This is an excerpt from “With All the Precision Possible” by André-Jacob Roubo, translation by Donald C. Williams, Michele Pietryka-Pagán & Philippe Lafargue. The following text is part of an essay about Roubo’s workbenches written by Christopher Schwarz.
One of the biggest obstacles, downsides and joys to a French bench is the massive slabs used to construct it. Finding wood that is big enough to use without laminating thinner pieces together can be difficult. Laminating thin pieces together to make the thick pieces required for the top and legs is a lot of work without the help of machines.
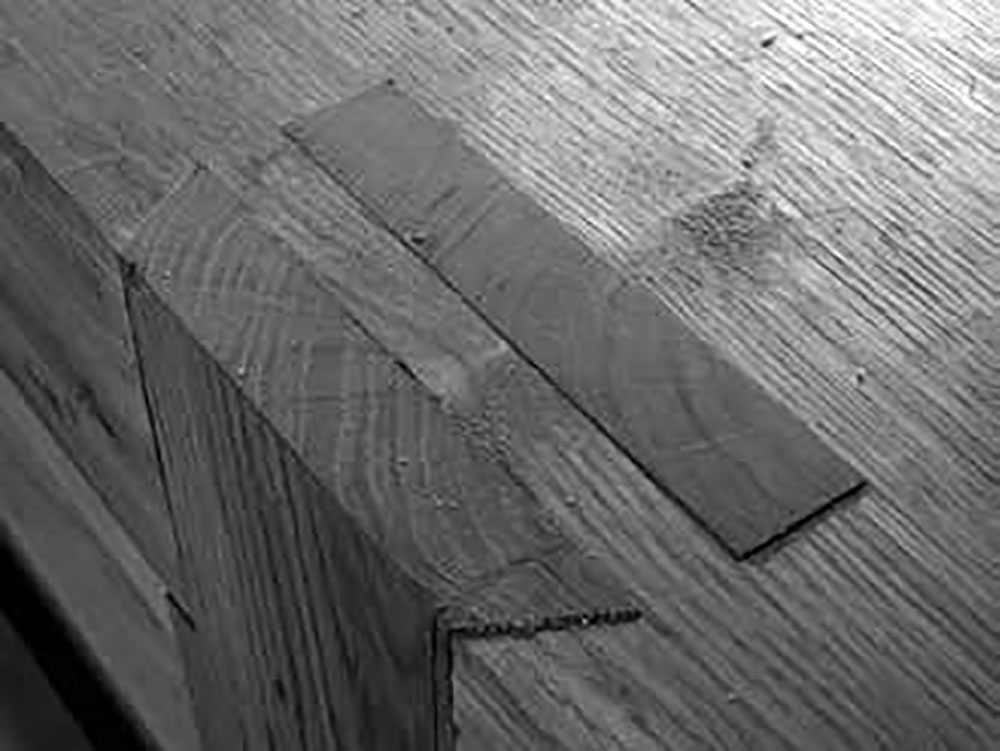
If you do find stock that is 6″ thick and 22″ wide for your benchtop, it almost certainly will be wet in the middle and prone to distortion. The first French bench that I built used a 4-1/2″-thick cherry slab that had been seasoning in a lot for about five years. The first couple years with that bench were rough. The top shrank at least 1/16″, leaving the through-tenons and sliding dovetails proud of the benchtop.
After planing those flush, the top didn’t shrink much more, but it sagged a bit in the middle during the third year. And now the benchtop is quite stable – yearly humidity fluctuations have little effect on it. The tops of the legs and the benchtop are always in the same plane and the overall shape of the top is consistent.
The French oak that I used in 2013 was likely even wetter than the cherry. For starters, the oak was thicker. And thick material takes a lot longer to dry than thin material. When we first cut into the oak, we used a moisture meter on the wood and found its moisture content in a few places was off the charts. Most places on the bench were about 30 percent moisture content, which is quite wet by furniture standards.
Two months after completing the bench, the top was so wet that it would rust the surface of a holdfast left in a hole overnight.
Like the slab cherry workbench I’d built years before, the oak benchtop shrank around the tenons by more than 1/16″ during the first six months. And the middle of the benchtop began to sag. I flattened the oak top twice during the first nine months in order to be able to plane thin stock on my benchtop.
This begs the question: How flat does a bench need to be? The answer is: It depends on your work. If you plane woods that are less than 3/4″ thick, benchtop flatness is important. I shoot for getting the front 12″ of the benchtop so flat that I cannot get a .006″ feeler gauge under a straightedge anywhere in that area.
If you work with thick stuff or do mostly carpentry, you can be more cavalier.
So if thick slab workbenches are so difficult to find and fussy at first, why bother?
After they settle down, slab workbenches move very little. The same forces that make the top dry slowly also retard its ability to take on much moisture during the seasons (thanks to Steve Schafer for explaining this via Fick’s Second Law, a diffusion equation). After about five years in your shop, your benchtop should be well acclimated and monolithic.
— MB
For unrelated reasons with some friends we are testing leaving hardwood in salt water. My guess is that weigh might up as the wood gets some salt in (or not, if more water comes out due to osmosis). Because salt is hygroscopic, we are testing whether the wood will settle on a given % humidity and stay reasonably put irrespective of the indoor climate — the experiment is being carried out in Finland where houses are very dry and wood tends to shrink a lot (and get quite brittle). Basically absorbing salt could give more buffer in terms of humidity range.
Has anybody tried something like that (1) at all and (2) specifically for bench tops?
I believe having a mineral soaked within the pores of your wood would severely damage any sharp edge put against it, but don’t quote me on it 🙂
I won’t 😉 but I would have though salt is soft enough not to dull metal?
I’m curious now if the dissolved salt increases the hardness of a wood. Surely it’s tougher than pine? I wonder how big the particles are once the water dissolves.
I guess it might be harder than pine, but we are testing it in oak. The salt, assuming it actually gets into the wood, should fill the pores to some degree. Admittedly we plan to ‘salt’ the wood after it has been cut and worked, so we would not really have issues of having to plane it again to flatten it.
There is an industry around salvaging old-growth lumber from lakes and the ocean. I’ve not seen reports on how the wood behaves long term. Search with terms like: reclaimed or salvaged wood from lakes or ocean. http://www.popularwoodworking.com/article/buying_submerged_lumber http://crossroadslumber.com/historic-large-dimension-ocean-salvage-timbers/
Thanks, I will probably contact them and ask what their experience is. They would not really work for us as suppliers (wrong continent) but they might have interesting insights.
From the academic access to WorldCat.org. The description of the book is followed by a listing of libraries that have uploaded records to indicate that they own a copy of the book. In some cases, libraries own books but do not upload records to WorldCat.org.
With all the precision possible : Roubo on furniture making
Author:
Roubo, M.; Don Williams; Michele Pietryka-Pagán; Philippe Lafargue
Publisher:
Fort Mitchell, Ky : Lost Art Press, 2013.
Edition/Format:
 Print book : English
Database:
WorldCat
Rating:
(not yet rated) 0 with reviews – Be the first.
Subjects
• Carpentry — Early works to 1800.
• Joinery — Early works to 1800.
• Cabinetwork — Early works to 1800.
• View all subjects
More like this
• Similar Items
1.
Jefferson Library, Thomas Jefferson Foundation
Jefferson Library, Monticello
Charlottesville, VA 22902 United States
For an excerpt, Roubo reads alot like Schwartz.. Or is it just me?
This excerpt is part of my essay in the book. Should have made that clear.
Tis okay, If you didn’t spend time writing about these, people might have forgotten.