
In 1808 Thomas Jefferson wanted a comfortable chair to rest his aging body. He ordered three Campeachy chairs from New Orleans. The chairs were sent by the most efficient and speedy means of the day: by ship. Unfortunately, the ship was lost at sea. Years later another order was placed, the ship arrived in Richmond, Virginia and Jefferson had his Campeachy chairs (or as we know them Campeche chairs).
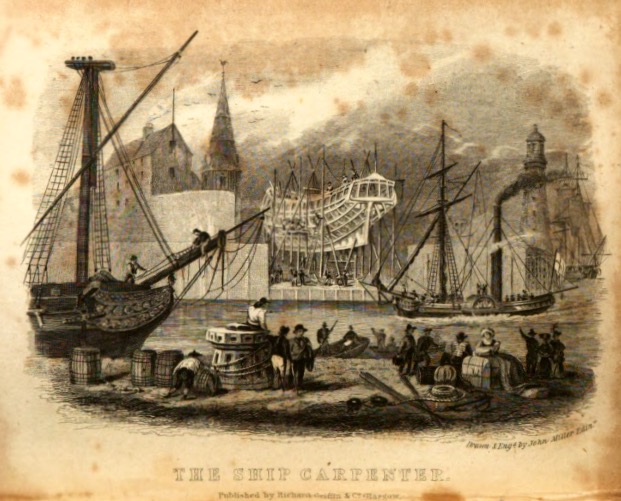
From the earliest days of the American colonies carpenters, sawyers, shipwrights and other craftsmen were recruited from Britain and other parts of Europe to build everything for the new settlements. Ships of all sizes were needed to move goods and passengers along the coastline, along rivers and bays. Major coastal and river cities, smaller settlements and plantations all had shipyards to build and repair all manner of boats.
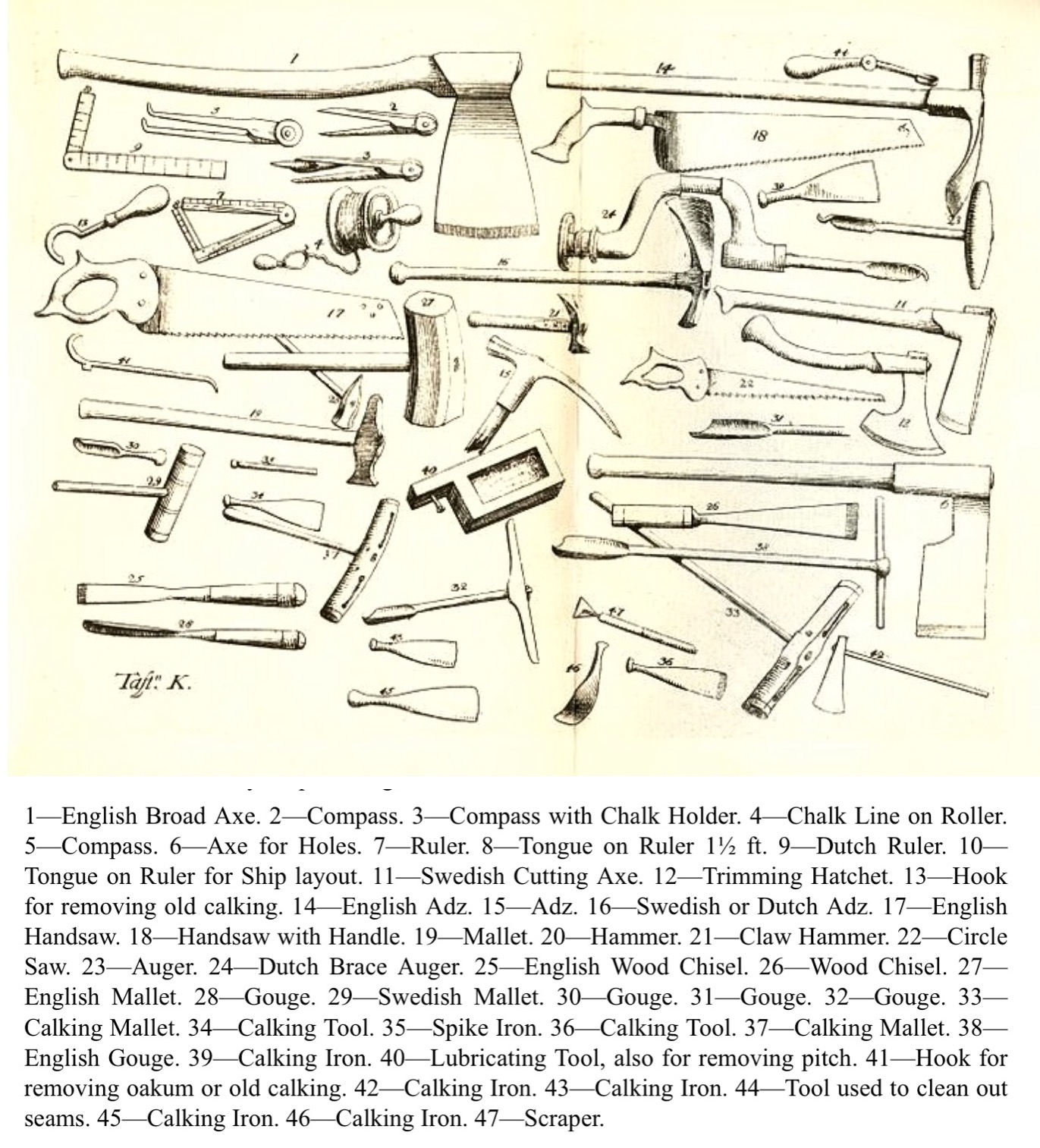
