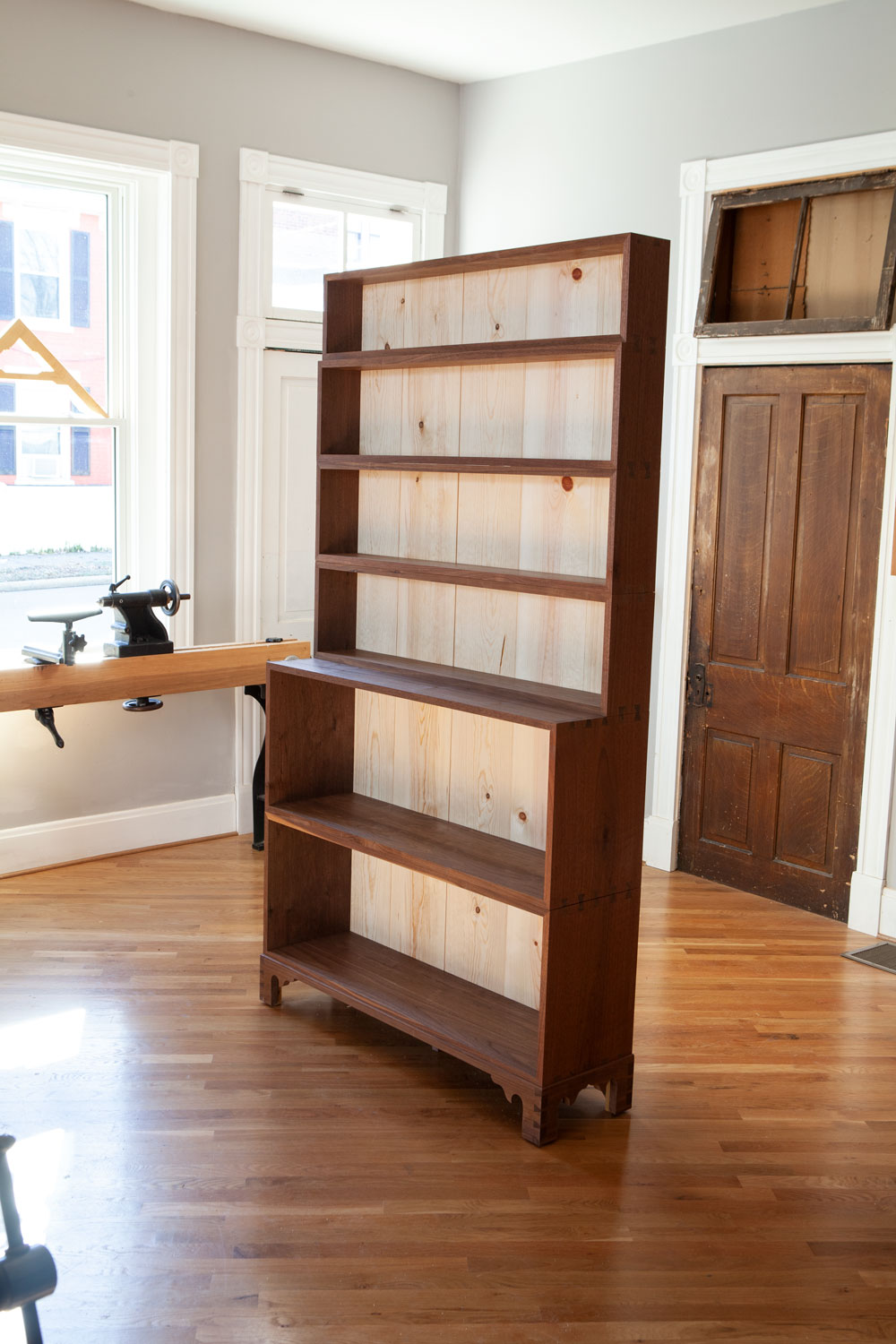
These bookcases are similar to a set I built for the June 2011 issue of Popular Woodworking Magazine, which has the complete plans with step photos and instruction. You can download a free SketchUp model of the bookcase here.
