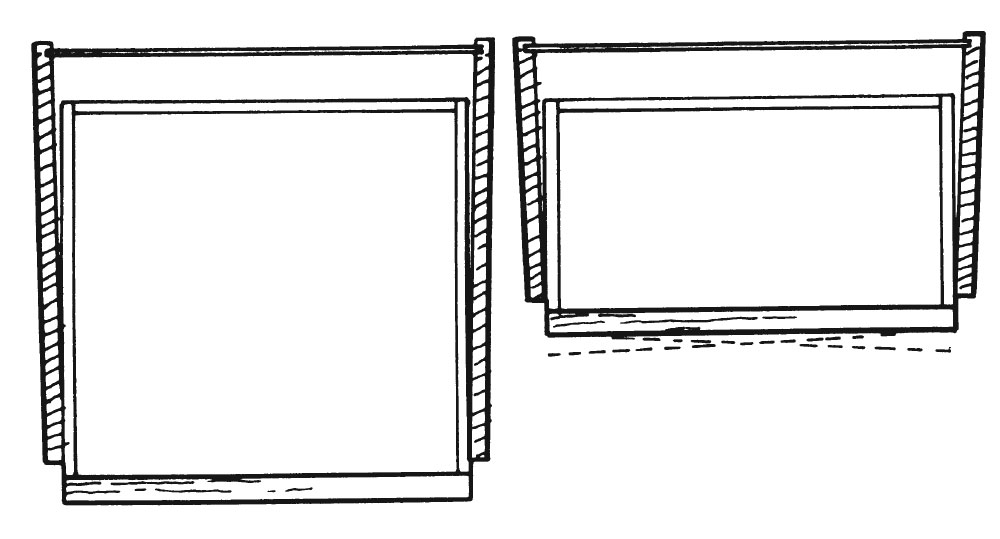
This is an excerpt from “The Essential Woodworker” by Robert Wearing.
A well-fitting drawer can be likened to a piston working in a cylinder. For a drawer to fit well, not only is it important that the drawer itself is absolutely accurate on the outside, but equally important is the accuracy of the opening into which it must slide. Therefore, when setting out a carcase, great care must be taken to see that the drawer opening is as large at the back of the job as it is at the front. Indeed, to ensure a really good fit, it is better to allow a very slight clearance at the back, both in height and in width. This will make certain that the drawer will not wedge at the back, and will allow for any slight inward bowing of the carcase.
The amount of this clearance is directly related to the length of the drawer side (Fig 471) but on the longest side should never exceed 1mm (1/32 in.) on each side of the drawer; a greater amount would allow the drawer to wobble even when nearly closed. In the type of job where drawer guides are used, this clearance can easily be obtained (in width, but not in height) by adjusting the guides when the drawer is being fitted. Any twist in the carcase or framing will also cause a drawer to jam.
Test the accuracy of a job as it is being built. Take a small strip of wood about 3mm (1/8 in.) square, and cut it to length so that it just fits into the front of the opening into which the drawer will slide. Push it to the back where it should be a much slacker fit. This ‘feeler gauge’ test should be applied both horizontally and vertically, and should also be applied at the glueing stage when distortion caused by cramping may occur.