All the shipbuilding tools should be familiar to the modern shipwright or any woodworker. It is thought that when Ake Ralamb started out publishing his scientific encyclopedia he was not saying these tools are new, rather these are the tools that have been traditionally used for shipbuilding.
Masts were generally made at a separate site from the shipyard and required another set of tools. The complexity of the construction depended on whether or not the mast was made using a single stick.
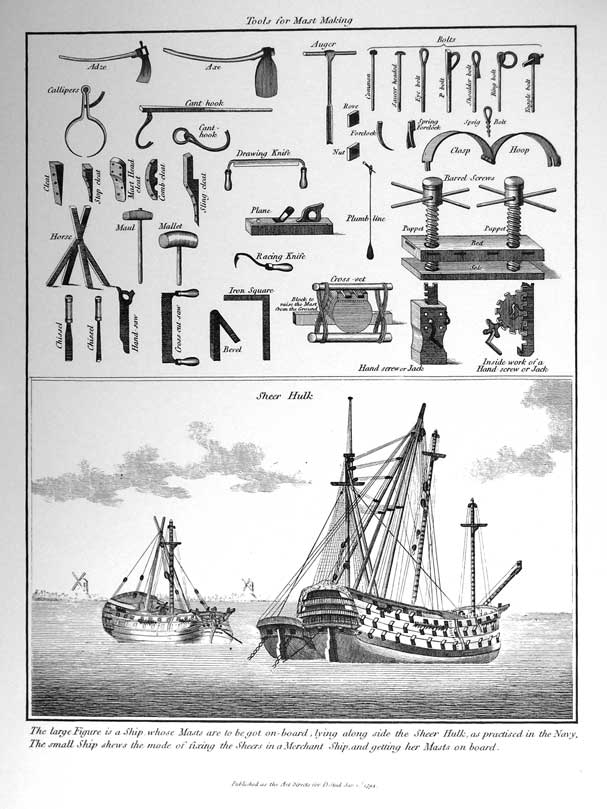
Here is an excerpt on making a single stick mast from ‘Masting, Mast-making and Rigging of Ships- Ninth Edition’ by Robert Kipping, 1864:
If you find that hard to follow, Charles Desmond’s ‘Wooden Ship-Building’ from 1919 has a simplified description of making a spar by essentially the same method:
“The spar is first worked to shape by hewing in the manner shown [1.]
