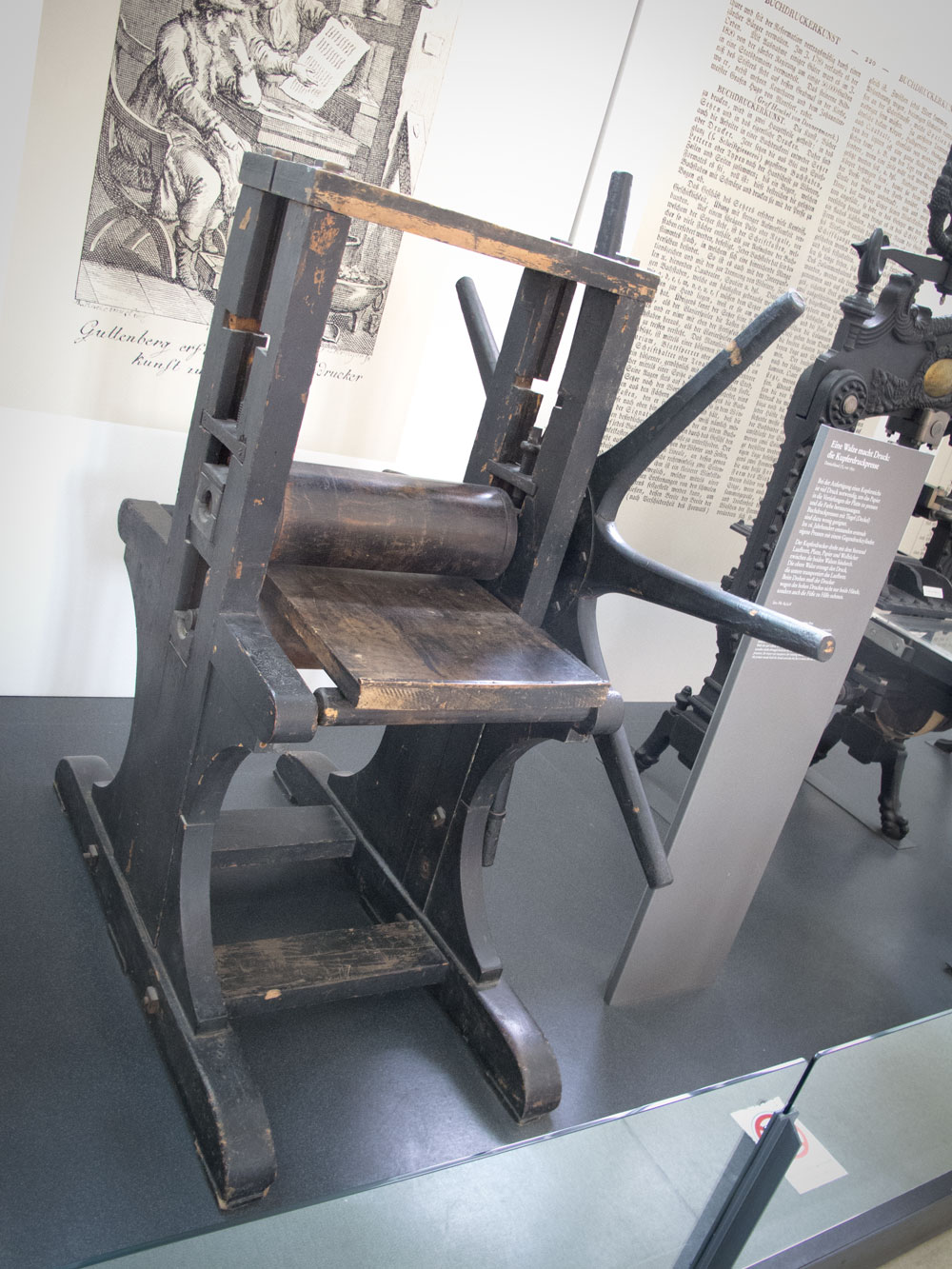
One of the most astonishing things about studying early plates in books such as A.-J. Roubo’s “L’Art du menuisier” is that the plates are not simply two-dimensional. There is a great deal of texture. The paper is radically depressed in the field where the paper went through the copperplate press. And you can feel every line.
