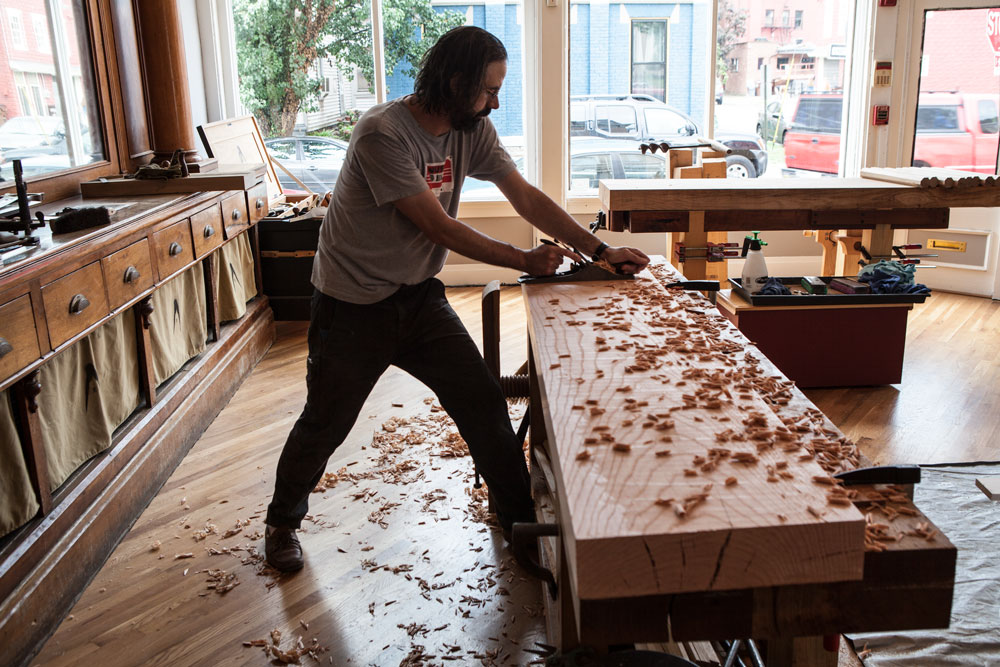
I only want to work each surface of this benchtop once. The slab weighs enough (approximately 115 pounds) that I have to struggle with it to get it in and out of the vise and onto the benchtop.
So every move with the slab is planned with care so I don’t end up injured or (at best) embarrassed at having to ask a friend to help me get the benchtop off the floor.
Today I dressed the two broad faces of the benchtop: the underside and the benchtop itself. Both have to be fairly flat and free of twist in my experience. Of course, this slab turned out to be a weird one. Typically the bark side of a slab will be concave across its width, and the heart side will be convex. This slab was reversed.
So I started on the convex face. Normally when I dress a rough convex face I remove the hump in the middle using with-the-grain strokes with my jack. But because I had a lot of wood to remove (about a quarter of a thumb), I used a different tactic. I traversed the hump alone at first and stayed away from the long edges of the benchtop. Traversing allowed me to take a bigger bite with the jack plane.
