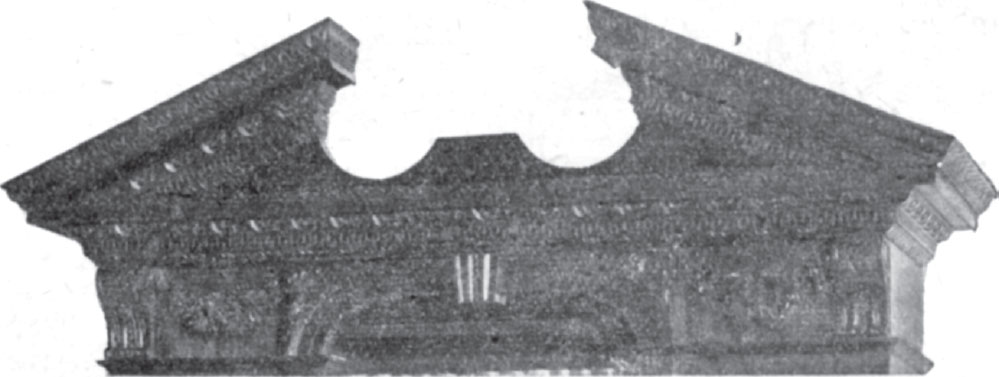
This is an excerpt from “The Woodworker: The Charles H. Hayward Years: Volume II” published by Lost Art Press.
Of course, you realize that the feature that makes this work awkward is the fact that the moulding which forms the pediment slopes upwards towards the middle. It necessitates a different section from that at the sides, and introduces an interesting problem in mitreing. The pediments of doorways, windows, and mantelpieces often had this feature.
A little reflection will show you that the moulding which runs around the side of the cabinet, the return mould as it is called, must necessarily be different in section from the sloping mould at the front (raking mould, to give it its technical title). Apart from anything else, the top surface cannot be square but must obviously slope to agree with the raking mould, and its top square member must be vertical. The whole contour, however, is quite different because it would otherwise be impossible to make the members meet on a true mitre line. These points are at once clear from a glance at Fig. 2 (A and B).
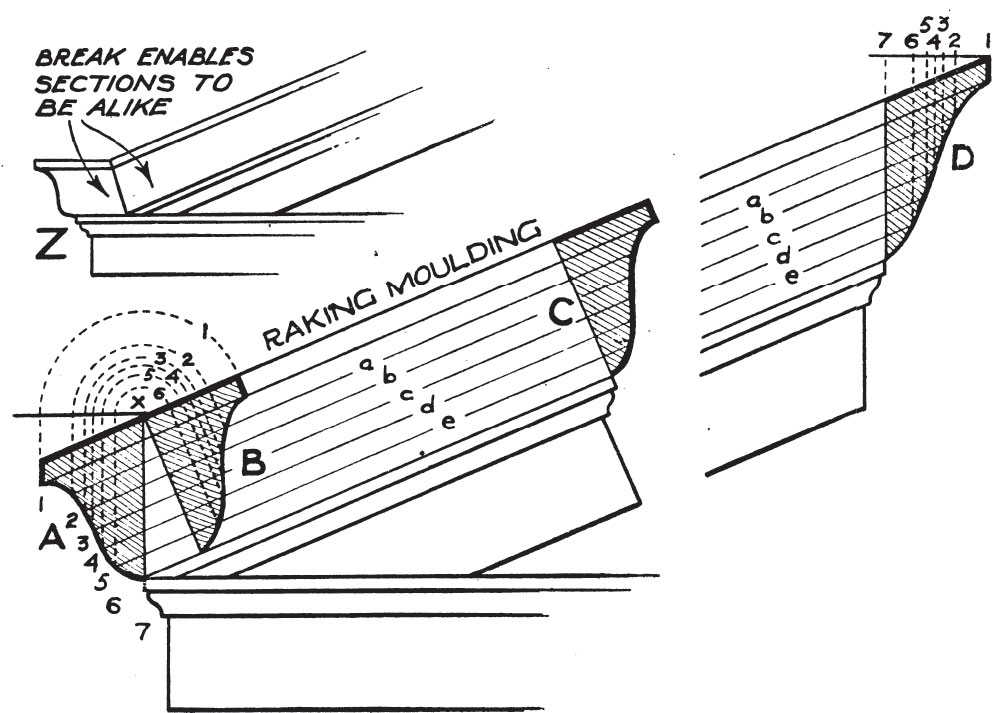
Before proceeding farther, it will be as well to explain that so far as the centres of these broken pediments* are concerned there are two distinct methods that can be employed. In the one the same section is used for the return as the raking mould, so that the square members of the moulding which would normally be vertical lean over at right angles with the raking mould. The pediment in Fig. 1 is of this kind; also that shown at C in Fig. 2. In the second method the section of the return is different, and is arranged so that all normally vertical members remain vertical as at D, Fig. 2. This latter method naturally involves considerably more work but has a better appearance. Both methods were used in old woodwork.
