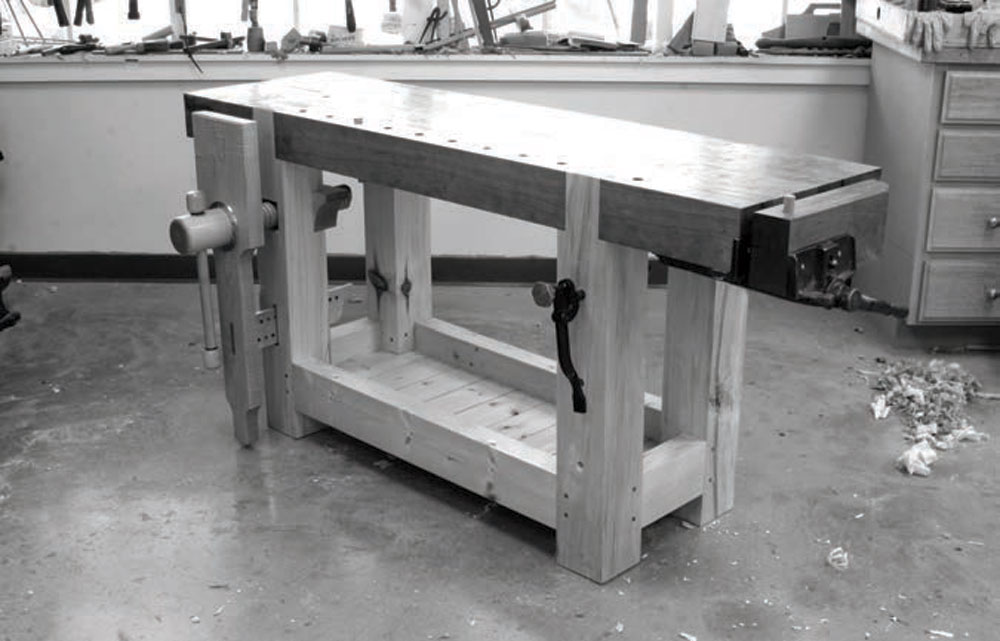
This is an excerpt from “The Anarchist’s Tool Chest” by Christopher Schwarz.
Workbench
I have written two books on workbenches that agonize over the details of joinery, wood selection, vises and so on. But if you don’t want to buy those books, here is the down-and-dirty data you need to pick a bench design.
Note: Before you write me an angry letter about this list – you don’t have to have a good bench to be a good woodworker. You can work on the kitchen table and make world-class work. But a good bench will make many operations easier. It’s simply a tool: the biggest clamp in the shop.
Rule No. 1: Always Add Mass
For workbenches, here’s my maxim: If it looks stout, then make it doubly so. Everything about a workbench takes punishment that is akin to a kitchen chair in a house full of 8-year-old boys.
Early Roman workbenches were built like a Windsor chair. Stout legs were tenoned into a massive top and wedged in place. Traditional French workbenches had massive tops (up to 6″ thick), with legs that were big enough to be called tree trunks. Later workbenches relied more on engineering than mass. The classic Continental-style workbench uses a trestle design and dovetails in the aprons and vises to create a bench for the ages. The 19th-century English workbench uses an early torsion-box design to create a stable place to work. And good-quality modern workbenches use threaded rods and bolts to tighten up a design that lacks mass.
Many inexpensive commercial benches are ridiculously rickety. They sway and rack under hand pressure. You can push them across your shop by performing simple operations: routing, sawing, planing. If the bench looks delicate or its components are sized like a modern dining table, I would take a closer look before committing.
A big thick top and stout legs add mass that will help your work. Heavy cabinet saws with lots of cast iron tend to run smoother than plastic ones. The same goes with benches. Once your bench hits about 300 pounds, it won’t move unless you want it to move.
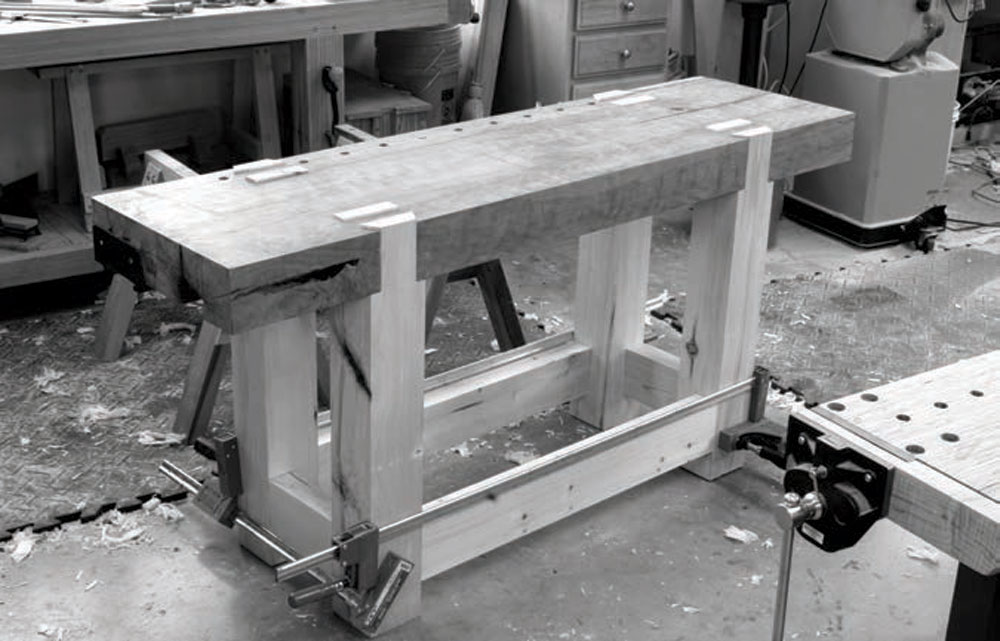
Rule No. 2: Use Stout Joints
Overbuild your workbench by using the best joints. These are times to whip out the through-tenon and dovetail. If you followed rule No. 1, then rule No. 2 should be no problem. Your joints will be sized to fit the massive scale of your components. If you cannot rely on mass, then you should beef things up with superior joinery. While dovetails and through-tenons are overkill for a towel rack, they are de rigueur for a bench.
That’s because you are applying wracking force to the workbench with typical operations and your vises will do their best to tear apart your bench. All wooden vises need to be overbuilt or they will self-destruct when you cinch them down hard. I’ve even seen a vise rip a benchtop from its base.
Make your tenons thick and your mortises deep. If you know how to drawbore a mortise-and-tenon joint, this is one good application. Have you ever been in a timber-framed barn? Did you look at the joints? They’re massive and pegged. Imitate that.
I think benches are a good place to practice your skills at cutting these classic joints, but some woodworkers still resist. If that’s you, you should investigate hardware to strengthen your bench. Threaded rods, bed bolts, special bench bolts or even stove bolts can turn a spindly assembly into something rigid that can be snugged up if it loosens. The hardware won’t give you mass, but it will strengthen a rickety assembly.
— MB
Chris, I made a bench based on your book on workbench design. Roubo designed and with stuff from Lowe’s and hardware from my old bench. Wagon vice and shoulder vice with square dog holes its stained and dented now ,it looks nothing like those pretty benches seen on this site. It is by far the best tool in my shop.
The top rests in shallow mortise but not glued or pinned to the base. Never had a lick of trouble. Flatten the top once at completion and again after 3 yrs. I use it every day. Thanks.
Bob