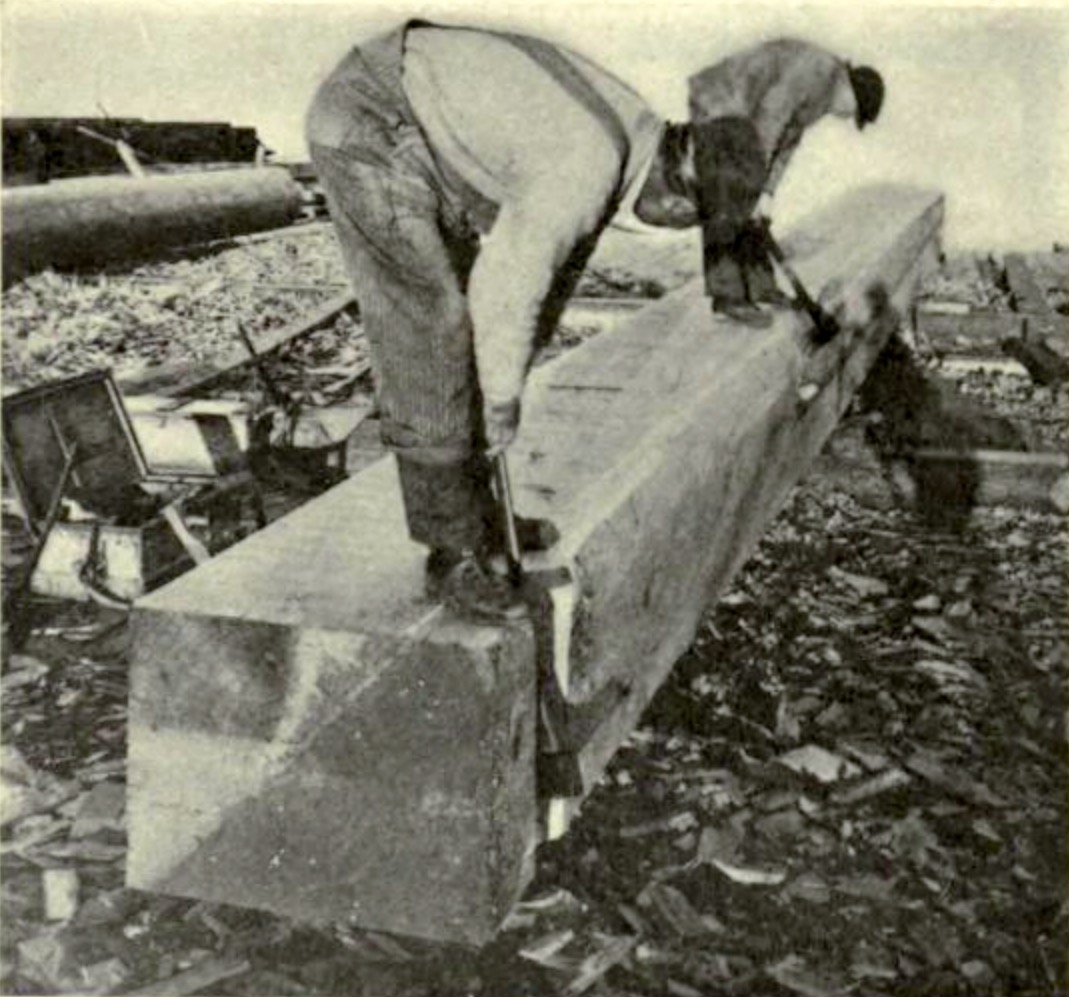
…and when this has been done, and the stick is fair, the sparmaker dubs off the square corners and makes portion of the stick that has to be rounded eight sided. Next he makes it sixteen sided, by again taking off the corners, and after this has been done the stick is rounded and made perfectly smooth [2.]
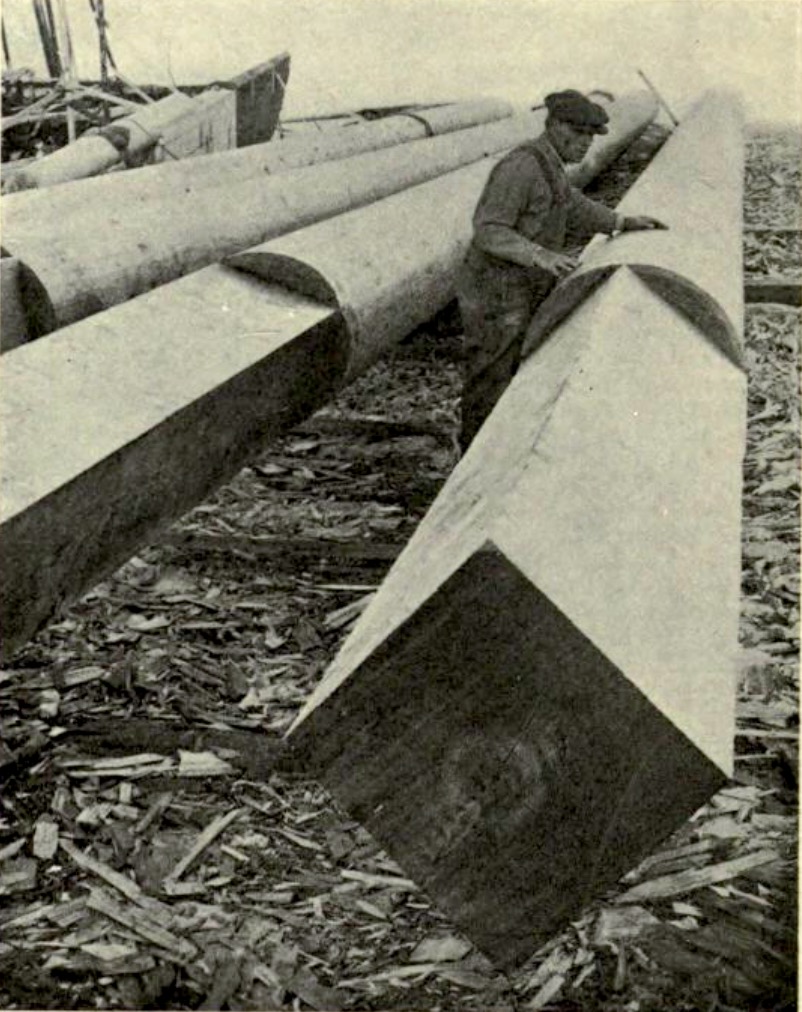
Of course as a spar has a rounded taper from butt to point of greatest diameter, and from this point to top, it is necessary that sparmaker “lay on” longitudinal taper lines very accurately and work them.”