To return to the outer corners, the first step is to fix the contour of the return moulding since this is the one which is seen the more when the cabinet is viewed from the front. Draw in this as shown at A, Fig. 2, and along the length of the raking mould draw in any convenient number of parallel lines, a, b, c, d, e. Where these cross the line of the moulding erect the perpendicular lines 1-7. From the point x draw a horizontal line. With centre x draw in the series of semicircles to strike the top line of the raking moulding, and then continue them right across the latter in straight lines at right angles with it. The points at which they cut the lines a-e are points marking the correct section of the raking mould, and it is only necessary to sketch in a curve which will join them (see B). The same principle is followed in marking the centre return D, but, instead of drawing the semi-circles, the vertical lines 1-7 are drawn in the same spacing as at A (the reverse way round, of course).
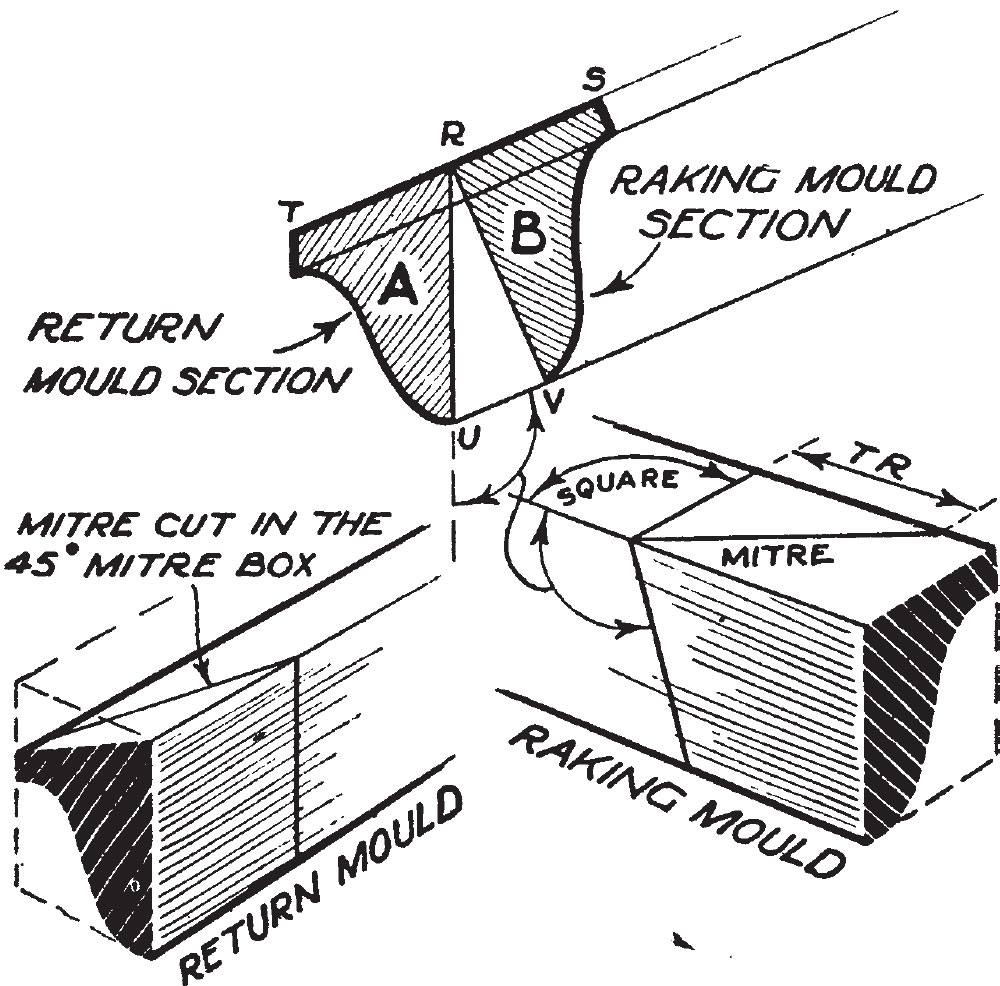
Having worked the sections the problem arises of finding and cutting the mitre. This is explained in Fig. 3. The return mould presents no difficulty, and it is usual to cut and fit this first. It is just cut in the mitre box using the 45 deg. cut. Note that the back of the moulding is kept flat up against the side of the mitre box, the sloping top edge being ignored. Now for the raking mould. Square a line across the top edge far enough from the end to allow for the mitre, and from it mark the distance T R along the outer edge. This T R distance, of course, is the width of the return moulding measured square across the sloping top edge. This enables the top mitre line to be drawn in. The depth line is naturally vertical when the raking mould is in position. You can therefore set the adjustable bevel to the angle indicated at U and mark the moulding accordingly.
