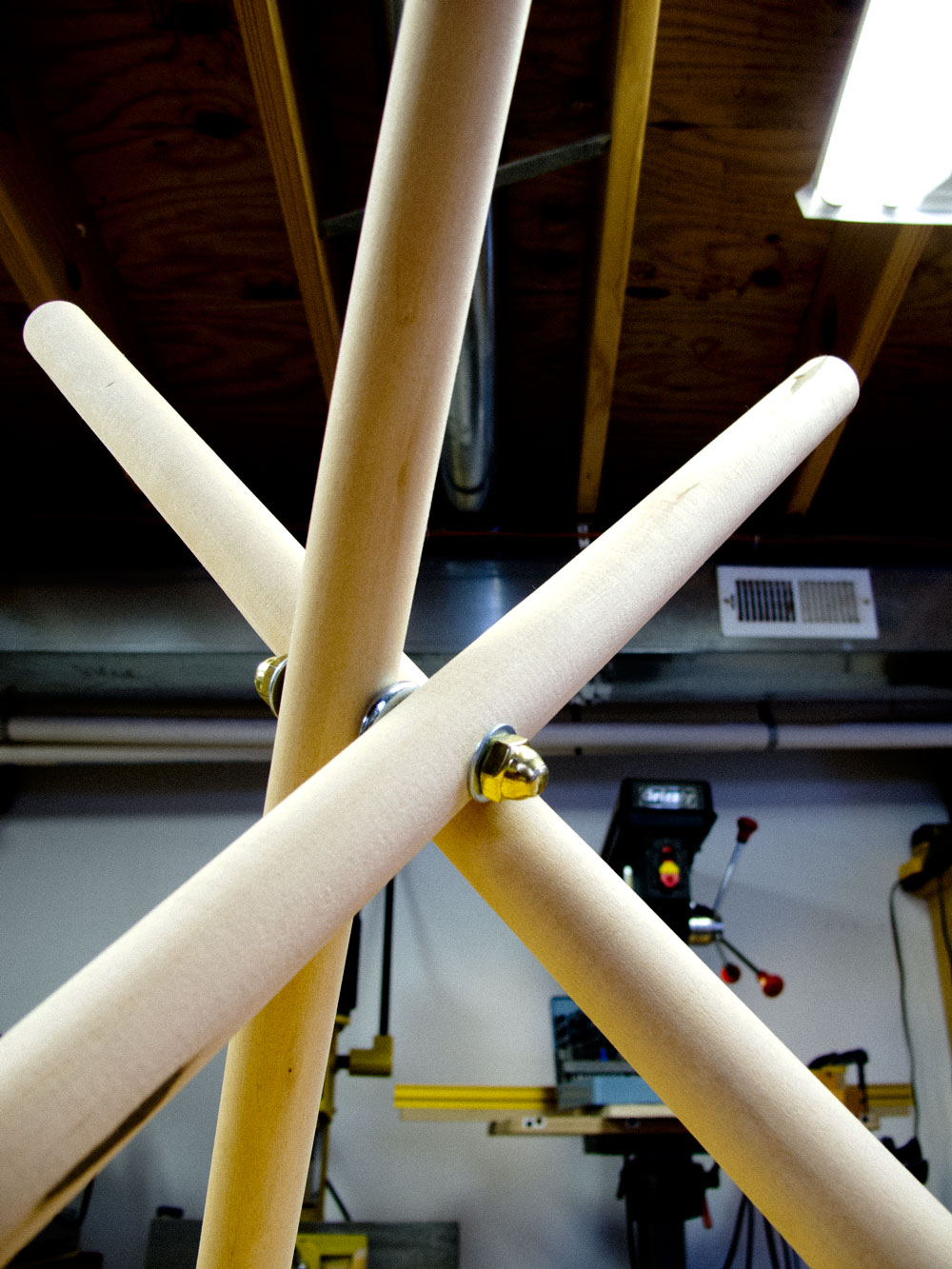
Today my daughter Katy was home sick and asked to give me a hand in the shop building a prototype of the Andre Roubo campaign stool.
