This is an excerpt from “The Anarchist’s Tool Chest” by Christopher Schwarz.
The funny thing is that it was my mad obsession with acquiring woodworking stuff that helped me find a balanced approach to the craft. You see, I became as obsessed with acquiring woodworking books as I was with the tools. I’ve always been a voracious reader, so consuming books on woodworking and tools was natural. (And add to that the fact that I was freelancing at the time as a contributing editor for the WoodWorkers’ Book Club newsletter. That job was a five-year-long force-fed diet of woodworking writing.)
Read enough modern woodworking books, and you might just want to gouge out your eyes with a melon baller. They are all so similar and shallow and filled with idiosyncratic information. I can’t tell you how many times I read the following phrase: “This might not be the right way to do this, but it works for me.”
Something inside my head made me wonder about that “right way” the author rejected.
It just so happened that at about that same time I had a short phone conversation with Graham Blackburn, one of my woodworking heroes. I had a few of Blackburn’s books from the 1970s, and I knew he had a command of woodworking history. So I interviewed him about the origin of the word “jack” in “jack plane” for a short piece I was writing for the magazine.
We then started talking about saws.
During the conversation, Blackburn said I could find the answer to one of my questions in the book “Grimshaw on Saws.”
Huh? I replied.
I’ll never forget what he said next: “You don’t have a copy of Grimshaw, and you’re an editor at a woodworking magazine? Hmmm.”
I was ashamed. So ashamed that I went down to Cincinnati’s public library that weekend to check out Robert Grimshaw’s 1882 treatise on saws. It was sitting on the shelf next to a bunch of other old woodworking books I’d never heard of. I wondered which of those books were also “required reading” in Blackburn’s world. I checked out as many of those cloth-bound books as the library would let me. I went home. I started reading, and I haven’t stopped.
The things I learned from the old books were different than what I expected to learn. I actually expected the shop practices to be different – you know, they had different ways of cutting a mortise, a tenon and a dovetail. But really, not much has changed in the way that steel (usually) defeats wood.