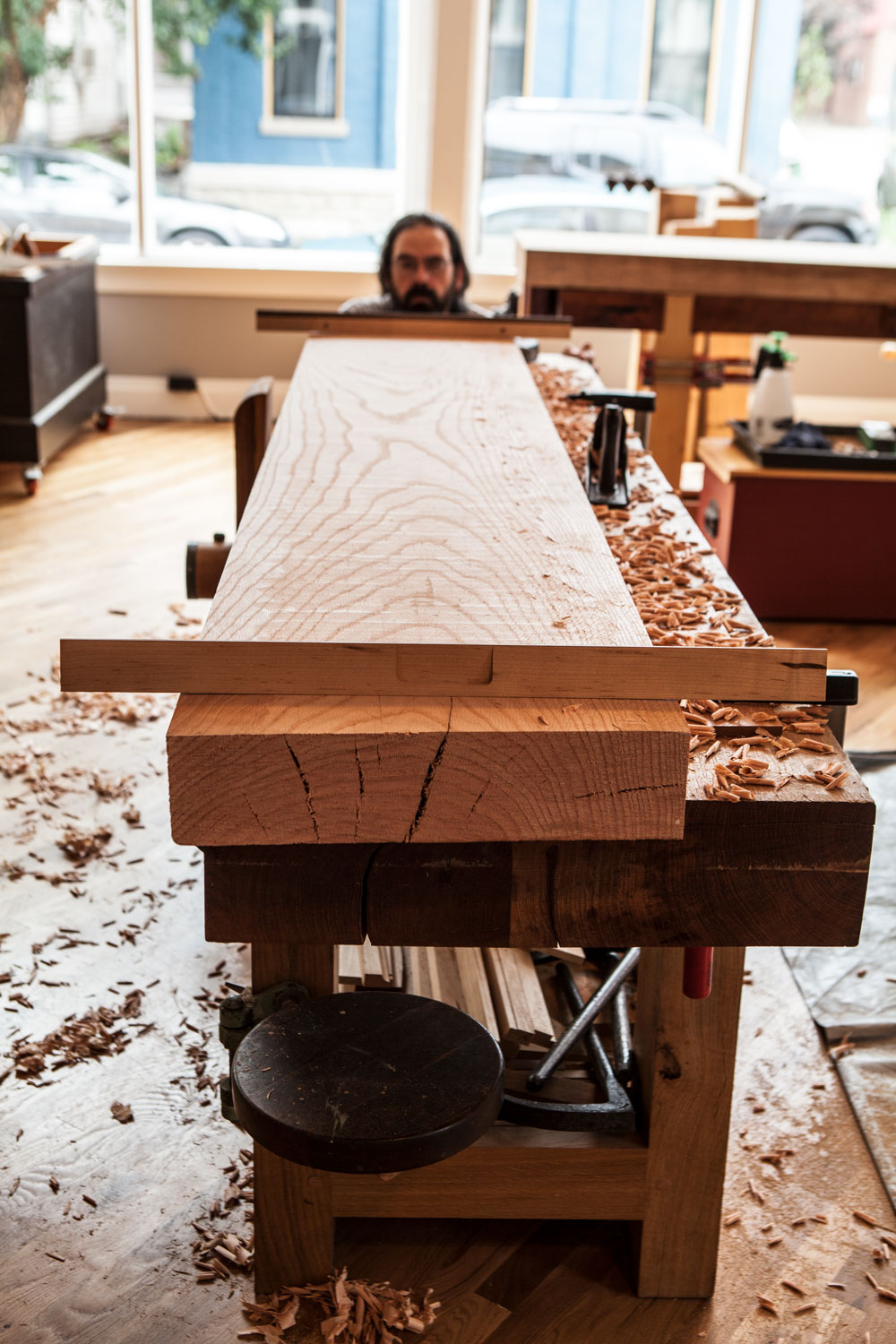
Once the hump was gone, I checked the top for twist. It was indeed twisted. So I used my jack plane to work away the two high corners, which were diagonal from one another.
When the underside was flat (according to the winding sticks), I dressed the entire underside of the top with the jack to leave a consistent and tidy (if scalloped) surface.
Then I flipped the benchtop over to work on the concave side.