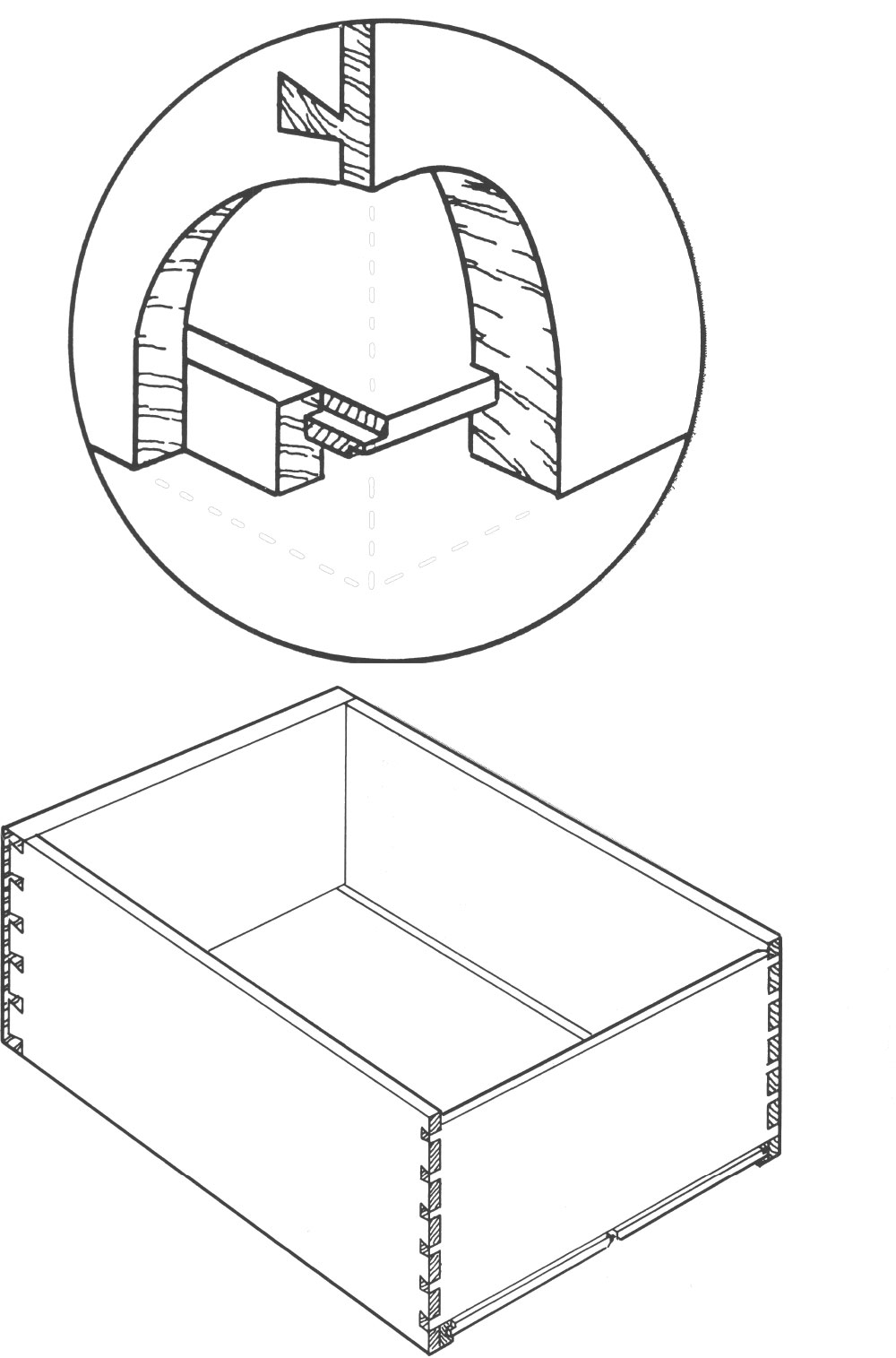
The joints on the previous pages (above and left in blog post) show the various joints used in drawer construction. The front joints are normal lap dovetails and, as they are exposed to view when the drawer is opened, they should be decorative as well as strong, with the pins not too large, say 3mm (1/8 in.) thick at their thinnest point. It is the practice of some craftsmen to make this dimension as small as possible – in fact only the thickness of a fine dovetail saw. This causes the pins to appear ‘floating’ or detached from the rest of the front and so generally out of proportion with the rest of the joint.
The through-dovetails at the back have a particular arrangement to allow for the fixing of the drawer bottom. The top edge of the back is set down about 3mm (1/8 in.), and the bottom edge is raised so that the drawer bottom can be slid in beneath it. These spaces above and below the back allow the air to flow in and out as the drawer is moved. A larger space at the top would allow papers and other flat objects to fall over the back; 3mm (1/8 in.) clearance is ample.