We made the prototype using 1-1/8”-diameter dowels made from some spongy wood from Southeast Asia. We’ll make the real campaign stools from mahogany spun on the lathe and leather scraps leftover from the Roorkhee chairs.
Today was all about getting the hardware working with the holes and the sticks. When everything is tuned correctly, the legs fold out without flopping out.
Today I taught Katy to use her first machine: the drill press. She drilled the holes in the legs. Her holes looked great because she drilled in from both ends and her holes met in the middle. My hole was so ragged that Katy was compelled to take a picture for you.
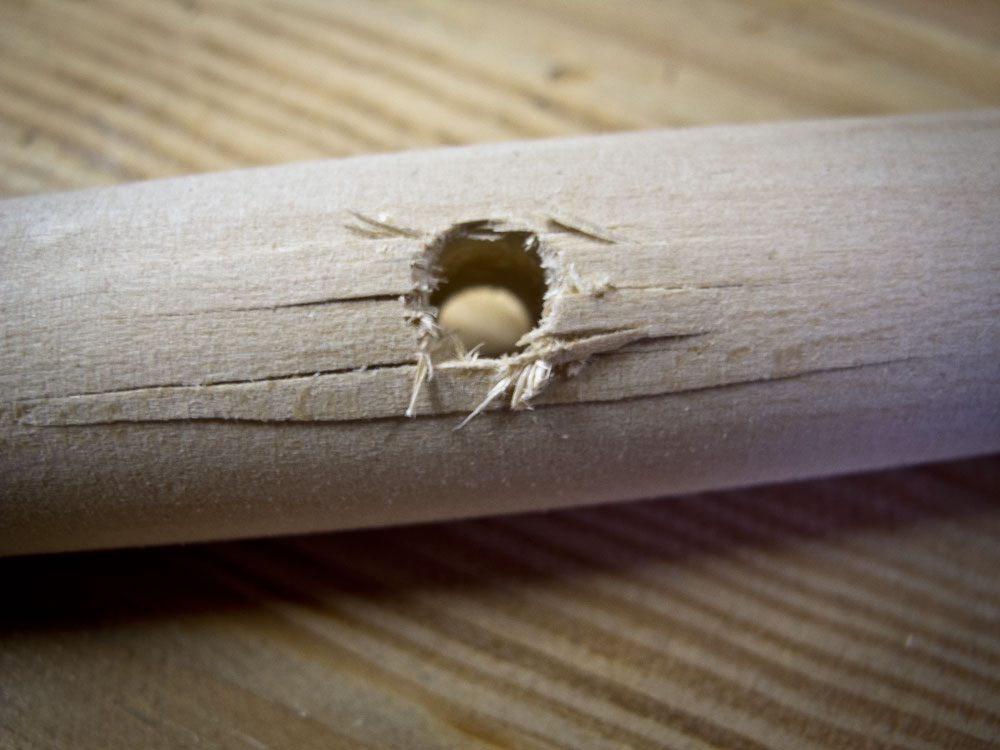
Note that we threw this one in the garbage and used her legs instead.
The hardware is the interesting thing. I’ve resisted making these stools in the past because the old books show making the hardware by soldering some round steel stock together and then threading it manually.
Instead, we’re using 5/16” all-thread rod that is bisected by an eye bolt to make a three-way joint. It works very well. The hardware is secured by washers and brass acorn nuts. Tonight my leather-loving shop assistant, Ty Black, is going to stitch up some different seats for us to try.
I hope (and also don’t hope) that Katy is sick tomorrow.
— Christopher Schwarz
Well done Katy! Perfect for Get Woodworking week.
You’re a good Dad.
Oh yes, it reminds me of that design: http://www.designsponge.com/2011/06/diy-project-tripod-camping-stool.html
That’s where I got the idea for the eyebolt!
