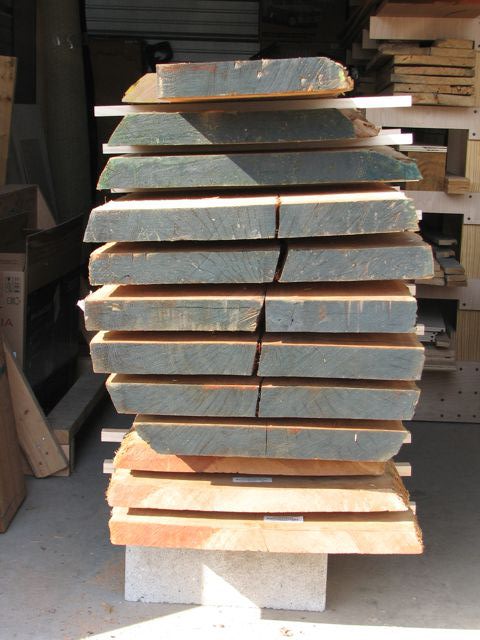
I recently returned from a week and a half in Colombia. While there, I got to experience some of the temperature and humidity extremes that we subject our furniture to: We traveled from the warm, humid llanos at Villavicencio, to the cool, wet cloud forests near Bogotá and in the Santa Marta range, to the hot, near-desert thorn forests of La Guajira. Fortunately, I personally contain very little cross-grain construction, so I emerged without any significant structural damage, save for a few mosquito and chigger bites.
Water exists in wood in two forms: Free water is water that occupies the voids in the wood, and generally behaves like a liquid. Bound water is water contained within the solid structure of the wood itself, and behaves more like a vapor “dissolved” in the wood. For our purposes, free water isn’t very interesting, as it moves freely (duh) via capillary action, and doesn’t contribute significantly to moisture-related wood movement. There is, however, some evidence that movement of free water is hindered when the surface of a piece of wood is very dry, which may be another contributor to the why-won’t-my-thick-slab-dry? phenomenon. As Chris noted previously, thick slabs often act as if the dry surface wood somehow seals in the moisture in the bulk of the wood, and it may be the case that free water is being trapped.
Bound water moves via diffusion. Imagine a large room containing 500 drunken woodworkers (e.g., the banquet hall at Woodworking in America). They’re all in there, randomly staggering around. We draw an imaginary line through the middle of the room, and discover that there are 450 woodworkers on one side of the line, and only 50 on the other side. Why? Guess which side of the room contains the open bar?
When the bar closes, the distribution begins to even out. This doesn’t happen because the woodworkers are purposefully trying to move away from the bar; it’s just that anything moving around randomly is more likely to move from an area of high density to an area of low density than the other way around, simply because there’s more “stuff” in the high-density area.
If the room has open doors, then some of the woodworkers will occasionally exit and end up in the hallway. As long as there aren’t very many woodworkers out there already, there will be more woodworkers exiting than coming back in. Eventually, a point will be reached where there are as many woodworkers randomly coming back in as randomly leaving, and the system will be in equilibrium. This is diffusion in a nutshell.
In a future installment, we’ll get into the nuts and bolts of diffusion, but for now we’ll skip all that and look at some wood, namely three boards, each 8′ long and 20″ wide, and 1″, 2″ and 4″ thick, respectively:
Imagine that you’re a molecule of bound water, located smack dab in the center of a board. Your quickest escape is through the face of the board, as the edges and ends are too far away. If you’re in the 4″ board, you have to travel four times as far (2″) to get out than you would if you were in the 1″ board. Remember from last time that the drying rate in this case goes as the square of the board’s thickness, meaning that it’s going to take you 16 times as long to go four times as far.