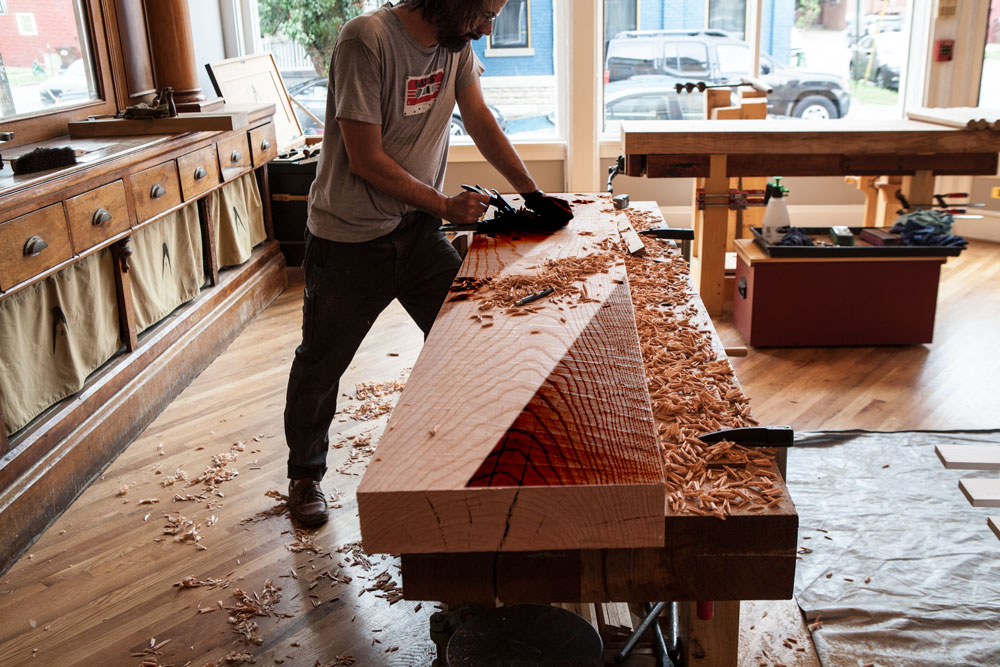
Because I knew this surface was also twisted, I began working away the two high corners straightaway. After bringing all the corners into the same plane, I dressed the surface with a jack. I’ll probably dress it with the jointer in the morning and leave it like that until after assembly – that’s when I’ll clean up the leg joints protruding through the benchtop and tooth the surface with a toothing plane.
I also managed to rough out the legs on the band saw today and hope to turn them on the lathe tomorrow.
If this sounds like a lot of work, it’s not. I have logged only two full hours of shop time. How much more time I’ll log will be determined by whether I decide to build an opossum or an arachnid.
— Christopher Schwarz
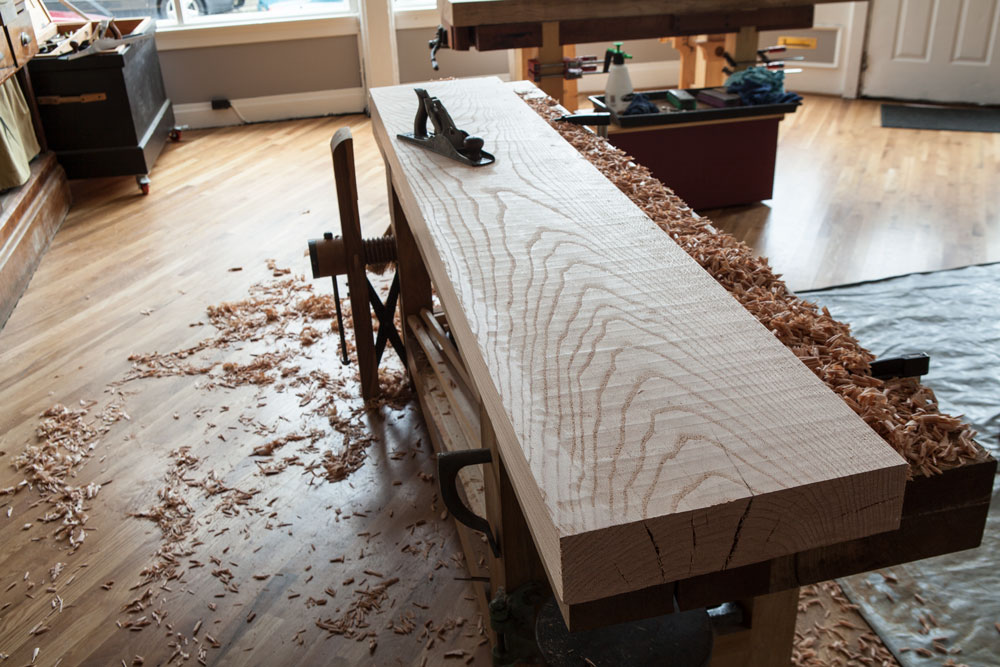
Beautiful chunk of tree there. I’m glad you’re posting these progress updates. It’s a very welcome reminder that while all the noise of politics and the like clamors for our mental bandwidth, there’s still room for a simple, direct task with an obvious aim.