The Story Behind the Shelves
I’m allowed to quote myself, right? Here, then, is the backstory on these shelves. Read it before I issue myself a cease-and-desist letter.
I like to think of Thomas Jefferson’s personal library as America’s first “Bookmobile.”
When the British burned down the nation’s capitol in 1814, the inferno took with it many of the books owned by the government of our young nation. Lucky for us, Jefferson had a personal library of about 6,700 books – an astonishing accomplishment for the time.
And after some negotiations, Jefferson agreed to cede his entire library at Monticello to Congress for the sum of $23,950. The question was, how to transport 6,700 books from Virginia north to Washington, D.C., with horse-drawn wagons.
Lucky for us, Jefferson was a clever man. He stored his precious library in pine boxes that were designed specifically to travel. While it isn’t known if Jefferson designed the book boxes (or “book presses” as they are sometimes called), they do bear the mark of his cleverness.
For when the day came to transport this massive chunk of knowledge, the process was straightforward. Scrap paper was stuffed among the books to protect them, then a lid was nailed over the front of each unit and it was loaded onto a wagon and carted to Washington.
Jefferson’s collection of books (which continues to make headlines even today) was the foundation for our Library of Congress. His method for organizing his books (memory, reason and imagination) pushed us into a more modern classification system. Until that time it was common to organize books by height or color.
But What About the Boxes?
While a good deal is known about the books in Jefferson’s collection that he sold to Congress, far less is known about the stackable boxes that he used to store his library at Monticello. By examining the written records, officials at Monticello built six bookcases for the museum in 1959 that are a good guess at what would have housed Jefferson’s library (though he could have had as many as 20 of these units, if you do the math).
Since the day I started woodworking, I have been concerned about amassing information on the craft. For me, the written word enhances my personal experience in the shop, and it is a way to stay in touch with the craft while I am on the road, in bed or sitting on the couch.
As my library got out of hand sometime about 2005, I decided I needed to build something to store all my woodworking books. I also wanted something that would allow them to be easily transported when my wife and I leave our house after the kids are off to college, and we launch the next phase of our lives.
And so I became interested in Jefferson’s book boxes. I read the original letters that describe how the books were transported. I used the standard measurements for books of the day to help fill in the blanks when it came to designing the three different case sizes Jefferson describes in his correspondence.
Oh, and what was the joinery on these boxes? Who knows. Perhaps the boxes were nailed together, as there were as many as 150 individual book boxes to hold the nearly 6,700 books.
But I prefer to think that our third president, who was familiar with the principles of joinery, would insist on something more substantial. And so, despite the fact that no surviving examples of these book boxes exist, I built each of these units using through-dovetails with mitered shoulders at the corners. (Here’s a video showing how to do it.) The backs are shiplapped and nailed on to the carcases.
This approach to building a box is typical for the time, and I bet that my modern book boxes would easily survive a wagon journey from Monticello to Washington, D.C.