Now imagine that you’re a molecule of bound water very close to the end of a board. Your quickest escape is through that end. As we go from the 1″ board to the 2″ board to the 4″ board, your local environment doesn’t change; you’re still very close to the end of the board. In other words, the rate at which you leave the board is independent of the board’s thickness. And this is what gives dry kiln operators nightmares (and why many of them won’t touch thick slabs): The disparity between drying rates at the center and ends of a board increases dramatically as the board gets thicker, and along with that disparity comes increased stress in the board. The rapidly drying ends shrink faster than the center, with end splits being the inevitable result, as in the photo above.
This also applies to the faces and edges of the board, but as we will see next time, it’s usually less of an issue there, except for certain species, such as oaks, that have a strong tendency to develop surface checks, especially on tangential (flat grain) faces.
Even though some of the boards in the photo aren’t cracked at the ends, they nevertheless contain a substantial amount of built-in stress, leading to an increased likelihood of cracking after the board is placed into service. Knowing how the board’s neighbors behaved, and depending on how it will be used, I might inset a butterfly key on the underside of such a board to help restrain it. If I’m really nervous about it, I might even cut the board in half lengthwise, plane the cut edges and then glue it back together, just to be on the safe side.
We can reduce the drying rate disparity by covering the ends of the board with a substance that retards diffusion. (Again, slowing moisture loss from the end grain is usually more important than slowing loss from face or edge grain.) People have used a lot of different materials for this. In my own experience, latex paint offers some protection, but seems to be more or less worthless in the long term. I currently use a commercial water-based wax emulsion product, Anchorseal from UC Coatings, with good results. The absolute best product for eliminating moisture loss that I’ve tried is Leak Stopper aerosol roof sealant, but it’s a bit messy and kind of on the expensive side. I’ve also heard that oil-based aluminum paint works well, but I haven’t tried it.
Next time: The scary-looking diffusion equation! (You may want to ask small children and sensitive adults to leave the room before reading.) Also, we’ll answer the question of whether or not it makes sense to drill holes in a thick slab to hasten drying.
–Steve Schafer
Excellent bit of instructive writing. Thanks.
I’m curious if putting smaller pieces in a vacuum bag would significantly speed the drying process.
It might help in the early stages if the wood is very wet, but unless you add heat to the mix, it’s probably not worth it. You’d get far more bang for your buck by building a small heating chamber from foam insulating panels and an incandescent light bulb. Heating the box to the 120-140°F range will be enough to significantly increase the drying rate (by a factor of four or so) without getting into the range where you need to worry about humidity control to avoid creating stresses in the wood.
Good stuff again! Thanks Steve (and LAP for believing this kind of stuff just might be helpful).
I’m wondering if a dryer similar to a “gear dryer” used for drying structural firefighting gear would help, low temps with long run times and dry air movement.
…just a thought from a beginner in the purest sense.
Thanks for the schoolin’. I had a notion of this, but this sounds righteous.
I think a practical exercise at the next WIA is in order.
Harrumph!
” … drying rate in this case goes as the square of the board’s thickness”
According to this, a 2″ board would take 4 times longer to dry than a 1″ one.
Data supplied by the Forest Products Laboratory for the 1″-2″ range of thickness suggests that it is not a square occurrence, but rather that it is linear.
I’m talking specifically about the center of a wide, long board (we started out talking about Roubo workbench slabs). As you make the board narrower and/or shorter, then the square-law thickness dependence mixes with the end grain thickness independence so that the average drying rate is increased. An example of this is firewood, which dries within a year or two even in thick sections, because it’s cut into short pieces.
I’ll be showing a more detailed model in the next installment that covers these additional considerations.
Forest Products Lab data shows the time required to air dry lumber, not firewood.
Seems to me that for chunks of firewood to dry so quickly, the axial component of the diffusion “constant” must be hugely larger than the transverse components. Also seems likely that acknowledging this high anisotropy of the diffusion of water in wood is central to understanding much about drying lumber ( as well as explaining many other interesting phenomena associated with moisture changes and wood movement; for example, why often it makes sense to spring an edge joint, but sometimes it might be counterproductive to do so). So far your discussion has focused on slow losses of water through the faces and ignores rapid losses out the ends. Many of the things that stress both wood and woodworkers come about because of a big difference between axial and transverse loss rates. Sounds like you may go in that direction in future installments. I look forward to them.