Last week at the Deutches Museum in Munich I spent the most time in the museum’s section on printing. I didn’t need to read much about the letterpress; we had one of those in college that I played with all the time instead of studying. But the copperplate press and its exhibit were fascinating. The exhibit showed how the thin copper plates were coated in acid-resistant wax and soot, and then how the engraver etched through these top mediums to create the image. Then the plate was dipped in acid to cut the image into the copper.
You can read more about this process on Wikipedia here.
Here is the (uncorrected) description of how the press works from the Deutches Museum.
A great deal of pressure is necessary for the manufacture of a copperplate engraving, in order to press the paper into the cuts and to suck the ink out. Letterpress printing machines with a platen are not really suited to the purpose. In the sixteenth century, presses with their own back pressure cylinders were used for the first time.
With the star wheel, the copperplate printer moves the running board, plate and wooden cloths through between the two rollers. The upper roller produces the pressure, the lower one transports the running board. Due to the high pressure, the printer needs both his hands and also his feet to move the star wheel.
The copperplate press is a reminder of the sheer amount of labor and willpower needed to create a book like Roubo’s in the 18th century. Even though our translation seems like a lot of work (I’m proofing the index today), it pales in comparison to what Roubo and the printers of the day had to do to produce the original volumes.
Viva la Macintosh.
— Christopher Schwarz
They sell copper plate press pictures of the historic Deutches Museum façade in the gift shop. Did you happen to see those and maybe pick one up?
Nope. We had to catch a train before we could visit the gift shop.
Curses.
I’ll see if I can get a picture to you when I get home tonight. I bought a small one when I was there and had it framed.
Christopher,
Your comment on the three-dimensional nature of early printing techniques is very perceptive, and something most people fail to see. In early impressions of engravings by such virtuosos as Goltzius, the ink stands so high on the paper that the surface of the print can appear sculptural.
I have not seen an early printing of Roubo, but from looking at my facsimile, I am pretty sure that the plates were engraved. Although they are both intaglio processes, engravings and etchings are made by two distinct and different techniques. Engravings are created by literally carving away the surface of the copperplate with a burin. The ink, which is more like thick paste than what we generally think of when we think ink, is forced into the incision made by the burin, and wiped from the surface of the plate. When pulled through the press, the ink is pulled from the incision and deposited on the surface of the paper. Talk about a lost art; there are very few people who practice engraving, and virtually no one at the level of the 18th C French. Check out some of Robert Nanteuil’s, or the Edelinck’s, among many others.
Etching, on the other hand, is the intaglio process that involves wax or various resin “resists” and acid baths. The plate is covered with varnish, or some other “resist”. The etcher draws the design on the plate by basically scratching through the varnish. When the plate is immersed in the acid bath, the acid etches the plate where the varnish was removed by the etching needle, but the remainder of the plate is unaffected by the acid. The printing technique for etchings is pretty similar to that of engravings.
The main qualitative difference between the two techniques is in the type of line each produces. The engraved line in the copperplate has sharp, distinct edges. The etched line, because it results from a chemical erosion of the copper, has a more “granular” appearance. The main advantage to etching, from the artist’s standpoint, is that it is akin to drawing. It is easier for the draughtsman to produce, because it does not require the discipline of engraving.
Sorry for going on about this, but it’s a subject near and dear to my heart, and I perceived that you were confusing the two techniques.
I definitely defer to you on this point.
The press looks like a variation of a workbench in design terms. It wouldn’t be much of a stretch to adapt the same joinery to create the rigidity required to resist the pressing load. Go for it, don’t wish – design and build a press of your own!