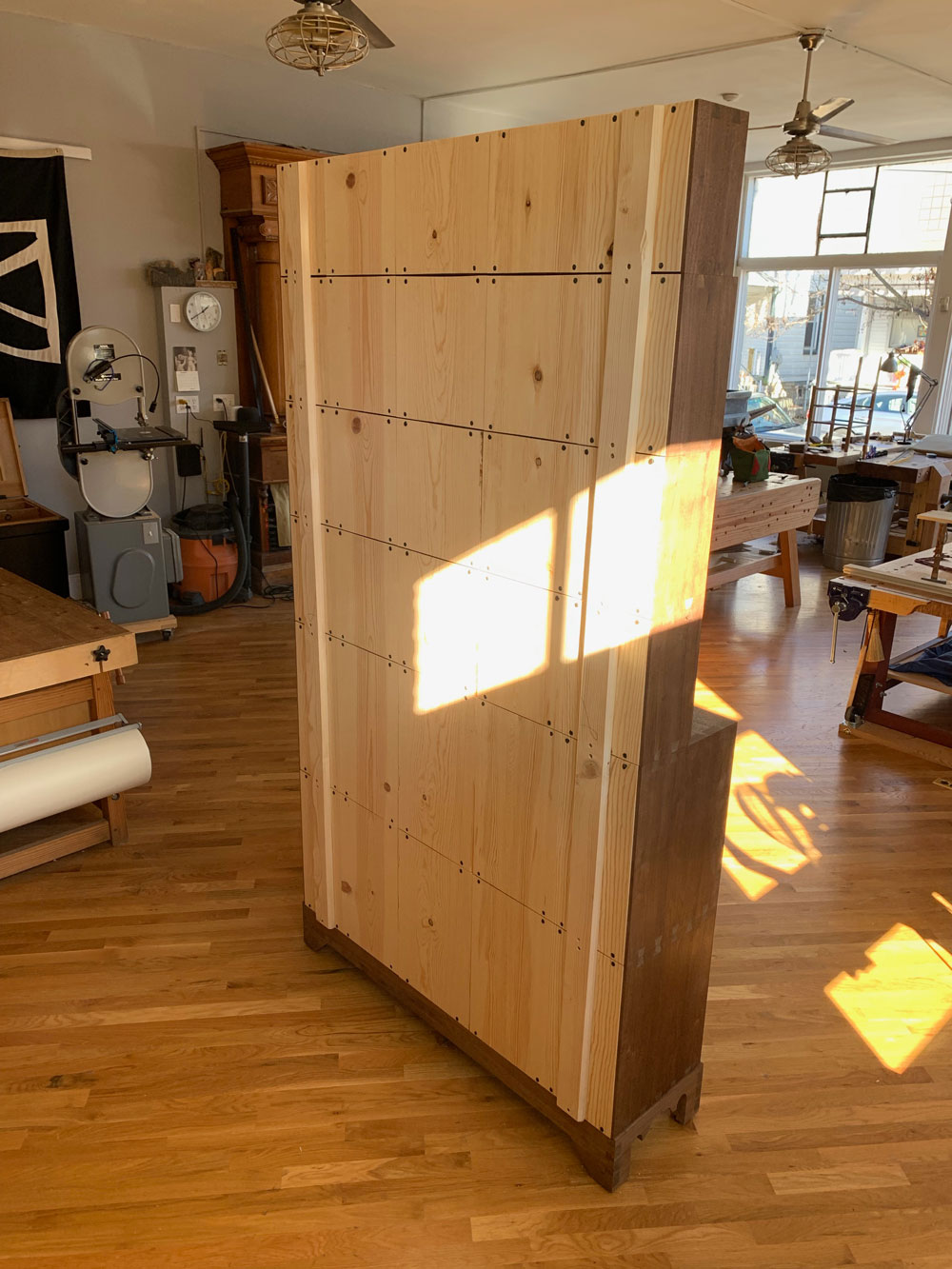
About This Set of Bookshelves
As I’ve gotten older, I’ve become more OCD (apologies to poor Brendan and Megan, who suffer my wrath when the shop’s coffee mugs are unwashed). So when faced with making a new set of these shelves, I decided to ratchet up the insanity.
At the customer’s request, all the visible boards are full-width (I hid a couple glue-ups and buried the seams below the tailboards). At my stupid brain’s request, I made the ends of the cases all one single board with the grain matched all the way up the 7’2” case. It took months (and cash) to find the right 14”-wide walnut boards.
To make it harder, I made the dovetails line up all the way up the case sides, a detail I cribbed from Jameel Abraham when he built his version of these bookcases.
Then, because that wasn’t hard enough, I made the backboards match all the way up the case. Yesterday I juggled 30 pine backboards that had to all line up or it would look like crap. Also, the way I staggered the widths of the backboards was a math equation. Let’s just agree that I made this harder than it should be.
The bookshelves are finished with shellac. The backboards are finished with two coats of super blonde shellac. The cases and plinth are finished with three coats of garnet shellac.
And now I just have to build the crate. This sucker has to go on a truck bound for Michigan at 8 a.m. Friday. This weekend, I’ll take it easy and complete a couple small projects for a customer in California. Then, on Monday, I start the most difficult and involved project so far (besides my kids). It’s a massive three-tiered campaign chest with three transit cases that store the disassembled chest components and then stack as a wardrobe.
