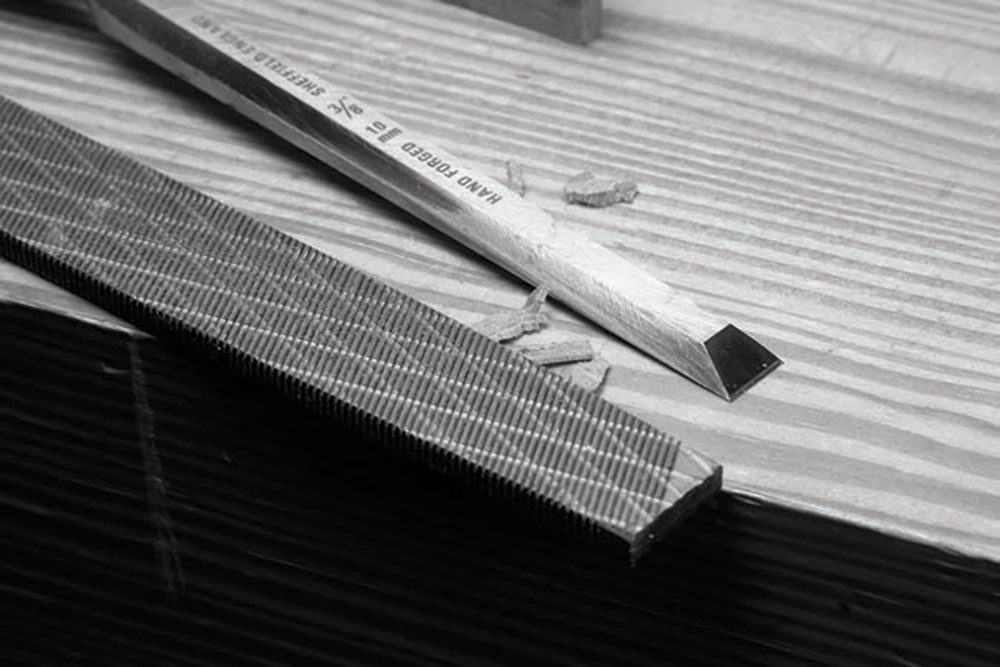
This is an excerpt of “The Joiner and Cabinet Maker” by Anon, Christopher Schwarz and Joel Moskowitz.
After years of dovetailing, I noticed that two of my chisels were seeing almost all the action: the 1/4″-wide and a 3/4″-wide tools. I use the narrow one for removing waste between the tails and the larger one for removing waste between pins.
If you are like Thomas and have limited funds for high-quality tools, these two chisels would be my first purchases.
But what about the so-called dedicated dovetail chisels you see in catalogs? As a beginning dovetailer, I had a crappy set of plastic-handled chisels, a newspaperman’s salary and a copy of the Japan Woodworker catalog. All three things conspired to make me miserable.
I wanted to cut dovetails with bold angles, but my crappy chisels had side bevels that were as big as Cheddar Mountain at Bonanza. So every time I went to clean out the waste between my tails, the side bevels would wrench a bite out of my tails.
I wanted to buy a sweet dovetail chisel from Japan Woodworker that didn’t have side bevels. That would allow me to sneak into the corners with ease. But I had a newspaperman’s salary, which made me want to sell drugs to the local Junior Leaguers.
Luckily, I met some clever people in my travels. Dovetailing demon Rob Cosman showed me his hot-rodded chisel on which he ground the side bevels down to nothing (and he shaped the chisel with a fishtail sweep). Woodworker Lonnie Bird showed me how he lopped the end off a plastic-handled chisel and reshaped it so that it was easy to strike.
And what did I bring to the equation? I figured out chisel geometry (like most woodworkers eventually do), which allowed me to make the tool take a beating like a rented mule.
Here’s What You Do
So let’s say you have a nice four-figure salary and can spring for one of the nice $1 chisels at the flea market. Here’s how you can make it into a sweet worker in about 30 minutes.
Step one: File the side bevels. The side flats below the side bevels on cheap chisels are too big for dovetail work. You need to file the bevels so that there is absolutely zero flat area on the long sides of your chisel’s blade. When you are done, the chisel’s blade should look like a decapitated pyramid in cross-section.
You can do this with a grinder, a stationery belt sander or a disk sander. Or you can take the cheap (and safer) route and use a Multicut file. This style of file, which is generally used for shaping metal, can dress the side bevels of a typical chisel in about 10 minutes.
Secure the chisel in a vise and work the side bevels with the file. Hold the file with two hands: one on the tang and one at the tip. Cut only on the push stroke. And stroke the file so your hand is never (ever) right over the cutting edge of the chisel. One slip and you are (blood-soaked) toast.