I think that furrowed surface is the best thing about traversing a board. I’m almost sad when it disappears under my try plane.
Do you have plans, or something written up about that awesome little stool (at least that’s what it looks like) on the one end of your bench in the picture with the winding sticks? That looks like an awesome addition to a bench.
He didn’t post any plans, but Schwarz did mention wanting a bench seat a while back. I think there’s some good stuff in the comments thread about it.
https://blog.lostartpress.com/2016/02/21/a-workbench-accessory-id-love-to-have/
Not sure where Chris got his, but Jameel @ Benchcrafted is working on a consumer-friendly solution to the Bench Seat.
http://benchcrafted.blogspot.com/2016/06/the-big-bench-seat-update.html
Looks good. I’m sure that one heck of a workout. I need to lose some weight so I need to get looking for boards that big.
Why the step with the toothed plane? I think I’ve been using mine for the wrong reasons.
How did you darken the two corners? Digitally?
Yup. In Photoshop.
Chris,
I’ve always wanted to ask you this on one media outlet or another, so I’ll ask now…
You often seem to start with or at least include heavy traversing when you flatten a large panel. I consider traversing invaluable in this application, as would most, but I try to minimize it given how much repetitive, jerky motion it involves. Making a “pass” of traversing strokes along a 2m board is hard work. As such, I’ll usually take a few traverse strokes at different points along the board to ensure cupping is present, and then I’ll make one or two long grain passes along the very edges. I find that these long grain passes can potentially eliminate an entire round of traverse passes. After the long strokes, I’ll do my traverse passes at the same few points as a “check”, and then either take another series of long passes or follow through with traversing the entire length of the board, assuming I’m getting almost full shavings on the “check” passes.
Obviously cranky grain which is prone to extreme tearout with low angle planes would tip the scales in favor of your method.
I’d be interested to hear your take on this hybrid approach. It may be worth noting that I use a 9.25″ radius camber instead of an 8″. This works a bit better in the harder, Australian woods with which I typically work.
Cheers,
Luke
The advantage of traversing is that you can take a huge bite with less effort. With this slab I had to remove 3/16″ from each side, so with-the-grain passes would have been a lot more work.
When working with minimally cupped panels that have been machined, your approach is very similar to what I do. But for heavy work, I traverse.
I actually don’t find traversing to be “jerky work.” Many students I’ve taught tend to do it in a way that wears them out. Basically, they use their arms like they are scrubbing the top clean. That will wear you out. I lock my arms and rock my torso forward and back. It’s a very smooth operation and not tiring at all.
Thanks for your comment!
Chris, the bench is interesting enough, but I’m even more interested in the tools the Roman’s would have used to build the bench. Do you plan to write about this in the future?
It’s not on my (long) list of projects ahead.
You might check out Ulrich’s book “Roman Woodworking” and Goodman’s “The History of Woodworking Tools.” Both have a lot of information on Roman tools and (importantly) cites for other primary sources for you to explore.
Awesome. Thanks for the information
I too am glad you’re posting these updates. It’s a fascinating process, and it will help me understand the finished product better.
Chris, its non of my business of course but why the effort of getting the underside of your workbench as flat as the work surface. The ends would look a bit funny and the legs would be of different lengths of course but does that really matter ? Its not a piece of furniture !
Just for the looks ?
Thanks & greetings from Sweden.
JosH.
If I didn’t flatten the underside, the legs would appear to be at three or four different compound angles. And this would drive me crazy.
You are right that it won’t matter to the function. But it will matter to my eye. And I have to look at this thing for the rest of my days.
Do you think that the Romans actually went to such trouble ? Having seen many work benches in many parts of the world , I dont think they did . I observation is that they would ahve hewed it flat enough stuck some legs in and got to work .
Roman woodwork had the same range as our own – from the dirt simpler vernacular to very intricate, moulded work with applied ornaments.
So I have no reason to assume anything about their workbenches other than there was probably a range, much like there has always been.
The end view photo shows what looks to be pretty decent-sized checks. Are you filling these with epoxy like you’ve done on other slabs / written about in your books? Thanks.
Nope. Just going to let them be.