While there are a wide variety of ways to perform every standard operation, the pre-Industrial craftsman didn’t seem to have secret tricks as much as he had lots of opportunities to practice and become swift.
Instead, what surprised me was the small set of tools that were prescribed for a person who wanted to become a joiner or a cabinetmaker.
Joseph Moxon, the earliest English chronicler of woodworking, describes 44 kinds of tools necessary for joinery in “Mechanick Exercises” (1678). For some of these tools, you’d need several in different sizes (such as chisels), but for many of the tools that he described, a joiner would need only one (a workbench, axe, fore plane etc.).
Randle Holme’s “Academie of Armory” (Book III, 1688) has approximately 46 different joinery tools explained in his encyclopedia. An exact number is hard to pin down because some of the tools are discussed twice(for example, mallets, smoothing planes and hatchets) and some tools seem shared with the carpentry trade.
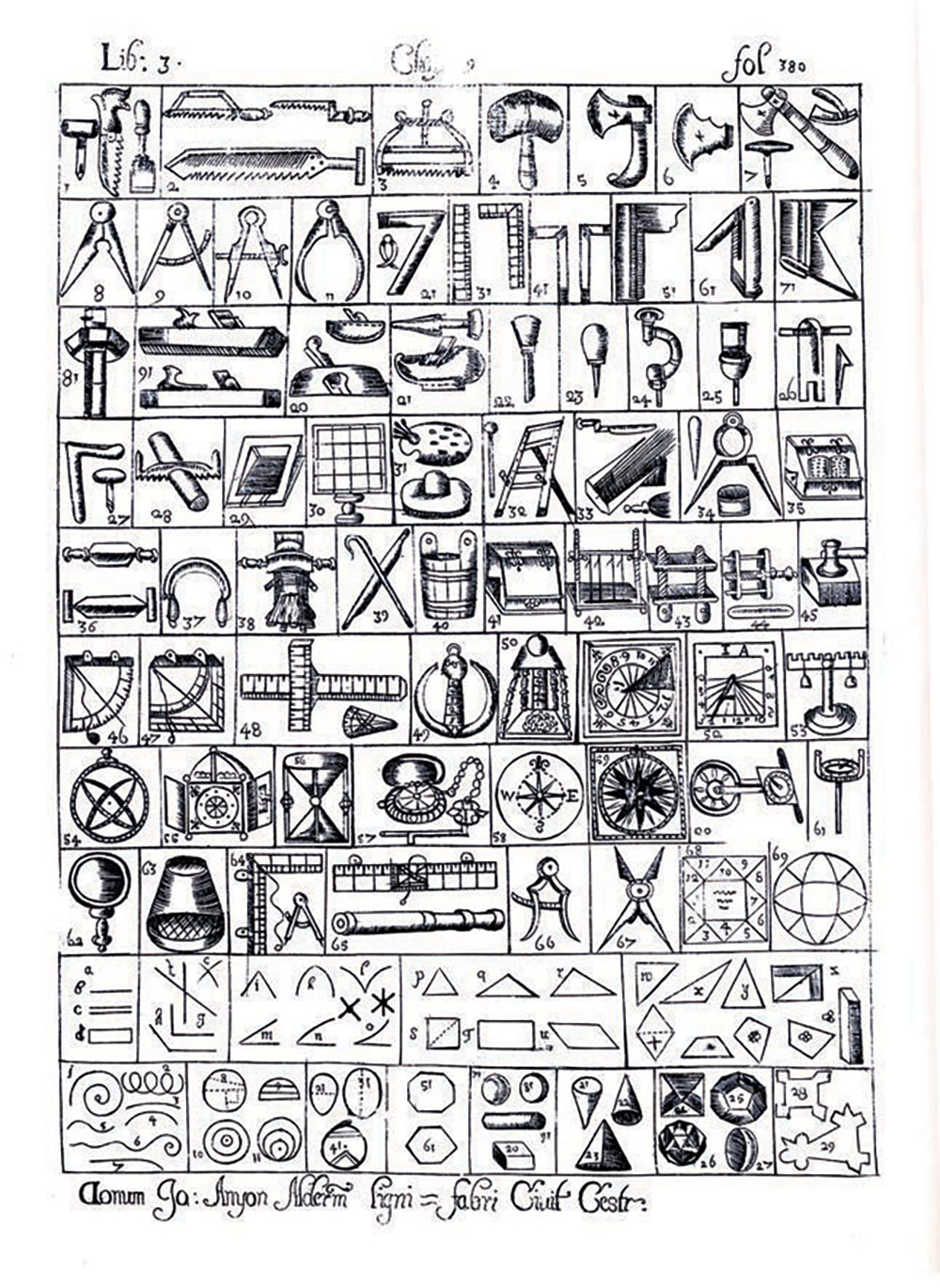
If we jump forward more than 150 years, not too much has changed. The list of tools required by the rural joiner in “The Joiner and Cabinet Maker” (1839) isn’t all that much different from the tool list described by Moxon and Holme. “The Joiner and Cabinet Maker” gives a significant description to about 40 tools used by a young apprentice during his climb to journeyman.
As the Industrial Revolution begins to crank out mass-manufactured tools, the basic list of tools recommended for basic joinery starts to expand. There are more kinds of boring bits available, new kinds of metallic planes (such as blocks, shoulders and routers), plus some new saws, including the coping saw.
By the 20th century, the basic list of tools for joiners stands at about 63, according to books by Charles Hayward, the traditionally trained dean of workshop writers. Still, when I looked at Hayward’s list it seemed rather paltry compared to what was in my shop. (See this book’s appendix for a comparison of these tool lists.)
At first, I attributed these short lists of essential tools to three things:
• Everything in the pre-Industrial age would have been more expensive because it was made by hand.
• The general level of economic prosperity was lower.
• Technological innovation had yet to produce the fantastic new tools shown in the modern catalogs.
But all that was just denial kicking in.
