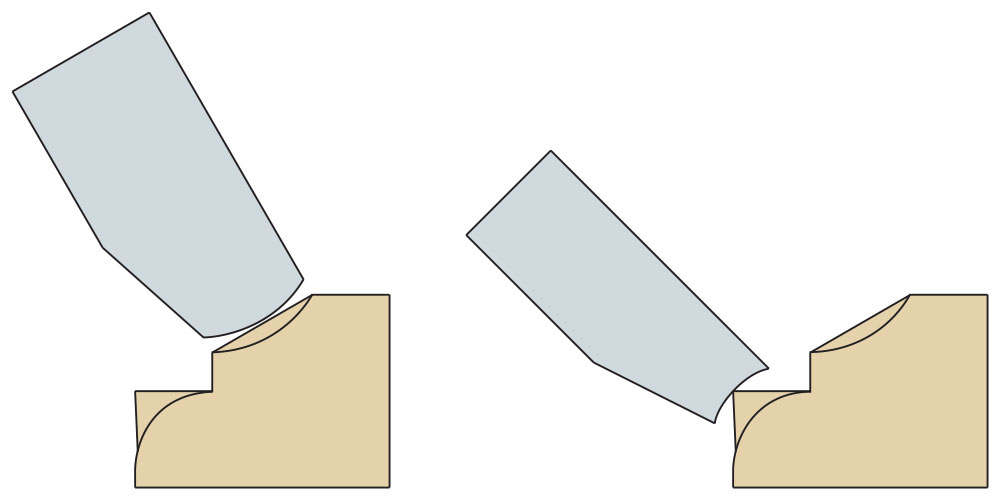
This is an excerpt from “Mouldings in Practice” by Matthew Sheldon Bickford.
I have spoken to scores of people regarding the methods of making profiles with hollows and rounds that I have covered thus far. While most new users find the techniques extremely simple and thorough, some more experienced woodworkers find it too calculated. In many ways I agree with this sentiment, particularly as you improve in your skills. In this chapter I will address a few of the techniques that many other woodworkers employ.
Many users much more accomplished than myself start the hollow on the single arris of a single rabbet rather than on the dual arrises of a chamfer. Similarly, for concave curves they start a round on a chamfer rather than the arrises defining a rabbet.
With these techniques, it is recommended that the user start the profile toward the end of the board, near where a pass with the plane is generally ended, and work his way back in abbreviated steps. The first pass with the round, using your fingers as a fence (I use my fingers on both sides here), will start the profile in the last 6″ of the board. With the second pass, back the plane up another 6″ and take another pass all the way to the end of the board. Proceeding in this way will create a profile that is ramped toward the end of the piece. To correct this, once the plane is tracking properly the user should begin to take passes abbreviated in the opposite direction – feathering the plane off the profile before the end – thereby evening the profile across its length. The toe of the plane will ultimately guide the cutting edge and the heel.
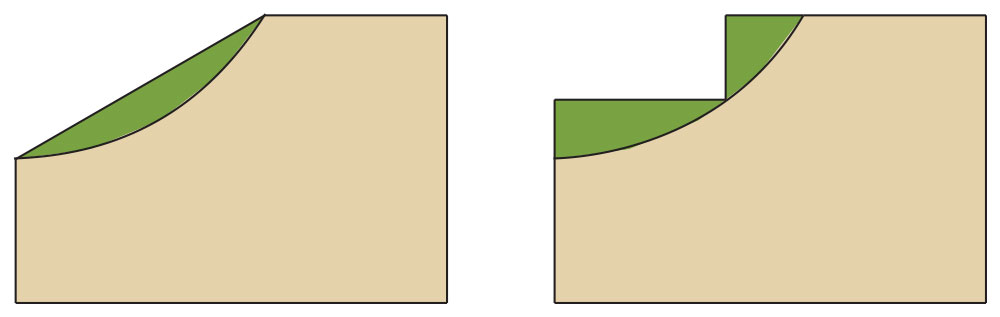
The advantage of working in this manner, from end to beginning, is that the plane creates its own chutes in which to fall. The first pass may be imperfect. The second pass, using the plane’s length and the chute that was started with the previous pass, will be slightly more accurate and uniform, especially toward the end. With each subsequent pass the profile will develop further and more uniformly. Accuracy here depends upon skill with steering the hollow and round, not on a square rabbet.