If the tree procured for a mast was examined and found not sound, or as the supply of massive mast trees was exhausted, another method was used to make masts. As Robert Kipping phrased it in his treatise, “They [the masts] are therefore composed of several pieces united into one body…seems to fulfill the old adage of “a bundle of sticks that could not be broken when so united.”
The Library of Congress has a short article on the history of the old (and very long) Mast House at the Norfolk Navy Yard. The description of composite mast fabrication using coaks (scarf joints) begins on page 5 and you can find it here.
When our waterfronts were crowded with sailing ships and the wooden masts and yards swayed as though blown by the wind the oft-used “a forest of masts” was a fitting description. Although there aren’t as many wooden ships on the water they are still made, and with tools and methods that haven’t changed much in the last few centuries.
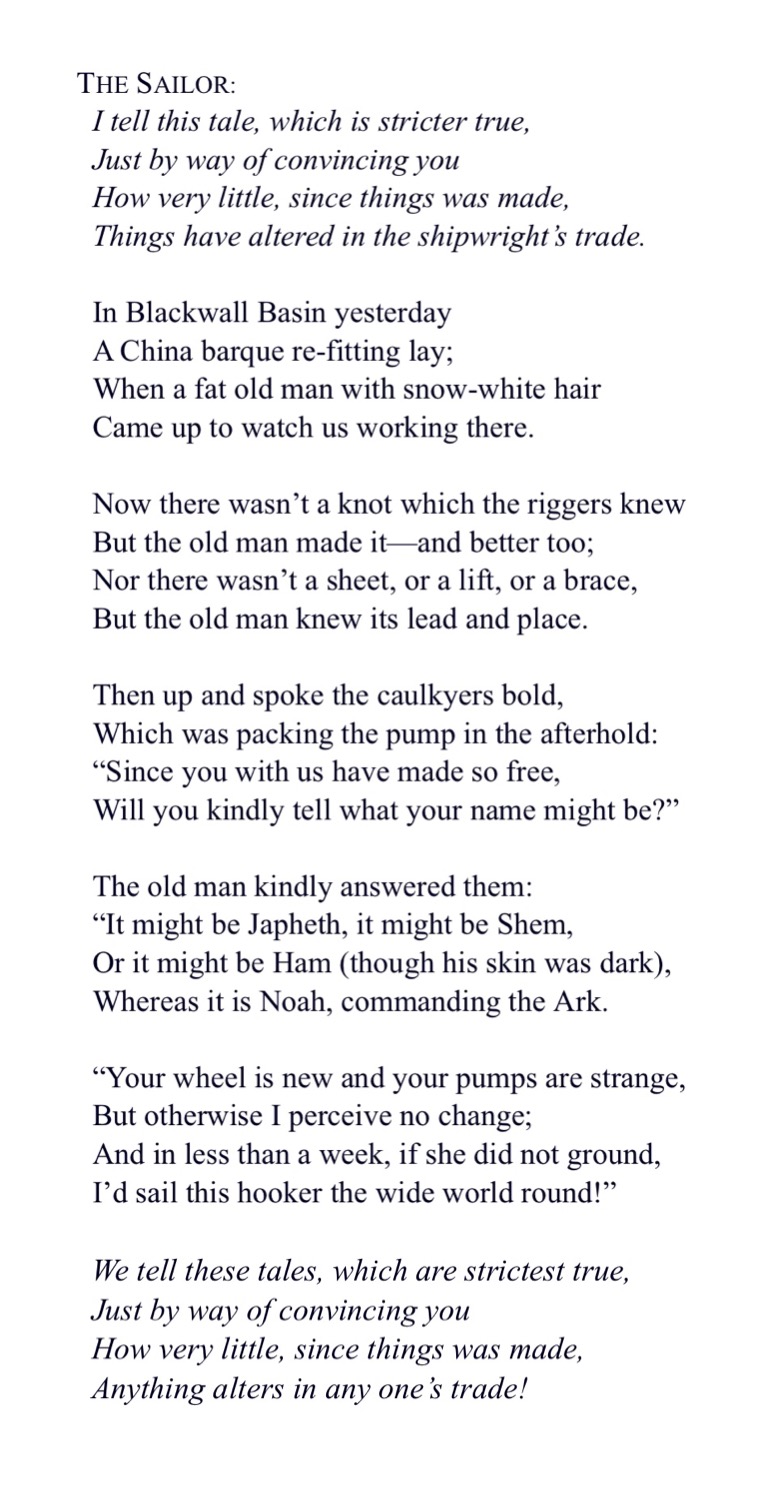
–Suzanne Ellison
It looks like they square the timbers before they shape them into masts. Why not just leave them in the round from the start?