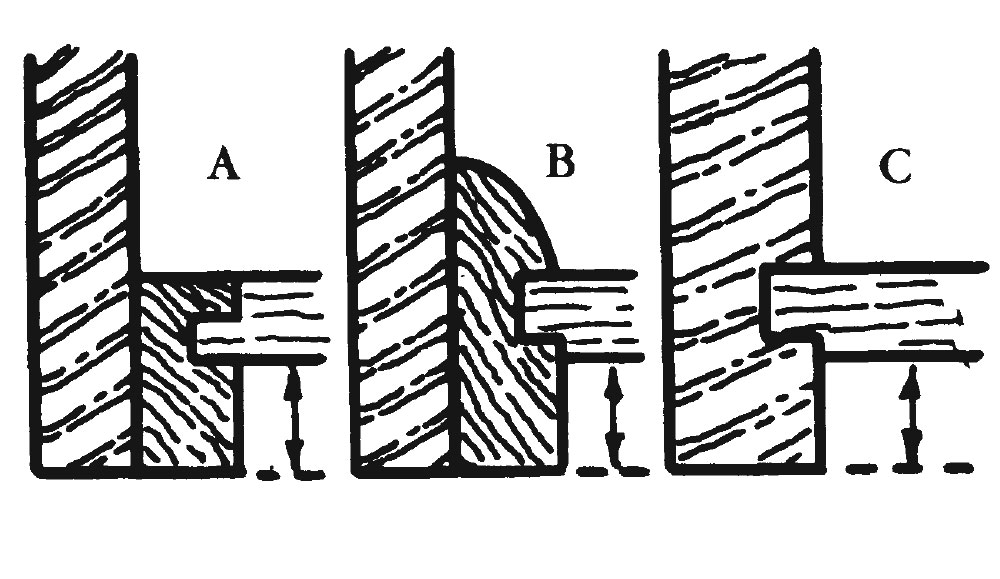
Drawer bottom: The method of fixing the drawer bottom to the side usually depends upon the material being used, or on the quality of job. Three commonly accepted methods are shown in Fig 473. Method A is used in the finest quality work, and with this method solid timber should be used for the bottom. If plywood were used, the top layer of veneer would be liable to chip along the shoulder. This method is suitable for desk drawers where papers and flat objects are housed. B is used in large drawers for housing linen, etc. It is somewhat stronger than A having a larger groove and is therefore capable of bearing more weight. Method C is simple and direct, but the absence of a drawer slip will cause the edge of the side to wear rapidly. This is usually countered by increasing the thickness of the side, but this gives the drawer a heavy, clumsy appearance. This method is used in carpentry, joinery and kitchen furniture.
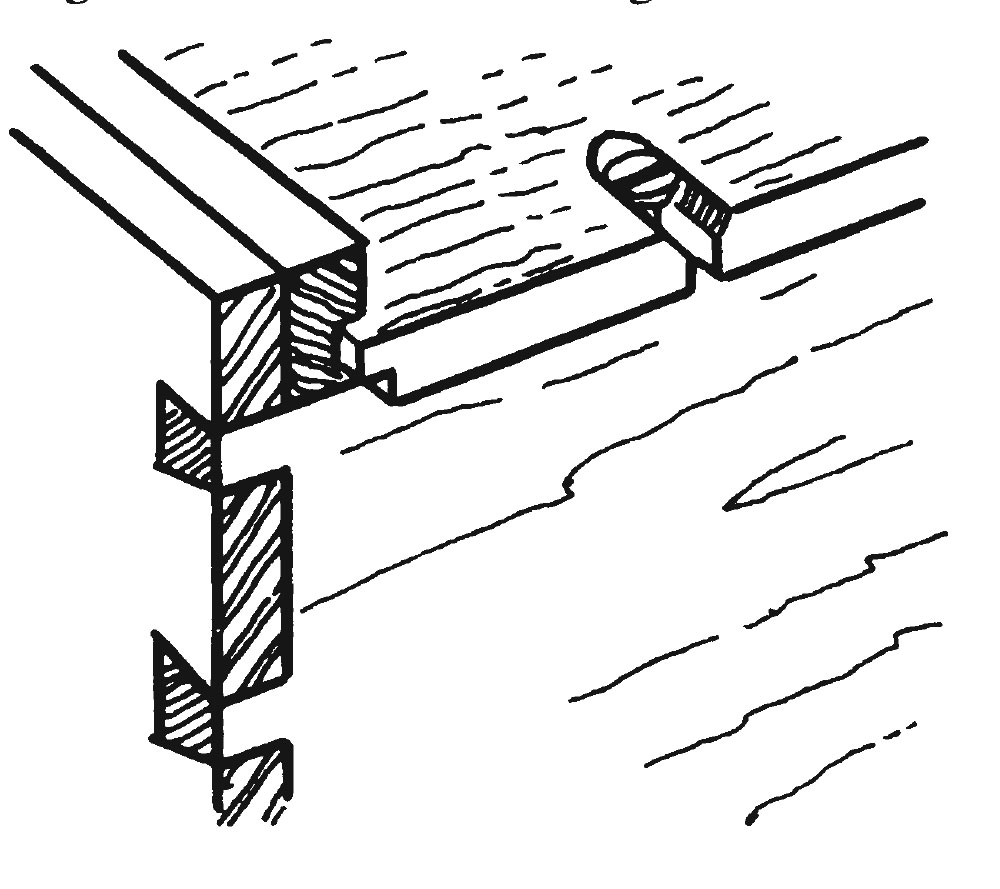
The bottom has an important function in the construction of a drawer. Its front edge is tongued and glued into the drawer front so that the bottom will hold the whole drawer framework true and square (see inset Fig 472). It also keeps the sides straight, thus helping the drawer to run evenly. Where solid wood is used the grain should run from side to side of the drawer. The bottom must not be glued along the slips since allowance must be made for shrinking. To secure it along the rear edge the bottom is either slot screwed (solid wood) or screwed (plywood) to the underside of the drawer back (Fig 474). Where solid wood is used the back edge is left protruding about 3mm (1/8 in.). When the drawer is very large (e.g. in a chest of drawers) the bottom is not made of just one piece because this would tend to sag or split in the centre. It is divided into two, or even three parts, and muntins are fitted between them. These are like very wide slips, except that they are not quite flush with the bottom edge of the drawer. They are morticed and tenoned into the drawer front and fastened up under the drawer back with screws.
— MB
do you have more info on the last part about the large draws? I have repaired a few and have never seen muntins on the bottoms. I end up using a lap joint and I am not happy with them.