— Christopher Schwarz
Those look incredible in Walnut.
Agreed. I love the contrast with the backboards as well.
I can’t wait to see that campaign chest, but holy crap Chris, are you really that strapped for challenges these day? Small publishing and tool making isn’t enough?
Hi Jason,
Everything I do starts with making furniture. It’s the most important part of every day and is what I look forward to every morning.
A customer approached me with the notion of building a three-tiered case (there’s one extant) with the transit cases. That’s impossible to say no to.
Also, now that I have left Popular Woodworking, furniture commissions are a *much* more significant chunk of my income.
Eminently practical set of bookshelves beautifully executed, but what about the lathe in the background? Is the bed timber? Certainly looks like something a bit different.
It’s a Conover lathe. Google it. It’s a sweetheart.
Given that typical base molding will hold the stack off the wall, I appreciate the vertical battens. Would you recommend a horizontal batten somewhere up the stack to fasten the stack to a couple of studs (with curtain climbers in mind) without pulling a back board loose with screw pressure.
This is one of my favorites. If we didn’t have a self-imposed ban on new bookcases in my household, this would be on my short list of projects.
This is *beyond*—the joinery, aesthetics and the challenges you added to the project. And then there’s the history. What a way to (almost) end the year.
A quick note. I own a copy of each book you’ve written so far. Its impossible to not be impressed with your work and your life story. I have some very special lumber hanging out in a corner of my shop. Its been there for about three years. Every time I go in there and after each day working in there, I make sure I run a hand over these pieces. They are large timbers, varying thickness, mostly 4 inches thick and average 6 to 8 inches wide. 8 feet long. They smell of smoke and a metal detector has discovered bits of shrapnel. These are special because they are teak deck boards from the WWII battleship USS North Carolina. I am an 18 year Air Force veteran. You understand why the wood is special. I won’t cut it until these boards tell me what their next life should be. I’ve thought about various bench designs.. I know I want the end result to be something people will sit on. And remember. Your suggestions would be greatly appreciated.
I take it your comment is addressed to Chris, though it appears in a reply to my comment. To make sure that Chris sees it, you should post it again as a standalone comment. Just want to make sure you have a shot at the response you’re hoping for!
Hi Drew,
I don’t know if your comments was directed at me or Nancy. If it was me, I’d probably make a workbench from the stock. If there was anything left over, I’d make a Roorkhee chair or two. Teak was a common species for those chairs and the project befits the military service of the wood.
Hope this helps.
Thanks Nancy! I am so happy these are done!
I’m so whack-a-doodle OCD each shelf would be a function of 9/16th to the one above, the bottom section being 9/16th of total height.
I also have a 3/8th, 5/8th obsession.
This is great and all, but what’s behind the old beat up door in the first picture? A broom closet? A portal to another dimension? A wall???
We uncovered that door when we pulled down a false wall in the bar. It leads to the second floor. This building was a combination bar a boarding house.
Chris, for the case in the pop wood article, that I think is the one there in the LAP store, didn’t you orient the backboards horizontally? If I’m not mistaken about that, why did you orient these vertically? Just for the long/tall look it creates?
Thanks for sharing the pics – the walnut/pine combo is amazing.
Orienting them horizontal is less work, and they look more like the crates Jefferson was creating. Orienting them vertical is a lot more work but looks better (to my eye, anyway).
I like the detail of the dovetails lining up in each section.
I agree with Nancy Hiller. There’s the history. I am so glad Chris you went with wide walnut. I wonder if your customer appreciates the wonderful walnut found in Michigan and the “link” his bookcase has to local timber. I’m from Ohio. I’ve sourced walnut from Michigan. But I digress. The history. How much of this case is handmade and how much machine? I’m not being sarcastic. I know you great work with hand tools and I am predisposed to think you did most of the work with hand tools. Good on ya. Seeing this makes me stare at the to do list which has a note forJeffersons lap desk. Again, beautful work. BTW. I am about to
finish my version of the Limbert bookcase you built a while ago. I made some hardware changes. Maybe you can critique it when I’m done?