I’m taking a educated guess on this but just leaving it round you would never find fatale flaws. Squaring it up you would find twists and other flaws that would fail in strong winds.
My guess would be that they needed to square it up to layout the longitudinal taper lines accurately. When rounding they went to eight sides and then to sixteen. They couldn’t just cut chamfers because because of the rounded tapering done on the spar: “(the) spar has a rounded taper from butt to point of greatest diameter, and from this point to top, it is necessary that sparmaker “lay on” longitudinal taper lines very accurately and work them.”
If you want to see how they “might” have accomplished this layout technique check out the link below. It is an episode of “Rough Cut” with Steve Brown helping to build a four post bed. The posts are tapered octagons and the layout is done with dividers and geometry. Steve’s explanation starts at 9:34. It gives you the idea of how they might have done laying out the longitudinal taper lines. The post is basically shaped like the spar.
http://tommymac.us/2014/09/episode-0503-pencil-post-bed-with-steve-brown/
I might be way off base, but it makes sense to me as a possible reason.
If I may…having helped with a few and study a number of old ones…and similar “wood members.”
When a Tree is cut down we have a log…that log is then turned into a “Bolt” and that bolt is then “canted” or turned into a Cant. Not a lot of info out there on this, but then again much of traditional craft really isn’t written down, and lost to the ages as mush was only orally passed down…
Cants typically have most of the sapwood removed, and as suggested already, also reveals flaws in a piece of timber that would then further offer the best use for it…or not the best as well.
Modalities of making Spar, Yard, Mast etc…vary in each seafaring culture be they European, Middle Eastern or Asian in orgin. Some (Asian) layout systems can work a bolt completely in the round to finish product without the need to ever render it square or rectangular, as they are perhaps the paramount culture in “lining methods” as it comes to layout systems of wooden members.
On the topic of “coaks” as I understand them have cut similar or employ such…are not scarfs…in and of themselves. Some scarfs may contain a “coaking” yet they are but a component of such.
Coaking is similar too (if not almost the same in many ways) to a the system of “toggling” as related to such things as found in “key beams” and other traditionally “built up” or laminated timber….such as a traditional Mast when long enough trees of quality cannot be found or sourced. There are many forms of these and a fascinating jointing modalit that is applicable in both furniture, as well as timber framing, shipwrighting and the related…
A challenge with many Coaking methods is shearing with the grain…unless…the coaking is not formed from the wood itself but a separate “key” or “toggle” with a more germane grain pattern of resistance…
(form:http://www.hnsa.org/resources/manuals-documents/age-of-sail/the-elements-and-practice-of-rigging-and-seamanship/page-1/):
“…COAKS are oblong ridges left on the surface of different pieces of made-masts by cutting away the wood round them; the intermediate part is called the plain.
COAKING is uniting two or more pieces together, in the middle, by small tabular pieces, formed from the solid of one piece and sunk exactly the same in the other, the butts of which prevent the pieces drawing asunder lengthways.
There are different methods of coaking, as follow. Coak and plain is when a coak is formed, and a plain surface follows between that and the next. Running coaks are coaks continued the whole length along the middle, but answer the above purpose, as the butts of each coak come one third their breadth within and without each other alternately.
Chain-coaks are formed one at the end of the other on the opposite sides of the middle-line. See Tabling.”
Another image source:
http://www.all-model.com/pages/clip2/img00/p28.html