OK, I feel dumb but I’m not seeing how the leg obscuring the drill press is held to the other two. Can you take a “birds eye” shot?
That leg has an eyebolt threaded into it; so by itself it looks like a weird coat hanger. The other bolt passes through the other two legs and the eye part of the eyebolt to finally be capped with acorn nuts.
Among the reasons for woodworkers to befriend blacksmiths is the general quality of store bought hardware today. You are about learn about the shear strength of Hillman all-thread, I fear.
Nice project, thanks for posting. This look achievable for all of our apartment-dwelling woodworking friends.
Looks like she has your knack for photography, as well, Chris. Great job, Katy!
Here is the source for that hardware configuration:
http://www.designsponge.com/2011/06/diy-project-tripod-camping-stool.html
School should never interfere with one’s education : )
I couldn’t agree more. I love the sick days.
Great job Katy. Make sure the threaded rod is just long enough. Cranking down too much on the acorn nuts will pop the little dome off. DAMHIK. More than once.
We did that, too.
I used threaded inserts (nuts) in the legs to avoid having to measure or tweak the screws length.
As a leatherworker back in the 1970’s, I used to make these. We used to buy a three way bolt with acorn nuts from Tandy Leather (made for these stools). They were made from some kind of diecast metal. Oh for a friendly blacksmith to forge them…
The leather top had a pouch rivetted onto each of the three corners on the underside, and we used to tool the leather top into assorted patterns. A great use for your leather off-cuts and residual rivets, Chris.
I was just wondering where your “Roubo Campaign Stool” name came from. Is there an illustration of this stool in a Roubo manustcript? I thought Roubo pre-dated the era of Campaign Furniture.
Greg,
Campaign furniture dates back (easily) to the 1600s in the literature. And there is a drawing and description of this stool in Roubo. See my first post of the day:
https://blog.lostartpress.com/2013/02/05/more-roubo-in-wood-not-words/
Well I’ll be a williewombat! There’s something new to learn everyday! I hadn’t seen the earlier post with the Roubo stuff about this kind of stool. Thanks for pointing it out.
Amazing … There’s a much longer heritage to the design than I realised.
Thanks, Chris.
I can think of three or four possible forged options. All would be more than the cost of the all thread and eye bolt. And of course I couldn’t forge an acorn nut very well. Personally I see a nice square nut to match the forged hardware, but I am sort biased.
“leather-loving shop assistant”. Everyone needs one of these. [snicker]
http://woodandfaulk.com/make/folding-tripod-camp-stool
Here where I saw it a wile a go. A friend of mine from france has one, he had it for a long time, and just cary it every where he goes!! It is a great stool!
Cheers
I love that Katy showed Dad how to drill the dowels. The best teachers are willing learners!
Perhaps this is the plan, but before the design gets out of prototype, I’d try to find a way to incorporate a smooth-shafted bolt into the arrangement. I have found when messing with this kind of stuff on my boat’s mast, that under stress the threads will chew/saw up the wood fairly quickly and enlarge the holes eventually to the point where the leg would be weakened.
It’s great your daughter gets to help you on projects and that she wants to. Great job Katy!
It would be quite easy to make a smooth shafted steel bolt by cutting a piece of steel rod to length and threading the ends. A die (and a handle to turn it) in the size for the steel rod doesn’t cost much. I know you know how to use a threading die from the photos/videos that accompanied your various posts on your “milkman’s” portable workbench. It’s just a little harder to turn than the threads you made with the Beall threader because you won’t have router assistance to make the threads — you have to use brute strength. If you can pick up your Dutch travelling tool chest, you have enough brute strength to put threads on a steel rod. It would help prevent your falling on your butt when the questionable shear strength of the store-bought all-thread rod gives way.
As a stop-gap fix, copper (or brass) tube used as bushings would delay wear considerably.