The advantage of this method in using a round is that there is less stock to remove in profiles of 60° as shown in Fig. 13-2.
There is, of course, much more stock to remove with a hollow using this method as shown in Fig. 13-3. There is, I guess, also one less step.
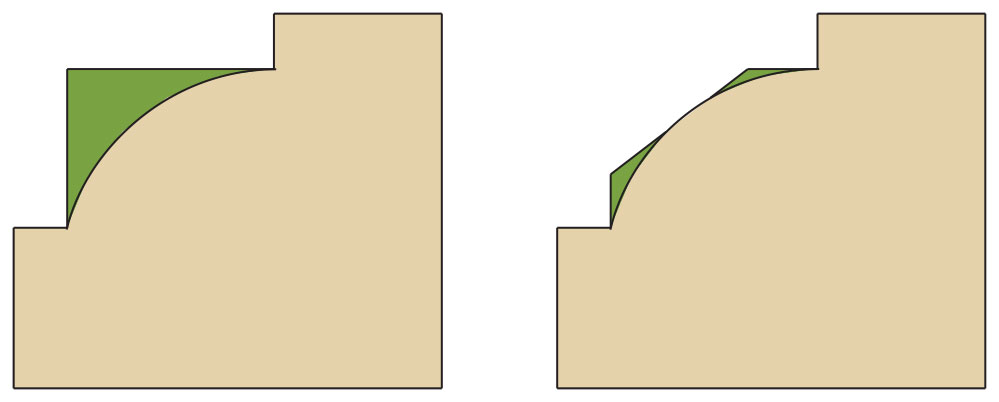
The disadvantage of this traditional method of using hollows and rounds is in its inaccuracy for beginners. It is much easier for the new moulding plane user to achieve consistency when the plane has two points upon which to ride. However, I have introduced this technique here because there are times in which it is useful, even necessary.
For example, I use this method exclusively when working with No. 2 planes. You will notice that I never illustrate knocking the corners off the square facet before creating a bead, as shown in Fig. 13-4. Working a rabbet plane into that tight area is dangerous in regard to the surrounding profiles, especially given that the adjoining surfaces are complete at that stage.
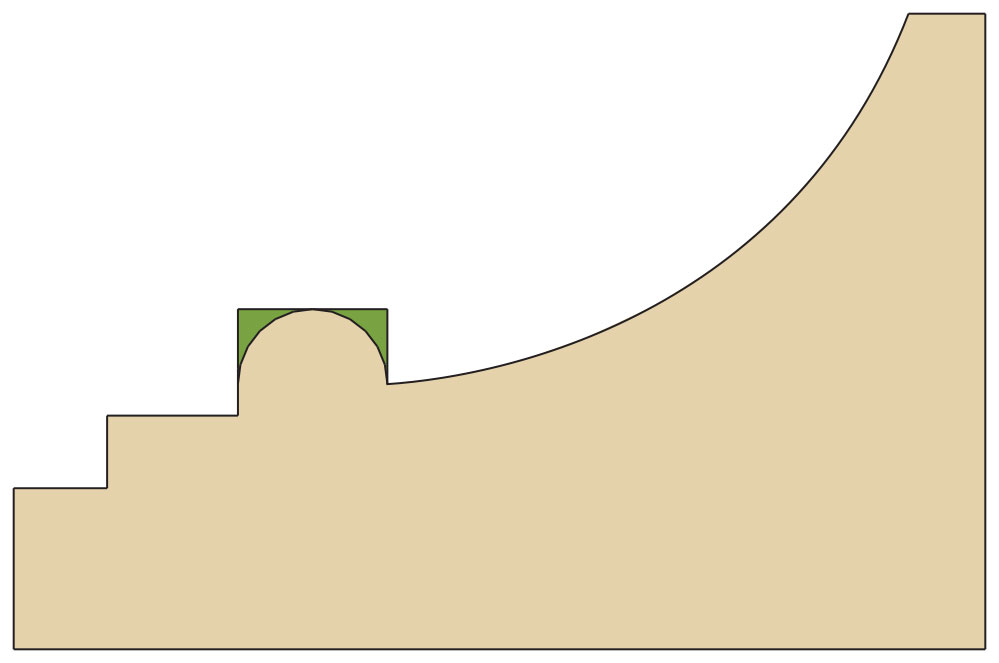
The rabbet necessary to guide a No. 2 round is absurdly small; the two points upon which the plane sits are so close that they are somewhat irrelevant. I create a chamfer here and use the above method as shown in Fig. 13-5.