Worked and cut in this way the mouldings should fit perfectly. We may mention, however, that you can get out of the trouble of having different sections by allowing a break in the raking mould as at Z, Fig. 2. The mitre at the break runs across the width, and the one at the corner across the thickness.
The method of ascertaining the sections of mouldings should be used for all large, important work. If, however, you have a simple job to do requiring just one small length you can eliminate the setting out altogether. First work the return mould and cut its mitre. As already mentioned this is at 45 deg. and is cut straight down square. Fix it in position temporarily and prepare a piece of stuff for the raking mould. Its thickness will be the same as that of the return mould, but it will be rather narrower. Mark out and cut the mitre as described in Fig. 3. If preferred the adjustable bevel can be used entirely as in Fig. 4. The tool is placed so that it lines up with the slope of the raking mould, and the blade adjusted to line up with the mitre (see A). This gives the top marking.
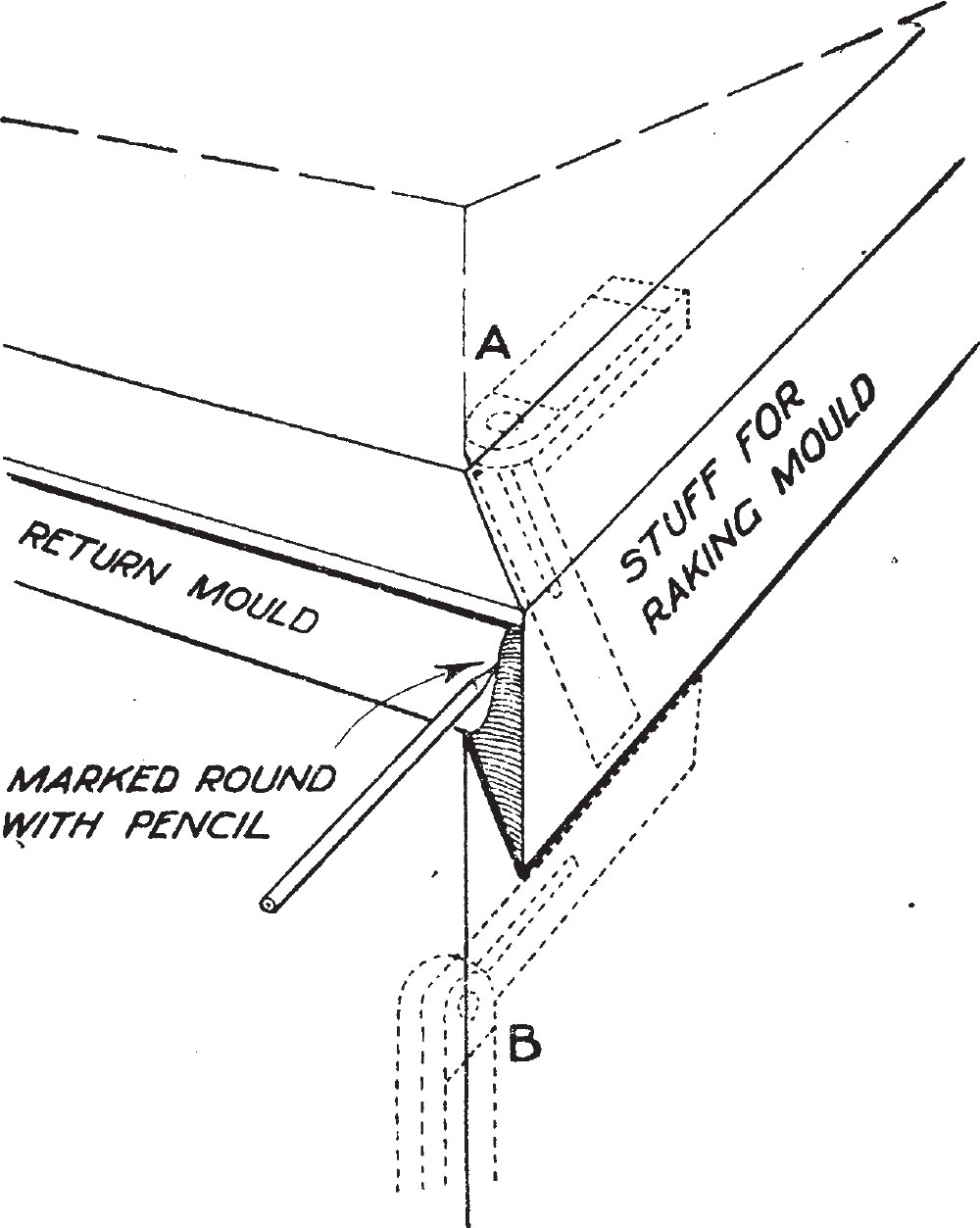
Now set the bevel to the slope of the raking mould as at B. Mark the back of the mould and cut the mitre. Offer it up in position and with a pencil draw a line around the profile of the return mould as in Fig. 4. Work the moulding to the section thus produced.
— MB
*A broken pediment is one in which the raking moulds, instead of meeting at the centre, are stopped short and are returned as in Fig. 1.