After filing the side bevels so they extend to the flat face of the chisel, clean up your work with light strokes of the Multicut file. Then clean up your work (if you like) with a fine file or sandpaper.
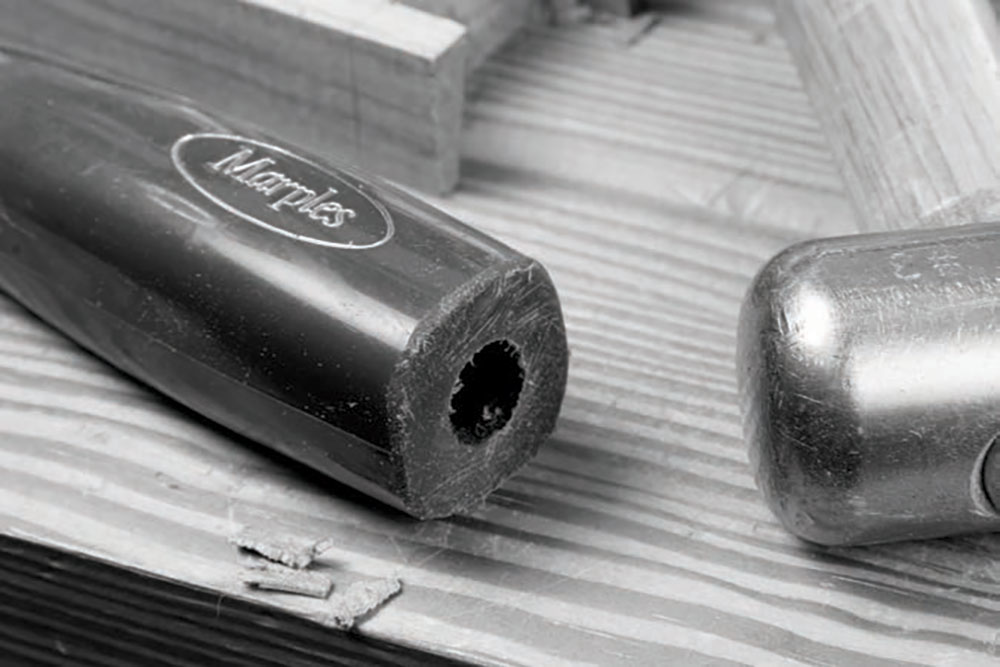
Step two: Adjust the handle. If the striking end of the handle is rounded and plastic, it is likely too top-heavy to wield comfortably. The chisel should feel like a pencil, and the rounded end is probably difficult to strike without your mallet glancing off the end oddly.
Take a hacksaw and cut off the top 3/4″ of the handle. Try the balance. Still feel top-heavy? Lop off a bit more. Make sure you leave enough handle so you can grasp the handle in your hand to strike it without striking yourself.
Once you get the balance right, file the top of the handle flat and dress the sharp corners to remove any odd burrs.
Step three: Sharpen the edge correctly. Grind the primary bevel of the tool at 25°. Then grind a 35° secondary bevel on the tip. It will be a tiny secondary bevel, which is a good thing. The advantage of this steep bevel is that your tool will be durable through a lot of chopping. A steeper honing angle increases edge life. And the steep angle isn’t a detriment to chopping out waste – it scarcely feels different than a 25° chisel.
Then you are off to the races.
— Meghan B.
I did nearly the same thing about twenty years ago. I was working late shifts so I could do the mods on the boss’s dime. LOL I also ground one to a point which I still use to this day to clean up inside corners. Haven’t broken the tip off yet.
I did a similar thing, here in Sweden you can buy old EA Berg chisels on Ebay quite cheaply. I took a 1inch chisel to a friendly knife/skate/plane iron sharpener here in Göteborg and they made a lovely fish tail chisel which works like a treat. I also took two 1/2inch chisels to them and got the blades ground at about 40 degrees (instead of the usual 90 degrees) one right & the other left hand. These are also great for getting into tight corners.
“stationery”? okay, fine, call me a wiener.
But, by the way, this is an awesome post which makes me want to buy the book. So, thanks!
Speaking of slipping whilst filing edged woodworking tools… a few months ago I bought my first Hock blade to replace the Titanic one from a no-name #5 clone. I didn’t have time to camber it, but I wanted to try it out, so I chucked it edge up in a machinist’s vise to take the corners off with a needle file (which is the wrong thing to do). Yep, third stroke I slipped, laid the tip of my thumb open to the bone.
Fortunately, I had paper towels and duct tape so I could keep right on working.
DAMN that man knows how to make a sharp blade!
Shinogi nomi are not actually dovetail chisels, they’re made for cleaning up the ends of mortises.
I’m not sure who started advertising them as such, and they do function well as dovetail chisels but I thought I’d make mention.