@dzj9,
It would be useful if you would indicate which FPL data you’re referring to.
As a counterexample, if I eyeball the optimal-start-date red oak data from Simpson WT, Hart CA (2000) “Estimates of Air Drying Times for Several Hardwoods and Softwoods” for Charleston WV and 20% MC, I get 1.125″/57 days, 1.375″/85 days, 1.688″/128 days, 2.188″/230 days. Excel tells me that the best-fit exponent for that series is 2.09. That said, I should point out that the thickness range of the data in that paper is actually too narrow for a reliable measure of the exponent. (Determining the best-fit exponents for the other data sets in the paper are left as an exercise for the reader.)
Also, from McMillen JM, Wengert EM (1978) “Drying Eastern Hardwood Lumber”:
“Thick stock naturally takes longer to dry than thin material. One theoretical approach suggests that drying time, under identical or similar drying conditions, is a function of the square of the thickness. In actual kiln drying, the effect of thickness is slightly less.”
PVA glue as a sealer for the ends should also be a pretty good and readily available solution. I haven’t tried any of those things yet, but I have often had the idea.
Ordinary PVA has poor weather resistance, so it’s probably not a good choice for wood that is air drying outdoors. As an indoor-only sealer, it’s probably pretty good, but as with other coatings, the thicker the better.
Waterproof Type II PVAs (e.g., Titebond III) might work better outdoors, but I don’t know if anyone has done any research with them.
This would explain why the 6″ thick walnut in my shed for 15 years is still sopping wet inside, and the island legs I tried to turn from them promptly split in a half dozen places. And what happens to the WIA attendees who are too tipsy to find the door?
“Also, we’ll answer the question of whether or not it makes sense to drill holes in a thick slab to hasten drying.” Way to set the hook Steve. I’m looking forward to it.
Thank you for the excellent instruction. It explains why the 2-inch walnut slabs I had cut a few years ago have split badly, even though I painted the ends. I used Anchorseal on some mulberry slabs, and they’ve fared a little better, but some of them have split, too.
@steveschafer
It was a link from Mike Siemsen in your previous post.
https://blog.lostartpress.com/2013/12/21/water-vs-wood/#comment-23725.
I ploted results from the first 3-4 charts they give and they were all pretty much linear.
http://www.fpl.fs.fed.us/documnts/fplgtr/fplgtr121.pdf
A few things:
1) That paper appears to be aimed at kiln operators, who are air drying first to reduce the load on their kilns. That’s why the moisture measurements only go down to 20% for hardwoods, which is just the beginning of the drying journey for most woodworkers.
2) Drying times to 30% aren’t very meaningful for our purposes, as this involves mostly the release of free water, which as mentioned previously is transported by a different mechanism and doesn’t play a role in wood movement. The 25% curves should exhibit mixed free/bound characteristics, while you have to go to the 20% or lower curves before the behavior is dominated by bound water diffusion.
3) Curve-fitting is fraught with peril. Any curve will look like a straight line if you examine a short enough segment of it. If you do a linear fit to just the data points extracted from the paper, you will find that the line intercepts the t = 0 axis at a thickness of around 7/8″, predicting that wood less than 7/8″ thick dries instantly, which is clearly non-physical. You have to include the t = 0, x = 0 point in your fit, and when you do that it becomes obvious that the process is not linear.
At whom the paper is aimed at it doesn’t say. That’s your extrapolation.
It’s not really a short segment, but rather the one most often used (1″-2″).
And in this range it is linear.
Awesome stuff Steve. I have passed this along to my entire sales staff told them to read it and there will be a test later.
Steve, great couple of articles. I look forward to the next installment.