— MB
I’ve read this passage in The Anarchist’s Tool Chest a number of times. Every time I read it, I feel a bit sick and hollow inside because I live more than a hundred miles from the nearest real library. I would love to read Grimshaw on Saws. Alas…
Start here:
https://books.google.com/books?id=0_IqelmQZCgC&dq=grimshaw%20on%20saws&pg=PP2#v=onepage&q=grimshaw%20on%20saws&f=false
I like this source — a bit more versatile format (though I think Google’s collection of works is much larger): https://archive.org/details/sawshistorydevel00grimrich
Also here: http://www.woodworkslibrary.com/repository/saws.pdf
Interestingly enough, I feel sick and hollow inside for different reasons – because I have no idea how to pare down my tools to anything close to 63 (much less 40, 44, or 46) tools.
Wondering if I should pull the 40 from my existing tools and put them in my toolchest and store the others away for a while, try and work from what I have and see how it goes before I try purging other tools?
Ethan,
I have more than 63 tools (though they do all fit in my tool chest). These lists are (and always have been) a starting point for making furniture.
Many beginners won’t start building until they have every tool in the catalog. That is unnecessary.
I have far more than 63 tools… But they were all acquired under the same system, I bought them when the need arose. Some of those needs were the ability to do a task already mastered faster and later many more came along as a way of doing something in a different or more interesting manner . But universally the ones I bought just because I wanted them have fallen by the wayside, sold or given away.
Even with that understanding, I feel the urge to purge tools – duplicates that have “sentimental value” that really DON’T have such value (aside from being old tools I first had or something that is really cool but I don’t use it as much as my standard version because that one works better), crappy tool-like objects I should not have ever bought (but don’t entirely know if I am comfortable re-selling to anyone else because I don’t want to perpetuate their existence), and partial planes I’ve scavenged parts off of.
Nothing emphasizes “too many tools” more than having to pick up shop and moving into something temporary, so that you have to spend a significant portion of time looking for the tools you need before you can use them. Or maybe that emphasizes a lack of organization…
Having just recently picked up a walnut carpenter’s chest that is just a few inches smaller than the ATC, I think my current plan of action should be to move the indicated 63 tools into it and see how well I can work out of it with minimal use of my other tools. This might give me a better handle on what else needs to go.
Appreciate the feedback, Chris.
Purges feel good. And they greatly help the woodworking community.
I love the illustration of necessary tools from Randle Holme’s “Academie of Armory.” Do you have a good high resolution scan of this that could be used to print a wall poster?
Practice makes perfect (or somewhere close at least). If you have 500 tools, then how long will it take to master them all? Is it possible that some of the around 50 tools in the basic kit would do a lot of the jobs, if you take your time at mastering those first, before venturing out in more purchases?
A very saying picture of this is the senior joiner attending one of Chris’ courses, opting to bang out the dove tails at the base with a chisel in stead of using a coping saw to rough them out. I bet he never had a dove tail gauge either. He most likely would make do with a bevel square. Some tools are simply invented to sell, much more than be of any real practical use. I’m not saying neither the dove tail gauge nor the coping saw are in this category, but it just shows you can do fine without. For this application at least. This is especially true to various jigs and newer tools promising to take over every operation in the shop, if you only buy this.
I finished ATC over the summer. It was an absolute joy to read, and since reading it I have found that I have referred to it regularly as I purchased new tools (or chose not to purchase in some cases). The time and money I have saved by applying some of the concepts, alone they make the book a worthwhile purchase. But the quality of my work has improved as well. Thank you for sharing this passage!
Please tell me of a place to donate good usable tools. I can give them to the local thrift store but for some reason I don’t like the thought of my tools languishing on the shelves marked “junk.”
Habitat for Humanity’s ReStore will gladly take them (I’ve seen a Stanley 45 at our local one!).
The other option is to offer them for the cost of postage on WoodNet or one of the other formus, which have “Swap ‘n’ Sell” sections.
I love the drawing of the artist’s palette and the easel. Adorable.
I’m wondering if Christopher has a reading list available anywhere of these older books that are generally considered classics or must-reads?
Well, any of the historic LAP reprints might qualify.
He has a few books listed in this post https://blog.lostartpress.com/2012/11/30/10-books-that-changed-the-way-i-think/ from a while back.
Popular Woodworking published a list of classic WW books in the June 2011 issue referenced here http://www.popularwoodworking.com/woodworking-blogs/chris-schwarz-blog/roy-underhills-3-favorite-books
Fantastic. thanks