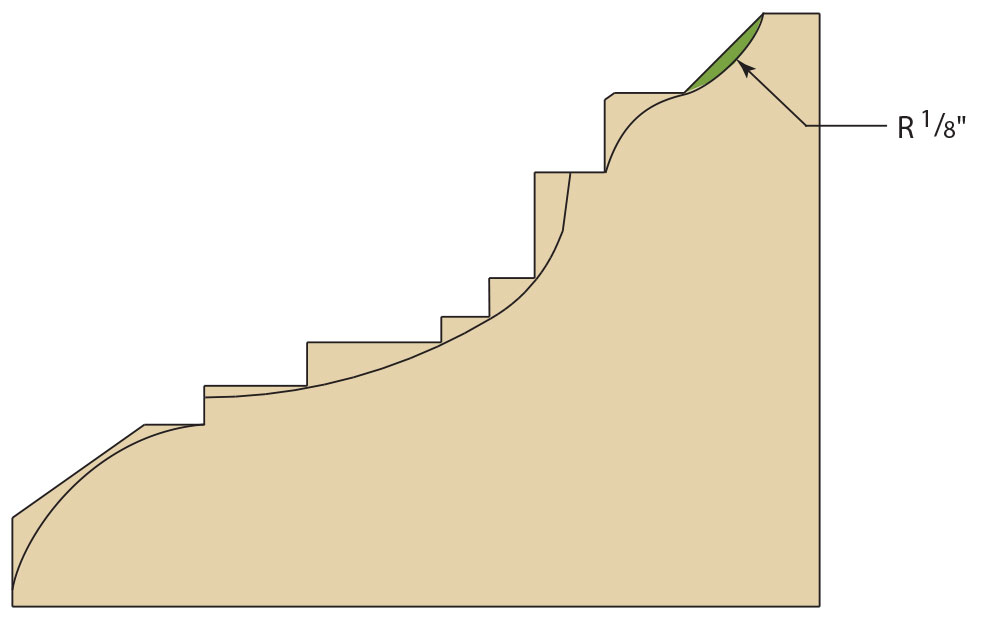
I also use these methods at times when working with larger planes, but their use is much more sporadic. Again, the further one progresses in his skills, the more individual preferences develop. You may try this method and prefer it – there is no question that many use it quite successfully. I will not argue with success.
— MB
Having recently acquired a #45 and #55 along with a handful of wooden hollows and rounds (from a $10 bin) I find this to be terribly interesting. The stepwise approach of using easily sharpened rabbeting planes for roughing out material reminds me of high school math fundamentals prior to introducing integral Calculus namely Reimann sums. http://mathworld.wolfram.com/RiemannSum.html
This is quite freeing as compared with the constraints of router bits, stacking of shaper cutters and bearings or grinding corrugated knives to fit into the moulding head. Perhaps a 5 HP tilting arbor shaper that can support a 1 1/4″ diameter spindle can wait.
I am fearful as to the amount of time that will be spent sharpening (rather honing) complicated cutter profiles. The approach described above should help to reduce that. I wonder about how much the powered upside down router or the table saw dado stack will be performing the rough out in the basement shop after the novelty of hand plane plowing wears off.