I think I understand your question. I have some of my great grandmothers furniture and one of the dressers has this set up. The best way to describe it is it looks like frame and panel with a stile running front to back separating the two pieces that make up the bottom of the drawer and in my case the “stile” is proud of the surface and rounded on the edges. So if you think about that when reading the last part, it might make more sense. I had to read it twice myself. (Three times if you count the time I read the entire book.) I hope this is what you were referring to. Hope this helps.
that’s kinda what I had envisioned. but I do a lot of repair stuff and have never seen this.I do find bottoms were the center rail has worn a hole in the drawer bottom.. I will use that on my next piece…….Thanks Toolnut
Found a pic. On page 245 bottom right hand corner fig 16 and (16)A. Don’t worry, the link starts at page 244. If you have trouble Google “Encyclopedia of Furniture Making Ernest Joyce Alan Peters”. I copied the link and tried it in another browser window and it worked.
https://books.google.com/books?id=6MazKMAhAPYC&pg=PA244&lpg=PA244&dq=english+drawer+construction+slip&source=bl&ots=WbAf9unuwf&sig=WY8GV5-LgjLIdY5KAiCRT0G0osE&hl=en&sa=X&ved=0ahUKEwi8z_LNisHRAhUow4MKHcrmAaUQ6AEIOTAH#v=onepage&q=english%20drawer%20construction%20slip&f=false
Drawer making is one of those things where it looks easy when I look at factory drawers, then I see something like this and think it looks super complicated.
its not at all complicated, do your best to get the back and front the same length and the same with the sides. don’t freak out about making sure it’ square cause the bottom will square it up and keep it that way.
Chris, I have got to make a comment from an engineering perspective. The joint shown as B has one flaw. The rabbet joint places the wood fibres of the draw bottom in bending when the drawers is heavily loaded. The fibres at the right angle will start to tear, Making for a weak joint. A better way to construct is to leave the shear area of the side rail, as indicated by the arrow, but change the joint to a dado. This way the drawer bottom is in compression and much stronger. Who is going to check the bottom of a drawer for the precision of your joinery? You will also save a lot of construction time.