Hi Drew,
In terms of time, I spent 10 days working on this piece (about four to six hours a day). Of those 10 days, only one was in the machine room. The rest was at the bench. All the joinery was cut by hand. All the beading. All the surface preparation was via handplanes. All the lumber was thicknessed and cut to final size by machine.
Very nice work! I guess you will not have to go crazy with the crate, it looks quite sturdy.
So did you gang-cut 12 tailboards together to get everything to line up? Sounds like a job for Roy’s extra-long dovetail saw. Great job by the way. I wasn’t sure what to think when your previous post said you were using walnut. I’ve never been a huge rain but the garnet shellac gives it a great tone. Time to rethink my opinion on it now.
Thanks for sharing and inspiring.
Mike
*huge fan* not huge rain
Months sourcing the lumber? Seriously, Chris, if this commission causes another commission, let me know. I have a (limited) supply of Missouri walnut that would suit your needs. Some of it is absolutely destined for my own purposes, but to see it put to use in something like this? By you? I’d part with a bit of it for that.
And then you could spend just four hours getting lumber (we could meet half way?) instead of four weeks.
All that aside, this is a beaut of a bookcase. I dare say Jefferson would be proud to see his ideas taken to such excellence.
Ethan
Thanks Ethan,
I will definitely ring your bell if I need more.
To be exact, I wasn’t spending all day for months looking for walnut. I was asking whenever we placed an order or I was at a yard. It took months before Alf Sharp hooked me up.
All best
I know what you meant. 😉
Just know I have some here if you need it. Also, it should likely have been a veneer log. There are no knots in these boards. 10’ long. Beautiful wood.
These ARE the boards you’re looking for.
I think they’re a fat 6/4, so maybe rip-able for bookmatch ends all the way up if you so choose to take your OCD to such extremes… (tempting I know)
Oy. My midbrain is twitching.
Walnut from Alf, he has a wonderful supply of hardwoods. Just curious, is this walnut from the gGovernors Plantation?
If it is, he did not mention it.
Can’t wait to see the crate you build for your book crates.
Adding this to the short list of (long for me) projects. Looks really fantastic!
I’ll want to see photos of that campaign system when you’re ready to share them.
I’m _still_ dithering about my own bookcases — something like these or barrister’s modules (which might derive from thiese open-faced boxes), built-in, other…
BTW, the box-per-shelf approach was not uncommon at the time. Some of the period houses here in the Boston area have similar examples. One docent pointed out that not only do modular bookcases make organized moves easier, they also (if not battened together) allow efficiently rescuing books from a house fire — which, given availability and cost of books at the time, strikes me as a valid consideration.
Dear esteemed blog authors (and commenters), I’m looking for insight into a topic semi-related to woodworking: small business insurance. Are there any insurance firms that specialize in coverage for a small woodworking business? I haven’t found a relevant blog post for my question, so I’m posting it here.
I would like to begin making a few things to sell (not a full time gig) and see where it leads. I’ve done a few pieces of furniture, and built-in cabinets for others in the past. The fine print in my homeowner policiy says it will not cover my shop if I’ve been using it for business purposes. The insurance options are varied, but the premiums I’ve been quoted are more than my home policy. Some want proof of a dust collection system, some want a regular inventory of the wood stock, and others want to know what chemicals I might use. Any help would be appreciated.
Very cool. In the summer of 2017 I was able to spend two months in the North East of the US for work. I also had a two week vacation and went from Main (Lie Nielsen) through MA (Shaker place with Round Barn) and to Washington DC. There were lots of highlights on that trip. I was able to spend a good deal of time in the library of congress, got a library card, and was able to spend a fair bit of time looking at Franklin’s books. Awesome memories.
I visited Monticello this summer with my wife and that is the first time I have seen the Jefferson bookcases, although I heard of them while in Philadelphia two years ago. Just this morning I was thinking I’d love to make some of those cases! Thanks for posting this.