I have been studding Hayward for some time. I am curious if anyone has book no 4 and if so are they getting allot out of it? The Workbench Design Book by Schwarz is such a great book that when I look at the fourth book and see the hideous benches in the excerpt I just can’t! I hate having incomplete collections and its messing with my OCD.
I’ve just bought my own copy of Vols III and IV so have not had time to read them thoroughly. However: articles on benches cover about 20 pages, then it moves on to bench fittings, tool cabinets and bench fixtures; even then, this is still the minority of Vol IV. What made my eyes pop was that this was followed by a whole lot of household furniture articles – the illustrations are mouthwatering. So if you’re fighting shy because of the workbench articles, that’s only a small part of the 300+ pages and the second half is the bit I think I’ll get the most out of.
Thank You.
In which volume is this information?
This makes my brain hurt.
The are isn’t dead it has just changed. If we were to produce this piece today the profiles, cabinet parts and mitres would all be cut on the CNC. We have produced pieces in similar complexity including curved miters for bolection moulding using cnc technology and highly skilled Craftsman. The largest hurdle is that cost and demand do not line up. Depending on design I would estimate the bid price for this piece to be in the 8k -12k range.
Meanwhile, that hand-tools guy picks up his hollow and round planes and gets it done in a few hours… 😉
Add to previous comment:
I would also estimate production time (again design pending) at 90 – 120 hours.
That’s kind of a lot of time for 6 pieces of moulding.
Apparently I was looking at this from a different perspective which is a complete late 1700 Victorian armoire with hand carvings, custom mouldings, full cabinet construction, with a shop finish.
Por que isso é fundamental? Comprar, assinar,
aprender algo).